Introduction: CNC Milling a Boat Propeller in Only 3 Axes
This project was made for my capstone class for my degree in Sustainable Manufacturing at California State University Chico.
Propellers are complex objects. Their non-linear lofted blades and exact concentric dimensions make them a challenging product to make. Normally, propellers are investment cast, which is a much more efficient means of high production for complex geometry. In this case, CNC milling was chosen because it has the ability to make parts with less set up and higher accuracy. This process allows the use of hard-to-cast materials such as titanium or high grades of aluminum. This manufacturing system would be ideal for making a limited number of propellers, a prototyping environment, or making extremely strong propellers for special applications where maximum performance is needed. The assembled nature of the fixture used in this CNC process allows for easy fixture changeover for different propeller sizes or geometries.
This Instructable chronicles my entire project from the design all the way through manufacturing and completion. I will try to use less technical language and cover as many points as possible, but reader beware, this will be a thick document and some parts of it might be hard to understand without a good grasp of production level CNC machining principles, as well as SolidWorks CAD and CAM. I will make use of in text links to connect you with good information whenever possible. Please comment if you need something clarified and I will add it.
This project wouldn't be possible without the inspired instruction and awesome laboratories of the Chico State department of Sustainable Manufacturing. Go WildCats!
Step 1: Project Overview: Problem and Design
Problem: Create a manufacturing system for cutting propellers in a 3-axis machining center.
Scope requirements:
- only use 3 axes
- produce a viable propeller that could be put on a real boat motor
- use available materials (project was done on a student's budget)
- use an assembled system to accommodate different geometries
- incorporate Poke-Yoke (mistake proofing)
- incorporate precise locating features to produce repeatable tolerances
- use standardized parts
- use efficient methods to reduce operator interaction with part and reduce cycle times.
Step 2: Components Overview
Using the above scope guidelines I was able to design a system with the following components. This is just a list, I will discuss each component in depth next.
Components:
- propeller
- fixture plate
- blade support lobes
- fasteners
Step 3: Propeller
This is a system to make propellers so it's only logical to start with the design of the prop I intend to make.
Using SolidWorks CAD I made a 5 bladed propeller with a diameter of 8 inches and a shaft height of 1.5 inches. The blades of the propeller were made by first sketching two slanted rectangles on two separate planes parallel to each other, and then creating a loft feature in between these sketches. This feature was filleted (given rounded edges) to create the smooth corners and then cloned in a circular pattern with equal spacing around the central axis of the propeller. Key design feature: there are no undercuts on this propeller! All of the geometry on one side can be reached in a straight plunge of the machine Z-axis. Put another way, no part of one prop blade is over any part of another prop blade when the propeller is seen from above. This is the key to making a propeller in 3 axis. Any prop without overlapping blades can be cut in this way.
I did not make this propeller to be a good propeller. I'm not a mechanical engineer and don't understand the fluid dynamics of flow, cavitation, or flow resistance required to make an effective boat prop. This propeller is made to look like a propeller and prove my machining concept. I picked 5 blades for no particular reason.
Here is a link to basic information about how good propellers work: http://www.hhprop.com/how-boat-props-work.php
This propeller is going to be cut out of 8 inch diameter 6061-T6 "aircraft" aluminum. I chose this material because it was free (Thanks to Danny!) and provided good machine-ability, dimensional stability, and was comparable to the material that some propellers are made of for real life applications.
The hole pattern in the middle was used for sheer simplicity. Three holes allows for good even clamping and prevents any rotational motion of the part in the fixture. Because this propeller was designed as a proof of concept for the machining operation and not for use on an actual boat, I didn't bother to use an actual mounting system. However, mounting systems for any propeller could be used in this system by attaching a mounting point to the middle of the fixture plate instead of the hole pattern.
Step 4: Fixture Plate
The fixture plate for this process is an 8.4 inch square plate of 1 inch thick aluminum. There are two circular concentric hole patterns and a locating feature machined into the plate. One hole pattern consists of 10 ¼-20 UNC holes for the mounting of the support lobes. The other pattern is the 3 ½-13 UNC holes in the center for the mounting of the part to the fixture plate. The locating feature is simply a machined square corner that is referenced throughout the CAD and CAM programs as a datum to orient the machining off of. I chose to locate the machining datum here directly on the plate as opposed to the circularity of the part stock because the plate has much less potential to move, thus providing a more exact datum. The top and bottom of this plate were faced to increase their dimensional accuracy.
This plate can either be attached to the machine table with toe clamps or fixtured in a vise. I fixtured it in a trammed vise for convenience in setup.
Step 5: Blade Support Lobes
The blades of the propeller need to be supported in the second operation or they will deflect because they are thin features. To fix this I made some support parts that mirror the propeller blade geometry in order to provide full contact support and also help locate the features.
