Introduction: Faux Wood Cardboard Shelving
This shelf started as an attempt to organize the chaos that has become my dresser top. Being the only free horizontal surface in my room, it tends to collect a lot of loose stuff, especially my wife's collection of cigar boxes. I also used this shelf as an excuse to use up left-over hexacomb cardboard from previous projects. This is the third project in my hexacomb phase, you can find links to the other two projects here:
Step 1: Materials and Supplies
For this project you will need:
- 1" Thick hexacob cardboard. It's hard to say how much as I pieced mine together from scrap, but I would say a full sheet would be more than plenty
- 1/2" & 1/8" foamcore. Various scraps to use as shims and spacers
- A full sheet of chip board
- White Glue
- Faux Wood Paper or other decorative paper of your choice (I picked mine out at Flax in Oakland)
- A good hobby knife, with a full set of new blades (I used the small Olfa snap off blades)
- 3 foot metal straight edge
- A metal square that you can cut against
- Containers of various size, eg. cigar boxes, mason jars, tins
Step 2: Measure & Cut Strips
You first need to Identify the measurement of your deepest container / item. This will establish the overall depth of your shelf. Mine was a Band-Aid box that I use to hold pencils and pens at 8.5". Cut long strips of hexacomb cardboard at this depth. The longer the better.
I was piecing my strips together from scrap of the cardboard chair project, so I had to splice some pieces together to get enough length, but with a fresh sheet, you should be able to cut longer cleaner strips more easily.
Identify the overall width of your shelf. Mine was based on the width of my dresser which is 3'- 0" wide, but this can varry. Make sure you have a strip for the base that is at least that length.
Identify the overall height, this is a looser number. I identified my height by stacking up my boxes and adding an inch between each box. I then added 6" just to have some room to grow if needed. I ended up with 26" tall. Make sure you have at least 2 strips of hexacomb cut to the height for the sides of the shelf.
Step 3: Laying Out the Containers
Lay out your boxes using some scrap hexacomb to provide the spacing and do your best to get it all to fit together without any gaps. Now, some gaps are inevitable, so use the thinner foamcore materials to either fill in gaps or to act as a thinner wall if there isn't enough room for a box. Getting this layout down accurately is key. Try to make your spacing consistent. I left about 1/6" additional room all around each item so everything can fit back in easily.
I unfortunately did not snap a photo of the boxes shimmed into place, but you can see in the photo of the shelf with the unfinished edge the varied material thicknesses I used in order to get it all to work. You can see I had to get looser with the material thicknesses as I got closer to the top and there were less boxes to choose from ;)
Step 4: Cut Strips to Length and Join
Starting with your base and bottom row of boxes, line them up and cut into the base strip for the vertical pieces to fit in. Use a square to be sure you are cutting perpendicular across the strip. Don't cut all the way through, just through the top layer of the hexacomb and core, then hog it out by hand leaving the bottom surface intact. I did a sample piece in the pictures above.
You can now set the bottom surface flat down onto a level table, and slip vertical panels into these slots to act as the walls. Make sure you have two taller side panels to go at the ends, these will bound your shelf. Push the wall panels down into the base and slip your boxes in between. You may need to tape the end panels in as they don't have material on both sides to hold them in.
Using the boxes as your guides, mark the desired height of the wall pieces. These will be jointing into the next horizontal surface above, so take them out, mark a line 1" (for the top joint) + 1/16" (offset width) above the marked line, and cut the inner walls to length. For the side walls, mark a line 1/6" from the marked line and another line 1-1/16" up from the marked line. Score and hog this out like you did on the base, the horizontals will tab into the sides to keep them whole.
to glue the pieces together. fill the scored side with a lot of hot glue, then push the vertical panel into the trough. Make sure it is pushed all the way down and the joint is square before the glue sets. Puddles are good, a bigger glob of hot glue will stay liquid longer, and you will need the time to adjust the squareness of the joint. The excess should fill the voids in the edge of the hexacomb, and any squeeze out can be shaved away with your knife afterwards. After the joint sets, check that it isnt opening up. If it does, squeeze more hot glue into the gap and squeeze it back shut to dry.
