Introduction: DIY Folding Knife With Button Lock
Hi! This is my instructable about my homemade folding knife with button lock - that locks the knife in open position.
This is my 8th knife so I can probably say that I know something about knife-making.
It took a lot of time and efford but I am super pleased with the result.
Step 1: First :
Before you start making i need to tell you that this is a very hard build and I think that fortune was on my side with this knife. So if you are a beginner I would recommend you to start with simplier project e.g. small, solid, full tang knife. I worked with iron and wood since I was a child and despite all of this, this build tested my skills like nothing else so far. It was much more difficult than I expected and I had to face new problems all the time. But if you feel like doing it GO FOR IT! It's the best feeling to just have somehing like this on your table, knowing you made it on your own.
Step 2: Info :
There is a sumup of almost everything about this knife
Dimentions : blade : 8cm long
1,3 mm thick
mirror polished
razor sharp
custom etched logo
handle: 10,5 cm long
1,5 cm thick
made from stainless steel and black zebrawood
with button locking system
Materials + costs : old saw used to cut metal - FREE
stainless steel from old washing mashine - FREE
zebrawood - FREE (because my father works with wood colours and got some samples of different type of woods)
another pieces of iron found throughout garden - FREE
so it costed me just time, sanding discs and electricity
Step 3: Making Blade :
Note: some of these photos are not taken from making of this knife but the method is the same.
First you need some good quality, high carbon steel. Good for this are saws e.g. circular saw blade. The best of course is spring steel. You can check if the steel is high carbon steel by grinding it with bench grinder. If the sparks are long and narrow = mild steel, if the sparks divide into several smaller sparks = high carbon steel.
If (as me) you are using some old saw, you need to "slacken" it. This means that the steel is too hard to be worked with so you need to make it soft. The best and most convenient way is to just throw it in fire and leave it in there over night so the steel heats up and than cools down very slowly. (you might need to do it several times).
So let's say you've got some nice, good quality and soft steel. Now you need to come up with the idea of the shape of your knife. For this one I needed to make a special shape so I could make the locking mechanism. As you can see i did several prototypes. Than you trace it onto the steel. Drill the hole (if you cannot cut it, it's still too hard and you need to soften it even more). Than use angle grinder to cut out the rough shape. Even it out with something like bench or belt grinder.
Now clean the steel and get rid of all marks on it. You can again use belt grinder or just like me sanding disc attached to a drill press.
After the cleaning start beveling. I used handheld belt grinder.
I wanted to make "thumb rest" so I took leftover steel and tried different methods. The one I liked the most I transfered using hacksaw and small metal files onto my blade.
Here i stopped because I didn't want to polish it later again if I scratch it.After the handle was done I heat treated it using propane torch to red hot and than quenched it in oil. Than I sanded it with different grid sandpaper and finally polished on a buffing wheel.
Step 4: Making Handle :
Using the exact same method I cut out and sanded pieces of stainless steel. I drilled four holes one for a bolt second for the locking mechanism and other two for spacer.
Step 5: Making Handle :
In front part of the handle I wanted to have steel pieces so the lock would be more steady. I made these the same way as blade and that stainless things. I used 0,5 cm thick steel bar. For the safety pin you need to drill the hole into the back one but not all the way so the spring can rest there! And the front one has smaller hole from outside and bigger one from inside so the safety pin doesn't fall out. And for the bolt I drilled hole with diameter shown on back side of caliper so you can make thread for bolt in there. The bolt I needed I didn't find anywhere so I made one on our old, not precise lathe. Than I made the thread and cut a groove in head.
Step 6: Making Handle : Safety Pin
This thing is the most precious, hardest to make and smallest thing in this build.
Let me first tell you something : My original idea was to make a simple friction folding knife so I designed it and made a blade. But than during a "entertaining" hour of biology I started to think about the knife. I thought that I might make some kind of locking mechanism. After several minutes i got it. I though that i came up with the right idea how to make the locking mechanism. So I made another desing and another blade and hoped for the best. I haven't tried anything like this and was very curios if it's going to work.
During the build I found out that it's not going to be as easy as i expected but that it's still possible.
So using our old, not precise lathe, drill press and many other tools like metal files, sandpapers and more i finally, after around 3 hours, finished the pin.
