Introduction: Easy Air Engine
Have you ever wanted to BUILD your very own ENGINE!!? Engines fascinate me. I love them all, but the older they are the better. I designed this engine based on another I found here on instructables, but simplified it to the point that my 8th grade students can build them using only a drill press, a welder, and other basic hand tools. NO MACHINING whatsoever!
This style of engine is commonly reffered to as a "Wobbler" or "Oscillating Cylinder" engine. According to wiki- "An oscillating cylinder steam engine is a simple arrangement which does not require valves to direct steam into and out of the cylinder. Instead of valves, the entire cylinder rocks, or oscillates, such that one or more ports in the cylinder line up with corresponding ports in a fixed port face or in the pivot mounting." (http://en.wikipedia.org/wiki/Oscillating_cylinder_...)
My engine is capable of running on as little as 2 p.s.i. and as slow as roughly 125 RPM. It can also run much, much faster, as you can see in the video clips. Some days I will hook it up to the air turned down low and just sit and listen to the relaxing chuff-chuff-chuff of the engine.
Before you get started, you may want to check out a few other instructables on various kinds of engines.
This is the one that inspired me to design the Easy Air Engine. Very similar but VERY machining intensive.
https://www.instructables.com/id/Air-Engine/
My SUPER easy Toilet Paper engine:
https://www.instructables.com/id/Toilet-Paper-Engin...
My Penny Engine:
https://www.instructables.com/id/Penny-Engine-micro...
And a pop can stirling engine I built using an instructable that is apparently MIA...
http://dorkpunch.blogspot.com/2011/11/popcan-engin...
Had enough? Ready to start!?
Supplies
Pretty simple list of parts to build this engine. Please keep in mind that the metal and parts used are NOT required to build this engine- it can be made in just about any configuration with just about whatever scrap you have laying around the shop. However, you will have to adapt and modify things to fit.
SUPPLIES
Metal needed:
1- 4" x 4" x 1/4" steel- base plate.
1- 1 1/2" x 2" x 1/4" steel- crank support.
1- 1" x 2" x 1/2" steel- valve plate.
1- 1/2" x 1/2" x 2" steel- cylinder.
1- 3/8" round x 1 3/4" steel- piston.
1- 2 1/2" round x 1/4" brass- flywheel. This can actually be made out of anything- I have even made them out of flat plate in a square.
1- 1/8" x 2" welding rod- crankshaft.
Parts needed:
1- Zip tie (small)
1- 1/8" inner dia. hose, roughly 6" long
2- 6-32 nuts
1- 1/4"-20 bolt, 2" long
1- 1/4"-2- nut
1- 1/4" washer
1- 3/8" x 1" spring
1- 1/8" roll pin
TOOLS
Layout Tools
Steel Rule
Dividers
Scratch Awl
Center Punch
Square
Sharpie
Hand Tools / Etc.
Hammer (yes, that's first on the list!)
File
Vise
Hand reamer
Hacksaw
Drill bits:
3/8", 1/4", 13/64", and 1/8"
Taps & Dies:
1/4" 20 tap, 6-32 tap, and 6-32 die.
Sandpaper
Cutting Fluid (I'm using ATF)
Power Tools
Drill press (could substitute a regular drill if you think you can drill perfectly perpendicular holes)
Welder ***PLEASE NOTE*** This engine could be built without a welder, but you would have to use some different pieces of metal and adapt the design. The main reason welding is a part of this project is so that my students actually have the opportunity to USE a welder to MAKE something.
Hand Drill
Not required but handy:
Belt sander
Welding booth supplies- Magnets, clamps, table, etc
Metal cutting band saw or abrasive cuttoff saw- really speeds up cutting out all of the parts.
Sandblaster for cleaning up parts after welding and assembly.
Step 1: Crank Support and Measuring and Drilling Processes
Lets start off with a very simple piece to practice our layout skills. The Crank support is made from the 1/4" thick 1 1/2" x 2" piece of steel. It has one 1/8" hole drilled through it as shown in the blueprints.
LAYOUT.
1. We are using regular old Sharpie as our layout fluid- makes it easy to see scribe lines and easy to clean up. Color half of one side using the sharpie as shown in Picture 2.
2. Using the steel rule, mark an arrow 1/2" down from one edge as shown in Picture 3, then scratch a line through it using the square as shown in Picture 4. Remember, MEASURE TWICE, cut once! Check the line you just scratched and make sure it really is at 1/2" (Picture 5).
3. Using the steel rule, measure over on the line you just scratched 3/4". This should be the center of the line. Mark an arrow as shown in Picture 6. CENTER PUNCH the mark as shown in Picture 7.
DRILLING.
1. It is VERY IMPORTANT that all of the holes be drilled perpendicular. If they are off, the engine can still be made to work but it is very hard to do and the engine won't run smoothly at all. Before drilling, use the square to make sure that the table on your drill press is perpendicular to the spindle of the drill. Check it in multiple directions!
