Introduction: Geometer's Triangle Pen
I found myself with an assignment to build whatever I wanted out of metal, with full access to Stanford's Product Realization Lab, a fairly extensive shop.
With the opportunity, I wanted to make something I could use and admire every day. As a student, I decided to make a pen, something that would both get a lot of use as I worked and serve as a work of art on my desk.
It's not just any pen, though. The body has a triangular cross-section, making it much more comfortable to hold and write with than an ordinary, round pen. It's beautifully geometric, is bead-blasted and anodized blue-grey, twists to move the ink in and out, and has my insignia etched into the back. It slides into a blue, powder-coated base that I cast out of aluminum.
The base is in the shape of something called a constant-width solid, which is a shape that has the same diameter everywhere yet is not a sphere. It's my favorite shape, because it's a reminder that we often imagine constraints on things that are not really there, just as we might imagine that a solid with constant diameter must be a sphere. That's what thinking outside the box is: discarding imagined or conventional constraints, while keeping real ones. What could be a better place for a reminder of that then in a base for a pen, an instrument of recording ideas.
It's quite a challenge to get all the triangle-based geometry in this project. In this Instructable, I'll walk you through the steps needed to build the pen from scratch. Whether you're planning on building something similar yourself or just browsing for fun, I hope you enjoy the read!
Besides being for fun, this project is an entry for the 3D Printing and Metal Contests. I would really appreciate your vote!
**Please click on the orange vote ribbon in the upper right-hand corner of this page if you enjoy this Instructable.**
Step 1: Design Overview, Required Materials, and Tools
I've attached the plans and some screenshots of CAD models, above.
I'll talk more about materials and equipment requirements in a bit, but the pen and top were machined out of a piece of 6020 aluminum bar, while the base was cast from a 3D printed pattern.
The pen body is drilled out, and the pen spring and ink cartridge sit against the end of the drill hole. I cannibalized a twist mechanism from a broken pen. The twist mechanism is epoxied into the cap and has a spring that holds it tightly into the pen body. Three tiny, 3mm ball plungers are press fit into the triangular cap aligned with the triangular pen body. In a round pen, the alignment doesn't matter--a rotated circle is indistinguishable from the original--but the triangles would look strange if they didn't snap into alignment.
Here's a SolidWorks animation to help illustrate how the parts interact with one another:
I've also included a screenshot of the bill of materials I made when starting the project, which should give you a sense for how much the project costs, what to buy, and where to buy the parts. For the pen parts, I gutted a fairly nice but broken pen that I had lying around at home. Please see the last photograph, if you're curious.
As far as tools go, you'll need access to a pretty fully-featured shop to have enough equipment. Here's a rough list of the tooling required in addition to that on the bill of materials. You might be able to get by with less, but it's best to do things right.
- 3D printer with at least a 4"x4"x3" build area
- Scroll saw and spindle sander
- Access to a foundry or a foundry job shop nearby to contract out
- Milling machine
- Rotary Table
- Angle Table
- 2x Hex Collet Blocks
- 2x 13/16 Collets
- 2x Mill Vises
- Edge Finder
- Strap clamps, etc.
- 45-degree angle block
- Metal lathe, tools, keyless chuck for tailstock
- Metal Band Saw
- Belt sander for metal
- Selection of center drills and drill bits, including numbered and lettered sizes
- Access to an anodizer and powder coater or the ability to do those things yourself
- Beads and sandblaster
I'll walk through the base first, then the pen body, and finally the cap.
Step 2: Preparing Base Pattern for Casting
We'll sand cast the base, but first we need a pattern to make the mold from.
I 3D printed the shape of the base itself, since there's no sane way to make it by hand. It's amazing what shapes you can make and cast using a 3D printer that you'd otherwise be unable to make.
I used a FDM printer, since the shape is big enough that you can save a lot of material by having the lattice inside. That means you need to sand it afterward to remove the ridges, since otherwise they'll catch the sand and prevent the pattern from being removed from the mold.
You'll notice that there are two tabs protruding from the base. Those are to fixture it on the mill when cutting the triangular slot. The STL file for the base, tabs included, is attached.
You also have to make the gate and runner. I cut mine out of foam using a scroll saw and then added 15 degrees of draft with a spindle sander.
It helps the sand not stick if you add a couple coats of shellac before you move on to making the mold.
Attachments
Step 3: Sand Casting Base
Use some industrial double stick tape to attach the gate to the pattern, and then go ahead and ram up the free pattern, having it extend up into the cope and the drag extend up into the hollow base. It's a little hard to remove the pattern without damaging the drag, so it may take a couple tries to make a successful mould.
I used a piece of wire to cut a vent coming out of the top of the base.
I had to use a riser to get enough height in the snap flask, so that's why the snap flask was still on during the pour.
Also, I poured at 1160 Fahrenheit to try to get a better surface finish, but YMMV.
Hack saw the sprue off when you're done.
Step 4: Cutting Triangular Hole in Base (part 1)
This is a little tricky, since mills are made to cut along the axes, not in triangular patterns along a spherical surface.
Set up an angle table on the milling machine, square to the x-axis, and strap clamp the base onto the table so that the tip and highest point in the top edge arc are at the same height.
Step 5: Cutting Triangular Hole in Base (part 2)
Referring back to the plans for the base, use an edge finder to determine where the center of the triangular slot should be. Then, take the biggest drill bit available that is less than the diameter of the circle inscribed in the triangle and drill out that material.
Swap in the 3/8" end mill for aluminum, and use it to drill out the holes at the four corners, and connect the holes with slots. You'll have to rotate 60 and -60 degrees for the second and third slots.
