Introduction: Working Hand Cranked 35mm Motion Picture Movie Camera
My Dear Makers,
I embarked on an ambitious project last month: the creation of a homemade hand-cranked motion picture camera from scratch. I also endeavored to develop the film myself using household chemicals and further to reverse the film negative so that it could be projected and viewed!
I'm still working out the bugs in my processes so you will be learning with me over the next few weeks. It's exciting to be in the same shoes as the first motion picture pioneers of the early 20th century. I've loaded a couple clips that are proof of concept. My camera can hold 100 feet of 35mm film. Most tests have been shorter runs of film. Clearer, better results are completely possible with experimentation!
For this project, I used a 3D printer and a laser cutting machine but one could complete it using hand tools and careful measurements, too. I admit, although the idea has been rattling in my brain meat for years, it was not until I found a book called The Boy Mechanic (published in 1915) that I found a basic enough design that would work. I have included the photos from this book to reference as well.
So let's get started!
Step 1:
Step 2: Materials and Cost
The materials list can vary from maker to maker. There are certainly substitutions allowed here but I will tell you what I used and later I plan to provide my source files for 3D printed parts and laser cut parts.
a) $30, Several sheets 4.8mm thick Baltic Birch Wood (Ganahl Lumber, Home Depot)
b) $5, A couple meters of 8mm thick dowel rod (You'll have to sand it a little sometimes) (Ganahl, Home Depot)
c) $20, 10+, 16mm outer diameter, 8mm inner diameter ball bearings.(Amazon)
d) $20, Polyurethane belt material for pulley systems. (amazon in various thicknesses and lengths)
e) $10, Black cotton velvet and black felt.
f) $15, an enlarger lens with a 3.5 inch focal length and F-Stop adjustments (ebay, vintage stock works fine)
g) $35, Thick and Medium CA glue and Accelerator (this is more preference but I love this stuff.)
h) $40, 100' roll of 35mm film, 100 ISO or 50 ISO (available from B & H Photo, Amazon, Ultrafine Xtreme)
i) $20--$100, Film Developer and Reversal Chemicals (I use all home brewed film chemicals and I may need to publish another instructable for this)
Step 3: The Source Material and Basic Concepts
Filming motion is a complicated venture. The problem is as follows: how do we expose film, then cover the film, and move it out of the way so another piece of the film can be exposed? Not only that, but the film must remain absolutely still while it is being exposed to light. This process being done in rapid succession is what a motion picture is made from. It is literally a series of still photographs taken in rapid succession. There are other factors, such as flicker rate and frame rate that we can come to later.
For now, remember that the device we are building moves the film, holds it still for exposure, covers it, then moves it forward. It does all of this with 1 moving part: The Cylinder Shutter.
Step 4: The Cylinder Shutter
This is the heart of the camera. It's like a Swiss clock, in a way, because of it's simplicity and multi-tasking function. I used a 3D printer to make it but you could just as easily do this with hand tools and dowel rod. The dimensions are laid out in the antique book page I scanned so I will leave that up to you.
The cylinder has some off-set metal prongs that stick out a few millimeters. These are responsible for advancing the film. Their proper placement ensures that the cylinder rotates freely while the film stays completely still to be exposed. The cylinder also rotates freely against the film as it covers the film so no light hits it. Then, the teeth grip the film and advance it. This is the process that makes capturing motion possible with 1 moving part.
Let's get a body for this heart...
Step 5: The Body of the Camera
Body General
The basic design follows what was outlined in the 100 year old instructions. I've made mine with 4.8mm thick wood that was cut in a laser bed. I also integrated 16mmx8mm ball bearings so that the rotation of the pulley system would be smooth and prevent damage to surrounding wood from pressure. The cuts that accept the ball bearings are slightly smaller so they pressure fit. I also use a little glue because I was not hugged enough as a child.
Light Leaks
Light leaks are common and easy to take care of from the inside of the camera. Glue strips of black felt wherever there is a leaky joint. You'll note from my design I use sliding doors. This is an easy way to ensure that an access port is light tight. After all, light doesn't turn around corners, unless it is in close proximity at near right angles to a black hole or other gravitational anomaly.
The Shutter's Home
The cylinder shutter's home is noted in the second photo, object C. It lives in that triangular room. That's why I made an access port on one side of the camera--in case I need to get in there again. The position is pretty important. My designs are precise and the result of hours of experimentation. The trouble was, the cylinder needs to be far enough away to let film slide without the engaged teeth and close enough for the teeth to engage properly without ripping the film. It was maddeningly. You could alternatively hit yourself in the face with a plank of wood. Which brings us to the pressure plate.
The Pressure Plate
This is what keeps the film from moving between frames of motion. You'll note it in the diagram as E and K. You use strips of velvet here. It will take some experimentation. The back door plate needs to be carved or dremeled out so that the teeth don't hit it when the cylinder turns. Sanding and placing strips of velvet over and over is a great way to find yourself.
Step 6: The Pulley System
The pulley system is designed to facilitate the rapid movement of the cylinder shutter without cranking wildly like a lunatic. The crossover you see is because the pulley won't crank in the proper direction without crossing the belt. It looks cool too. You'll need a few drops of silicone lubricant so the belt will easily slide on itself.
The smaller pulley wheel is about 3cm while like larger one is closer to 9cm. This gives approx. 3:1 ratio. Although a greater ratio might be better, it would not fit in the design without a more radical change to the dimensions of the box. No time for that!
The belt is a 'polyurethane belt' material available on amazon. The thickness you'll need will vary based on your wood thickness. I used 3/16" It's a great material for pulley systems because it can be made in any size and melted together. It's stretchy enough to keep tension but not enough to become loose with use.
Step 7: The Lens
The lens I used was meant for an enlarger. I only used it because I knew it had a 3.5" focal length. This is important because the front of the camera is 3.5" from the back. If the focal length were wrong, the film would get fuzzy images.
I think you could probably use any kind of lens with f-stop adjustments as long as it has the proper focal length. Alternatively, you could find a lens and adjust the size of the camera to match its focal length. I just really liked how this one looked.
I will tell you though, it has an extreme telephoto effect. You have to stand about 6 meters away to get a whole body on film. If you know a little more about lenses and focal length, feel free to comment!
Step 8: Conclusion, Files, and to Be Continued!
Developing Film
I created a separate instructable for film developing. Check it out! :)
Concluding Notes
This was a remarkably involved and technical project. It was intensely fun. I have not gone over every little detail here and I'm still working on the camera myself! (such as the take-up roll in the bottom part of the camera. There is another pulley I'm installing for taking up the loose film that's been exposed). There is definitely potential here and I believe I will very soon achieve a 1 minute movie with remarkable clarity.
Step 9: The Take-Up Reel (continuation 03/04/2019)
Okay, so you can't crunch 100' of film in the bottom half of the camera. It's a tricky bit to design because the movement of the film is intermittent and you don't want the take-up reel to yank on the film. My solution was to over-engineer the take-up reel to under-perform. The result is a loose roll of film that stays out of the way during filming. That's really all that is needed.
There can be some slippage or tightening depending on how you make the take-up reel. I encourage you to experiment. Knowing how this very basic motion picture camera works insside and out allows you to become mechanically creative and to come up with your own solutions. I've found that a loose belt is helpful so it doesn't have enough force to yank on the film even if the ratio isn't perfect.
Stay curious.
Attachments
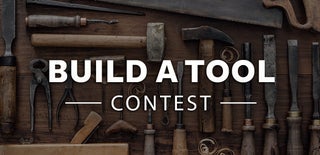
Participated in the
Build a Tool Contest