Introduction: Dry Ice Fortnite Jetpack
I'm sure many of you have heard of the new game Fortnite and its increasingly popular Battle Royale mode. There are many similar games that people prefer or maybe you just aren't into gaming at all. Nevertheless, we can all agree that some items from games just look SUPER cool. One such item that I thought would be fun to make is the jetpack from Fortnite. Paired with a costume to look like a Fortnite character, this could also make for an awesome Halloween costume. (I will probably make one later to pair with this so keep on the lookout!)
And just for an added touch, I decided to add a compartment where you can put dry ice for cool effects. The LEDs at the bottom of the boosters illuminate the fog in the dark to look like the blue flame you see in game. Of course, this is completely optional if you don't want to handle dry ice. There are other alternatives to producing fog, but dry ice just happens to be a cheap option I had available. Commercial fog machines work too if you can get your hands on one - just be sure you have a power source or it has a battery.
This project consists mainly of 3D printing, painting, and some soldering if you are adding in the fog effects. I was lucky enough to have access to a HUGE build volume 3D printer at my local library (over 1 cubic feet actually). Because of this printer, I was able to print large parts, the biggest one being 1 foot tall booster segments on the sides.
Step 1: 3D Printing and Materials
I used Sketchup Make to design the majority of parts, and my brother helped me out with certain parts by using Blender. The first two images are from Blender, the third from Sketchup, and the fourth is the actual model from the game. I'd say we were pretty close aside from some tiny details here and there.
To give a sense of the amount of filament needed, I paid 5 cents per gram and the cost for all the parts ended up at around 75 dollars. It is important to print in PLA or another filament that won't melt in acetone based spray paint.
The other materials you will need are:
- Light Gray Spray paint + primer
- White spray paint (optional but recommended)
- Clear coat spray
- Red, yellow, blue, black, white, green, dark gray/pewter, and silver acrylic paints.
- thin plastic sheeting
- Electrical Tape, packaging tape, masking tape
- Wires and solder
- Hot glue and epoxy
- 25 RGB LEDs or 23 Blue LEDS and 2 Red LEDs
- Arduino board or similar board
- MDF board
I have attached all the STL files to this step. If you have a smaller printer, you may want to split a few of the parts in half. For the most part, all of the parts printed out fine. The only exception would be the middle nozzle and spike which had thin parts that I had to reinforce with hot glue and epoxy.
After the parts were printed, I used a rough 60 grit sandpaper to get rid of any edges and then worked my up the grits until I smoothed out the parts and the scratch marks were smaller than the filament thickness. I also sanded along the layer lines so the paint looks normal when I applied it.
Attachments
Step 2: Primer
I used a spray paint and primer 2 in 1 so that the paint is a bit thicker and it covers the plastic better. I spray painted all the parts light gray, except for the four tank pieces. Those parts are meant to be red so I just spray painted with clear coat. I didn't have enough light gray PLA to make the rest of the jetpack so I used dark gray as well. To make lighter colors show up better, I used a first light coat of white primer, then went over for a second coat of light gray. You will see this same technique being used for the acrylic paints later.
Step 3: Yellow Acrylic Paints
The jetpack has yellow stripes that angle away from the center. First, I taped the two halfs for each booster together using masking tape. Next, I made a horizontal line of tape just above the indentation and below it as well (First pic). You can see in the second picture that the tape wraps around and is perfectly straight. I then used strips of masking tape that I had cut in half to make the stripe pattern. I spaced out each strip approximately one inch apart and I made sure to press the tape to the surface even over the areas that had rivets or other features.
The Yellow paint is much brighter than the gray underneath so I first painted with white acrylic paint and then painted over again with a bright yellow paint.
After the paint is dry, I took off the tape and spray painted it with a clear coat. This makes the paint look shiny and brighter, but also protects it from eroding off.
Lastly, I used a fine tip paintbrush and painted over all the rivets with a pewter gray color. It is basically dark gray with some mica power to look like a dark shiny metal. If you need to use masking tape for this, make sure the clear coat has dried and cured so it doesn't peel off with the adhesive.
Step 4: Red and Copper Acrylic Paints
The fog box clip is another part that needs to be painted by hand. It is possible to also use spray paint for any place where I used acrylic paint, but details like this is hard to cover evenly without messing up surrounding colors.
This part has many crevices so I spray painted it light gray first. Then I painted the outer rims of the coil and the switch plate dark gray. The switch itself was painted bright red, and I used a copper paint on the coils. You can use the second picture for reference. Quick Tip: If you want shiny paint, just add a bit of mica power to it. Adding brown mica powder to light brown paint should get a copper color. I just happened to have a copper shiny paint anyways so that is what I used.
