Introduction: Captain America Helmet Using Many Materials.
In this, my first Instructable, I will show you how I made my captain america helmet from start to finish, using a combination of many material. I've seen peopl fight on forums about which materials are best overall, to which i say, all materials are great for one thing or another, but the best results you get are by combining and experimenting with these... so here goes..
for more of my work please check out my page www.facebook.com/lxcosplay
Step 1: Foam Basics
starting off with a foam pepakura file, i got the basic shape of the helmet
Step 2: Coating
after the foam shape was put together, a thick later of resin was applied, followed by a layer of fibreglass tissue to stiffen the shape
Step 3: Filler Filler Filler!
with the basic shape more solid, filler was applied to be able to add a smoother outside and to help define the lines more
Step 4: Quick Mould!
with the basic shape finished, a quick 2 piece fibreglass mould was made. this was done to allow for a fibreglass cast, much easier to work with than the foam and body filler i find.
Step 5: Working With the Cast
with a cast made from the mould, i found the eyes to be too small and the helmet to be too wide. After cutting down the middle, sanding each side, bonding them back together , filling and sanding, i found the shape to fit a lot better.
Step 6: Worbla!
Worbla is a great material, great for one off pieces and for adding detail. I cut and then heated and bent the worbla in place to create the raised sections of the helmet detail.
Step 7: Smoothing!
one problem i do find with worbla is it's hard to get smooth. Filler primer i found helps to smooth it off a bit, but due to not wanting to get it over the rest of the cast, I painted it on rather than spraying it. Once 2 layers were applied and set, I sanded it down to get it nice and smooth.
Step 8: Final Mould and Casting
with the pattern finished, I created a silicone and fibreglass mould to pick up all the details. With the helmet cast from the mould, a quick sanding was done over the raised areas to get them completely smooth.
Step 9: Carbon Fibre Vinyl and Painting.
to get the look I wanted on the helmet I opted to stick and heat carbon fibre vinyl over the lower sections of the cast. Before doing this I applied a quick layer of gloss black to help hide any areas I may have missed. Once the vinyl was on the helmet was masked up and sprayed the colours needed. The reason for adding the vinyl before painting was because the vinyl needed cutting, if it were done so after the paint was on, it would quite likely leave cutting marks on the paint.
Step 10: Adding the Last Details
With the main helmet finished, a 3d printed A was made, moulded and cast in resin mixed with aluminium powder, then heated and bent over the helmet, and finally stuck on. leather was applied onto the inside, with webbing, a chin guard and metal buckles. To add the last detail, I had 2 clips 3d printed in steel made up and stuck onto both sides.
Step 11: All Finished
All finished! added to the costume I've been making, looks the part!
for more of my work please check out my page www.facebook.com/lxcosplay
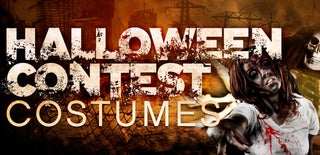
Participated in the
Halloween Costume Contest