Introduction: Fully 3D-printed Lampshade
Hello world. This is my first instructable in a very long time so please bear with me.
Quite some time ago now, an old and ugly lampshade came down in the office-space of my apartment. With the light in the northern hemisphere fading rapidly due to the approaching winter, it’s due time to stop living in the dark like a complete caveman and create a light fixture to have light again in my room.
I currently live in an rental apartment, and I think the light fixtures that came with the apartment are
as old as the building itself, that would be, from the 70’s. So old. It goes without saying then, that the replacement of the fixtures is far overdue.
The idea for the dodecahedra lampshade has been in my head for a long time already and I saw this as the prefect opportunity for a perfect weekend project.
Supplies
We will need:
- a computer capable of running fusion360
- a 3D-printer with your filament of choice
- calipers to accurately measure things
- and a small screw terminal for attaching the lights to the main voltage
- (3) Light sockets with cables and lights. Preferably the light sockets have a bolt at the end of them, this makes them more easily installed in the 3D-printed lamp shades.
- wire strippers or good skills with scissors
Step 1: Instructive Video
Because a picture can say more than a thousand words, I have tried to post as many pictures as possible. And because a video says more than a thousand pictures, I have also made an instructive video on YouTube about this ible. You are welcome to read through or watch through my instructions.
Step 2: Designing the 3D Models: Dodecahedron
You often hear that, to really enjoy 3D printing, you should be able to make your own 3D models. Even though I personally do not agree with that statement, it is also true that basic 3D modelling should not be so hard as many people believe.
To prove that 3D modelling of basic shapes can be easy I will explain here how to make a dodecahedron lampshade and the ceiling canopy needed for this project.
Because a picture can say more than a thousand words, I have tried to post as many pictures as possible.
A quick search on the internet yields this information: a dodecahedron is a regular polyhedron, built up of 12regular pentagons at an angle of 116.6° to each other. This is important information to get started.
Designing the Dodecahedron
[1] We start by making one of the pentagons. In F360 there is a build in function to generate regular polygon. You can find this function in the Sketch menu > Create > Polygon > Circumscribed or inscribed polygon (does not matter which at this state). To generate this polygon, we take the origin as middle point of the polygon. The size of the polygon does not really matter at this point.
It is also not strictly necessary to fully constrain this sketch. It is however a good practice to do this. in order to achieve a fully constrained sketch, we make one side of the polygon vertical or horizontal by going in the sketch menu > constraints > Horizontal/vertical.
After drawing the polygon, finish the sketch.
[Picture 1]
[2] From this sketch create a patch by going to the surface menu > patch > and then selecting the sketch of the polygon we just made > Click "OK"
The patch now appears as a flat body (=patch) in the bodies folder of the browser.
[Picture 2 and 3]
[3] Now we will take our design into the third dimension: We copy the polygon patch-body and paste it. This will create an exact copy of the polygon. This will also reveal some options on moving and rotating the copy we just made. [Picture 4]
If we would rotate the object now, it will most likely rotate around a corner. This is not what we want, we want it to rotate around an edge. Luckily we can select the specific point around which to rotate with the "set pivot" option in the "MOVE/COPY" pop-up. Click "Set pivot" > Select any edge > Click the green check mark to confirm. [Picture 5]
Now we can rotate the copy of the polygon around that edge. Remember that the angle is 116.6 degrees. [Picture 6]
[4] Next we can either repeat step 2.3 until we have the complete dodecahedron. OR we can be lazy and use the "circular pattern" tool in the Surface Menu > Create > Pattern > Circular Pattern> Select the upright pentagon and the Z axis around which it should revolve > create 5 copies. Et Voila, that finishes the first layer of pentagons. [Picture 7 and 8]
[5] Now we have to repeat the steps 2.3 and 2.4 again to create the next layer: Copy one pentagon and rotate it around one edge to an angle of 116.6 degrees and make 5 copies in a circular pattern to make things easy for us. [Picture 9]
[6] The last pentagon will close off the dodecahedron we are building. This last pentagon is put into place by copy pasting one of the pentagons of the last layer just as we did in steps 2.3 and 2.5 [Picture 10]
[7] If everything went according to plan, you now have a bunch (12) pentagons as flat bodies (patches) floating in the 3D space to make up the sides of a dodecahedron. In order to make this a solid body we will stitch the patches together:
In the Surface menu > Stitch > select all patches (all edges should turn green) > Click "OK"
This turns the bundle of patches into one solid body. [Picture 11]
[8] Up until now I have claimed that the scale does not matter. Now that we have a solid body we can check how large it is. For this go to the Objectfolder in the browser and look at the properties of the dodecahedron. In the Properties pop-up there is a section called bounding box, here we can find the dimensions of the smallest box that our model could fit in theoretically.
This box should fit inside you print volume while still being large enough to be able to incorporate a light. In my case I have made my model way to large, the largest dimension of the bounding box was 600mm, while my printer can only handle 230mm at the most (let's say 220 to be on the safe side). To know the needed scaling factor to get our model within our printer volume we divide the printer dimension by the largest dimension of the bounding box. (In my case this is 220/600 = 0.36666...).
To scale our model we go to the Solid Menu > Modify > Scale. There we can enter "0.36666" or we can just be lazy and type in the formula "220/600" and let F360 calculate it for us.