Continue this process by adding and joining the parts, using thinner materials where needed, until You have your structure together. Use the long stock strips you cut at the beginning and cut them to length using you metal square as a guide.
Step 5: Cover Edges With Chipboard
In order to glue the final paper onto the piece, you need to seal the open cells of the cardboard's edge. To do this, I glued the whole front face of the shelf to a full sheet up chipboard, then cut out the cells.
First, make sure you have a flat surface large enough to fit the whole chipboard sheet and lay it down. Now, lay your shelf down on its back so the front edges you are going to glue are facing up. Pour white or a thin wood glue into the edges. dont flood it, but be very generous. Now flip the shelf face down onto the chip board sheet and put a bunch of weight on the back to hold it down. Let it set for a day or two to dry, give it the time it needs.
What happens is the generous amount of glue you filled the edges with will flow down and settle onto the chipboard inside the edge. This pools inside the edge against the chipboard and makes a strong connection. Even if the hexacomb edge isn't perfectly smooth and doesn't sit perfectly against the chip board, the glue will bridge the gap and you will have a smooth front edge when you are done.
Once the glue is entirely set, cut around the edge and remove the excess chipboard. The best way to do this is to cut from the back with just a blade, pressed flush against the hexacomb. Cut a slit at either end of a long straight edge, then flip the piece over and cut from the front with your long metal straight edge, connecting the two slits that came through from the back. This method ensures the straightest final edge.
After the front is finished, repeat the process to finish the top two edges of your sides. I also covered the two sides of the shelf with chipboard because they were starting to get a little wavy with all the horizontals that were jointed into them.
Step 6: Cut Open Each Cell
Now you have a shelf with all of the cells closed, so you have got to cut them out again. Feel them out with your finger, then cut a small hole into each cell right in the middle, careful not to hit the edge. Carefully enlarge these holes until you have about an extra 1/8" of chipboard around the opening.
Now, press a blade down perpendicular to the chipboard edge until it stops against the cardboard behind (see the pictures above, they will be clearer). Do this in several locations along the edge, then using your straight edge, connect the lowest extent of these lines with a final cut. They should pop out like teeth and you are left with a nice clean & flush edge.
Repeat this process with all of the cavities until they are all clear. You can stop here if you like the paper look. It's not to shabby, and a bit more honest use of materials. But I wanted to go full faux wood, DIY IKEA don'chya know :)
Step 7: Cover With Wood Patterned Paper
To glue down my faux wood paper, I continued with white glue. I started with the whole front, similar to how I added the chipboard. Spread an even layer across every part of the edge, then smoothed the paper down onto the front and cut out the cells. Save the paper cut from the cells and glue them down onto scrap hexacomb. You can then cut these out and slide them into each cell to act as a back stop to each container. I cut mine a little large so they pressure fit into the holes, but you could also glue these in from the back to make them permanent. Make sure they are set to the right depth first though, each one will be different based on the container.
Continue the process of gluing and trimming the wood paper around the outside of the shelf. I use a fresh Olfa blade pressed flush against the perpendicular edge to cut the paper flush. Always use a new blade for this and it will slide through like air and make a very clean cut. I then came back and rounded down the edge of the paper with some pressure from the back of a fingernail. This helps to blend the papers edge over its neighbor and makes it look more continuous.
I did not glue wood into the cells that will have square boxes in them because those surfaces will not be visible, but some of the round containers needed to have the interiors coated with the wood paper as well. I did these by spreading glue on a strip of the paper instead of the hexacomb surface, then carefully wrapping that into the interior of the cavity, burnishing it into the corners with a metal straight edge. Let the material overlap at the top of the cavity to be less visible. (You can see this process with the mason jar cavity pictured above)
Step 8: Load Up and Enjoy Organized Chaos
Set up your shelf and load it with your things. Enjoy the beauty of your orderly dresser, it certainly is quite a sight to behold. look at all of that space in front of the shelf just waiting to be covered with more stuff :0 Ah well, it looks nice now anyway...
Thank you for reading,
Happy making Instructablers!
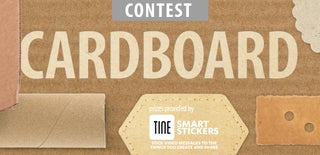
Participated in the
Cardboard Contest 2016