As with the other acrylic paints, I painted over with clear coat again to protect it and make the colors show up brighter.
Step 5: Blue-gray and Green Paints
The middle nozzle is a bluish gray color and the spike is a greenish tint of the same color. To make it, I mixed around blue, dark gray, white, and black paints together. The blue and gray paints got me close to the desired color and the black and white paints helped to increase lightness or darkness. Adding both black and white paints also decreases the saturation of color and made it more gray. This step is mainly trial and error and I could only compare the paint color I had to the actual game model image.
The spike is a similar color with a greenish tint, so I tried replicating the recipe for the blue-gray paint and added a bit of green to it. Since both colors have a grayish component to it, I didn't need to paint with white first.
As always, spray paint with clear coat afterwards.
Step 6: Fog Box
The center box in the jetpack is a 6" wide x 5" deep x 9" tall box and the topmost 1 inch is reserved space for electronics.
If you want the fog function in the jetpack, You need to make a 6" x 5" x 8" box and add the additional one inch afterwards. The reason why the extra inch is separate is because I didn't want the water vapor to touch my power source which I stored there (A phone power bank that gave USB power to an arduino).
I used 1/4" MDF for this part because It is easier to cut and sand than wood in my opinion, and it won't splinter easily while being cut. Because of the thickness, the dimensions for each side changed a bit. Here are the parts which you will need to cut out, the right column is for fog and the left is just for the jetpack without fog.
- Two 6" x 8" panels | Two 6" x 9" panels
- Two 6" x 4.5" panels | Two 6" x 4.5" panels
- Two 7.5" x 4.5" panels | Two 8.5" x 4.5" panels
- Two 5" x 1" panels (not needed for non fog)
- One 5.5" x 1" panel (not needed for non fog)
- One 5" x 6" panel (not needed for non fog)
I used a coping saw because that was the one I had on hand, but any other saw with a thin blade will work as well. Any saw that is based on tearing instead slicing will rip the edges of the MDF. A bandsaw would be best for the straight cuts.
If you did this by hand, you will need to sand the edges flat with a rough grit sandpaper. Also, have a vacuum cleaner nearby to pick up the sawdust. This much cutting and sanding tends to make a mess.
Step 7: Assembling the Fog Box
Since there will be fog produced in this box, there shouldn't be any leaks. To prevent leaks, I sanded all the edges flat and roughly assembled the box together. I then used a pencil to mark on all of the parts where I needed to remove some material so the box will look like one piece when glued together.
Next, I used hot glue to hold the parts together and using some sandpaper, I went over all the surfaces to smooth it out. You can tell by the pictures that it makes a lot of dust and it gets everywhere. I used a vacuum to clean it off. Glue, especially hot glue, will not work well on a dusty surface. Before finishing the box, I used a can of compressed air to blow off all the dust. You can also use a damp towel to wipe off any excess dust. Then, I glued the inside edges of the box with some clear two part epoxy. Once that is cured, you can even take off the temporary hot glue and replace it with epoxy. This is will make the box stronger since it holds the weight of everything, and it will make it airtight so dry ice fog wont escape from the box and rather go out through the jetpack boosters.
Step 8: Fog Box Hole
Next, make two holes in the fog box. This will hold the boosters as well as allow fog to escape into the boosters. You can tell by the Sketchup design that the hole placement isn't in exact inches. I made the hole in the side of the box about 2 inches deep from the front face, and 3 5/8 inches high from the bottom face. I then traced out the circle for the booster's pipe by holding the 3D printed part to it.
This is where you need to use a coping saw. First, I drilled a small hole in the center, then passed the blade of my saw through. I reassembled the saw back together and cut out a circle and repeated for the other side. Then, I used a 60 grit sandpaper to smooth the sides and let the booster's pipe just fit in. If you find that there is too much material to sand but too less to cut a larger hole, use a dremel with a sanding bit, or the curved side of a wood file.
Step 9: Added Space and Painting
I wanted a smooth surface inside the compartment for electronics, so I painted the fog box first, then made the extra one inch, and then painted again. This isn't really needed but my power bank happens to have suction cups on it that would stick better to the spray paint surface than MDF.
To paint, First apply a primer coat (White is preferred) and wait for it to cure. Use a high grit sandpaper such as 1000 grit and sand smooth. Then apply a second coat of light gray paint. I wanted my box's surface to be super smooth so I did a total of 3 coats and a layer of clear coat on top. When it was dry, it was almost as smooth as a glass surface!
