Introduction: Dr Seuss Inspired Desk
I built this desk in my downtime over a period of about six months. I used four kinds of plywood, a lot of auto body filler, and some very fancy spray paints. It consists of a left and right side, each of which has a wavy protrusion at the top and is connected to half of the desktop. The left side is shorter and contains three drawers, and has a curly footrest. The right side is taller and has six drawers. The desktop comes apart in the middle for ease of moving (and ease of construction!). I painted the whole thing in various shades of blue with a gold accent strip down the middle.
I am fortunate enough to have a CNC router at my disposal, but the parts could be cut on more commonly available equipment a bit more slowly. The wavelike protrusions I carved by hand anyway - at least, by powered hand tools directed by eye. The shape was absolutely inspired by the wavy, silly, curly shapes drawn by Dr Seuss, and I considered painting it plain white with red drawers, but eventually decided I wanted it to be more intricate. I didn't know for sure how I was going to paint it until extremely late in the construction process and I even changed my mind some during the painting process.
Here is how I did it all. There are some things I would do differently if I did it again. I don't think anyone will (or should) make an identical copy, but I hope someone uses some of the ideas in their own way!
Supplies
Materials:
1/2" plywood for the frame
1/4" plywood for the drawers
1" lightweight ply (MDF would work as well) for the wavelike protrusions
wiggle wood for the curved surfaces
vast quantities of auto body filler
8 or 10 colors of blue spray paint and 3 shades of gold
2 part Spraymax gloss finish
premade wood drawer pulls
Tools:
CNC router, but everything I used it for could be done with a jigsaw, tablesaw, and/or bandsaw
jigsaw
powered carving tools (I used Arbortech attachments for angle grinder)
a variety of hand and powered sanding equipment
wood glue
pneumatic stapler
clamps
Step 1: Drawer Prototype
I am small and the desk was planned for a small space, so I wanted to waste as little drawer space as possible on the slides. I decided to try using just prefinished plywood to hold the top and bottom of the drawer sides, because it was the skinniest thing I could think of and I had prefin scrap.
I also wanted the drawer fronts to sit into pockets in the desk front, so they'd be the same level. So I made a single drawer prototype to test my idea. I discovered while assembling it, that the drawer needed to be pressed against the bottom of its slide, while its front was attached, or the drawer front would be too low and not quite fit into its pocket. Finding this kind of subtle issue is one of the many reasons to make prototypes. Overall, it worked well enough that I decided to continue on.
Step 2: Cutting the Frame Pieces
Next I CNC'd the frame shapes: the front and back of each side, the drawer frame parts, the drawer parts (offset 1/16" from the frame dimensions). I didn't cut the desktop yet as I wasn't sure exactly how big to make it. I figured I could assemble the two sides and then test distances to see what I liked.
I also cut the wavy shapes for the curlicues from a 1" thick, lightweight ply. Initially I cut them all exactly the same, to be carved down later.
I didn't cut the pieces for the curvy ends, as I didn't yet know what the right size and shape would be.
Step 3: Gluing the Frame Together
I glued the various parts together using Titebond wood glue, and stapled them to hold it while it dried. First I assembled all the drawer supports, which I had labeled to keep track of them as each drawer is a different size and shape.
Then I assembled the front and back sections with the drawer supports in the middle. I had cut dadoes on the front and back pieces so I would have an exact location for the placement. This was still quite tricky, to get each drawer support end placed in its correct dado slot, while the glue was drying! I recommend finding a second person to help out if you attempt this.
Finally I glued the faces, where the drawer fronts will sit, onto the desk sides. I clamped these rather than stapling so as to avoid having to fill the staple divots.
Step 4: Assembling the Drawers
I glued and stapled the drawers together. There are nine drawers, all different sizes. The bottoms are 1/2" prefinished ply, and the sides, front and back are 1/4" ply. The stapling was thus a little tricky and I did miss in one or two spots and had to clip off and grind down a staple leg that stuck out.
Normally drawers are made with heavier sides and front/back, and a thinner bottom. The bottom is usually slid into a groove near the bottom of the sides, and often not glued down at all but just trapped by the sides. (This is to allow the different woods to move in their own way due to heat and humidity.) The sides sit on the slides, or have separate slide hardware attached to them.
