Introduction: Magnetic Mod Shelf
This is a handy little shelf for keeping entropy at bay in the kitchen, and a magnetic back means it can be shifted out of the way when needed. Constructed from hexacomb cardboard with a maple veneer skin, this is a relatively cheap and light weight project, and It can be built with little more tooling expertise than some handy exacto skills. A nice weekend project for the ambitious papercrafter!
This is another in a series of projects I've been making out of Hexacomb cardboard. It is a great material, super light and strong, I have used it to make a seat, a cubby shelf, and a boat form in the past. Wrapped with a sturdy skin, it can last for quite some time; In fact it is similar to the material used in the ubiquitous $10 Lack Ikea table.
Disclaimer: My camera is stolen half way through this project, so the first half of this instrcutable is pieced together in miniature, or from previous projects. If any confusion results, please ask in the comments and I will clarify.
Step 1: Getting Started
You will need the following ingredients for this project:
Materials:
- 1/2" thick hexacomb cardboard. Salvage if you can, it is often used in the packaging of large items for shipment. Larger art supply stores may have sheets
- 1" thick hexacomb cardboard
- hot glue sticks
- Maple Veneer, I used two 2' square sheets from my local art supply shop. Get the kind with a paper backing for extra strength
- wood glue
- Yes paste
- Scrap Cardstock, I used an old cereal box
- Magnets, rare earth are the strongest if you've got them, you can also get a handfull of the 1" round flat black ones.
- A wood dowel for the paper towel bar
Tools:
- Hot Glue Gun
- A nice sharp hobby knife with spare blades, I use Olfa snap off blades, they are extra easy to replenish.
- A solid metal straight edge
- Any squares or blocks you can use to set 90 degree corners. I have been known to improvise with a nice solid hard cover book
Step 2: Cutting Out Your Parts
Using the measurements included on the previous step, we will first cut out the three main parts of the shelf from your hexacomb cardboard.
With your hexacomb sheet on a flat sturdy cutting surface, cut out the forms with a long solid straight edge. The material is thick, and your cut can get wobbly if you cut all the way through in one go. Instead, what to do is cut through one side of the material, making sure your knife goes through the back at the beginning and end of the cut only. Then flip the material over and cut through the other side of the material. With the through cuts you marked on the first pass, you will have two points to connect when you cut the reverse.
Once the pieces are cut, measure, score and remove the material for the connection joints, as illustrated in the photos above. The back piece will get all of its sides hogged out, and the sides will get slots hogged out to catch the shelf.
Step 3: Bending the Sides
The initial inspiration for this project was the nice radius that resulted from bending hexacomb over a hard surface, it is almost too easy!
Line up the edge piece on a hard surface, overhanging 4 inches, and bend it down. Flit this against a 90 degree inside corner and score the crunched up portion of the inside surface (see images). Pull off the additional scrunched up surface, fill up the hexacomb with hot glue, and set it up against a 90 degree block to set.
Step 4: Embed the Magnets and Assemble
With the help of a sharp blade, cut out pockets in the edge of the Back piece. Slip in the large black magnets, being sure that they fit all the way inside. Add a dab of hot glue and set them in for good, still being careful to check they fit clear all the way into the material.
I also had on old neocube that was already missing a good portion of the balls, so I salvaged a few more and hot glued these into the edge of the Top and Sides piece. Make sure that they are on the back side, without the radius corners.
Apply liberal quantities of hot glue to the back edge of the Top and Sides piece and set it into the back piece. The larger the glob of hot glue, the longer working time you have before it sets so I always use a lot then trim off the excess after it sets.
You can go ahead and glue in the shelf portion now as well, using liberal quantities of hot glue as before. Make sure it is flushing up with the front of the Back and Sides piece, and landing straight on the bottom edge of the Back piece. (my apologies, no pictures of the shelf getting blued in)
Step 5: Skinning the Edged With Cardstock
Using whatever cardstock you can salvage, cut strips and hot glue them to the exposed open edges of the Hexacomb. I cut mine a bit large, then trimmed them back after they were set to be sure everything flushed out.
Let the final edge be the self. The material is 1/2" thick, but you will skin it with a 1" strip to give a lip to your shelf. First skin the inside of the shelf with the veneer (process covered in the next step), then skin the top inside half inch of the shelf edge and glue that to the shelf edge (see images)
Step 6: Skin With Maple Veneer
The veneer skinning process is next (unless you are a staunch Kix brand loyalist). It is a straightforward process, but it takes a steady hand and patience.
Spread the wood glue with a spare piece of cardstock, making sure the whole surface is covered. As with the hot glue liberal is ok here, excess can be wiped away. Cut the veneer a bit larger than needed so you can trim it flush once dry. Burnish once set down to get any air pockets out.
I had to use two pieces of veneer to wrap the entire length of the sides and top, so there is a seam at the top. use some tape to pull this joint tight to hide it as much as possible.
The joint at the front of the bent portion takes an mitered cut. If you cut the top portion extra wide, it will wedge down into the mitered portions on either side and you can get a nice clean seam.
Once it is all skinned and dry, hit the edges lightly with a fine sandpaper to blend them together. It helps to make it look more like a solid piece of wood.
Step 7: Cut in Your Dowel
Next we will cut in a void in order to slide in the dowel for paper towels. I used the center of the 2" radius on the bottom of both sides as my center marker. I used and angled piece of wood stock because I had it left over from a previous project, but I think a round dowel would be a little more in style with the shelf, and a bit easier to carve out of the shelf sides.
You will want to cut clear through one side, then only through the inside surface of the opposing side. This will provide a stop for when you slide the dowel through. Slide in your dowel, mark the length, and cut it to size.
Step 8: Tacky Up the Back
The shelf is just about finished, looking good. If you stick it to the fridge though, you will notice that it tends to slide down when weight is added. Something must be done! We need to coat the back with a tacky finish so it sticks better. not wet sticky, but more like how a vinyl sticker sticks to a window.
The best solution I found from my crafting supplies is Yes! paste, a paste I've used in the past for binding books. Its pretty good, but not as great as rubber or vinyl, I am open to suggestions.
Apply a thin coat to the back surface of the shelf, let it dry for a couple days (its a slow drying paste), then you will have a solidly tacky surface on the back of your shelf. After sitting on the fridge for about a half minute, the shelf is well set and you can load it up as much as you'd like.
Step 9: Stick and Enjoy
There you have it, a nice weekend project for the ambitious papercrafter! (Or the shopless furniture maker). Load it up and enjoy.
Thank you for reading, happy making! Please, if you have enjoyed this instructable place a vote for in the shelving contest!
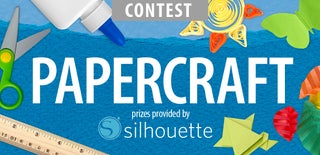
Participated in the
Papercraft Contest 2017
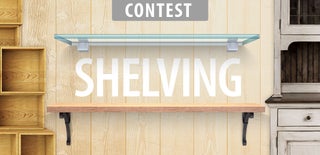
Participated in the
Shelving Contest 2016