Introduction: Glowing Reaper Skythe
Every year I look at my projects that are still useful and try to find ways to improve them. This year, my focus was on my Reaper Scythe (https://www.instructables.com/id/Grim-Reaper-Scythe...). The current model was well received wherever I went but it was time for an upgrade.
Inspired by a glowing red "EXIT" sign near my office cube, I decided that I could rebuild the scythe blade with glowing red edges to make this a very dramatic scythe at night.
Here's what you'll need for this instructable
- OPTIX 0.22-in x 24-in x 48-in Clear Acrylic Sheet - should be able to find this at your local hardware store.
- 1/2 inch to 1 inch, dense foam board. You can use the 2 inch thick foam boards but it will require a little more work to reduce the overall thickness of your blade. I used 1/2 poster board with black foam inside. I salvaged this from some old signs that my company was throwing away but the foam board mentioned above will work just as well.
- Spray adhesive
- Jigsaw
- Belt sander
- Scrap wood
- Led light strip - Approximately 6-8 feet of length
- Battery pack, wire and switch
- Household Bondo
Step 1: Step 1: Blade Design
Consider your materials and design carefully up front. This is going to be a scythe blade so I did not want it too thick. It needs to look like a thin metal blade so design is critical. My goal was to keep the overall width under 1 inch.
Initially, I also wanted to put glowing designs or alchemy symbols on the side of the blade as well but after a bit of trial and error, it would have made the blade over 2 inches thick and would have looked less authentic. I may revisit this again later to come up with a thinner design but that might come at a risk of a more fragile acrylic blade which I want to avoid. Don't want this breaking while in use.
Using the 2x4 acrylic sheet as your size limit for this project, cover it with some paper and start sketching a design that appeals to your needs.
Transfer that to a template that will be used to cut the other materials. I had 1/2 inch poster board lying around that was large enough for this purpose. A decent piece of cardboard or heavy stock paper would also work just fine.
Step 2: Step 2: Cutting
Using the template you created, transfer that to the acrylic and the foam board. I found that my jigsaw worked perfectly to cut these shapes. Be careful to not apply too much pressure to the acrylic while cutting. You might crack it.
After doing some sample testing with the leds to see how I wanted the lights to shine through the acrylic, I decided that I would set them back about 2 inches from the edge of the blade.
Going back to my template, I sketched out the area inside the blade, keeping at least 2 inches of thickness around the edges. This is also thick enough to keep the acrylic strong enough not to break later. Next, transfer that inner opening to the acrylic and remove that piece.
One note, if you have never drilled through acrylic - do not do it with a regular drill bit. YOU WILL RUIN THE ACRYLIC. Go to your local hardware store and buy a special drill bit for acrylic. Drill a couple holes in the acrylic and then use the jigsaw to remove the remaining material.
Once I cut the template, I mounted it on my old staff to make sure the size and look was what I wanted. This is actually my second blade design because the first did not look right after I saw it on the staff.
Step 3: Step 3: Lighting
This takes a bit of careful planning and design. I’m sure there's more than one way to handle this but as you can see from my pictures, I wanted to keep the acrylic in one piece for stability, so I chose to work the wood core in a way that would fill the void in the acrylic but overlap the acrylic at the point where it attaches to the staff. This was not an easy task so if you don’t have some decent wood working tools available, like a band saw, you might not want to use a solid piece of wood.
As an alternative, you could use 1/4 inch thick plywood to create three layers. Glue them together and effective get the same result.
Once again, using the hollowed out template, I transferred the inner shape to the wood and then removed about 1/8 more material to compensate for the led light strip thickness. The wood core was a stock piece of pine, 3/4 inch thick. Depending on the led light strip you use, simply use double sided tape to adhere it to the wood or if you have the light strip with a sticky back, just peel and stick.
Carefully fit the core in place and once satisfied with everything, use some spray glue on the acrylic where the wood overlaps and clamp in place until dry.
This is also a good time to start thinking about how you want to run and hide your wires. Considering your design might be different from mine, I'll leave this up to your imagination.
