Introduction: DIY Circle Map Lamp From Scratch
[ Overview ]
Hello everyone! This instructable will walk you through some steps to create this (or similar) table lamp. The lamp's pattern comes from an electron microscope image of a leaf. Dark areas in the image translate to small circles, while lighter parts of the image generate progressively larger circles. The image is cut into four panels which make up the lamp itself.
The whole lamp costs about $25.00 if you have free access to a laser cutter. I am fortunate enough to have access to a laser, which I used to make this lamp. However, you can simulate the effect by using a hand drill or drill press.
The pattern is generated digitally, using a program called Grasshopper. I'll only discuss this briefly, as this is not a technical tutorial and Grasshopper is a very complicated 3D modeling program. That said, I will post the pattern, drawing files, and source image along with this instructable for those who wish to use it. You can find a pattern online, make your own, or use mine.
[ Materials & Tools ]
1/8" Thick Hardboard – this makes up the four panels and the base (Lowe's has 4' x 8' sheets for $9.00 and will cut down to size for you)
Alternate: Hardboard is sturdy and fairly easy to work with. However, you can use cardboard (which is surprisingly sturdy when laminated) or chipboard, or even thin plywood.
Laser Cutter
Alternate: Drill or Drill Press
Vellum or Mylar – this is used to diffuse the light (can find at artists supply store)
Alternate: rice paper, trace paper, or other translucent scrap-booking paper
Spray Mount (Supper 77) – can find at hardware stores or artist supplies store, or places like Michael's
Screwdriver
Small knife or wire strippers
Lamp cord (with or without inline on/off dial) – Hardware store, less than $6.00
Lamp holder (plastic or ceramic) – Home Depot, Lowe's, Ace. Costs about $2.00
2 small mounting bolts to secure the lamp holder
2 washers for bolts
2 nuts for bolts
Linseed Oil (optional) – used to coat hardboard in order to provide a nice finish and darker material
Small piece of walnut or other wood (optional)- used in an optional detail to help hold lamp together
Super Glue (Loctite Gel)
Alternative: Hot Glue Gun
Foam Brush or Rag - for applying Linseed Oil
Step 1: Brief Description of Digital Pattern Generation
I will keep this portion fairly brief, as it relates to complicated 3d modeling and is probably beyond the scope of this tutorial. The thing to understand about the pattern, is that a script is used to take color data from an image an translate this data into a visual pattern of circles, or “circle map”. A black and white source image of high contrast is used and the script places the largest circles over the lightest areas in the image. The darker the pixels in the image get, the smaller the circles get. The result is a sort of gradient map of circles that relate the source image.
The images show some examples, as well as the image map I used. The script allows me to try different images and different scales very quickly. When I settle on a design, I export the pattern into AutoCAD for prepping my laser cut files.
Step 2: Making Your Own Pattern
IF YOU DONT HAVE A LASER OR DON'T HAVE THE CAPABILITY TO GENERATE A PATTERN...
I do not expect that too many people to have access to programs like Grasshopper to make these kind of patterns. As such, I can explain how to get a similar effect. You may not be able to get as tight a gradient, but you can easily make your own design to suit your tool set. The following steps can be done with a CAD program, or by hand...
To Make a Random Pattern
1. Determine your panel dimensions and draw this out.
2. Lay out a grid over your panel dimensions. Make each grid square (cell) the same size and pick a size you can work with, The smaller the cell, the more drilling/more holes.
3. At each of the intersection points of the grid, draw a circle. Select a diameter which will be the largest diameter you will use. For example, 1/2” is the largest diameter in my lamp pattern. All of your circles in this grid should be the same diameter at this point. Make sure to leave enough room between circles so they don't overlap. Make sure your diameters correspond to your drill but size. Use the intersection pints as center of circle. This will be where the bit goes.
4. Now, you can randomly erase circles to create a randomized pattern
To Make a Randomized Pattern of Varying Diameter
1. follow steps 1-4 from above, but do not erase the grid.
2. Randomly select some of the grid intersection pints and draw circles with varying diameters. Again, use diameters for which you have drill bits for.
