Introduction: Faulty Bosch 18V ProCore Battery - Issues, Diagnose & Repair
In this video I'll investigate and solve the issue why Bosch ProCore 4ah battery which isn't taking a charge and gives no power to the tools. Also, I'll show the BIG BIG issue why it is a terrible idea to try to "jump start" faulty battery.
How I did it - you can check by looking DIY video or you can follow up instructions below.
For this project you will need:
Materials:
- Pure nickel strips 0.3mm of thickness Link to product!
- Faulty cell replacement, in my I used case Samsung INR21700-40T
Tools:
- Screw driver
- Multimeter
- Rotary tool with grinding and cutting disc Link to product!
- 5S JST balance wire Link to product!
- Smart charger (I used an awesome ToolKit RC M7AC Link to product!
- Soldering iron
- Spot welder https://malectrics.eu/
Step 1: The Situation
Your Bosch ProCore battery is displaying no charge, isn't providing power to the tool, or accepting it from the charger. After a quick test, you found that it has a very low voltage - and you're contemplating using a redneck trick: connecting a pair of wires to a healthy battery and using it to jump-start the low-voltage one. STOP! Just get rid of this stupid and dangerous idea. I'll demonstrate its dangers later in this video. Instead, grab a screwdriver and open the case to investigate the issue.
Step 2: The Issue
From the very first look - there's nothing major; just this small crack in the case. Let's check the voltage of individual cells. And here is our problem, we have two cells that are completely dead and should be replaced.
Step 3: Why "Jump Start" Battery Is a Terrible Idea!
Before diving into the repair, let's revisit that "genius" idea of jump-starting. Just imagine, you will connect the 18V battery to the 12.6V battery. 12.6V - because only 3 cells are working and that’s their full state of charged voltage.
So, where should the remaining voltage and current go? In the best-case scenario, it converts into extreme heat on some components, potentially causing spot welds or melting. In the worst-case scenario, all that excessive energy could find a way to escape instantly with big fireworks. So, do not attempt anything similar!
Step 4: Disconnecting the Cooper Tabs
To extract the faulty cells, I need to remove the copper tabs first. Using a rotary tool with a round ball burrs diamond bit, I carefully grind the spot welds until I reach the surface of the cell. A gentle lift with a screwdriver breaks the last holding part, allowing the copper tab to be removed by twisting it. Just like that. Applying the same technique on the other side worked as well. It might seem complicated, but the key is not to grind into the cell. Take your time, proceed slowly, and with a light pass of the grinding bit – everything comes out nice and safe.
Step 5: A Bit of Cleaning
After a couple of minutes, the cells were free to come out of the housing. While they are still held firm - we need to clean those spot weld leftovers. Once again, a rotary tool, cutting disc on it, slow RPM, and working with patience did the job very well.
Step 6: Removing Bad Ceels
Those cells sit inside quite snugly, requiring a moderate amount of force to push and pull them out. Do you see those small flex cable ends? This is a clever Bosch solution to monitor and balance individual cells. That’s why cells have no insulation wrap. The cell body has exposed a negative battery terminal, and through those flex cables, battery electronics will measure the state of charge of individual cells. That's why cells sit very snugly, ensuring proper contact between the cell and flex cable.
Step 7: Replacement Cells
Bosch packs ProCore batteries with Samsung INR21700-40T cells. So, I bought a replacement pair of the same model. There are two minor differences between them - the new one has insulating wrap and is reclaimed from some previous battery pack. So, some spot weld leftovers are exposed, and we need to address that with a rotary tool. Reclaimed cells bought from a trusted seller mean you are getting cells that aren't used. They have zero cycles on them, but due to quality control or other issues, the battery pack of those cells was disassembled, cells were tested, and they are sold as reclaimed ones. So, it's a great option to get unused cells with a nice discount.
Step 8: Placing New Cells
Removed the insulating wrap and pushed cells into the case. And yes, it required a bit of force to do that.
Step 9: Connecting Cells Back
To connect the cell back in series, I will not use those copper tabs. They are 0.3mm thick, and this is too thick to spot weld with my current spot welder. Instead, I’ll replace them with two layers of 0.2mm thick pure nickel strips.
Step 10: Checking If All Goes Well
Those spot wells look nice and clean, let's check if the battery electronics accept that. And they do, nice!
Step 11: Balancing Cells
One last step is needed before assembling the battery back. We need to ensure that each cell has the same voltage. In our situation, cells are slightly off. I could fully charge an individual cell with a smart charger or any other 4.2V power source, but it will require 5 iterations and take too long. Instead, I'll use this 5S JST balance wire soldered to each cell. This allows me to charge and balance all cells with a single charge cycle.
To charge and balance the cells, I’ll use my recently purchased M7AC smart charger from ToolkitRC
Connect the balance wire to the balance port and alligator clips to the positive and negative battery terminals.
Step 12: A Bit Information About the Charger
The charger gets readings from the battery of total and individual cell voltages. So it means the balance wires were soldered properly and the charger could balance the cells.
For charging, I leave LiPo mode. For cell selection, I also leave it on auto, but it's possible to set it manually. We are using the charge feature, and it balances cells by default. The end voltage per cell is set to 4.2V, and let's increase the charge current up to 3 amps. And let's start. The charger kicks in, pushing all 3 amps to the battery. While it's charging, we can check some live data of individual cell voltages and even internal resistance, which is super cool. For those unfamiliar with this parameter, in general, internal battery resistance describes how healthy it is. In my case, everything looks spot on!
I've had it for not longer than a month, but I’m very impressed by its size, power, capabilities, and features. I think it is worth a quick review video in the near future.
Step 13: Reassembling Back
The battery was fully charged, and the cells are nicely balanced now. Let's desolder the balancing wires and assemble the battery back for a final test on tools and the original Bosch charger.
Step 14: How Does It Works?
The state of charge indicator shows that the battery is full, and it powers the impact driver as it should.
Let's check if the original charger will accept the battery and initiate the charge procedure. The internal charger relay click signals the start of the charge, and the blinking LED confirms that.
Step 15: Some Final Thoughts
So, those two $8 worth cells saved us a $50 worth battery. I would call that a great success. And yes, you may say that some additional know-how and skill were needed to accomplish this. That's exactly why I’m creating these kinds of videos. I’m willing to learn new things by myself, gain experience, and share the accumulated experience with everyone.
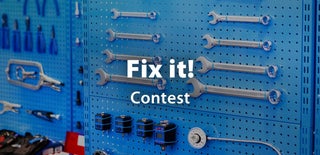
Participated in the
Fix It Contest