Introduction: Ground Mounted Solar Panels With Adjustable Angles
I've wanted to experiment with solar panels for some time but I wasn't too enthusiastic about mounting panels on my roof. So my aha moment was realizing that I have a concrete walkway that was seldom used and the walkway runs from east to west. So mounting the panels along the walkway was just about perfect in terms of having the panels facing south; the walkway also makes a stable ground anchor.
Here's the main points I considered before starting the project:
- I wanted a ground mounted system as I wasn't comfortable working on the roof and I also wanted to have the panel angles adjustable. Also, ground mounted panels are easy to access for repair and replacement.
- Solar panels typically have a 25 year plus life span so it made sense to make the mounting system out of materials that would last that long. So I went with pressure treated wood, plated hinges, galvanized lag screws and SS screws. (The panels are further secured with aluminum flooring strips and PVC angle.)
- I wanted to have a system that didn't require any heavy metal work or welding so the frames that hold the panels are made mostly with 2x4's and plywood.
- I wanted a system capable of withstanding high winds and snow loads. The unused walkway works perfectly in providing a secure mounting method. Of course if I didn't have the walkway to work with I would have had to look at alternative ground mounting methods such as concrete piers, heavy blocks, screw anchors, etc.
I had enough space on the walkway to comfortably install two sets of five 100 watt panels. Each of the two "arrays" are therefore rated at 500 watts maximum total output.
Step 1: Designing and Ground Preparation
Design
I've been picking up the 100 watt Coleman brand solar panels from our local Canadian Tire store whenever they were on sale. Each panel measures approximately 26-1/4 x 39-3/4 inches. Those were the first dimensions that I started with to determine the lengths of the 2x4's that would form the main part of the panel support system. I kept in mind that there will be some thermal expansion of the panels so a space is required for this variation in size.
Also, each array must be sized so that adjusting the panel tilt angle can be done comfortably by one or two people. I selected 2x4x12's for the long dimension of the panel frame structure. This size holds 5 of my panels with a good space between panels. The overall height of the panel frame structure is approximately 48 inches.
(My original thoughts included a remote control angle adjustment. I have two 12 volt electric car jacks on hand and figured that they would be just "perfect" for this application. But after some sizing and wind load considerations I dropped this idea and went with the manually adjustable system that is described in this instructable.)
Ground preparation
I decided to anchor the panel system to the concrete walkway with pressure treated 4x4's that are seated in galvanized saddle brackets. (Saddle brackets are more commonly used in deck construction where the deck post ends fit in the saddle brackets. In deck construction the saddle bracket shafts are normally secured to the ground by embedding them in concrete piers.)
The most difficult part of this project was drilling the holes in the concrete walkway. I started with my consumer grade hammer drill with a 7/8 inch masonry bit. I ended up renting an industrial grade hammer drill that made the job much easier.
(I realize that most readers of this instructable will not have an unused concrete walkway available for solar panels so my main objective here is to show how the 2x4 panel support system was made and how I incorporated the adjustable angle feature.)
Once the holes were drilled I anchored the saddle bracket in the walkway with 2-part epoxy.
Note 1: To make handling easier I used 2x4x12's (rather than the heavier 4x4x12's) to get the saddle brackets positioned and glued in place. Once the epoxy cured I removed the 2x4's, painted the 4x4x12's, and installed them in the saddle brackets.
Note 2: I live in a high wind area so having the solar system firmly grounded was of primary importance. In this regard I anchored the 4x4x12's as well as the angle adjustment arms. An alternative to this design is to leave out the 4x4 component altogether and go with anchoring the angle adjustment arms only. The panel frames would then be hinged directly to the angle adjustment arms.
Step 2: Building the 2x4 Frames
This is perhaps the most significant part of the project as the primary goal was to have a way to mount the solar panels in a secure way and to have the tilt angle adjustable - all to be accomplished with readily available 2x4's, 4x4's and plywood.
The 2x4 frames hold the solar panels, and in turn, the frames are mounted to the 4x4 bases that are firmly anchored in the concrete walkway.
I built the fames on my back deck.
Referring to my rough sketched plans I cut the ends pieces of 2x4's to 40 inches. (The solar panels measure approximately 26-1/4 x 39-3/4). The 2x4x12's didn't need cutting.
To get a feel for the overall structure I test fitted the five panels in the clamped-up frame. Seeing that the sizes and spaces were good I then proceeded to nail the frame together. Before driving the first nails I made sure the structure was square by checking the diagonals. I double checked for square as I went along.
The 1/2x6x48 inch pressure treated plywood boards have two main functions: they serve as gussets between the 2x4's (thereby joining the corners and keeping the corners square), and they support the solar panels. I cut the boards on my portable table saw from a sheet of 1/2 inch 4x8 ft. pressure treated plywood.