To Make an Image Based Pattern
1. Determine your panel size.
2. Determine your source image
3. Over the source image, draw your panel outline
4. Next overlay / draw your grid
5. Use the dark and light parts of the image to guide your circle making process. Since you have a grid, if the cell/grid point falls on dark part of the image, make a large circle. If falls on light part of the image, make a small circle. The trick is to be selective with your diameters. Stick with 4 or 5 sizes at most, or you'll be swapping out drill bits a lot. Using 4 or 5 different sizes will give you a nice variation, if you use less, the clarity of the image will be less. I'm not saying this is going to be easy, but it can be done with patience and eye for detail.
OR...
Go to a hardware store and buy some pegboard. Pegboard has per-drilled holes on a grid. You can use this, or drill out some of the holes to be bigger.
OR...
Download and use the patterns I have provided in next step!
Step 3: Panel Design and Templates
Panel Design and Templates
As I have already mentioned, you can use the ideas presented here to make your own lamp design. That said, I will discuss this specific lamp from here on out. The files you will need have been provided.
So...the source image has been selected and a circle map has been generated. Now the panels need to be laid out and a template for the laser (or drill) must be made.
I laid out each panel next to one another. Each panel is 9”x23”, making the overall lamp 9” x 9” x 23”.
The circle map is spread across two panels, that way when you look at the lamp from an angle, you'll see the leaf image in the pattern.
Files Provided
Plans in .dwg format provided (AutoCAD file) Plans for entire lamp are in this file, which is draw at full scale.
Templates in .PDF format provided - These are to scale (1:1) so you can print them out and use them without any issue)
Source Image provided for reference
Step 4: Lamp Parts
Lamp Parts - See provided files on previous step
Base – the base slots into the panels to hold the lamp together via some small tabs. The length of the tabs. This is also where you will mount the lamp holder/bulb.
4 Panels – each one is 9” x 23”
Cover – goes on top of the lamp, but doesn't get glued. This way you can change the light bulb.
Bracing – simple corner braces to stiffen the assembly
4 Joint Covers- this is an optional detail I designed to cover the slots in each panel that the base piece notches in to. You don't need them if you glue the base into the panels, but it is nicer and looks cool. These are just 1/4” wide pieces of walnut that get glued over the slots.
Step 5: Fabrication
Using my university's awesome laser cutter, I cut the parts. I cut the parts out of 1/8” hardboard. Some people call this Masonite. You can cut the parts out of anything, but if you change the material thickness, you'll have to adjust the pattern accordingly. Each panel has a pair of slots in it that accept the tabs from the base. These slots are 1/8” wide to accommodate the 1/8” thickness of the hardboard.
Once cut, I used Linseed Oil to coat each piece. Linseed oil is super cool. You can put it on any kind of wood product (or paper product) and it will bring out all sorts of nice tones in the material. Here, I use it to give the hardboard a darker tone and in normal light, it looks sort of like a bronze material.
Just use a foam brush or rag and apply. Wipe when done with rag or towel. No need to wait for it to dry, the material will soak it up nicely. You can see in the images the difference in coloration between what has and has not been coated.
Note: you do not need to do this, but it will look better. Also, no need to coat the bracing pieces or the base, as you will not see these.
The cover pieces are walnut scraps I had laying around that I cut down. Walnut looks really, really, really, nice once coated.
Applying Mylar Diffuser
To diffuse the light and make an overall nicer lamp, I used Mylar. Iput the pictures in order.
Using some spray mount, spray the back of each panel with a good coat of Super 77 ( an aerosol glue). Lay down some disposable protection to keep spray mount from getting on your table. Lay the panels on top of your diffuse material (can be anything that is transparent, like rice paper, trace paper, or vellum) and press down firmly. Once all the pieces are laid down, put something heavy on top to make sure there is good adhesion. Leave it sit for 30 minutes or so. Do the same for the top cover piece.
You can see in the images, the spray should coat the panel in a film of white. You'll also see that when you finish gluing the paper to the panels, the back will seem very ugly. Don't worry, the faces you see will look great!
Note: Be sure to know what side is the back and which is front before you do this. You will not be able to get the glue off if you mess up. To find the front and back, line up the panels so that you see the pattern. Two panels for the one image. The panels are mirrored so the image is duplicated. Review the images in this tutorial.
