Introduction: Basic Beginners Mini 3 Axis CNC Mill
I've been a CNC machinist just short of 20 years. Owned a Fadal 4020 with extended Z made some neat gadgets with it. About 5 years ago after illness I started back working and looked into and purchased some micro-controllers. All with the idea of building my own little machines. And explore what makes it all tick. Above are two pictures of where my build started and ended over a 24 day period. I'll be doing updates and more instructables around this project in the future. Please enjoy and criticize where needed my first Instructable and CNC competion.
Step 1: CD Tray Axis Mods
I pulled 2 of these trays from CD players in my junk pile. Purchased the 3rd at a thrift store for $7.
Remove the CD spin motors and set them aside for spares.
Cut 4 x 1/4-20 all thread 1.25" long. Gather 12 nuts as well.
Small hardware for limit switches:
2 x 2-56 screws (x & y axis)
4 x 2-56 nuts
1 x 6-32 stud (z axis)
2 x 6-32 nuts
(use what's available or necessary due to variations)
Pic one show all the materials less the small hardware.
Pic two shows on-board limit switch, 6pin port, and 5v motor.
Pic three shows the various switches found in the lids of CD player.
Pic four shows the pinouts we can use (use for referance later on).
Pic five shows the all thread stabilizer mount.
Pic six shows tray variation on stabilizer mount.
Pic seven shows the screw and switch used for X and Y axis.
Pic eight and nine shows switch positioning. Used an existing hole on both X and Y axis trays for attaching. Had to open diameter up for clearance on my screw(2-56).
Pic ten we wire the new add-on limit switches to CD spin motor points on PCB.
Pics eleven thru thirteen show bracket and other limit switch variation. As well as pit falls to hopefully avoid.
Step 2: Lower (Y Axis) Mount
This here is the lower base(Y axis) and should/could be the base plate for all axis's.
Pic one gives basic dimensions
and shows parts list.
1 x 1/4 plate per dimensions
4 x 1/4-20 all thread 2" long
12 x 1/4-20 nuts
8 x 1/4 flat washers
Pic two shows all thread stud construction. Screw into plate till their flush on bottom. Use a nut to lock it to plate from the top.
Pic three shows fitting an axis tray. Watch the limit switch we added. I had some minor interference and adjusted around them.
Pic four shows completed build and dimensions to hold.( 1.375" for reference).
Step 3: My Crazy X Axis Cradle
I made this early on it looks good and works well but is unnecessary. You can use previous lower plate and add the 6-32 all thread as shown in pic four. Follow pics for theory. Note the 1.250" dimension in pic three.
If you go with all plates for holding the axis trays, use 4.00" x 3.15 for outside dimensions.
Hardware you'll need:
4 x 1/4-20 all thread 1.750" long
12 x 1/4-20 nuts
8 x 1/4 flat washers
1 x 6-32 all thread 1.625" long
2 x 6-32 nuts
1" x .75" x .125" square washer with .145 dia. hole thru(custom made)
Step 4: Joining the X and Y.
Pic one shows the thru hole. Also there were some tabs that stuck up here. I filed them down to have my cradle sit flush. When we fit the table I'll show you how to avoid the file job.
Pic two shows the custom washer plate and 6-32 all thread holding axis's together.
Pic three is the completed lower assembly.
Step 5: Z Axis Plate
Pic one shows hole patterns for the U bolts and hole sizes. Also note we drill .250" thru holes instead of 1/4-20 thread for axis tray attachment.
Pics two to four show the build.
Pic five shows our 1st booby trap. Had to bend tab out if the way.
Step 6: Main Base and Column
Pic one shows an old indicator base I've had around for awhile.
Pic two shows the axis assemblies mocked up on it.
Step 7: H Bridge Motor Drivers, 555 PWM Circuit, and Manual Control Buttons.
Pic one is one if three H bridges you'll need. I've shown where signals go in. Note that one yellow wire is of position by one from the 1 k resistor this is wrong sorry.