These parts were top-down designed from the master assembly. They were made to allow some overhang of the propeller blade around their edges to provide for tool clearance, but still contact enough of the blade area to provide good support. Two holes were drilled to provide a close fit for ¼-20 UNC socket head screws, with counter sinks to allow the bolt heads to recess in order to keep them from interfering with the part. I made one support lobe for each blade and mounted them in a circular pattern around the fixture plate center.
In order to cut these parts out of 1.5x1.5x2 inch aluminum bar stock I made a simple fixture block that was the same size as the stock with faced sides to locate from.This block was necessary because the complex dimensions of the support lobe are impossible to cut if the part is in a vise. The block had two holes drilled in it and tapped to fit the ¼-20 bolts, to hold the drilled stock.
Step 6: Fasteners
Two kinds of fasteners were used for this process. The blade support lobes and their fixture used ¼-20 UNC bolts. The central stock mounting holes used ½-13 UNC bolts. Both of these thread designations and sizes were chosen because they are very common standard sizes and I had access to the proper drills and taps to cut them.
Step 7: Materials Selection
This entire project was made of 6061-T6 “aircraft” aluminum. I chose this material because it was conveniently available. This fixture is not designed for high-volume manufacturing, and is instead intended for prototyping or very short run environments where a limited number of propellers would be made. Therefore, I felt that aluminum was also adequate for this fixture. Furthermore, this is an assembled fixture so if the geometry were damaged the lobes could easily be replaced as needed without scrapping the entire fixture. Also, the mounting plate is thicker than it needs to be, so it could be lightly faced a few times to bring it back into tolerance if it was damaged.
Ideally, this fixture would be made out of O-series oil hardening steel for a good balance of dimensional stability, wear resistance, machinability, and cost. Case hardening of the material would also be helpful to reduce wear, especially around bolt holes.
According to Bay Propeller, the most common materials used for propellers are aluminum, stainless steel, and an aluminum-nickel-brass alloy called Nibral.
Step 8: Making the Fixture Plate
The fixture plate was rough cut from 1 inch stock using a bandsaw. The edges of the plate were roughed using a 1 inch 2 flute High Speed Steel end mill in a Bridgeport manual mill. The faces were faced flat using an 8 tooth carbide insert facing mill, also on a manual mill. A CNC program was written which first spot drilled all holes using a .25 inch spot drill, and then peck drilled the ½ and ¼ inch hole patterns through with jobbers drills. The program then tapped the holes through and milled a datum surface on the plate corner using a ½ inch 2 flute coated carbide end mill. Finally, a 2-flute 1/2 inch end mill was used to cut the locating feature in the lower left corner of the plate, using a very small cut depth, maximum coolant flood, high RPM, low feed, and conventional cutting to achieve the best surface finish possible. The plate was deburred with a belt sander and manual abrasives.
CNC tapping is a scary process. You need to set the feeds and speeds exactly, the tap needs to be perfectly oriented in the hole, and all your calculations need to be correct. I did the tapping on a Haas Mini Mill, which is the smallest CNC machine I had access to. I was lucky to use the smaller machine because I messed up the calculation and the 1/2 inch tap got stuck on 2 out of the three holes. If I was using a machine with more horsepower it would have broken the tap or sheared the threads. Thankfully it just stopped and errored out, so I was able to back the tap out and finish those threads by hand. The resulting threads were a bit coarse but serviceable. Thankfully, the threading of the smaller holes went perfectly.
Step 9: Making the Support Lobes/ Lobe Fixture
Lobe Fixture Block:
This fixture was cut out of 1.5 inch square aluminum bar with a horizontal band saw to 2.5 inches in length. Then, it was faced on all sides using an 8 tooth carbide insert facing mill on a Bridgeport manual mill. This block was then fixtured in a vise, using the vertical side of the vise as a locating feature. A CNC program was used to spot drill two holes using a 0.25 inch spot drill and then peck drill these holes through using a 0.25 inch jobbers drill. These holes were manually tapped using cutting oil and a ¼-20 UNC HSS tap.
Support Lobe:
The stock for these parts was cut out of 1.5 inch square aluminum bar stock on a horizontal bandsaw to two inches in length. Then, one long side was faced flat on a manual mill using an 8 tooth carbide insert facing mill. These pieces of stock were placed in a vise, locating off the side of the vise jaw. A CNC program was used to spot drill two holes with a 0.25 inch spot drill, and 0.25 inch through holes were peck drilled with a jobber’s drill. Finally, the holes were counterbored out to fit the bolts heads using a 2 flute carbide end mill. Then, the fixture block was placed in the vise and located off the vise jaw. The drilled stock was placed on the fixture block and fastened in place using 2 ¼-20x1.5 bolts. A CNC program was used to rough the part using a ½ inch 2 flute carbide end mill, and a ¼ inch 2 flute carbide ball mill was used to finish the complex surface. The parts were manually deburred.
