Introduction: Building a Bass Guitar
This Instructable is for building a bolt on neck, 5 string bass guitar, however all these steps are applicable for a guitar or 4 string bass as well.
This project requires that you have woodworking skills and you know how to to safely use all of the tools stated below.
For this project I used over 20 different tools; however you really only need a few.
Tools:
-Jigsaw
-Sander (Orbital, Belt, or Drum)
-Router (with many bits)
-Drill
-Drill press
-Forstner bit kit
-12" Drill bit
-Wood rasp
-LOTS of clamps
-Fretboard radius sanding block
If you have the money a jointer, planer, bandsaw and ripsaw are also very helpful.
Materials:
-Lumber (I will explain latter)
-Bolt on neck (Hopefully I will soon post another instructable on how to build necks)
-Woodglue Tight bond 3
-Pickup/s
-Copper tape/ Conductive paint
-A LOT of little screws
-Finish (I will explain latter)
-Strings
-Tuning keys
-Pre-amp
-Neck mounting screws
-Bridge
-Neck plate
-Jack plate
Step 1: Plan
It is very important to plan ahead if you are going to do this project.
First come up with a design.
You can either make a stereotypical design such as a J-Bass, or you can make your own like I did. (just dont use my design, it is heavy and not very useful)
You also need to figure out what type of woods you are going to use.
For bodies most woods work except Oak, Cedar and Pine.
Some really great choices are:
Mahogany, Alder, Maple, Ash, Poplar, Cherry.
Fender basses use Alder and Maple which give you alot of room to mess with the sound.
Mahogany and Cherry has a very deep bassy tone.
Ash sounds really funky and is often played slap.
Poplar sounds just like Alder just cheeper.
If you are going to build your own neck only use Maple, DO NOT trust any other woods, unless you are going to spend a lot of money on Mahogany, Wenge or another expensive neck wood.
If this is your first bass, I would advise using Poplar as it is the cheapest and sounds just as good as Alder.
Other than the wood you also need to plan what type of pickups you are going to use and how many of the, you want. There ares Single coil, Split single coil, Humbucker, and soap bar. You can also get all of those active.
Step 2: Start Your Woodworking
When you go to buy (or find) your wood, try to find something between 1 1/2 to 2 inches thick and 14x20 inches wide and long.
You may have to glue several pieces of wood together to match your design, However if you do end up gluing pieces together you MUST use a jointer to make sure there is no gap in between your pieces of wood. Use as many clamps as possible.
While you are waiting for the glue to dry make a full sized template of your base out of MDF.
Once your glue is dry draw your template on the wood. Use a band saw or jigsaw to cut out your design.
Use a wood rasp and orbital sander to shape the contours of the bass.
Step 3: Drilling and Routing
If you do not have any experience with power tools especially routers, PRACTICE BEFORE you route your bass.
Try on a piece of plywood or MDF.
As each design is very different I will just give you a basic tutorial on how to route your bass.
You will need a round over bit to round the sides of your bass. Buy a sevral different sizes and test them all out before to make sure the cut is not too big or small, once you have made the cut, it's done.
Remember, do not push the router bit all the way in to the wood or you will burn the wood. It is easier to just sand rough edges than to sand away burnt wood.
To route the pickup cavaties and neck slot is a bit easier. You will need to use a straight side bit. 1/8" will work.
Use a drill or drill press to hallow out the area that you are going to route so that your lines are cleaner, straighter and easier to make. (see pictures) Practice a lot before you actully route the finished product and always use templates. If you are useing a top on your bass routing can decrease the weight by 1/2 pound!
You need to route the neck pocket, pickup cavities, electric cavities, and possibly under the bridge.
When routing the pickup cavities, make sure that you know exactly where you want the pickup and how deep you want your pickups. The position of the pickups and distance between the strings and the pickups all deturmine the sound of your bass. Look online for standard pickup depths and positions.
The electronic cavity has to be large enough that all of the pots, resisters and other electrical components. While it does not really matter where you put the electronic cavity it should be close to the pickups and 1/4" jack so that wiring is easy enough. You also need to leave a lip so that the cover can sink into the wood slightly. Use the drill press to create holes the width of your potentiometer shafts.
When you route the neck pocket make it slightly smaller than needed the first time, then come around a second time to perfect the lines. If you feel uncomfortable using the router to do the fine details, use a chisel set. When drilling the holes for the neck pocket measure many times to make sure that you are not sinking the neck too low. First make the pocket shallow then make it deeper and deeper until you like the string height/action.
