Introduction: Gyrocompass Dead-Reckonator
This started out as an attempt to make a Gyrocompass from 3 hard drives; and ended being a Dead Reckoning Navigation Device (keeps pointing at its initial heading).
A gyrocompass is designed to find and point to true north, however in this case I think there is too much friction, and not enough rotational inertia for it to work.
I'll run through the theory and build anyway, and maybe somebody will have a suggestion to get it working? or will be able to build one better!
What it does now, is look really cool, spin up to around 12,000 rpm, and maintain its current heading. Because it maintains its heading while the base is moved, the degree markings can be used to obtain the new heading with respect to the original. In this way it can be used as a dead reckoning navigator. It is also very educational, I already knew theoretically how a gyro worked, but this puts it into perspective a lot better.
What you need:
2 hard drives
Assorted materials to create brackets/gimbals, I used brass and aluminium
Depending on your hard drive circuitry, you may also need a BLDC motor controller.
Equipment required:
Hand tools for dissasembly/assembly (hard drive take torx head screwdriver bits)
Metal working equipment to make brackets and gimbals
Step 1: The Theory
Once you get your head around precession, a gyrocompass is really a fairly simple device.
I found an article which had a very good explanation, and the figures are taken from that.
http://www.maritime.org/fleetsub/elect/chap17.htm
Firstly, a gyro works by using a spinning disc of high rotational inertia, gained by having large mass towards the edge of a disc spinning at high RPM.
The first figure shows a free gyro, with three axis of freedom, two are on pivots while the third is the gyro wheel's spin axis. A free axis gyro will keep a directionally constant spin axis as there are no forces acting on it.
Precession is how a gyro resists the change in direction. When a torque is applied to a gyro, it applies a precession torque perpendicular. One of the more practical instances of this is countersteering on a motorcycle, as the rider aggressively twists the bars (by pushing on the inside bar), the front wheel generates a torque to lean the bike into the corner, allowing the motorcyclist to change direction very quickly.
The second figure shows the type of gyro I have made; a Pendulous Gyro. This is just a free gyro, but with a weight at the bottom. This weight applies a torque to ensure the spin axis is always horizontal. Because this torque is applied to a gyro, it in turn applies a precession torque, which rotates the gyro around its vertical axis.
The third figure shows how this is used to create a gyro compass. As the earth spins, the horizontal heading changes unless the gyro is pointing along the same spin axis as earth. The gyro attempts to follow the horizontal heading due to the torque from the pendulous weight. Once the gyro spin axis is aligned with the earth's spin axis there is no applied torque to the gyro, and its heading stabilizes.
Step 2: Hard Drive Salvage
I started off with four hard drives for good measure, but the parts I used only came from two of them.
What we are looking for is the platters, the BLDC motor which spins the platters, and the read head frame and bearings. We also want to ensure at least one of the cases doesn't get too scratched up.
A good rule of thumb for dissasembly (as the hard drive you use will probably be a bit different) is to undo all the screws you can find!
After that there was still a strip of tape around the edge to pull off before I could get to the internals.
Once there it is simply a repetition of the undo all screws step! Just be careful getting the neodymium magnets out, the snap to metal with a lot of force.
You'll end up with a mish-mash of parts like in my last picture, now to measure them up for the design.
Step 3: Gimbal Design and Fabrication
This step is the one with a bit of creative license. In my case I went with a double sided gyro gimbal, and a simple heading gimbal. The brass parts were added for some flair, and to provide heading indication.
The important parts here are balance, and friction-free. The gyro gimbal must point downwards when at rest, and the heading gimbal must ensure things are level.
The parts we use from hard drive salvage:
The two read head bearings will be used for the gyro gimbal to pivot on.
One platter motor will be used to spin the upgraded platters.
One platter motor will be used as the heading bearing.
The hard drive case will support the heading bearing.
With the above constrains, there are only a few parts to design. Get a well balanced and sturdy gyro gimbal, and heading gimbal, and you'll be spinning; get some fancy heading indicators in there, and you'll be spinning in the right direction!
My stuff was design optimised for a CNC mill, so 6mm aluminium plate, and 3mm brass plate, with intricate shapes all around. The drilling and tapping was done with hand tools. The whole lot could be done with hand tools, and obtain the requisite precision through adjustment. I used adjustment in mine anyway.
I also decided to salvage the thread that the read head was screwed into on the hard drive case. I did this because it was an oddball size and I didn't have the tap for it. The two very small blocks ended up working nicely in the design, and provided the means to secure the two gyro gimbal plates to the read head bearings.
Step 4: Parts Pre-fitting
Some salvage parts required adjustment prior to assembly.
The hard drive case needed the read head thread machined out of it, and to engrave heading marks in it, as well as trimming down the raised peices of metal.
The spindle of one BLDC motor needed some extra holes and threads to fit the gimbal and brass heading indicator.
The coils were removed from one BLDC motor so there would be no 'cogging' in the heading axis.
Step 5: Assembly
Time for assembly!
Start off with the gyro and work you way out from there.
Firstly, the hard drive motor must be filled up with platters, I got 6 onto mine, more weight is more rotational inertia.
The rest of the assembly is pretty much design dependant. When putting the gimbals together, leave the final tighten for after you have ensured the axis spins freely, and is correctly balanced.
For the wiring to the motor I just used the wires out of the disassembled hard drive motor, they are thin but strong and mean you can just loop them in the general direction, rather than routing them and having them wind up ad put torque on one of the axis.
The ciruitry to drive the BLDC motor might still run, depending on what hard drive you get. In my case it ran for about 10mins and shut off with the original number of platters, and would not run with 6 at all. However, BLDC controllers are fairly cheap, or easy to make if you can be bothered.
Step 6: Result!
Well, not the result we wanted, but it does look cool, and if you start it off pointing northish, nobody will know the difference!
Initial testing was done with the gyro point east to west in order to obtain the maximum tilt from the earths rotation. The hard drive motor was spun up to approximately 15,000 RPM with a hobby BLDC controller at 15V. Instead of oscillating back and forth, it simple continued to point east to west. I think it is due to not enough rotational inertia, and too much friction in the gimbals.
However, it does maintain this heading very well, and could be used as a dead reckoning navigator.
It also is very interesting to have the precession effect displayed hands on. Pushing the heading gimbal around raises one side of the gyro gimbal, I was very surprised at how much movement there was, and how much force was required.
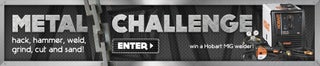
Finalist in the
Metal Challenge
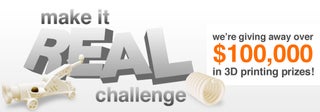
Participated in the
Make It Real Challenge