Step 10: Making the Propeller/ Stock Preparation
Stock Preparation:
The propeller stock was cut from an 8 inch diameter aluminum cylinder using a horizontal band saw. Then, it was fixtured in a vise with v-blocks for even clamping and faced on both sides using an 8 tooth indexable carbide facing mill in a manual mill. The stock was then placed in a different vise in a CNC machine and fixtured again using v-blocks. A coaxial indicator was used to locate the part center. From this origin, a CNC program spot drilled the central hole pattern with a ½ inch diameter spot drill. Finally, the holes were peck drilled by a ½ inch jobbers drill.
The Propeller:
First, the mounting plate was fixtured in a vise and located off the cut datum corner. The propeller stock was bolted in place on the plate using 3 2 inch ½-13 low profile socket bolts. A CNC program was run in three stages to mill all the reachable geometry. The first operation used a ¾ inch 2 flute carbide end mill to rough away material at 60 IPM and 10,000 RPM. The second operation used a ½ inch 2 flute carbide ball mill to rough to a closer finish at 40 IPM and 10,000 RPM. Finally, a ¼ inch 2 flute ball mill was used to perform the final part finish at 60 IPM and 10,000 RPM.
For the second operation, the three central bolts were removed and the half cut propeller was removed. The 5 blade support lobes were bolted in place. The workpiece was turned upside down and replaced in the fixture, exactly as it was before except upside down. The three bolts were replaced and the same CNC operation as before was run to complete the propeller. After cutting was complete, the part was deburred with both manual and belt sanding procedures.
Step 11: I Messed Up! (Learning Experiences)
The first propeller I made has several problems:
- I failed to locate the plate properly in the X axis, offsetting the edge finder value of 0.1 inches the wrong way. This resulted in an imperfect propeller that had uneven radii, a non-cylindrical central shaft, and uneven blade thickness.
- I failed to face the stock to exactly 1.5 inches before I began cutting, leaving it slightly oversized. This meant that it did not fit snugly against the blade support lobes in operation 2, resulting in slight chatter in the finishing operations. This was the result of forgetfulness on my part, and could have been avoided by a simple measurement before cutting.
- The stepover (scallop height) on the finish pass was too great and resulted in an unsatisfactory surface finish.
During the second roughing cut the ball end mill was running into the steel mounting bolts because I forgot to designate a boundary around that area in the CAM software. This was a problem because I had to run this operation at a much slower feed to avoid breaking the tool, and it damaged the bolts pretty badly.
Step 12: Future Improvements
This was just the first propeller, more of a proof of concept and to work out problems with my system. After analyzing the part and process, here are some improvements I plan on doing to make a much better second propeller
- The system of locating off a milled right angle corner was a chance for the operator to mess up the location, which is exactly what happened. A better method would have been to press fit a precision pin into the corner of the mounting plate and locate coaxially off of that. That would give a clear dial indicator readout of the accuracy of the location, and involve just entering two exact values into the machine, as opposed to having to add or subtract offsets.
- When I was bolting the support lobes to the plate, I noticed that they were moving around slightly when I was tightening them in place. The bolt clearance holes they are held in place through allow way too much room for movement. To solve this, two matching hole sets need to be drilled in the support and the plate underneath it, with the holes in the plate sized to a slip fit, and the holes in the supports sized to a press fit. Pins could be press fit into the holes in the the support, and they could close slip fit into the holes in the plate in order to locate much more accurately.
- The central holes in the propeller are too large to provide a close fit on the 1/2 inch bolts. I need to use a smaller drill bit to predrill the propeller stock, in order to reduce rotational movement of the propeller on the plate.
- I cut too slowly on the roughing passes. For the initial roughing, I can push the speed up from 70 IPM to around 100, surface finish does not matter for this operation and the tool I am using is thick and rigid enough to run at these speeds. For the second roughing, I could easily run at 70 for the same reasons. In the second roughing and final finishing passes I kept on having to adjust the feed rates because the machine sounded like it was cutting through way too much material in the area around the base of the propeller blades. This was most likely because I had accidentally offset the propeller as mentioned in the previous step, so it had to cut an extra 0.1 inch of material on one side, and 0.1 inches less on the other side. Another cause for me to lower feed rate on the finishing pass was the very loud chatter that was occurring because the blade was not contacting the support, most likely due to my other errors. Fixing my errors and raising my feed rates would easily decrease my cut time by at least half an hour, by my estimation.
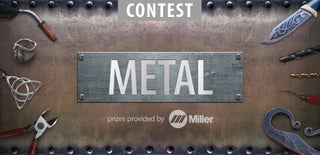
Participated in the
Metal Contest 2016