2. Notes on drilling: We are using the "pretty darn" method of accuracy here. Meaning, when someone ask how close you are to the specified tolerance, you say "Pretty darn!!!" (Thanks Kent!). This is also known as the Calibrated Eye method. We are assuming (this should be verified) that the drill bit is perpendicular to the drill press table, and that our vice is also in alignment.
3. Clamp the Crank Support in the vice, and using your Calibrated eye align the edge of the metal with the top edge of the vice as shown in Picture 8. You can set the vice on your drill press table and again check with the square to make sure the surface of the metal is perpendicular to the drill bit. Once you have verified that it is, you probably do not need to do this every single time you clamp something in the vice but it will be way more accurate if you do.
4. Drill! Add a few drops of cutting fluid, make sure your drill press is set to the correct RPM, and cut the hole. (Picture 9) Once done drilling, MEASURE AGAIN to make sure it ended up in the right place!
5. Using the hand reamer, de-burr both sides of the hole. Be careful not to wallow it out though, this hole is the "bearing surface" for the crankshaft and if it gets loose the entire engine gets wobbly.
Done! Set this aside for now, we'll need it again later.
NOTES.
If the hole got mucked up somehow, don't throw this piece away! Simply flip it over, re-mark and re-drill a new hole at the opposite end of the metal.
Step 2: Valve Plate Part 1 - Layout and Pilot Holes
Here's where we start to get a little fancy. These holes have to be VERY precise for the engine to run well. If the holes are a little off, the engine will still probably run just not as well as it could. If the holes are too far out, the engine isn't going to run at all. That said, if my 13 yr. old students can do it, so can you!
LAYOUT
1. Sharpie for marking fluid again...
2. We will be making 3 holes in the face of the plate and one on one edge. The first hole is the pivot hole. It is marked on the face is a marked as follows:
Measure down from the end 1/4" and mark a line. Find the center of the plate using a ruler, and mark a line down it using the square.
The second two holes on the face are intake and exhaust holes and are marked as follows:
Measure from the same edge of the plate down 3/4" and mark a perpendicular line across it using the square. From the center line you marked previously, measure OUT on each side 1/8" and mark these two holes.
3. Center punch these three holes. See Picture #3.
4. Mark the exhaust hole exit on one side of the valve plate (either side will work) as follows:
Measure from the same top edge down 3/4". Mark a line across the side. It should line up exactly with the line we used to mark the intake and exhaust holes. Find the center of this line (should be 1/4" from either side) and mark it. See Picture #4.
5. Center punch this mark. See Picture #5.
*** VERY IMPORTANT***
The hole on the side is the EXHAUST HOLE. The hole closest to it on the face of the valve plate DOES NOT GET DRILLED ALL THE WAY THROUGH!!!! Please read the drilling instructions very carefully.
DRILLING
1. Mark the exhaust hole on the face of the valve plate. This hole is the one that is closest to the hole we marked on the side. I like to use a paint pen and put a dot next to the center punch mark. DRILL THIS HOLE LAST!
2. Clamp the Valve Plate in the vice, and using your Calibrated eye align the edge of the metal with the top edge of the vice as shown in Picture #6.
3. Drill ONLY the pivot hole and the intake hole!!! These two holes go all the way through the valve plate.
4. Prep the drill press to drill the exhaust hole as follows:
-Align the drill bit with the hole
-Raise the table up until the tip of the drill bit is in the divot made by the center punch as shown in Picture #7
-Tighten the table
-Set the depth gauge on the drill press for 1/4" as shown in Picture #8.
5. Drill the exhaust hole! Again, it is ONLY 1/4" DEEP, it does NOT go all the way through!
The face is done, now to finish the exhaust hole.
6. Turn the Valve Plate on it's side as shown in Picture #9
7. Prep the drill press as explained in step #4 above, but set the depth gauge to 7/16".
8. Drill the hole. You should feel the drill break through into the other hole we drilled. Don't go too far!!!
NOTES
Check that the exhaust hole was drilled all the way through by using something like a zip tie. Push it into the hole and see if it comes out the other side, as shown in Picture #11!
Step 3: Valve Plate Part 2 - Tapping the Pivot Hole
In the last step, we laid out and drilled the pilot holes in the valve plate. Now we're going to finish it off by drilling and tapping the pivot hole.
DRILLING
1. Clamp the Valve Plate in the vice, and using your Calibrated eye align the edge of the metal with the top edge of the vice as shown in Picture #1.
2. Change the drill bit from the 1/8" to the 7/32" drill and adjust the RPM of the drill press accordingly.
3. Re drill the pivot hole.
TAPPING
1. Clamp the valve plate in a vise as shown in Picture #2.
2. Using a 1/4"-20 tap, thread the hole. Tips for using a tap:
-use cutting fluid!
-make sure the tap is PERFECTLY aligned with the hole! Look at the work piece and tap from multiple sides, and make sure the tap is perpendicular to the surface. See pictures #3 and #4.
-Break the chips! Turn the tap in and when you start to feel resistance, stop, and back the tap out a half turn. A good rule of thumb is to go about a half turn in, back it out a half turn, go a half turn FURTHER, back it out, repeat until the tap is all the way through.
-CHECK the threads with a bolt! It should thread in easily. If it's rough, run the tap through it again once or twice. See picture #6.