In addition to the plywood supports I decided to use Simpson galvanized corner brackets on the other side of the 2x4 frame. This might be a bit of overkill but I went with it anyway.
At this stage I already had the saddle brackets epoxied in the concrete so I went ahead with painting the 4x4x12's. After that I removed the temporary 2x4x12's and permanently mounted the 4x4x12's in the saddle brackets.
I also painted the panel frames to get them ready for mounting to the 4x4's with hinges.
Step 3: Mounting the Panel Frames to the 4x4x12's With Hinges
This was a satisfying part of the project as two major sections of the system were completed and now I just had to join them together with hinges.
As the 5/16 x 2 inch galvanized lag screws were driven into the wood along its length (rather than near the ends) there was no need to drill pilot holes before driving the screws home.
Hinges are forgiving when it comes to connecting large wooden project sections where there might be some warping, twisting, cupping or other kinds of distortion due to wood movement. And in this project the concrete walkway sections no doubt shift up and down with the seasons. So even if the solar panels were not intended to have adjustable tilt angles, the hinges would still be a good choice to make the connection between the ground anchors and the panel frames.
(5-1/4 inch "gate" hinges were chosen for this part of the project.)
Step 4: More Ground Anchoring for the Angle Adjustment Feature
As with the rest of the project I didn't skimp on parts and materials for the panel angle adjusting feature of the project. I went with Simpson stainless steel concrete anchors and galvanized angle brackets.
In this step the photos show me removing some sod to make good clearance for the 2x6, ground anchored, angle adjustment bar. This step was necessary as the turf was somewhat higher than the concrete walkway. I found that a long blade in my reciprocating saw worked good to cut the sods before tearing them out with the pickaxe.
I first secured the bars to the already anchored 4x4's with Simpson angle brackets. This helped keep the bars in place while I drilled the 1/2 inch holes in the concrete for the Simpson concrete anchors. The video in Step 1 provides more info on this procedure.
Step 5: Lots of Holes in the Angle Adjustment Bar
Before I got serious about cutting 2x4's for the solar panel adjusting system I whipped-up a rough mockup of the angle adjustment components. A length of 2x4x48 represented the panel frame section of the triangle.
The final selected length of both the ground anchor bar (48 inches) and the adjustable angle bar (60 inches) gave me a solar panel tilt angle range from about 20 degrees to the horizontal to about 76 degrees to the horizontal.
I made up a drill press jig to keep the holes evenly spaced in the adjustable angle bar. The hole spacing is equal to the distance between the two in-line holes in the T-hinge. With this spacing, and after selecting the tilt angle for the panels, I could use either one or two bolts to secure the panel/frame assembly in place. As the tilt angle would be adjusted seasonally I used stainless steel bolts, flat washers, lock washers and wing nuts to make the join reliable and convenient over the years. (After completing the project I found that just one bolt was sufficient to secure the panel assembly firmly in place.)
The video in Step 1 further describes the jig and the drilling process.
Step 6: Time to Get the Solar Panels Installed in the Frames and Secured in Place
When installed, the panels rest on one leg of a length of PVC plastic angle. The other leg of the 90 degree angle angle keeps the bottoms of the panels in place. The tops of the panels are secured in place with a strip of aluminum flooring trim.
Before installing the panels I adjusted the frame to the maximum tilt angle (about 76 degrees) as this was found to be the most convenient angle to aid with installing the plastic angle and the flooring strips.
I cut both the PVC angle and the aluminum trim on my miter saw. I secured both in place with stainless steel wood screws. The screws self-countersink in the plastic angle.
Temporary wooden spacer blocks make the spacing between panels equal.
The video gives a good idea of the procedure that I used.
To remove a panel for repair or replacement you only have to remove the top strip of flooring trim. The panel can then be tipped out, lifted, and removed. The reverse procedure is followed to install a panel.
So a big question is how long will this solar system last... to get some idea please see the next Step.
Step 7: Fast Forward Through Two Winters to Present Day
I finished installing the system in November (about 18 months ago) so the system has endured two winters, and of course spring, summer, fall, and spring again.
All photos and the video in the preceding steps were taken about 18 months ago; I took the photos in this step over the past 2 weeks. (Yes, this is the kind of spring we get here.)
Observations after 18 months
- Some light surface corrosion on the gate hinges
- Paint will require some minor touching up this summer
- The exposed MC4 connectors now have a chalky like finish
- All panels are still giving electrical output
I am very pleased with the condition of the solar panel system after spending 18 months in our climate. Looks like the system will give many years of service without having to spend much time on maintenance or repairs.
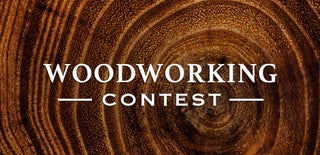
Participated in the
Woodworking Contest