Introduction: Custom Scifi Robot Helmet
This is a helmet I built as a client commission for someone at the end of 2015.
In this intstructable I will show how I built it from start to finish, the tools I used and some the the techniques I have picked up along the way. Total build time about just under 2 months.
PLEASE NOTE: I DO NOT own the rights to this helmet. This design is copy written my by client and he owns all the rights to the design. I am not selling kits or completed helmets. This is just a how to to show you steps and ways to create any kind of helmet as all of these techniques can be applied to different designs. CREATE, DONT COPY. :)
Supply list (in no particular order):
1/4" MDF
Elmer's School Glue
Insulation foam (EPS)
Bondo Body Filler - (Amazon)
1/16" ABS plastic (can substitue for styrene)
Super Glue - (Amazon)
Acrylic Paint
Rub N Buff (Amazon)
Sand paper (100 and 220 grit) - (Amazon)
Spray paints - (Amazon)
Filler Primer - (Amazon)
Graphite Powder (or grid up some pencils) - (Amazon)
Steel mesh (Amazon
Rasp (Amazon)
Silicone Molding Rubber (Amazon)
Polyurethane Casting resin (Amazon)
Welding Visor (Amazon)
Masking tape (Amazon)
Polyester Resin (Amazon)
Fiberglass Matt (Amazon)
Chip Brushes (Amazon)
Hot Glue gun and glue sticks.
Wooden dowel
Wing nuts and Bolts (I use 1/4")
Rotary Tool (Amazon)
PVC pipe
Lathe
Drill
Pop rivets and rivet gun (Amazon
RESPERATOR!!!!!
EYE PROTECTION!!!!!!!
RUBBER GLOVES!!!!!
Step 1: Build a Frame
So the first thing I did was draw out a blue print in InkScape and scaled the helmet design to the size of my client's head leaving about 1/2 on all sides for padding and Murphy.
I tacked them down onto 1/4" MDF with some white school glue. After it was all dry, I cut everything out with a jug saw and assembled the frame using hot glue.
Step 2: Make a Mess!
Now I took my insulation foam and cut it into squares, this allows me to fill the wooden frame I made.
All the pieces were glued into the frame and to each other with school glue and allowed to dry.
Step 3: Shaping
I started cutting down the foam blocks with a regular kitchen knife to block it out and remove most of the bulk so that I could begin it see the MDF frame. This also helps cut down on a ton of foam dust.
Once I had it carved mostly to shape, I took a rasp to the foam to refine the shape a bit more.
after I used the rasp, I took a bit of 100 grit sandpaper to the foam to smooth it out a bit more.
Step 4: Seal the Foam.
The thing about EPS foam is that it doesn't really like shaking hands with polyesters so I had to seal the foam with a couple layers of acrylic paint before adding body filler.
Polyesters tend to melt the foam and we don't really want that...
Step 5: Filler
So this part took a bit of time....
I covered the whole thing in body filler and began taking away the high spots with the same rasp that I used to take down the foam in step 3 (I used this tool a lot).
This process took 3-4 passes of filler and rasping to get to mostly covered.
The trick here is letting the filler sit for about 5 minutes after it begins to cure (15 minutes for full cure to be able to sand it) before taking the rasp to it. This will allow you to shave off excess filler and it almost looks like grated cheese as you're doing it (DONT PUT IT IN YOUR MOUTH!!!! IT'S NOT REALLY CHEESE...)
Doing it this way also cuts down on the dust from the filler.
Step 6: Start on the Visor Area
I cut out a long rectangular piece of the ABS that secured it to the helmet using some random sheet metal screws and 5-minute epoxy that I had laying around. The packing tape was used to make sure the ABS stuck to the form as close as possible while the epoxy was setting.
Step 7: More Visor Stuff
I used more ABS that I cut into 1/8" wide strips and glued them along the length of the visor area and also used it to create the angles on the sides of the visor. I dis this on both sides.
Step 8: Filling
Because the visor panel I added onto the form was straight and the form is curved, I had to back fill the empty area behind the visor and blend the top edge of the visor to the crown of the helmet itself. (sneaky huh?)