Step 4: Step 4: Cover With Foam
Before you cover the outside of the blade with the foam, you'll notice that your blade is not flat. The acrylic is ~1/4 inch thick but the core is 3/4 inch thick. This creates a bit of a challenge to glue the foam on. My solution was to use the template to outline the inner core area on the foam board and then, using my router, I removed about 1/8 inch of material. This recess allowed the foam to fit nicely over the wood core and leds.
Without a router for this work, you will find this challenging to solve. One other option would be to remove the inner core of the foam board just like you did with the acrylic and then glue that to the blade. Now the foam would be firmly attached to the blade but you'd have the core exposed. Simply cut a new piece of foam to fit exactly into the core opening and then glue that into place. At that point, you just need to remove the additional foam material after assembly which is the next step anyway.
The key to this step is to make sure you have clean contact between the foam board and the acrylic to ensure everything is tightly bonded together. Once you start the next step, it will be hard to correct any areas that are not securely glued together.
Step 5: Step 5: Shaping the Blade
Using a belt sander made quick work of removing the excess foam and grinding down the edge of the acrylic. However, be careful and take your time. A belt sander works very quickly and one wrong move, you could remove too much material.
If you don’t have a belt sander, this will take a lot of time with hand tools but I'd recommend using a rasp and files to shape the foam and acrylic and then finish off with a sanding block.
Whenever sanding, choose the grit appropriately. I started with 80 grit to quickly remove the bulk of material and then switch to 120 grit for the final removal. I could have gone down to 220 after that but the 120 grit left a good roughness to the foam and acrylic that appealed to me. I didn’t want the blade to look perfectly smooth. I wanted an older, rougher look.
There's going to be some gaps between the foam and the wood. To solve that problem, simply get some household Bondo from your local hardware store to fill in and smooth over the gaps. I always have a gallon of that stuff handy in the shop. Quick to dry and can be easily sanded.
While shaping the blade, I took the time to light it up occasionally to ensure I was getting the effect I wanted. I didn't want the edge of the acrylic too sharp and I had to adjust the angle to keep just enough foam on the blade but expose about 3/4 of the acrylic to glow. You can also see the light bleeding through the foam when I started sanding a bit too much material off of the blade. This is where Bondo comes in handy to fix those areas.
In hind sight, I sould have covered the sides of the leds with black electrical tape before applying the foam to prevent any light from escaping through the foam.
Step 6: Step 6: Finishing Touches
I covered the blade with metallic spray paint that produces a hand hammered look. Only needed one can for this job. Once dry, I hand sanded the edge of the acrylic to remove any paint from the blade edge.
Fit the end of the blade into the top of your staff. Once placed, you can safely use a regular drill bit to drill through the staff stock and blade end. Since the acrylic is sandwiched in between the wood, it will not splinter or crack.
I drilled three holds and secured it all with a few wood screws. I didn’t mention wiring above because you can handle this in many ways but at this point, you have to look at where you want to keep your batteries and where you want to place your switch. Depending on what you figure out in your situation, you'll just need to run the wires in a way that works for you.
My solution was to use my dremel to create a grove into the wood staff for the wire. I then covered that wire and filed that grove with wood filler. Once dry, a little stain to darken the filler and some polyurethane blended it all together. I positioned the battery pack at the top of the staff and covered with a rubber skull. Looks good and functional too, who knew!
Whatever switch you use will also determine how you attach it to the staff. I had this little round button lying around so I simply drilled a hole through the staff and affixed it in place.
I also found some grass string in the hardware store that I used to wrap the handle and joints which gives an older, hand crafted appearance. I felt it was a nice touch but you can finish this up any way that suits you. You can see in one picture, the top of the staff without the string wrap. I think the string definitely helps.
That’s it. Carry it around with the lights off and it looks great. Most will just think it's a solid blade but when you get close, and hold it near someone, hit the button and enjoy their reaction as the blade appears to glow red hot.
Happy haunts and hope you like this instructable.
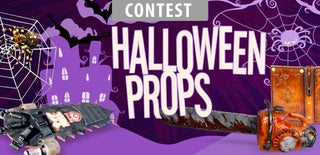
Participated in the
Halloween Props Contest 2016