Clean up with a triangular file afterwards, if necessary.
Step 6: Sanding the Base
I then buzzed off the tabs with a belt sander, since I had no further need for them. Sawing them off would probably be less wasteful. I also cleaned up the bottom on the sander.
I then hand sanded the rest of the surfaces up to about 320 grit, filled in small pits with jbweld, and sent it off to be powder coated midnight blue.
Step 7: Starting the Pen: Turning Down the Blank
Now we'll start on the pen body. Since bars come a bit pitted and out of round, the first step is to turn the bar down to 13/16", the next standard collet size.
Leave an extra half inch on each side of the material you'll need, since we'll need that to fixture it in the mill.
You need to use a live center to support the bar, since it'll wobble otherwise. You won't be able to get anywhere near the precision shown by the calipers without it!
Step 8: Concentric Hole Drilling
Slice off the turned down part of the bar on the bandsaw and face it to length with a collet.
Then start drilling it out with the tailstock, biggest diameter to smallest, adding 0.5" to each depth, since we'll take that material off later. Refer to the part diagram for diameters. They're all standard US sizes. The depths are to the edge of the drill bit before it starts to taper, and I'd recommend measuring depths with calipers and a piece of tape on the bit.
The trick is to drill that 5.5" hole down the center without getting the bit stuck or melted in there. Make sure to proceed slowly and back out whenever you start hearing squealing. Kerosene is your friend.
Then flip the blank around and drill the ink hole out the front.
Step 9: Fun With Collet Blocks
We're going to use hex collet blocks to get the triangular/hexagonal geometry.
Mark 0.5" in from the end on each side of the blank.
Then, put less than 0.5" in each block, and get the blocks very, very tight. You do not want them slipping and ruining your piece once you've started milling. Put each in a vise on the mill.
Step 10: Mill the Cross-Section
Put a big end mill in, touch off, and trim all three sides down to the depth indicated on the part diagram.
Step 11: Add Long Chamfers
Repeat the same procedure for the chamfers on the long edges.
Step 12: Admire the Cross-Section
Take a second to admire having created triangular geometry on a mill!
Then trim off the back's round end with a hack saw.
Step 13: Scribe Lines for Tip
Use dye-chem and a scribe to scratch in where the tip angles should end.
Step 14: Mill the Tip Angles
Put an angle table on the mill and a vise on the angle table.
Set the angle table to the shallower angle indicated on the part diagram, and secure the pen between one small and one wide side.
Mill the tip down to the line you just scribed. Repeat on each of the three wide sides.
Step 15: Add Tip Chamfers
Add chamfers in the same fashion, and clean up the tip. Also clean up the back, bringing the pen to length.
Step 16: Admire the Pen Body!
Admire the pen body!
Step 17: Beginning the Cap
Begin making the cap by turning down a section of bar, just as before. I decided to modify my design to have the push bearings in the cap, and therefore went with a .450” cap instead of the original design, but the original design would work, too.
Step 18: Drill Out Center
Drill out the center, just like before.
Step 19: Face Down to Size
Cut the cap blank off and face both ends to some reasonable size.
Step 20: Make Cap Cross-Section a Triangle
Make cap cross-section a triangle, and chamfer cross-section.
Step 21: Top Chamfers
Use a 45-degree angle block to do the top chamfers.
Step 22: Corner Chamfers and Face Off
Chamfer the corners, again using the angle block.
Then, face off the cap.
Step 23: Drill Ball Plunger Holes
Edge find and drill the holes for the ball plungers. You’ll need to use jumbo jaws to hold the pen vertical. Use a tiny center drill to make the holes to receive the balls.
The holes for the ball plungers should be drilled with a #32 bit, so they're just tig
Step 24: Sand and Bead Blast
Sand the body and cap up to 1200 grit or so, taking care to preserve chamfers and keep the cap and body dimensions the same.
I chose to directionally sand the cap and tip and mask them with adhesive vinyl so they would look different. This visually ties together the two areas involved in the twist mechanism. I used a CNC vinyl cutter to cut out my logo and put it on the top of the pen, so it would show up bead blasted.
Do NOT sandblast the pen. You will destroy it. Instead bead blast at as low of a pressure as you can get away with and still have it feed. 20 PSI, if you can.
Step 25: Get the Aluminum Pen Parts Anodized
This makes them look better and helps protect the finish. I chose to get them anodized Grey-BL.
Step 26: Put Feet and Velvet on Powder Coated Base
Cut the nonslip urethane feet into triangles and apply them. If everything else is a triangle, the feet may as well be, too.
We also need to cut pieces of the adhesive velvet to pad the pen. Cut an arc, not a strip, since the edges are curved, to fit in the triangular slot, and a shield shape to pad the tip.
You can see how nicely everything fits together in the photo above.
Step 27: Press Fit Ball Plungers
Tap the plungers into their holes using a mallet. If you were to use a proper press, you’d smash their thin walls. Careful! This may take 30 minutes or more of careful work, as you really don't want to mess this up.
Step 28: Epoxy Twist Mechanism
There’s no way the thin twist mechanism would hold up to a press fit. Instead, we epoxy the twist mechanism into the cap. Remember to degrease, abrade, and degrease again for a good bond.
Step 29: Project Complete!
Admire and try writing with your work :)

Participated in the
Metal Contest
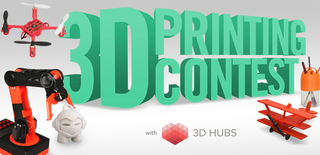
Participated in the
3D Printing Contest