Introduction: Cow Skull Tool Bag
This tool bag was an idea I had in my head for quite some time but I just wasn't sure how to execute it. First I couldn't decide if I wanted to do a human skull or a cow skull. I actually started a human version but it didn't quite look right so I abandoned it. Second, once I settled on the cow skull I wasn't sure if I wanted it to by hyper-realistic or more abstract. I think this falls somewhere on the spectrum towards realism.
This tool pouch is made specifically for the tools that I use on the job daily but it could be modified to suit other applications.
Supplies
- 7 - 8 oz veg tanned leather (approximately 2 sq.ft.)
- 5 - 6 oz veg tanned leather (approximately 2 sq.ft.)
- 3 - 4 oz veg tanned leather (approximately 1 sq.ft.)
- 8' x 4' 1/8" hardboard
- Leather dye
- Leather sealer
- Space Bag
- Vacuum
- Clamps
- D-ring
- Stylus
- Brushes
- Daubers
- Punches
- Needle
- Wax Thread
- Snaps
Step 1: The Design
The overall design is that of a cow skull. Obviously a real cow skull is much larger than I would be able to use for a tool pouch so it had to be shrunk down, but the general shape is good for my needs. I image searched some pencil drawings of a skull and shrunk it down to the size I needed, about 8" tall overall. Once I printed it out I noticed that if I was going to maintain the proportions there wouldn't be much room for my tools...it wouldn't be wide enough. To fix this issue I split it down the middle and separated the top about an inch. The "pouchy" part is going to be from the top of the picture to just about where the nasal openings are. I also knew I wanted there to be distinguishable eye sockets and a nasal opening.
Step 2: The Shape
I am not a very good sculptor. I tend to form things lopsided and asymmetrical. What I can do pretty well is visualize shapes in layered segments like a topographical map. I've used this technique on other projects to make complex curved shapes. I think of it as a poor man's 3D print. I recently saw another author on here refer to it as "serial plane" sculpting. That seems way more legit than what I call it.
First, I cut a bunch of pieces of the 1/8" hardboard at about 11" x 8" just big enough for the skull picture to fit on.
Next, I glued 4 of them together and traced the skull pattern on top when it was dry.
Then, I used a scroll saw to cut the shape out.
I called this base piece #1. I then used the original picture as a guide to trace the next layers progressively smaller in different areas paying attention to the shading and the contours to approximate the actual shape of a skull. I would cut out one layer and then trace it onto the next piece and adjust my outline as appropriate. Just like a topographical map, if I wanted an area to have a steeper slope I would draw the lines of the next layer close to the layer below it. Shallower slopes would have lines further apart.
After it was all cut out and glued together I sanded the whole thing down to smooth it all out. I think I captured the eye sockets, nasal bridge, and cheek bones fairly well.
Step 3: Forming the Pouch Body (part 1)
The main body of the pouch is going to be three parts. Two front layers which will be wet formed over the wooden form and the back which is flat. Wet forming complex shapes can be difficult if the object is too tall or has any undercuts. The end result also depends on how thick the leather is. For large scale operations I have seen specialized vacuum forming machines with thick plastic sheets and industrial vacuum pumps for getting a good seal and a nice tight form...This is not that. I have found that an old vacuum and one of those vacuum clothing storage bags works well enough. This first layer which is the inner layer of the skull shape is only 4-5 oz leather so it is fairly light.
First I cut out a piece that was about 4" bigger than my wooden skull on the sides and bottom. The top of the leather will be aligned with the top of the skull since I had allowed for a little extra on top already.
Next I soaked the leather in luke warm water for about 15 minutes. When you submerge the leather you'll see bubbles coming from it as it absorbs the water. After a few minutes I like to work the leather a little bit beneath the water to help it get a little more pliable. I just roll is around a little.
As the leather is finishing its soak I cover the wood with cling wrap. This is just so the wood doesn't get too soggy. I wasn't sure if I was going to be using the form more than once so I didn't want to destroy it.
After the leather was finished soaking I removed it from the water and let the excess water drain off of it a little bit, then I laid the leather over the skull form. I aligned the top with the skull and used my hands to gently form the leather to the skull. I do this to give the leather a preliminary shape to help it maintain its position on the skull when I turn the vacuum on. Once the vacuum bag starts to shrink up it will have a tendency to scoot the leather around if it not firmly in place.
Next I carefully placed the leather and skull in the vacuum bag and seal it shut. I used my hands to get rid of most of the air and get the bag formed to the shape as much as possible before applying the vacuum. Once I was happy with the placement and reasonably sure the leather wouldn't shift I applied the vacuum. There was nothing special about the actual vacuuming part, it goes as per the directions on the bag. Any old vacuum will do.
