Introduction: DIY LED ALUMINUM LEGO
Since a lot of people liked my DIY Lego in which I made some Aluminum Lego Blocks. I decided to kick it up a notch in preparation to an Arduino Lego project. Or better, a form of open source mindstorms. So it will be tiney but I will go workshop all out on this.
With this instructable I would also like to demonstrate how fast you can go from an idea to prototype.
Let's do some rapid prototyping (time 22.29hrs gmt +1) go
The goal is to to make a single unit block that:
Is self powered
Can be switched on and off
Gives of light using an LED
Is fully compatible with Lego
Batteries must be easily replaced
So lets work from that.
Step 1: Aids, Tools and Materials
Safety gear:
Earmuffs
Goggels
Blue Gloves (got to have some blue gloves, nitrile gloves work best for most occasions)
Aids:
Some real authentic LEGO from which to derive proper measurements.
Tools:
CNC mill
Clamping tools
Calliper
measuring clocks (the linear and swivel type)
40mm face mill
2mm flat end mill
3mm flat end mill with 3mm shaft (important)
Lathe
Lathe cutting tools
Soldering station
Scissors
Scalpel or exacto knife
Tweezers
Materials:
Double sided carpet tape (no foam core)
20mm diam natural nylon stock
Aluminum stock
10mm diam Aluminum round stock
PCB stock
PCB warm white LED's (you will want a few of these)
Solder
4 Batteries (GPA76 button cell RS components)
Tape
Copper foil (believe mine is brass actually)
Second glue (cyanomethylacrylate glue)
Step 2: Design
As the core of the design we take our batteries. (First pic)
I have put a piece of scotch tape on the - of the battery. This is to prevent it from shorting while I use my callipers to measure it.
Diam: 11.52mm Hight: 5.24mm Thickness scotch tape 0.04mm gives a total hight of 5.2mm
So get out some Lego and by eye find out that the battery would easily fit in a square 4 stub block.
Which would measure Length: 15.928mm width: 15.928 main body hight 9.6mm
As derived from my previous Instructable DIY LEGO.
A standard high power white LED requires approximately 3.5V but from experience it will work just fine if not better with 3V. Lessening the voltage will lower the light output slightly but also will make the LED produce a lot less heat.
This means our block will be two main body hights high 19.2mm.
this means we have 8.8mm left to place connections, the bottom wall and bottom cavities.
We will need hight 2.5mm for the bottom cavities and 1.5mm for the bottom wall (pic 2)
Next I would like to use the PCB board as the main material to make the battery, the PCB is 1.6mm thick.
To allow the LED dial to rotate I will drill a hole in the face connection plate and stick the flange on the back of the LED dial through the hole of the face connection plate.
The pics say it all.
I have added the Sketchup file, please change the TXT extension to SKP before opening.
Tada rough sketches done, time 00.34
Two hours from idea to 3D design including writing the Instructable so far, sleep time.
Attachments
Step 3: G-code and Work Procedure
There are still a few things in the design that I have some thoughts about. The main being to put a cover plate over the LED to make it look nicer. This will be just a circle of clear plastic with a dent in the middle. So although it is not in the design I will prepare a code for it any way.
For making the G-code I use a CAM program, you can find these all over the web.
I found that from scratch starting to work with any CAM program is not easy. But in time when you want to do full 3D structures it is well worth it. Writing the G-code for a 3D build by hand will take years, with cam just an hour or two.
Again this is not the most challenging code making all parts are 2D, that means no warped or curved surfaces in the Z direction its all flat.
Having made the rough designs, I will redesign all the parts in the CAM program. Since I will use 3axis only every face of every part will be a separate operation.
The first step is to start with all components that are from a sheet like stock. This because these will be clamped flat on the table. So these can best be milled before we install the machine clamp. All PCB's can be milled with a 2mm flat end mill in a single step.
The next step would be to make the actual block. This will be done in the machine vise.
From rough to fine, first the rough material has to be faced to perfect little blocks.
Next come the stubs and bottom cavity, with a 2mm flat end mill.
Last will be the cavity in which to fit the batteries.
In all files and operations the bottom left corner will be x,y=0,0
The top of your stock will be z=0
Time to make some chips (11.43 hrs been at it for about 1 hour 45 min today to design all the mill paths)
Step 4: PCB Milling
And stick some double sided tape, the not foamy kind to the underside of your PCB.
And stick it to something flat that you dont mind milling in because the mill will have a break through of 0.25mm. For this I use some Arcrylic sheet left overs, in general this type of material is flat well within a tolerance 0.02mm.
As you can see in the video, I use some aluminum foil as a feeler to zero my Z axis, the aluminum foil I use has a general thickness of about 5microns. (standaard house hold aluminum foil works fine. This again is well with in the tolerance, you can compensate for the foil thickness but it is not needed.
I ended up with a bunch of parts, decided to make a few of each enough for about 4 blocks. In the end I want to make just two blocks (battery limitation) but I figured that since there will be quite some manual manipulation in the next steps. I'd better have a few extra to mess up.