Step 4: Connecting the Neck to the Body
Unfortunately, this instructable is only about building the body and constructing your bass. However hopefully I will soon post another on how to build a neck.
You can find bass necks on the Internet.
Prices range from $80-400. For a cheep j style neck check this link out:
http://www.ebay.com/itm/1pcs-JP-Style-Bass-J-Bass-...
For a very nice custom neck check out this link:
http://www.warmoth.com/Bass/Neck/Warmoth.aspx
You may need to use a chisel to perfect the neck pocket, remember you can always make cavities bigger making them smaller is very difficult. You want the neck to fit very tight in the neck pocket so don't chisel away to much.
Once your neck fits tightly in the neck pocket you want to make sure you don't need to angle the neck forward or back at all. Because this is a bolt on neck it is unlikely you will need to angle the neck however if you use a Gibson style bridge you may need to set the neck back a bit.
Once you feel comfortable with he angle and feel of your neck; use the neck screws and neck plate to screw your neck And body together. You don't have to use a neck plate, I did not, however it gives it a nice look.
Dont glue on the neck unless you are 105% sure you are not going to take off or replace your neck.
Once you have screwed on your neck,measure where you need to place your bridge. Measure sevral times, you only get one chance at this. The average scale is 34", however make sure that the neck you ordered is 34" and if it not adjust where you are going to put your bridge. You can make minor adjust menus on the bridge, however measure from the nut to where the strings first make contact with the bridge.
If you have not yet put on the tuning keys do that, you may also have to put on string tees/trees to keep the strings on the nut.
Once you have found where to put the bridge, screw it on and string up your bass. Try playing it a little. If the action is too high up at the higher frets, then take off the bridge route wood from under the bridge. String it up again and see how it plays now. Keep doing that until the actin is perfect. Only route small amounts of wood off at a time. Once you have found the perfect action take off the tuning keys, bridge, string trees and any other piece of metal other than the neck plate.
Step 5: Applying Finish
Applying finish is the most time consuming step out of this entire process.
First you must choose the type of finish you are going to use.
Tung oil is a great choice because it is light weight and does not take too long to dry.
Spray on lacquer is very nice because it gives your bass a shinny look and is relatively easy to apply.
Do not buy lacquer from Home Depot or your local hardware shop. For tung oil use Sam Maloof oil finish, and go on http://www.allparts.com/ to find lacquer finishes.
Follow the steps that your finish says, however the standard finishing steps are:
Sand 100 grit, Sand 200 grit, Sand 400 grit, Sand 600 grit, Sand 800 grit, Sand 1000 grit, Sand 2000 grit, apply finish 3 or more times.
You are almost done, hang in there.
Step 6: Electronics
If you know nothing about soldering or electronics you may want to let someone that does do this for you.
Use the 12" drill bit to drill a hole from the bottom of the side of your bass, through the electronics cavity to one of your pickups. A wire is going to go from your pickup, (if you have more than one pickup you must use a drill bit to connect the two) to the electronics cavity, to the 1/4" jack. You may have to make the hole slightly larger for the male 1/4" TRS jack to fit inside.
Cover the inside of the electronic cavity and electrinc cover with conductive paint.
The wiring diagram shown here is a very basic diagram for a single coil pickup with a volume and tone knob.
If you want more complex wiring diagrams, just google what you are looking for.
EXAMPLE: bass dual humbucker wiring diagram
I advise using alligator clips first to make sure that every thing works before soldering.
Once all the electronics are done, screw on the electronics cover and jack plate.
Step 7: Finishing Steps
Put your bridge, tuning keys and trees back on and string it up.
Congrats, you have officially made your very own homemade bass guitar!!!
I would love to see/ hear any of your own creations.
Please post in the comment box below.
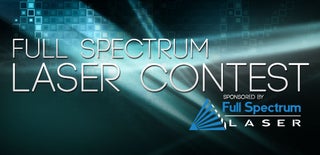
Participated in the
Full Spectrum Laser Contest
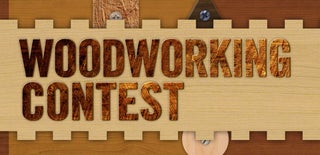
Participated in the
Woodworking Contest