Introduction: Portable CoreXY Laser Engraver
This instructable is for my build of CoreXY movement style laser engraver. There are a lot of instructables regarding building CNC so I will not go into details as this is not a simple build and certain knowledge of basic CNC construction and setup of electronics is expected.
CoreXY is rather interesting CNC movement style that enables the machine to be more streamlined placing x and y steppers on the same plane making it flat.
More about this style of movement can be read on corexy.com
Items needed:
2.5W laser - $128 - Any laser would do but I used this one and laser holder
2 x Nema 17 stepper motors - $13.25 x 2
3 Axis Stepper Motor Driver Board - $26.99 - You could make your own with Easystepper driver board or Using GRBL shield for Arduino
4 x LM8UU 8mm Linear Ball Bearing - $1.69 x 4
UPDATE:
I realized that there was a part missing. At the start of the project the laser carriage had standard LM8UU ball bearing but as they were cheap ones they had a LOT of play in them so the carriage was redesigned to accommodate s 8mm x 11mm x 30mm copper graphite bushing instead.
2 x 8mm x 400mm Cylinder Liner Rail - $5.49 x 2
2 x 2GT 16 Teeth Timing Pulley and 5M 2GT-6mm Belt - $9.72
8 x GT2 16 Teeth Synchronous Wheel 3MM - $2.46 x 8 - This part is rather controversial as I used wheels with teeth but should be without. The reason is that wheels without teeth are way more expensive than the ones with teeth. Regardless I found that it works fine. You can exchange this part for GT2 16 3mm wheel without teeth.
36W 3.2A 12V Input AC100V-240V Power Supply - $5.79
Also a bunch of M3 nuts and bolts. Various length.
Also access to 3D printer is needed and also access to CNC is preferred.
All parts for 3D printing are embedded as SketchFab previews. click on the small icon on the left of the preview to go to the page of the part and there is download button.
Core XY
Step 1: Plate
Attached are files needed to make the base plate to which all components will be attached.
If you need files in another file format send me a message and I will add it.
You will need a CNC machine or a steady hand and a good ruler to cut them out.
I used 8mm HDF but MDF board is also good. You can use any thickness you like of currently have at hand. You will just need longer screws.
The plate is 50x50 cm in size.
Plate
Step 2: Printing of Parts - Part 1
Download the first part of 3D Printed items needed.
You will find in the file:
2 x Y axis guides that hold LM8UU 8mm Linear Ball
Laser holder that hold 2 x LM8UU 8mm Linear Ball
4 x Holder for Linear Shaft. Use this to attach the shafts to the base board
8 x Nema 17 distancers. Use this to connect Nema 17 stepper motors to the base board. Before you connect the steppers to the base board add the Timing Pulley Wheel to them. It will be harder to put them on later.
4 x distancers for Synchronous Wheels. Use 3D model in step 1 to see which wheels need to be distanced from base board and Y axis guides.
Load them into your favorite slicer program, I used Cura and print them. You can split them apart and reorient them as you see fit for better printing based on your experience. If you need additional help, contact me.
My settings were
Layer height 0.2
Shell thickness 0.8
Fill density 30%
Print speed 50 mm/s
Use M3 screws to connect them. Tolerances are such that you will probably not need nuts on the ends.
Note: Use longer screws on bottom 4 holes of the laser holder (X axis) as they will be used to secure the belt once its threaded in between the grooves in the bottom of laser holder.
Part to print - part 1
Step 3: Printing of Parts - Part 2
Here you can find Feet that are attached to the base plate.
You do not need to print them.
Make them as you see fit but do make them the same height.
Also included is handle for easier transport. Print two of them and place them to the sides.
Combined Feet
Handle
Step 4: Construction
For construction use reference model at the top of the page or on first page OR the one located bellow. It is a full 3D representation.
Core XY
Step 5: Setting Up Electronics
Now comes the interesting part.
Connect your Arduino board to computer and compile and upload attached GRBL firmware.
GRBL has added coreXY to its base code but it needs to be enabled and homing cycles adjusted.
Stepper motors have 4 wires. Use your multimeter to check which wires are pair. To do this set your multimeter in continuity mode and connect one wire to red probe and another to black probe. Do this until you hear a beep. The two wires that have that beep are connected and are pair. Paired colors for used stepper motor (JK42HS34-0404) is Black-Green and Red-Blue. Connect them to your grbl board Black-Green-Red-Blue. If at the end steppers are moving in opposite direction you can reverse them or change the direction in GRBL setup.
There are a lot of instructables about this if you get stuck. Also you can contact me.
Connect your steppers to X and Y axis on the board.
Attachments
Step 6: Laser
Now, I had issue with laser once it arrived. The fan was broken and I replaced it with larger one, a 40mm x40mm x10mm Brushless DC Cooling Fan. The holder for laser was made with that in mind but it should still work for stock laser. One additional bonus of larger fan is that in the laser holder I modeled in side vents that help in cooling the aluminium block and the vents at the bottom help in removing smoke from the path of laser beam. This is rather important as a lot of smoke is generated while engraving and smoke reduces the effectiveness of the laser beam.
Laser holder V2
Step 7: Controlling and Generating Gcode
To generate gcode to control the engraver use Inkscape 0.48.5 and a Laserengraver plugin.
You could also check https://www.repetier.com/repetier-g-code-plugin-for-inskscape/. I have not yet tested this but looks promising.
Step 8: Conclusion
If you have any questions or suggestions please contact me.
Please note that it could take me couple of days to get back to you.
I need to restate that there are a lot of Instructables regarding building CNC so I did not go into much details as this is not a simple build and certain knowledge of basic CNC construction and setup of electronics is expected.
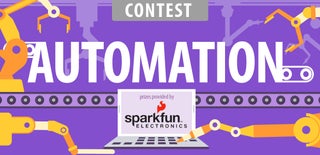
Participated in the
Automation Contest 2016