The mill file attached is for the full set you see in the picture. You will need a square of PCB measuring 60x60mm plus some space to clamp it down. If you decide to only double tape it to your something flat you need to clean your surfaces really well otherwise they might fly off during milling.
I would suggest a few good wipes with some ethanol or spiritus (denaturated ethanol) will do the trick.
For those paying attention, clearly I skipped the cleaning step and had to do some touching up of some parts with a scalpel.
The stuff you see on the sides of the pieces is residue from the tape, some white sticky gue. This comes of easy with a few wipes of lamp oil.
The milling of the PCB's took about 20minutes.
Step 5: The Main Block
The final block hast to measure L*W*H 15.928*15.928*21.300mm
For the rough cutting with a hack saw, or in my case a band saw I suggest to make aluminum blocks that are 18*18*23.5mm for easy measure. Why aluminum, well SHINEY :D
Next is to use the 1 step 40mm face mill to face the blocks, after each operation check the measures of the block.
I use a 500mm/min feed @ 7500 rpm (nice light cut) and plenty of coolant.
The program assumes the top of the stock as 0 and will mill away 1mm (-1 mm) you can play within reason to manipulate the final cutting dept.
2 step is milling the stubs on top of the lego using a 2mm flat end mill, left bottom corner is x,y=0,0
Top of stock is z=0.
I use a 400mm/min feed @ 7500 rpm and plenty of coolant.
3 step is milling the bottom cavity, flip the stock 180 deg and mill as with 2 step.
The last step is mill the cavity that will fit the battery
4 step 3mm flat end mill.
Mind you, stubs upward in the y direction see pic and mill time.
Use a 3mm shaft 3mm flat end mill because you will need the clearance for the full depth reach.
Being done with this you can chamfer the edges, I use the back of a scalpel for this. just tracing all the edges.
No need to make your life complex and write seperate codes for this.
Take it for a polish, using a sisal fiber brush @ something like 1200 rpm in the bench drill with some cleaning paste.
Finish with a cotton brush @ 1200 rpm with some polish paste.
Please change the extension from txt to nc if your program does not accept txt file codes.
Step 6: The Turning Flange.
I did this as a free hand on my lathe (check the video)
I made a 3.9mm diam 1.75mm long stub on a 7mm diam flat which is about 0.5mm thick, maybe slightly thinner.
Just dont forget to check if the stub fits the hole of the face plate and protrudes slightly so you have some space for any wobbles and inperfections. No insult meant but humans do make things like a machine, we program the machine fine but if you ask me to cut a pice of pipe square to 0.001 deg, well forget it.
With the lathe it will be sqaure (90 deg angles) but then I start sticking things together with my thick fingers that's when you need some bigger margines.
Step 7: Assembly
I put the total assembly and test video on the first page :D
First off i stacked the two contact plates on top of each other put them in the battery cavity and put the face plate in vertical. That was a really tight fit so I sanded the face plate on the contact edges for a bit more space. It only took a few strokes with some 150 grid carbide sanding paper (carbide waterproof sanding paper really is the good stuff as far as sanding paper goes)
Next I put some solder on the front edges and soldered the face plate to the contact plates.
This makes for a good bond for care full use so I added some second glue on the corners for reinforcement. After all I will never be too old to play with lego and I have clumsy fingers :P
While the contact assembly dried I soldered the LED on it's PCB.
I used some strips of copper foil to lead the contacts from the front to the back. Copper foil is a nice springy material, this can be used.
I soldered the strips to the front and folded them over to the back. I trimmed them so they stick about 3mm towards the centre of the back.
Time to apply some glue to the top of the swivel flange, you will have to be extremely care full to only put the tiniest amount of super glue on the top of the stub. I just used the mouth of the bottle, gently touched it with the top of the sub. You need to be quick, the stub goes through the hole of the front plate to the back of the LED plate.
Hold for about 30 seconds.
Put two batteries together in series and wind some tape around them. Remember the body of the block is made from Aluminum which can short your batteries. So some tape around the sides of the batteries does the trick. You can also turn out a fancy plastic battery sleeve on your lathe. Again I'm taking the lazy way out hehe.
So but the batteries between the plates and turn the LED plate so it makes contact.
Not that a LED is a diode which will only work one way around unlike an incandescent light bulb.
I sanded of the edges of the contact plates for an easier fit, I really designed everything very tight. I always forget that if I assemble something I need a few microns more for my fumbling.
As an after thought I put a nylon disk of 5.5 mm thick on with a 5mm diam 4mm deep hole in it to fit the LED. Just to give it a nicer finish and diffuse the light a bit because this uber bright LED causes you to see spots.
I stuck the nylon on with a hotmelt gun. Almost no other glue will stick to nylon but Hotmelt at the right temperature will almost never come off. For the best adhesion you will want the nylon to get near its glazing point.
Tada done, play time.
Total time, about 9 hours from first idea to two working models, not bad I would say.
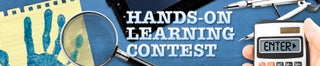
Participated in the
Hands-on Learning Contest
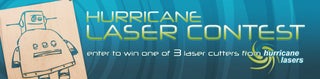
Participated in the
Hurricane Lasers Contest