Let me explain it to you : the front part of the pin (the one without the ring) serves as a block for the blade. It sits on a spring so when you push the other end, it squeezes the spring, comes down and allows the thinner part of the pin to slide through the the blade slot. The ring on the other end serves as a block so the pin doesn't fall out of the knife.
Despite the difficulty of making one I was forced to make two because the first one I made was a bit loose and that caused wobble of the knife. Because this was not machined the blade still has some wobble to it but minimal.
Into the back piece you need to put some sping so the pin comes back and locks the knife - I cut one from ballpoint pen spring.
Step 7: Making Handle : Even It Out
As the title says even everything out using whatever method you prefer - I used combination of everything.
You also want to make a spacer. I made one from another piece of stainless steel. I drilled two holes into the handle and into the spacer and than cut rod which is 2 milimeters longer so I can hammer it down to make it flat.
Step 8: Making Handle : Wooden Part
As i mentioned earlier I used zebrawood. I don't recommend it for begginers because it's really hard wood and it's hard to work with. (I know what I am talking about. I had to make one scale twice on different knife because I didn't know how it's going to behave.) The easiest to work with and still well avaible wood I found is beech. It's quite hard but still easy to grind.
First copy the patern of your knife onto the wood. Than roughly rasp it to shape and using round file make finger slot. Than using different files and sand papers make it round and nice to hold. Use your pins to hold it so it's nice and even.
Step 9: Finishing
It finally looks like a knife. Congratulations! The only thing that's left to do is to sand it with different grids of sandpaper and polish it on buffing wheel.
Now glue the wooden scales with epoxy glue and secure it with pins. But not all the way - just to the stainless steel part so your knife can go in. Now cut those pins to size and sand it flat. For the finish I used some kind of oil. You can use anything from oils, waxes, colours, varnishes and so on.
Because I wanted to mark it somehow I etched my logo to the blade using two nine volt batteries and a vinegar. You pour some vinegar to small container and put there some salt - enough to the point that the salt no longer disolves. Now take a q-tip and dip it into the solution. Than connect two batteries. The positive wire connect to the blade and the negative put on the q-tip so it touches the cotton saturated in the solution. Prepare your blade by cleaning it with alcohol or soap. Use nail polish to cover the area where you want your logo. Scratch your desired image with toothpick. Now you can start etching. (I recommend trying it on some spare metal, because you won't do it well on first time.)
Another good thing is to punch out of plastic paper organiser two small circles with holes inside. Take these and put them between the blade and the steel part of the handle. With a bit of lubrication using WD-40 the knife opens and closes much smoother.
The last thing is to sharpen it. I used wet stone and some rod used to sharpen kitchen knives and finished with a strip of leather. I compared the sharpness with my old razor blade and I must say that it's almost the same.
And that's it. 40 hours of fun, dubstep music, sweat and blood (yes blood I am not the most careful guy so with literally every knife I own, I have cut myself at least once). But it was worth it. The best thing that you can hear from others is when they ask you where you bought it and if your job is going to be making and selling knives.
Step 10: Leather Sheath
For better carrying around I made homemade leather sheath. First take a foam and cut out the inside according to your knife. Than take a piece of leather and soak it in warm water. Than make a sandwich from piece of wood at the bottom than knife, plastic bag so the knife doesn't get wet, leather, foam with hole, full foam and another piece of wood. Than clamp it in vice and let it dry overnight. Than just sew it to another piece of leather, add a stud and belt clip and you've got it. (if you would like to check my more detailed instruction on how to work with leather check my instructable on how to make a leather wallet here : https://www.instructables.com/id/Custom-Leather-Wallet-with-Burned-Logo/.)
Step 11: Photos :
There are just some photos of my finished work I took in nearby forest. I'm going to go to the forest and test my knife at cutting wood and other materials. Hope you liked it. Because this is the prettiest and the most difficult build I have ever done. If you are intrested in anything just ask me in comments. I would love to have some feedback. If this instructable pushed you to make a knife be sure to send me a picture ;)
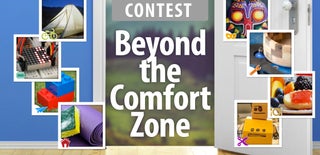
Participated in the
Beyond the Comfort Zone Contest
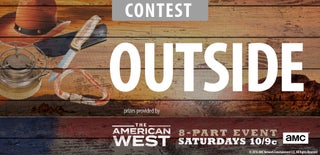
Participated in the
Outside Contest 2016