Parts list for one H bridge:
4 x 4401 NPN transistors
4 x 1N4007 diodes
4 x 1k resistor
Various jumper wires
Pic two shows the three H bridges and corresponding axis.
Pic three is a 555 PWM circuit. I have this here just for manual speed control. It's some what functional I found myself bypassing it for more power.
Parts list:
555 timer IC
100k potentiometer
.01 uF capacitor
.1 uF capacitor
2 x 10k resistors
Various jumper wires
Pic four is the manual button control.
Pic five is the connections between button and H bridges.
Pic six shows an overall layout.
Step 8: Motor Wires and Manual Tests.
Pic one has the 6pin port scavenged along with CD tray. It has been connected to a barrier strip. I've cut wire and connected to the other side of barrier strip.
Pic two shows wires used green/white for limit switches and black/red for motor.
Pic three shows the X axis connections. Once its wired up you can use 5v power from microcontroller to test it. If the limit switches are set right you'll get a bounce back effect. If their backwards it will jam the gears. Reverse your green wires to fix.
Pic four shows testing of other H bridges and buttons.
Pic five shows 6pin port in use.
Make sure to check all axis's and H bridges.
Step 9: Attaching the Table
Pic one shows hole diminsions for depths. The all thread attachment screw should be centered on plate. The other two are for attaching fixtures/subplates.
Pics two thru five show the build.
Pic six the finished assembly and mock up candy chuck.
Step 10: Mechanical Encoder Wheels for X and Y Axis.
Pic one shows a PS2 mouse I picked up for .99 cents(grab a few actually). I found all kinds of neat parts in there.
Pic two shows the front and back of the mechanical encoder wheel.
Pics two thru nine show the build and pit falls I fell in. This is a work in progress. I'll be investigating these devices abit.
Step 11: Original Test Spindle and New Revision
The spindle is my bane so far. Needs more work. But I've had some success.
Pic one shows some initial test parts and manual work.
Pic two shows my simple flex shaft holder. Worked fairly well.
Pics three thru five show some details on my new spindle holder also a work in process. Almost decided to make a CNC lathe to avoided it.
Step 12: Secure the Axis's to Main Base and Column
Pics one thru four show securing the axis assemblies to base and column.
Pretty simple here.
Step 13: Wiring Axis Trays and Encoders to Microcontroller.
Pic one reminds me of my Z axis bane.
Pic two has us adding a barrier strip to both encoders. Only one is shown here.
Pic three shows the X axis motor/limit switch hook ups. Used zip ties to secure barrier strip.
Pic four shows the Y axis motor/limit switch hook ups. Left it un secured Y axis motor stays stationary.
Pic five shows the Z axis motor/limit switch hook ups.
Pic six details the X axis encoders barrier strip.
Pic seven details the Y axis encoders barrier strip.
Pics eight thru ten show the hook ups to microcontroller and breadboards.
Step 14: Final Wiring of Motors, Limit Switches, and Microcontroller.
Pics one thru three show wire management for microcontroller to H bridge. And motors/limit switches to H bridge.
Pics four and five show hook ups for the Vdd(positive+) on the limit switches.
Pic six show the motors to H bridge hook ups.
Pic seven shows the limit switch normal open wires. This takes some debugging to get right. I flagged wires with tape(yellow arrows) once i knew what was what.
Pic eight is the microcontroller hook ups it also required some debugging to get right.
Step 15: The Candy Chuck and Manual Cuts
I turned up the candy chuck on my mini lathe. And used it for some manual test cuts.
Pics above show some drilled orange candy and a cherry "rune" stone.
Step 16: Safety Shield and Pbasic Code
Pic one is a safety shield i added on an adjustable arm.
Pic two is a screen shot of my Pbasic instructables MDI CNC test terminal.
Pic three the over all end for now.....
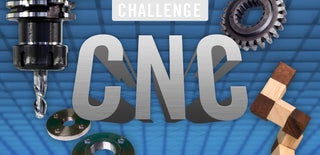
Participated in the
CNC Challenge