I then glued on the other parts for the top one inch and did the same steps as earlier to make sure it fit perfectly. I then spray painted it light gray and added clear coat.
Step 10: Center Plate Lighting
Originally, I was going to wire all colors of RGB lights to my arduino, but I realized I just don't have that many analog pins. It was easier if I stuck to just the primary and secondary colors. The color of the center plate is closest to the secondary color of aqua (blue plus green).
First, I glued a plastic sheet into the three holes on the center plate by just tracing it out. I used the plastic packaging from a box of spinach but anything similar is fine. I lightly painted over it with gray paint so you can't see into it, but the light can still come out. Quick tip while painting, Hold the can of paint 2 feet away and start pressing the nozzle while aimed away from the part, then make a light stroke across the part, and finish by releasing the nozzle. This will create a light mist that will settle evenly similar to how snow falls. I learnt this from experience after trying multiple techniques - even using the compressed air to blow off any excess paint.
I hot glued 3 LEDs into each of the back cavities of the center plate. I bent down the common wire, which is the voltage pin for me. Make sure that you know which LED you have, common anode or cathode, and how it works, current sinking or current sourcing. Depending on which one you have, programming to light up LEDs may be different. Since I am not using any code in this project (so far - I might add code in later upgrades), the only difference between the two LEDs is which pin is positive and which one is negative. If it doesn't light, just try switching the power source around.
I then wired all of the common wires together using a green wire. It is important to stick to the same color for wires as much as possible to avoid confusion. I then insulated them with electrical tape and wired all the green and blue pins together (red wires). Lastly, I bent all the wires down and taped it so I could start assembling.
First, glue the fog box clip part (the one with red and copper paint) onto the bottom of the fog box. Then, the center plate aligns with it on the curved surface. It should still be taller than the fog box clip once glued in place (see last pic). I then wired the green and red wires through a small hole I drilled in the upper one inch compartment. It will eventually go to the red tank and power the LEDs.
Step 11: Outer Jetpack Halfs
The outer jetpack halves are the ones that have the fan for moving the fog. Ignore the fan part of this step if you aren't using fog. You will need to replicate this and the following two steps for both sides of the booster.
I used some silent cooling fans - the exact diameter doesn't matter as long as it can fit in the jetpack at some height (since the width of the jetpack varies by height). Mine is a bit more than 5 inches across.
First, break off the outer casing by using diagonal cutters. Usually, the fan's motor is connected to the frame by a few plastic rods. Just break it as far away from the center as possible because it will give you more space to mount the fan. Next, hot glue it into the casing so that it is perfectly horizontal when the booster is held vertical. Make sure that the fans spins freely even when you place the other half of the booster on top. Make sure the flow direction is out of the jetpack as well.
For the LEDs, hot glue 3 of them near the bottom spaced evenly. To make the entire jetpack have even lighting, put them on the second, sixth, and tenth flat surface. When you do this for both halves, the LEDs at the edge are spaced evenly as well.
Next, I wired all the ground pins together and all the blue pins together, and then soldered them in place. I used hot glue to reinforce the solder joints and to hold all the pins to the casing. Then, I soldered two thin wires to the ground and voltage wires and taped them up past the fan all the way past the top of the casing by around 6 inches. The thinner the wire, the less risk there is that the fan will hit the wire as it spins. I also wired two wires to the fan and brought it past the top by around 6 inches.
Lastly glue the middle nozzle at the bottom using the thin parts on the side. The part where it starts to shrink in diameter should line up with the end of the booster casing. Then, glue the center spike in the middle nozzle. In my opinion, it is easier to glue the spike into the middle nozzle first so that I can easily rotate it and see if it is tilted to a side.
Step 12: Inner Jetpack Halfs
The inner parts have clouded plastic similar to the center plate. The only difference is that it can be placed behind the hole and doesn't have to be cut to the perfect size. After learning some lessons from the previous part, I chose to use the spray paint method and get an evenly coated piece of plastic, which you can see me doing in the first two pictures.
Then, cut out two rectangles on the parts of the plastic which is evenly coated and see through. Using tape and/or hot glue, secure it behind the hole. Make sure not to block the hole with tape otherwise a shadow will show up when the LEDs are turned on.
Next glue an LED at the top and at the bottom as showed. Through trail and error, I realized that that the center LED showed isn't really needed and makes the other LED colors appear dim. The original plan was to make the top one blue, the middle white, and the bottom red. This should give the gradient color that the actual game model has. Since the plastic is cloudy though, it works fine without the center one and the gradient is still visible.