Step 9: Facial Features
After I had most of the crown where I needed it to be, I began blocking out the mouth and chin area of the helmet.
This was achieved using more ABS cut to shape and super glued onto the helmet one by one. This would leave more negative space between the panel and the form, so it was back filled with body filler before moving on to the next piece.
Step 10: More Face Stuff
The helmet is supposed to have these "D" shaped vent bits on the sides which will eventually have mesh in them, I had to fabricated those. MORE ABS!!!!!
I don't have a laser cutter so I had to used double stick tape and double up the ABS to cut and sand down the details on both pieces at once. They were then separated and used on overlays that were the same shape and glued to the helmet and back filled with more body filler. YAY!!!!
Step 11: Steps and Other Bits...
So, this helmet design is supposed to look like it has layers to it, one kind of laying over another to make it look like its a multi piece type of thing. to achieve this look, I first drew out my lines and using the same method as I did on the visor, I cut out 1/8" strips of ABS and glued them down to the form and used that as my hard "clean" edge for the level. I would then use body filler between these lines and shape them down with the rasp and 100 grit sand paper as before.
I also did this to shape out the rest of the helmet profile cheek area. (I thought it was a pretty neat trick. I dunno...)
Step 12: First Primer
I used gray filler primer here to see what I needed to work on and what I had done so far.
It's pretty difficult to tell of you have symmetry when your piece is 100 different colors and has lines all over the place.
This also gives me a first look at what the helmet might look like in the end and I always picture a 3D render at this step of a build.
Step 13: Ear Bits
So for the ear area I took a bit of PVC (also made of ABS) and glued down small sections of it to a square of flat ABS. I then trimmed off the excess and blended it into the sides of the helmet with more filler after cutting out the holes with a holesaw attachment on my drill.
The pucks for the ears were made with a wooden dowel on my lathe and molded to make 2 identical pucks that were then glued into the PVC recesses I had blended into the helmet.
A little bit of primer over that area just for the look (I use way too much primer just to take cool photos).
Step 14: Back End...
This step I was either super smart or super dumb but it all worked out in the end so it's coo...
I cut out a section of the back of the form and covered it in more ABS. The edges were slid in under the shaped area of filler on the top to hold it in place and the bottom was secured with pop rivets.
I then used filler to blend all the seams together and hit it with a small bit of primer.
I created the bar detail with more ABS strips that I bent into shape and glued to the ABS panels from the last step.
The voids were filled with more filler and tried up while curing with the tip of a chisel. ( I know right?!?!?!)
A little more primer and check him out!!!!
Step 15: Rounding Corners
This is just the way I do it, I'm sure you can do it with filler as well but this is just how I did it so yeah....
Take a bit of Apoxie Sculpt (plumbers epoxy will work too) and stick a bit into the corner that you want to round out. Flatten it down and press a round tube (Drinking straw will work too) into it by the edges that create your corner. Pull tube away from the corner taking the excess putty with it and let cure.
Sand smooth.
Boom! Done!
Step 16: Final Master Sculpt.
All that's left to do now is fine tune it a little and you're ready to mold it. This was about 10 days into my build.
I painted the bottom of the sculpt black to show what part would get cut off after molding and casting.
Step 17: Mold
I made what is called a Matrix mold.
You cover the sculpture with a layer of water clay in the shape that you want your mold rubber to take and cover that with body filler, resin and fiber glass mat, remove the jacket, remove the clay, set in the master and fill the negative with your rubber.
My buddy Bill at Punished Props made a great how to video on that here: YouTube
Step 18: Casting
I pulled the master from the mold, put the mold back together and I Rotocast (slush cast) a hollow copy of my helmet and I finally got to take my first selfie!!!! YAY!!!!
My buddy Harrison at Volpin Props did a fun little demo on how this works here: YouTube
Step 19: Trimming
I found that a jigsaw works great on trimming visors out of castings.
I drilled pilot holes and used a jigsaw to cut out the visor.
The back end of the sanding drum was used to make a lip area on the inside of the casting to rest a visor on. I did the same thing for the cheek vents and ear pucks.
I then put on the casting and looked up at the sky in triumph!