After the initial vacuuming I allowed the bag to sit for about 30 minutes. These bags are not that good and eventually start to lose their seal. This isn't necessarily a bad thing though because the vacuum forming itself is just supposed to get you your shape quickly and effectively without risking too many tooling marks that you may get from forming by hand. You'll need air to get to the leather or it will never dry and the shape won't set.
Next I opened the vacuum bag and gently removed the leather and form together without separating them. I used a cloth to remove the excess moisture from the bag and gently patted the leather to remove excess moisture from it as well. I allowed the leather to air dry for about five or ten minutes.
Next I placed the leather and form back in the bag and repeated the forming as before and did this two more times. The point of this cycle was to try and remove a good amount of the moisture while maintaining the shape tight around the form. When wet-forming leather by hand you would normally be making constant tweaks to the shape as the leather dries because as it dries it will tighten up and become deformed.
Lastly I removed the leather and form and strategically placed some staples to help keep the shape as it dried completely. This layer is going to be mostly hidden so the staple marks are not a big deal.
Step 4: Forming the Pouch Body (part 2)
This step is similar to the previous step except I kept the first layer on the form and covered it in plastic wrap as well. I did this because if I just formed another layer from scratch on the wood form it when I put the two layers together they wouldn't fit right. I need the extra thickness from the first layer of leather. The soaking, forming and drying cycle was the same as the first layer but this time I repeated the cycle three more times for an important reason. Since this is going to be the outer visible layer I didn't want any staple marks so I needed to remove as much moisture as possible before letting it air dry so that it didn't deform as much when it dried. I did add some staples to the outer edge to try to limit the deformation and I did end up hand forming it a little as it dried.
Step 5: Adding a Little Flair
As the top layer dried I added some lines to simulate the bone lines from where a real skull bones would fuse. This was done with a stylus and a small sculpting trowel to make the lines a little deeper. Unfortunately the top layer dried a much darker color than I had hoped because it was a different kind than the bottom layer. I was kind of hoping it would dry the same light color as the bottom layer to give it a more bleached bone-y look. Oh well, the natural leather look is good too.
Step 6: Making Some Cuts and Adding the Stitching Holes
The top layer is intended to be the skull analog with the bottom layer being the pouch that actually holds the tools. So I cut the eye sockets and upper portion of what I assume is the cow's pallet and nasal passages. I'm not a biologist but that seems right? I also trimmed the upper and lower layer edges to give about a 1/2" border where it would be sewn to the back of the pouch.
The back of the pouch is pretty simple. I put the lower layer on the form and then on a piece of leather and traced out what would become the back. I then put the upper layer on top of them and punched all of my stitching holes. This was tedious. I would punch a few holes and then put a small brad nail in one of the holes to keep the three layers aligned as I punched more holes. Next I cut the "nose" off the form so I could better fold the bottom layer to form the pouch bottom.
Step 7: Tool Organization
I mostly just carry small 6" hand tools; channel locks, crescent wrench, 6-in-1, speed wrench, T-handle allen. But I also carry a heavy flashlight, calculator, inspection mirror, and precision screwdriver. These last four tools are the only ones that I need/like to have in a specific place so they will have their own positions. The flashlight is comparatively heavy to the other tools so I needed it to be centered so the pouch didn't pull to one side. Luckily the skull is well shaped for that so I made a leather cylinder and punched some rivet holes in the bottom layer of the skull. The calculator needs a nice large flat are for it's holder so the back of the pouch was best suited for that. The flat calculator holder also got two smaller flat pockets sewn on the front of it to hold the mirror and screwdriver but I don't have pictures of that process.
Step 8: Dyeing
The dyed parts of the bottom pouch layer is meant to look like the void space in the skull so is it black where the "holes" would be. The last picture you can see the final shape of the back piece of leather. The little tongue at the top is going to be what loops around the belt. You can also see the small pockets for the mirror and screwdriver.
I also punched a hole center of the forehead for a decorative concho.
Step 9: Stitching
I really wish I had some pictures of the stitching process but I can't find them. I just aligned all of the pieces and stitched through the punched holes. The bottom of the pouch layer had the tip cut and folded to make some overlapping flaps to enclose it so it could actually hold tools. Its hard to describe but makes sense if you look at that last picture closer. I added two small handle type loops at the bottom to form that hoopy part of the cow's pallet and put a solid steel ring through it so I could hang stuff from it if needed. I also added a sheriff's star concho.
Step 10: Southwestern Flair
...or cultural appropriation to some...sorry :(
After wearing the pouch for a few days I realized it needed its own belt. So I made a simple belt which I didn't document. It has simple southwestern motif elements and a gunbelt-ish look.
There you have it. Hope some of my steps and explanations help you in your projects!
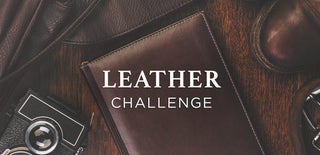
Second Prize in the
Leather Challenge