Using a sharp, fine blade (Olfa Knife, or Exacto Blade) trim the diffuse paper material along the panel edges.
Now your ready to move on...
Step 6: Lamp Holder Assembly
Parts
Lamp Holder
Lamp cord
Bulb
I bought a lamp cord with a bulb holder on it. This will not work, as it is too small. So, I cut it off. To wire a new bulb holder from scratch, follow these simple steps...
1. Cut off bulb holder end
2. Strip wire ends- cut about an inch or so of the plastic off with small knife, or wire strippers
3. Optional – If your inline on/off switch is too close to the bulb or not where you like it, you can move it very easily. Just unscrew the switch and move it further down the line. You'll have to wire the bulb holder after this step though, as anything downstream from the inline switch will have to be cut off because the wires will be cut. The switch will be self puncturing- meaning that it will tap into the wire itself when closed. NO need to solder or anything like that. Just make the wires look like the image. Takes 30 seconds.
4. Find the neutral wire, identify the hot wire
In a two wire, color coded system that has one white and one black wire, the neutral is the white one. If your cord is like mine, all one color, you can find the neutral wire by looking at the wire itself. The neutral will have a raised ridge in it, or a texture of some kind. The smooth wire, is the hot wire.
5. Wire the neutral to the silver screw and the hot wire to the brass by wrapping the exposed wire around the screw and tightening with a screwdriver. In virtually and lamp holder, the brass screw is the hot, making the other screw set the neutral. If your lamp holder came with a package, instructions will be written on the back.
6. Test the set-up.
Step 7: Mount Lamp Holder to Base
Now it is time to assemble the lamp...
Mount Lamp Holder to Base
1. Mark where your holes need to go with pencil
2. Drill your pilot holes- ( I used #24 machine screws, 3/4” long with matching nuts/washers)
3. Secure the lamp holder to the base
Step 8:
Insert Base Into First Set of Two Panels
1. Find the panel that has the notch at the bottom for the cord.
2. Fit this panel with the base, matching the tabs in the base with the slots in the panel. See First image.
3. Adjust lamp cord and run through the slot to keep the cord from getting under in the way. See Second Image
4. Once the first panel is in, add the second. Note: the panels will be wobbly and not very sturdy at this point, until you add bracing.
5. With both panels plugged into the base, glue a single brace piece at the top, between the two panels at the joint as shown. Leave 1/8” from the top to allow for the cover to drop in nicely.
6. Continue by adding a second brace at the same joint near the bottom.
7. Once you have these two braces in place, continue to add bracing along the joint as needed. I used four braces per joint (corner). One at top, about 3” or so from the bottom, and 2 more in between.
Note: If you use hot glue, you can remove the braces pretty easily without causing damage. This allows you to reposition the brace if needed. Take care to align the 1/8” thick brace pieces between the sets of holes, not over them. Take care not to cover up holes or run the piece across the holes. There is enough room to place the brace components between rows of holes. Do worry about spacing the braces equally. You won't see them, and it will very painstaking to attempt it. The inside can be ugly...you won't see anything in there.
Continue Installing Panels
Go one panel at a time, bracing each one as you install it. This gets tricky once you have the last panel on, but not too bad. Once all four panels are on and braced, its time to add the cover details over the slots.
Covering Up Slots
Using my walnut pieces, I use Loctite Gel (the best and only Super Glue I use) to glue these on as covers. They hide the burned edges of the base which poke through the panel, but also help to secure the bottom portion of each panel to the base by locking the panels in. Apply glue to the entire back side of the cover piece, and press firmly against both the panel's face, and the base tab inside the slot.
Step 9: Enjoy Your New Toy!
I hope this tutorial has been helpful in some way to you, or that it has provided some source of inspiration to you.
If there is interest and if I have the time, I would be willing to image map some pictures for interested parties should they want to make their own pattern. You can drop me a line though the site to inquire. This is of course, free of charge.
Check out my Tumblr blog here: http://thatsnotarchitecture.tumblr.com/
and give me a vote in the contest if you like. Thanks!
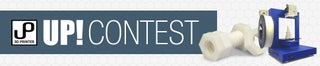
Participated in the
UP! Contest

Participated in the
Lamps & Lighting Contest