Step 4: Cylinder
This part is a little tricky. We'll be putting a big hole in a little piece of metal and again, we need the holes to be very accurately located and cut to the correct depth.
LAYOUT
1. Sharpie for marking fluid again...
2. We will be making 2 holes on one side of the metal and one in one end. The two holes on the side are marked as follows:
Mark a center line along one side of the metal. This would be 1/4" from one edge. From one end, measure down 1/4" and mark the Pivot Hole. Then measure down from the same end 3/4" and mark the Air Hole.
On the OPPOSITE end, mark a line from corner to corner diagonally across the end, from all corners, to make an X. X marks the spot- double check that the center is 1/4" from all side. (see picture 2) This is the Cylinder hole.
3. Center punch the 3 holes. See pictures 3 and 4.
DRILLING
1. Align the piece in the vise using our Calibrated Eye method, leaving the side with 2 punch marks facing up.
2. Drill both holes with a 1/8" drill bit as a pilot.
***VERY IMPORTANT***
The PIVOT HOLE goes all the way through. The AIR HOLE DOES NOT- it only goes half way through the piece - to a depth of 1/4"
3. Drill the end hole for the cylinder. It DOES NOT go all the way through- it should be 1 1/2" deep. Align the workpiece in the vise by gently aligning it with the drill bit as shown in Picture 6. FREQUENTLY allow the bit to come all the way out of the hole to clear chips or you WILL break the bit!
4. Leave the cylinder clamped in the vice and change the drill bit to the 23/64 bit. Change the drill press speed to match.
5. Re-drill the Cylinder Hole.
6. Change the drill bit to the 3/8" ream and adjust drill press speed to match.
7. Ream Cylinder Hole.
8. NOTE- CYLINDER WILL BE HOT!!! Remove cylinder from vice and replace it with the other two holes facing up. Make sure the cylinder is square with the vice, using your calibrated eye method.
9. Change the drill bit to 1/4" and adjust drill press speed to match.
10. Drill the Pivot Hole to 1/4". DO NOT drill the Air Hole - it stays 1/8".
11. Clean and de-burr the part.
FINISHING
1. We need to file a portion of the cylinder (see picture). About 1/4" below the Air Hole, use a file to cut a line roughly 1/16" deep.
2. File the LOWER portion of the cylinder. DO NOT file on the end with the holes! The goal is to remove a little material so that the whole cylinder won't rub on the valve plate.
3. Using a belt sander, polish the upper half where the 2 holes are. If it polish part of the lower half, you didn't take enough metal off and will need to file a little more.
NOTES
Clean all of the shavings out of the cylinder when you are done!
Step 5: Piston
LAYOUT
1. Sharpie for marking fluid again...
2. We will be making 1 hole at the end of the piston. The hole on the side is marked as follows:
Mark an arrow 1 1/2" from one end of the piston.
3. Center Punch the hole by setting the piston in a partially opened vise as pictured.
DRILLING
1. Align the piece in the vise using our Calibrated Eye method, leaving the side with the punch mark facing up.
2. Drill the hole with a 1/8" drill bit.
***IMPORTANT*** The drill may wander off to the side since the surface is curved. If this happens, stop drilling. Loosen the vice, and rotate the piston so the started hole is straight up again. Continue drilling.
FINISHING
1. Both ends of the piston will need to be filed so the edges are not sharp. It can also be helpful to clamp the piston in the drill press and sand it with some emery cloth while it is spinning. Just don't take too much off!!!
Step 6: Crankshaft and Flywheel
CRANKSHAFT
Order of Operations:
1. Cut metal to approximately 3” long.
2. Measure 1” from one end and bend 90 degrees
3. From INSIDE OF THE BEND, measure 3/8” and bend it back 90 degrees
4. Trim long end off so there is only about 1” on that side.
5. Thread the long side using a 6-32 die.
FLYWHEEL
Order of Operations:
1. Cut bar stock to approximately ¼” thick.
2. Find the center.
3. Mark the center with center punch and drill using a 7/64” drill bit.
4. Tap the hole using a 6-32 tap.
Step 7: Welding
Welding the crank support to the valve plate is a little tricky, but fairly straight forward.
The video demonstrates the process of aligning the parts, tacking them together, and fully welding the parts into one solid piece.
Step 8: Assembly and Testing
Assembly and testing requires a bit of patience. But it is SO satisfying when the motor finally takes off and RUNS! The video goes over a few tips and tricks to tweak the motor to run better.
Step 9: Final Words
I hope you've enjoyed this Instructable! These engines are a lot of fun to make, and my students have built hundreds of them with a pretty high success rate.
Keep in mind, this is a great START to an engine, and with some time and effort, I've been able to make many more refinements to this design that makes it run even better.
I've even built a 2 cylinder version of it!
I can't wait to see what y'all do with this. Thanks for watching!
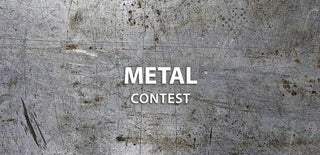
Second Prize in the
Metal Contest