Introduction: Flatland Furniture - How to Cut, Bend, and Glue Metal
A parametric furniture series produced using only sheet materials that can be produced on demand. The series was geared towards a designer-producer business model. The project was based on broad concepts of post-industrial design with a focus on customization and digital fabrication. The design requires no special molds to form the parts and all components can be readily ordered from any water jet/laser cutting shop. The furniture uses no mechanical fasteners, instead, all parts are formed and powered coated separately. Then fastened using industrial strength 3M epoxy and clamped until cured. This method allows for multiple color combinations between parts and an almost magical feeling since there are no visible attachment methods.
If you have some basic experience in CAD or illustrator, draw up your own design!
Check out the presentation version of the project on Behance.
Supplies
- 4mm sheet steel
- CAD or 2D program to design you parts
- Water jet or metal laser cutter supplier
- Metal brake
- Powder coat supplier
- 3M Scotch-Weld epoxy
Step 1: Cut Your Parts Out
Most of my time was spent perfecting the Solidworks model and trying out several design configurations. More time can be spent designing because manufacturing the parts is actually a quick process. I had access to an older water jet cutter and I think It on took a few hours to cut out all of the parts for a pouf, a side table, and a large chair.
I would probably use a metal laser cutting supplier next time. I had found a supplier but they took too long to get back to me with a quote since it was quite a small job. The cost was totally reasonable and the edge finish would have been a lot better compared to the water jet.
Step 2: Bend Them to Shape
Working with metal is quite different than working with wood. There was a lot of trial and error - bending a little to far, bending it back a couple degrees, etc. until I got the parts to fit together nicely. I was pleasantly surprised at how forgiving the steel was.
Measure twice, cut once, is a good tip for woodworking. But I'd say that steel is more of a bend a little, bend some more until it's close enough. There are CNC metal brakes that will give you pretty much perfect bends, but I didn't need that kind of precision for this project.
Step 3: Powder Coat
Some things are best left to the professionals. I found a local powder coating shop and got a good deal since I used the same colors they were prepping that day for a larger job. Normally you can specify exactly which color you want by looking at a chip sample set at the shop or by selecting a RAL color.
Powder coating is a great method to add a surface finish and color to your metal project.
Bonus:
While I was waiting on the powder coating to be done, I popped into a fabric shop close by and snagged a few meters to make some cushions with. I had actually never used a sewing machine before this project but with the help of a friend we dove right in. Don't be intimidated to try something new! I won't give tips on sewing here (since I have none) but the cushions were a learning experience and turned out alright for my first go at it.
Step 4: Glueing Metal, Is That a Thing?
Adhesives are used in tons of products. 3M has a product lines of industrial strength epoxies that hold the products you use everyday together. I ordered some 3M Scotch-Weld for this project. It is important that the two part epoxy is mixed at the correct ratio. They sell an applicator gun and a mixing tip so you don't have to worry about it. Just pull the trigger on the gun and a perfectly mixed epoxy squirts out of the gun.
Since I had never worked with this adhesive before, I just free-styled a bit when applying it to the parts. I clamped everything together and let it cure for 24 hours or so. When I took the clamps off... I had an insanely strong bond and a finished set of furniture that was ready to use.
Step 5: Final Result
This was an interesting project where I experimented with some new manufacturing techniques. I would recommend everyone to try building some furniture with metal - it is very forgiving and the results are very rewarding.
It's been a few years since I built this furniture and I still use it everyday! The 3M epoxy has held up phenomenally through several moves and tons of guests testing its limits.
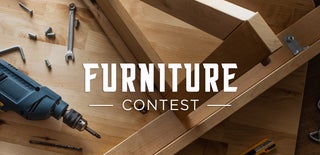
Participated in the
Furniture Contest