Introduction: CNC Router Enclosure
This is the build log for the enclosure I built for my Shapeoko 3 Desktop CNC machine from Carbide 3D
If you would like to know more about some more technical aspects of the enclosure and the machine itself, please head over to my Instagram
Also please check out my youtube channel: https://www.youtube.com/channel/UC1qIml4_nky4rELA_rbljaQ?&ab_channel=NickCharlton
So the idea behind this built was to create something that my machine could be fitted within and it would enclose all the dust and most of the noise.
Step 1: The Frame and Lining the Walls (1)
This has been an ongoing project for a while now and began shortly before the delivery of my Shapeoko 3 Desktop CNC machine. With my previous CNC, the Shapeoko 2, I cobbled together a wooden enclosure with polycarbonate sides and a removable front panel. It was effective at containing dust and isolating some noise but it wasn’t much to look at.
This time I wanted to do things right.
As I began to plan this build, two options of construction technique were in my mind as the most efficient and aesthetically pleasing methods. The first would be to use lengths of aluminium extrusion to construct the frame and fill in the gaps with insulated panels which could then be cladded with plywood or mdf. Alternatively I could buy a unit that the machine could fit inside and mod it appropriately, adding sound insulation as needed. I went with the latter
Steel frame shelving units can be bought relatively cheaply and require very little assembly to produce a rigid structure and only two 18mm mdf panels to act as the top and the main shelf. The 3mm steel provides a sturdy structure and allows ease of mounting parts to it by drilling and tapping.
Step 2: The Frame and Lining the Walls (2)
The two main goals I hoped to achieve with this enclosure were to contain all dust and debris within the unit and to provide noise isolation as the Dewalt spindle on max speed is quite an irritating sound profile and when the machine is running on longer jobs it would be nice to be able to remain in the same room without having to wear hearing protection.
To achieve this I decided to line the walls and the back of the enclosure with noise dampening poly-urethane foam sandwiched between two sheets of 6mm mdf. I used about 60mm of foam in the wall cavities and held the layers together with spray on contact adhesive.
After the insulation foam was mounted the wall cavity could be closed off with a 6mm mdf panel either side held in place with more spray adhesive and a friction fit against the top and bottom. The rear of panel as assembled in much the same way but was mounted completely to the outside of the steel frame to maximise space inside the enclosure.
Step 3: Aluminium Front Frame
The aluminium frame on the front of the unit is definitely the most aesthetically and functionally prominent feature to this build and it is needed for a few reasons. It will provide a smooth and perfectly square surface to mount the polycarbonate doors to the enclosure but more importantly it allows for the spindle mount of the Shapeoko to stick out further than the base of the cnc machine itself. The dimensions of the aluminium I used were 50mm x 100mm x 3mm. The extra 100mm sticking out the front of the enclosure allowed for the clearance for the spindle mount.
Having the aluminium tube extension frame bolted to the front of the enclosure allows the Shapeoko to maximise its work area without having to keep the doors to the enclosure open so that the spindle mount does not hit them. Furthermore, you can also see in the picture the bit itself hangs over the edge of the Shapeoko’s work area so the aluminium tube frame would also allow for an extended work holding table to be constructed so the Shapeoko can absolutely maximise its cutting capacity. I will be building and extended work table in the near future.
Attaching the aluminium frame the steel frame required me to drill access holes through the front of the aluminium so that I could push the bolts through the aluminium and then add a nut to create a secure and rigid fixture to the steel shelving unit. I could have simply drilled and tapped the back of the aluminium tube and bolted through from the inside of the steel frame. The problem with this is that because the aluminium is only 3mm so the threads wouldn’t be particularly strong and I was worried that if I tried to tighten the bolts down I would strip the threads. In the end with the 3D printed plastic caps I designed it gave the overall frame a more industrial aesthetic.
Step 4: Dust Port
The next key feature I was keen to include in this build was some way of keeping all the airbourne dust in the machine. Even with doors shut some dust can still escape dues to the air being flung around inside the enclosure due to the fan in the Dewalt spindle. So to achieve negative pressure inside the machine which would stop dust escaping through gaps, I added this inlet which receives the hose of my vacuum cleaner with a smooth but tight fit.
Step 5: Doors
The doors for the enclosure was definitely the most challenging aspect of this build to get right. Because the doors would be set inside the frame to a clean and flush finish, they would have to be cut exactly… I did have some leeway as I intended to leave a gap at the top to allow inflow of air to aid the vacuum in creating the negative pressure inside the enclosure that I wanted. I used 10mm polycarbonate as a local workshop had a sheet that the didn’t need. This stuff is an amazing plastic, it’s extremely shatter-proof and is used in bulletproof glass. It will certainly protect me from any tool breaks or whatever may happen inside the enclosure. As a fun little test I took an off-cut of the polycarbonate and shot it with one of my pre-charged air rifles and it stopped the pellet so I think it will stop a broken tool from the router!
Anyway, I cut it down to size using a circular saw and a track, I didn’t cut it perfectly but it is good enough for his application. The only dodgy cut was the one that split one panel into two doors, this left a slightly bigger gap in the middle at the top than the bottom but I can cover this up if needs be.
Step 6: Handles
The final step of the front of the enclosure was to attach the handles. These are very chunky ABS machine shop handles, specifically designed to be used on doors in industrial environments. These simply attached with two large bolts through the polycarbonate. After this I wired up some LED strips to the top of the enclosure and set them for a blue tinted white. I like the cool (as in temperature) effect it gives for video and photos.
I also installed magnetic catches to hold the doors shut.
Step 7: Finished
All done, now to start making machining some projects with this machine!!!

Participated in the
Rainy Day Challenge
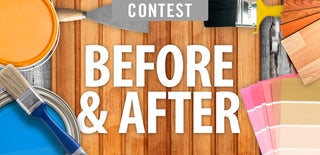
Participated in the
Before and After Contest 2016
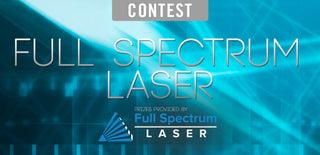
Participated in the
Full Spectrum Laser Contest 2016
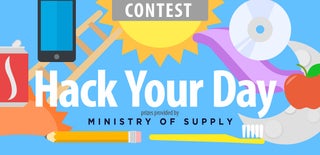
Participated in the
Hack Your Day Contest