Introduction: Christmas Decoration From Salvaged Materials
Having been a contractor in my previous career, I periodically came across materials that had been demolished from projects. Many of these materials were heading to the landfill, but much to my wife’s chagrin, I would lug some home from time to time.
In the following Instructable I explain how the salvaged remains of a dry cleaning conveyor became a moving Christmas decoration.
MATERIALS:
Parts from dry cleaning conveyor.
2x4s
4x6 pressure treated
2x6s
Carriage Bolts
Pipe Strapping
Screws
Plywood
Paint
Polyurethane
1” Galvanized Pipe
3/4" Galvanized Pipe
1/2 HP Electric Motor
V-Groove Pulley
V-Belt
Adjustable Lally Column Pipe
Extension Cord
TOOLS:
Drill Bits Electric Drill
Tree
Paint Brushes
Medium-sized Tree
Hack Saw & Blades
Framing Square
Two Wheel Cart
Tape Measure
Metal Files
Welder
Various Wrenches
Vice Grips
Saw Horses
Paint Roller
Step 1: Identify Treasure, Sweet Talk Spouse, and Idea
A number of years ago, I was going to do some work in a building that had once had a dry cleaning business. When I first walked into the job I noticed a pile of trash and metal in the middle of the floor. I recognized that many of the metal parts were from a dry cleaning conveyor that had been cut apart with a torch. Being a first-class scrounger, I asked the owner what the plan was for the metal and he said that it was going in the dumpster. Of course, I had to have it and upon gaining permission, loaded it in my truck. When I got home from a punishing day’s work I tossed it behind the garage. My wife came out to welcome me home and unfortunately caught me unloading my new treasure. Of course she was curious to know what I was going to do with “that junk”. I reminded her of the wonderful thinks I had used my previously procured “junk” for and she rolled her eyes and left me in my revelry.
Although I didn’t have a concrete idea at that time, within a couple weeks I decided to make a Christmas decoration out of it. I didn't make formal plans for the decoration, opting instead to use the time honored “build as you go” design process.
Step 2: Determine What Was Needed
The dry cleaning conveyor had been cut into indiscriminate sections with a torch when I got it. There was one curve, the gearbox, a couple lengths of pipe, a mangled section of track, and the track sprockets. It was necessary to get some lengths of 3/4" and 1" galvanized pipe to fix the track rail. The gearbox end was missing the curved pipe rail. The two sprocket ends needed to be spanned and connected to some type of beam and the entire assembly needed a means of support. There was also a need for a motor to make it operate.
Step 3: Metalwork
Since the missing curve was not easily replaced, I called a number of companies to get pricing on making a replacement. The lowest quote I received was $60.00. Because I knew I had to get a motor and other odds and ends, I decided to bend the curve myself. Fortunately, at the time, I had the perfect tree in our back yard. It had two trunks next to each other that came up and formed a fairly tight “V” shape. Using the intact curve as a pattern, I marked out the beginning, center, and end of the curve on the straight pipe.
I started the bending at one of the end marks and made incremental bends by moving the pipe to various positions between the trunks and applying force by hand and the use of a larger diameter pipe as a lever. The first time through I had a slight arc in the pipe. By repeating the process, I eventually tightened the arc until it became relatively close to the same shape as the existing curve.
To get the pipe to the correct curvature, I made a jig out of some 2”x6” scrap material. The 2”x6”s were connected in a double thickness. Once connected the arc was drawn and the curve was cut using a jig saw. The pipe was then connected to one side of the jig and bent until it fit as close as possible around it. The pipe was removed from the jig and further bent until it snuggly fit around the jig.
The new curve was welded to the existing flanges after the torch remnants were ground off. The track section was looked over it was evident that some parts needed to be replaced because they were damaged or missing. I found a company that had the parts and ordered what I needed and a few extra rollers and retaining pins.
Since I knew how much track I would have when the parts were fixed and replaced, I determined that the decoration could be fourteen feet in length.
Step 4: Wood Meets Metal
I decided to use lumber for the main beam as the metal ends were quite heavy (84 lbs and 140 lbs) and I wanted to keep the weight down as much as possible. The two ends were set on sawhorses and the track was placed around the sprockets. I then adjusted one end until the track was taut and then took a some measurements. A 4”x6” was used as the beam between the two ends. It was cut to 9’-6” and placed on the two ends. Locations for the bolts were marked and holes were drilled in the beam and through the metal at each end. The beam was then bolted to the end pieces.
Step 5: Pipe & Track
When set up to display, two sections from pipe (lally) columns are driven into the ground nine feet apart. The decoration then slides over the tops of the pipe.
Two sections of 1” galvanized pipe were purchased to replace the missing ones. The pipe sections were butted together and connected with a 3/4" piece of pipe used to span between the ends. Holes were drilled through the rail and connecting pipes and bolts were used to keep the connecting pipe in place. The track was slid onto the pipe prior to making the final connection.
Step 6: Hiding the Top
To hide the metal and beam at the top of the decoration, I used some more 2”x6”s to make triangular shapes that were screwed in place perpendicular to the beam. Originally, 1/4” marine plywood was cut and fastened to the sides of the triangles (cardboard has been used for this Instructable). The plywood covered the top and also provided some weather protection for the electric motor and gears.
Step 7: Power
Because the decoration was to be left out in the weather, an industrial water resistant motor was purchased. The motor was sized was based upon the original motor use and the fact that the weight it would be carrying would not be as much as the originally intended load. I settled on a 1/2 HP motor which has been in operation through rain and snow for many years. The decoration normally ran for around six hours each night for the two week season.
Step 8: Artwork
1/4” Marine plywood was also utilized for the figures. The artwork came from a coloring book one of our kids had at the time. The pictures were scaled up the old fashioned way, by using a grid system. After the pictures were transferred to the plywood they were cut out using a saber saw and then coated on both sides with exterior grade primer. My wife painted the figures using acrylics and they were covered with a two coats of clear marine finish. The figures were fastened to 2”x4” blocks held onto the track by screws and galvanized strapping.
Step 9: Entertainment
The decoration has been set up at our homes in New York and Pennsylvania since being built and it never ceases to get attention. We install it in our front yard with flood lights on it for night viewing and it is not uncommon to have people stop in the street to watch it.
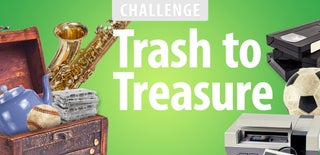
Participated in the
Trash to Treasure Challenge
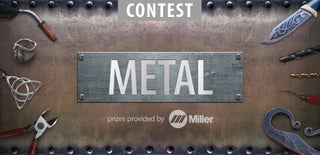
Participated in the
Metal Contest 2016