The bounding box is now at most 220, our maximum dimension our printer can safely handle.
[9] This solid body is made hollow with in the Solid environment > Shell > Click the top surface and create a shell of a reasonable thickness. I have chosen to input here my nozzle diameter, being 0.4mm since I will be printing in vase mode. [Picture 12]
[10] The last thing we need to do to our 3D model is putting a hole in the bottom to fit the cables through and screw in the light socket. For this we first have to measure the bolt at the end of the light socket (9.5mm in my case) and make a hole at the exact centre of the underside. The Hole making function should snap to the centre of the pentagon (the origin). [Picture 13 and 14]
Step 3: Designing the 3D Models: Ceiling Canopy
Apparently the little cap of a light that hides the cables going into the ceiling is called the "canopy" of the light.
This 3D model is far easier: we are going to make a hollow half sphere with a hole in it.
[1] First, roughly measure the hole in the ceiling. This was 7cm in my case, so to be on the safe side I have made a canopy of 9cm in diameter.
[2] Sketch a circle of 90mm with the origin as centre point. Also add a straight line that goes straight through the circle's middle point. Again, this sketch does not need to be constrained, but it is good practice to do this. [Picture 1]
[3] To make this sketch into a half sphere we use the Revolve function. To make this work we select one half of the circle as "Profile" and the line we drew through it as "Axis" to rotate this profile around. It will suggest revolving it for 360 degrees, but we only need 180degrees to create a half sphere. [Pictures 2 and 3]
[4] Also this design is hollow. This is done in the same way as the dodecahedron: with the Shell function that can be found in the Solid Menu > Modify. I have chosen for a more reasonable thickness of 1mm. Printed in PLA this will still be flexible enough to have some wiggle room, but be strong enough to not break that easily. [Picture 4]
[5] For the hole in the design, we first will make our initial sketch visible again. We will use the circles centre point as a guide to place our hole in order to make sure the hole goes straight through the middle of our design.
Solid Menu > Hole > place hole on centre point of 9mm (= rough guess of the diameter needed to fit cables though) > make the hole long enough to intersect with the rest of the body. This can be done in the Shape Settings > Extends to > and then selecting the rest of the body. [Picture 5]
Step 4: Print Your Designs
Dodecahedron
To keep things interesting I have printed three dodecahedra, all in a different colour: Red, Blue and Yellow.
The dodecahedron are printed in VASE mode with 3 bottom layers. Not only is this therefore a fast print, it also makes the lamp shades themselves very thin, making the light shine through easily.
Canopy
I have printed the canopy in 'normal' mode. I succeeded in printing this model without the use of supporting structures by setting the part cooling fan to maximum throughout the entire print. The inside shows clear signs of steep overhangs, but due to the 1mm thickness of the model, the outside is still as it should be.
Step 5: Assembly and Mounting
The assembly is pretty straight forward and will probably vary with the design of your light socket screw.
[1] pull the cables of the light socket through the hole in the dodecahedra, and secure the light sockets by screwing them in with the bolt. [Pictures 1,2 and 3]
[2] Pull the cables through the hole in the ceiling canopy, making sure the inside of the half-sphere is facing away from the dodecahedra. [Pictures 4 and 5]
[3] Connect the wires from the light sockets in parallel: Identify the wires coming from each of the three light sockets, take one wire from each of the sockets and twist those together. Do the same with the other three wires.
You should now have two triplets of twisted wires (try to say that 3 times fast out loud). [Pictures 6, 7 and 8]
next, fasten the two twisted ends into the screw terminal.[Picture 9 and 10]
Check if the wires are in there securely by giving them a small tug. They should be able to support the weights of the lampshades with the lights installed in them. Speaking of which, you can now twist in the light bulbs if you want.
[4] TURN OFF THE CIRCUIT BREAKER!!!
Electricity is not a joke, turn off the correct circuit breaker BEFORE coming near any live wires. [Picture 11]
[5] Find a sturdy step to stand on in order to acces the wires in the ceiling. Screw the main voltage wires in the other end of the screw terminal. This should also be secure enough to support the weight of the entire assembly.
Stow away the excess cables in the ceiling and slide up the canopy to hide these excess cables.
[6] Go and switch on that circuit breaker and go and marvel at your new lights.
Step 6: Lessons Learned
- Although the geometry of the lampshade is every bit as good looking as I envisioned, my decision of printing the dodecahadra in different colours now makes them very suited for a childs bedroom, but less for an office space. The colours really brighten up the room, but also block off a lot of light as well. This means that the light given of is quite dim. Also the general light temperature is very deep into the reds which, again, is not ideal.
Next time I would print all the polyhedra in white. More boring, pobably, but there will be more light.
- something to keep in mind. Being 3D printed lampshades, the lamps inside them can only be low-powered LED lights. A regular incandescent light bulb will quickly heat the plastic, malting it and creating a fire hazard.
- Overall I think this was a very fun and educational weekend project. It involves some basic and easy to understand Fusion 360 work and it uses two different printing techniques.
Thank you for taking the time to look at my instructable
Have a good day!
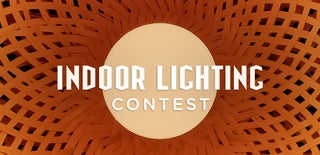
Participated in the
Indoor Lighting Contest