Because I was trying to get the widest drawers possible, I chose to have the walls be thin, to give myself the most width I could. The bottoms therefore would be the structural member, so I used thicker wood there. I set the sides next to the bottoms rather than having the sides rest on the bottoms, because that gave me more glue area, and it was much easier to staple into a 1/2" piece than a 1/4" piece. This is all nonstandard and I will see how well it works over time!
Step 5: Fitting the Drawers
There was enough slop in my construction methods for the drawers and the slides, that not all of the drawers fit exactly into their 1/16" larger housings at first. I did some sanding on the drawers themselves, sides or tops, and some sanding on the frame edges. I was able to get them all to slide well after a bit of this fitting. Took quite a bit longer to do than to explain.
Step 6: Drawer Faces
The shaped drawer faces fit into shaped pockets on the front of the desk. To get the alignment right, I glued the faces onto the drawers while they were in the desk. Since the drawers are shorter than the desk, I padded them at the back by taping on various items, I used rags at first but later changed to using scrap ply. I wanted to have them stick out from the front about 1/8", just enough that I could clamp the drawer face on tightly, but still have the face fit into the pocket. To keep the right offset between the face of the drawer and its surround on the desk face, I stuck folded bits of paper between them on 3 or 4 sides. To clamp, I used a piece of scrap wood big enough that I could clamp it around the edges of the desk facade.
Step 7: Reinforcing the Legs
At this point, both sides of the desk were supported only by the front and rear faces. I added horizontal struts to the left side bottom and footrest. It would thus rest on a flat piece of wood, and I could set a foot on the curly rest when using it. I cut these pieces to length on a chopsaw and glued and stapled them in place.
The right side's braces I did a little differently, higher up from the floor, since this side had kind of faux legs. Later, after I added the curved side panels, I put a solid block under the braces up against each leg, to give it a bit more strength and visual heft.
Step 8: Gluing the Wavy Stock
I glued up the wavy sections separately, all but one piece of each row. I kept them aligned in a jig I had covered with packing tape so the glue would not stick to it. Then I would be able to glue the two wavy curlicue blocks into their corresponding places on the frames later on, rather than trying to glue a series of small parts across a large gap. I kept one section out of the large glueup in case I needed to trim it in any way when gluing them into place on the desk, which I did.
Step 9: Gluing the Wavy Parts to the Frame
I glued the left side wavy block in first. That side is smaller and I could lay it on its back on a table. I used the glue bottle and a drill to prop up the wavy block to fit the desk assembly, and I was able to add a couple of clamps to hold them in place while the glue dried. Since this would all be carved down later, I did not have to worry super hard about the alignment.
Propping up the wavy block on the right side was harder, though, since the right side was enough bigger that it wouldn't easily fit on a table. I had to use a lot of stuff to keep the wavy block in position. I realized also that I wanted to carve away some of the inside of the wavy block for weight reduction, and I removed some of this material on the bandsaw prior to gluing, which was a lot easier than doing it after. I decided to lop off a chunk of the corners too, to reduce the amount of carving I needed to do later. I also was able to create a ledge for clamping, so I could glue one end at a time.
Step 10: Rough Carving the Wavy Protrusions
Back on the left side, the wavy protrusions were still square across the whole width. I drew lines about where I wanted to trim and started in with the jigsaw. I also trimmed the faces that were still sticking out on the right side.
To get closer to the final shape, I next tried a grinder, a belt sander, and a hand saw, none of which worked well for this, before I moved to a powered carving tool attachment for my angle grinder. With this I was able to shape the area down to where I could start sanding to smooth it.
As well as the curvy shapes, I needed a kind of groove to accept the 1/4" wiggle wood that I planned to cover the curved sides with. I made a groove for this purpose on both sides of both sides. That is, on the top and bottom of both the left and right sides of the desk! I had not been able to visualize how the wiggle wood would go on until I got to this point or I would have been able to prepare more for it.
Around this point I decided the desk was too heavy, and that I should have cut holes in the drawer supports for weight reduction. Since the sides weren't on yet, I could still do this roughly with a jigsaw, and I did.
Step 11: Attaching the Curved Sides
Wiggle wood is a special thin kind of plywood that is intended to bend. If you've seen a curved reception desk or shaped counter bottom, there is likely wiggle wood under it.