Step 20: Vents
I had this perforated steel laying around from my pitbull project, because I had it laying around outside and it isn't sealed, it rusted beautifully.
I cut these pieces to shape with heavy duty shears and test fit them to the casting.
Step 21: Fitting the Visor
I first create a faux visor from ABS and fit it into the helmet. The visor rests on the lip that was created when trimming the casting.
Cover the visor in masking tape and secure it into the helmet using wood screws (temporary).
The back fill the edge where the visor fits the helmet and let cure.
Remove the faux visor and sand area smooth.
Replace faux visor to test fit.
Cut out new (true) visor from the Tinted shield and use pop rivets to secure into the casting.
I used forsner bits to recess the rivet heads and then covered them in filler and sanded them smooth.
Step 22: Painting
We decided to go with 2 tones of black; flat and gloss. I first painted the helmet flat and masked off the areas that I wanted to keep flat and painted the rest gloss.
Step 23: Gluing in the Mesh
The mesh was glued in with hot glue from the inside of the helmet.
Step 24: Graphite
Graphite powder was used to give some of the flat black areas a more "gun metal" look.
This was just rubbed on with a cotton cloth and buffed a little.
Step 25: Weathering
Some of the hard and high edges were dry bushed with Rub N Buff Pewter for a bit of a worn look.
This also helps differentiate the edges from the black on black tones.
Step 26: Lighting
For the lighting, we decided to use Electroluminescent panels. The panels are powered by inverters that run on 3V each. I would be using one inverter for each panel so I designed a cool little holder in 123D and printed it on a 3d printer.
The inverters come with belt clips on them, I unscrewed them, slid the inverters into the holder and screwed the belt clips onto the back of the holder and everything is held in place that way.
Step 27: Light Shape
I took the EL panel and stuck some masking tape to it and drafted a simple zero design onto it. Using an exacto knife and a metal straight edge, I cut out my shape.
The cool thing about this is that I was able to take the tape off the first panel after it was cut, apply it to a second one and recut the shape to give me two matching zeros.
The shapes were then covered with some packing tape and trimmed.
The packing tape will serve 2 purposes.
1) Protect the open edges of the EL panel
2) Provide mounting points for assembly
Step 28: Extension
So the wires that connect the panels to the inverters are only about 12" long, this wouldn't be enough to wire up the helmet to have the inverters in a comfortable place so I had to extend them.
I didn't want 4 random wires sticking out the of the helmet, so I cut 4 lengths of 22 gauge wire and painted the tips and ends different colors to help differentiate them when I would be connecting them in line.
I painted both ends of 1 wire gold, another silver and another copper (I just had these colors laying around) leaving the 4th wire black.
I clamped the ends of the 4 wires into the chuck of my drill and spun them into a rope.
I then put a bit of heat shrink on the ends just in case.
Step 29: Mounting
I wanted to make the lights both removable and easy to position because I have never met the client and I want him to be able to adjust the lights to fit his eyes to optimize his vision.
To do this I decided to go with some adhesive backed velcro.
The panels have a small piece of velcro on both the top and bottom and the helmet has velcro on both the top and bottom of the visor so he will be able to adjust the lights as needed.
Hope that makes sense...
I then painted the inside of the helmet black and padded it with an Easton Naturals helmet fit kit.
Step 30: Try It On
Ahhhhhhh, We did it.
Step 31: Take Photos and Show Off!
Just took these photos with an iPhone 6.
Hope you guys like what I made.
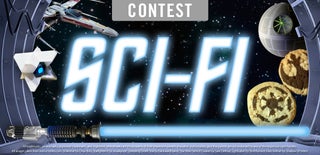
Third Prize in the
Sci-Fi Contest
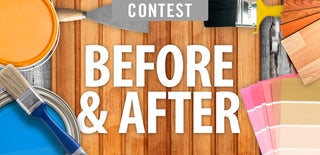
Participated in the
Before and After Contest 2016
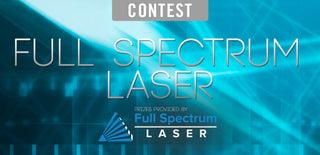
Participated in the
Full Spectrum Laser Contest 2016