Introduction: Curved Concrete Hearth W/ or W/o Fox on a Log
I got asked to produce a curved concrete hearth to match up to a curved steel wall. This was my first attempt at making a curved shape and thought of a few different ideas before taking the path I chose. Being that I come from the carpentry side of things I decided to just form the curves out of wood like a strip canoe meets a lathe and plaster wall. The other option was to carve out of foam but being that I suck at carving I stuck with the wood option.
I think I'll keep this more about the forming tricks than the mixing, pouring and staining as there is a lot of great info already out on that stuff. This mix was pretty standard stuff as the shape is really only a blob of concrete, just flowable enough to get around one tight side and to work out the air and trowel the curves.
There might have been animals harmed in the production of this picture, but honestly they weren't there when I finished pouring. They just appeared when I was sent this pic, but it is Montana, so.
Step 1: Make It Look Like This
This was a job site mock up provided to me. I needed to match this within about 1/16" of an inch on a few critical spots and the few straight lines. Now back to the shop and drawing board.
Step 2: Laying It Out
I transferred a sort of visible grid to the top of a sheet of plywood that would become the bottom of my form. Once I had the bottom horizontal curve laid out I needed to create the shape of the vertical curve. I just created a nice looking shape using a piece of metal to make the rib shapes.
Step 3: Boat Building
The next step is much like building a wood strip canoe. I took the rib template from the last step ( no pic, sorry) and just used a simple templating jig in the router to bust out 30-40 ribs. The ribs then got pocket screw holes to attach them to the plywood bottom grid.
The spacing of the ribs is random and more to the eye of the builder, just keep them perpendicular to your curved line on the bottom grid sheet. This keeps the curve in the same plane so only the one rib profile is needed for the entire piece. Glue and screw all ribs in and add top and back rails to make the assembly a little more rigid.
Now cut strips of 1/8" masonite to go around the curves. The tighter the curves the thinner the piece needs to be, but just test a few strip widths to see what bends the best for your shape. Bend, glue, and pin nail these around the form. Break them to fit a tighter curve if you have to, but it will be tougher to mud later.
Step 4: Adding Cloth
Next I thought I should add some strength and form the curves a little more. Spray adhesive the ribs then add fiberglass drywall tape to the entire form. Just stick down or cut out anything that pops away from the curve.
Step 5: Drywalling
Now just get a few different types of drywall mud depending on your mood. If you like frantic work get something that sets in just a few minutes and get after it. The less slop the better so smooth it out as you go. I used so many coats of mud to smooth a perfect the curve that I ending up liking the quick setting for the really curved areas that were tough to work but used a slower set to build the general shape of things.
I did make a few specialty tools for this part of the job. I took a large 24" plexiglass knockdown trowel and cut the shape of my curve into, it looked like a giant battle axe. I used this to drag in long pulls from top to bottom the first major layers of mud. It worked great except for the really tight turn at the one end. The rest got done with just a flat piece of plexiglass. Triangles worked the best, just bend it with both hands to meet the curve you need.
Sand a lot. More mud. Sand. Mud. Sand. Mud. or something like that.
Step 6: And Done With the Form
Now its nice and smooth and shiny and you almost feel bad that your'e going to fill it with concrete. But before that a few more things.
I grabbed some spray lacquer and coated the form to hold in the water in the concrete, Just lots of spraying and a little sanding to smooth it out.
I also need to transport this form out of the shop and 50 miles or so away and was really scared about it. I filled the back of the form with spray foam to lock it all together for the ride.
This was the end product of my first curved form attempt. Now to pour the thing.
Step 7: The Pour
I cut out the inside of the grid plywood bottom and left the outside to attach the form to the ground at the site. Just a few concrete screws to the slab and some angled braces to the top of the form. I also epoxied in some re-bar stubs and added a re-bar cage to match the form curves.
A ramp was added to get wheelbarrows to the top and I think I only dumped one and bloodied one shin so not to bad of a pour.
I also made a few curved trowels to handle the front bull nose. Just cut to shape from some trowels that I had around.
Step 8: Acid Stains
Just your standard 3 color mix acid staining. They were only mildly nervous when they saw it glowing orange and red but it turned out the right deep dark brown.
Step 9: And Done
Well that was my first attempt at such a curved and large form. Its more about enjoying the use of curves then an exact way of doing things. Once you use this method once, it opens up a large realm of possible creations to start forming on.
I wish I had more pics to show but at the time I was just documenting some things as I went and didn't really know about instructables. But as before, its just the idea and a few tips that's needed the rest can just happen how it does.
Thanks for checking it out,
Greg
Oh, and sadly the form did not survive the pour and removal, only a few tears were shed. But I did keep the rib profile just in case.
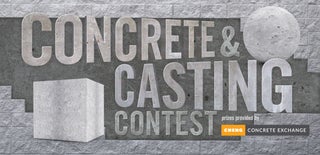
Grand Prize in the
Concrete and Casting Contest
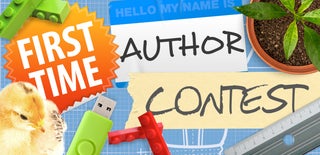
Participated in the
First Time Author Contest