I cut pieces to the appropriate width, but a bit longer than I needed. I clamped the piece to the sides of the desk, along the curves. Then I drew a line to try and match the groove in the wavy protrusions, cut the wood on the line, and tried the fit again. It took several rounds of trimming and testing before I got the fit good enough to glue and screw down.
I did this for each outside wall, each lower inside wall, and each upper inside wall (under the waves). On the right outside, the groove I'd cut in the wavy protrusions was too skinny to get a good overlap, and I had to extend it with a support block.
Step 12: More Work on the Curvy Sides
On the left side bottom, the wiggle wood didn't want to sit up against the frame except at the edges where I had screwed it down. I added three supports on the inside that I was able to screw the middle areas to. On the curly footrest, the wiggle wood doesn't curl enough. Instead, I attached wire mesh with the intent of later filling this with auto body putty. I also cut and fitted a strip of wood to fill in the tip of the curve.
On the right side, I drew, cut, and shaped curves mimicking a foot, similar to the curved shapes on the front and back facades. I have a tiny jigsaw, designed for carving gourds, that worked quite well for this purpose. I also carved a little with a knife and of course sanded them smooth.
I left the upper inside curved sides open for the moment, as I wanted to attach the desktop first.
Step 13: Filling and Sanding
With most of the desk frame together, and shaped how I wanted it, I started to make it smooth. This process consisted of applying a layer of body putty, letting it cure, and sanding it down. I also was smoothing the carved areas as I sanded. On the areas with wire mesh, I put a cover of masking tape so the bondo wouldn't push through.
Each layer I thought, this will be the last layer, when I sand this down it will be done! And each time as I sanded, I saw areas that just needed a little bit more fill. I didn't count but I'm sure I did 10 or more layers.
The inside of the curly footrest was particularly difficult as I could not reach it well either with a bondo applicator or a sander. I got all the wire mesh and tape covered up, used a microplane to smooth it as well as I could, and left it pretty uneven. I rationalized that it is hard to see, and decided I would paint it a dark color.
Step 14: Desktop
Next I set up the two sides, oriented how I wanted them eventually to go, and played around until I was happy. I made a cardboard template of what I ended up with. I decided to make it a two part top since I hoped to be able to manage the desk by myself, and each side so far I could handle. I cut the two parts on the CNC, and attached them together with screws before fixing them to the two side assemblies. I had a couple friends to help with that or I might not have been able to do it.
Step 15: Last Curvy Walls
With the desktop in place I could add the inner side curvy walls. I used another cardboard template. This area was troublesome, as the wiggle wood didn't really want to bend that much here either and broke on me once or twice. I ended up just attaching the pieces, and applied lots of body putty.
Then I did another 5 or 10 rounds of putty, sand, putty, sand.
Step 16: Primer
I took the desk apart and primed it with standard latex primer. Then I primed it again with auto body filler primer and sanded again... and primed again, and sanded again. Then I filled in tiny flaws with a one part putty. And sanded again.
I taped the drawer bodies, which I was not going to paint, and primed the fronts. Thankfully I judged they did not need the whole filler primer and sanding process.
Step 17: Base Paint
I put the drawers in the frame and painted them a couple shades of gold. Then I set them aside and sprayed a pattern on the frame in shades of blue and green. I had a couple false starts and redid it a few times but ended up with something I was happy with.
I also attached the drawer pulls to a stick and sprayed them blue and green as well.
Step 18: Masking
I wanted a kind of filigree pattern in gold, over top of the blue. I got some thin 1/4" auto detailing tape and made a stripe down the middle of the desk, up one side, through the desktop, and down the other. Then I just started applying the tape in whatever pattern struck me.
When I had done the whole thing I masked off the untaped areas with paper.
Step 19: Filigree Painting
I sprayed over the masked areas with a couple shades of gold paint. Then I peeled off the mask ... I was super pleased with how it turned out!
I put the drawers in again, masked them, and sprayed a filigree in blue.
The last step was to apply a couple coats of a hard shiny finish to protect it from use. Finally I attached the drawer pulls which I had finished separately.
Then I brought it home and put it in my room, and I am typing on it right now.
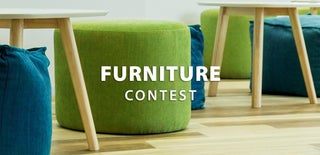
Second Prize in the
Furniture Contest