I also placed 3 LEDs at the bottom the same way as the other half of the booster. I wired the ground wire of these with the other two LEDs and passed the wire through the top by 6 inches. For the voltage wire, I connected it to the blue pin of all of the LEDs, except the bottom one for the gradient light - I connected it to the red pin for this one. Then pass this wire up through the top by 6 inches as well. Lastly, I loosely placed a piece of tape over the gradient light from the inside so that stray light from the red doesn't show up at the bottom where the "flame" of illuminated fog is supposed to be blue.
Step 13: Assembling the Boosters
I used clear epoxy for this step although you can feel free to use any other glue that works well for plastic. Just don't use hot glue because it will cool down by the time you are ready to attach the two halves together.
Spread the glue along the edge of the casing halves and add some the to the middle nozzle's connecting spikes (although if you are quick, hot glue is fine for the middle nozzle). Then, sandwich them together and quickly make sure everything is right - 3 sets of wires should be coming out the top, the jetpack casings should be flush where they meet, the middle nozzle and spike should be aligned straight, the yellow stripe patterns should match, and the fan can still spin. I used a can of compressed air to blow into the jetpack and see if the fan can spin.
Then, use rubber bands to hold the part together. It just so happened that a roll of 3M electrical tape will fit just over the top of the casing where it can make sure the parts fit flush (You can see it near the top of the third picture).
Lastly, if you can prop up the boosters such that the pipe fits through the hold in the fog box, you can go ahead and glue it together using epoxy. Make sure you use a strong epoxy because this small pipe lifts the entire weight of the booster. If you can't prop it up, wait for the boosters' glue to cure first so that it doesn't get misaligned in the process. The fourth picture is probably one of my favorite ones as I saw my project finally coming together. I also used epoxy to glue the tank clip to the very top center of the box. Make sure it is centered with the tops of the booster casing as well. You don't need to add the red tank just yet, I just did it to see what it would look like.
Step 14: Final Wiring
The red tank has just enough space for an Arduino Mega (or any smaller micro-controller of choice). The arduino has ports for 3.3 volts and ground and that is what will be powering the LEDs. The Fans are powered by two 9 volt batteries.
First, you will need to make a hole at the end of the tank. The reason why it wasn't in design is because the slicing software I used messed up the prints for some reason when there was a hole on the end. If you use a drill, make sure you have a hole saw bit and not a helical / screw shaped bit. A helical bit will try and pull up the plastic and it can crack or bend the PLA. A dremel with a sanding bit works perfectly for making a hole in the tank. I just used the dremel and made a semi-circle shaped hole in the ends of each red tank piece such that when they are put together, it is a perfectly circular hole. You may need to go over it with a rough grit sandpaper to smooth up the edges.
An easy way to connect the fans is to first wire both of them together inside the red tank, keeping in mind the polarity of the wires. Then solder it to a 9 volt battery clip. If you don't have a 9 volt battery clip, you can carefully dismantle a used 9 volt battery and get the top plate and solder two wires to it. Next, using diagonal cutters, break the battery clip in half so that each piece can still be attached to one of the leads on a 9 volt battery. Then just connect two 9 volt batteries together and connect the clips to the open leads. I chose to wire a slide switch in series so I can control when the fan is one by just removing a piece of the tank and flipping the switch.
Using a drill, I also made a hole at the bottom of the tank so I can slide in a USB cable to power the arduino. The other end of the cable is connected to a power bank that is inside the top compartment of the fog box. The wires for the center plate can just fit through the seam of the tank if the wires used are thin enough, otherwise it can go through the same hole as the USB power cable.
Lastly, to make my jetpack look more like the in game one, I wrapped all the wires coming from the top of the boosters to the red tank in black electrical tape.
Step 15: Finished
The jetpack is now complete!
In order to make the fog, I used Velcro tape to secure a water bottle in the fog box. Then I added a few large chucks of dry ice an then filled up some hot water, which starts to make thick fog as shown in the third picture. Lastly, I used double sided foam tape to secure the back panel to the box and make an tight seal.
If you want to use this as a prop or a Halloween costume, you will also need to put some straps on the back to wear it similar to a backpack. I found that a strip of packaging tape folded lengthwise is a nice width and strong enough, but I reinforced it with electrical tape to be safe. I then used some hot glue and more electrical tape to connect it to the inside of the fog box. Make sure to tape it flat past the edge of the fog box so that the fog box cover can still fit in place and make that tight seal.
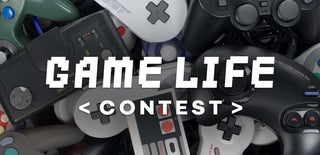
First Prize in the
Game Life Contest