Introduction: Shredding Meat - Wolverine Style!
Introduction:
My wife *loves* pulled/shredded meat. Pulled Pork, Pulled beef, shredded chicken, you name it. I've been just shredding everything with normal table forks and it's been getting tedious. Now they have these nice little plastic/epoxy ones online called "Wolf Paws" or "Bear Paws". They aren't very expensive. In my experience these things tend to break for me. Which usually doesn't bother me so much because then I have an excuse to glue them back together and make them stronger in the process. In this case, however, I thought I could make something better from scratch. So using some cheap metal skewers and some scrap lumber I was able to make some pretty handy meat shredders. In the end they end up looking a lot like Wolverine claws (from the X-men). So they should go over big at barbecue parties this summer.
And in the spirit of how the commercial ones are all named, I'm going to call these "Wolverine Claws", because that's what everyone in the shop asked me if that was what I was making when I made these. Technically Wolverine (from X-men) only has 3 claws, but I wanted more for shredding and I love prime numbers so I had to go with 5.
I should also mention that I made it at TechShop! If you don't have a TechShop in your town, I must say that I certainly felt your pain. That was until they opened one up within walking distance of me. Now I'm there every day almost! However that shouldn't dissuade you from trying this project, it merely sped up the time it took me to make these.
Materials:
Scrap wood you can make handles out of
Cheap metal kabob skewers
Dremel or hack saw
Wood Glue or Gorilla Glue
Drill (or Dremel)
Polyurethane finish (optional)
I made two different types of handles on this project. One was from a branch from a Mesquite tree that came from regular trimming and was designated to become charcoal. Another I just made from two small pieces of 3/4" plywood. I made this at TechShop so there's always a free supply of small plywood pieces available.
Step 1: Cut the Skewers
Ok so now we just want to make sure we cut our skewers to the same length. I cut mine at about 5 inches (13cm) long. One of the reasons that I chose this length was because it would be long enough and I'd be able to get two sets of prongs from each skewer. I also cut 5 skewers because I wanted 5 tines on my shredders.
Since I had access to a TechShop, I was able to cheat and do them all at once on the hydraulic sheer. Quick and easy. Then I used a bench grinder to smooth them out and even them up. It only takes a few seconds. I could have just as easily done this with a dremel with a stone grinder bit.
If you are doing these yourself, with a hack saw or a dremel, just make sure to get them all about the same length as best as you can. If you get them a little bit off just use a dremel or a bench grinder to make the longer ones shorter. Or you can make a jig or use a miter box to get them all the same length.
Step 2: Make the Handles
So for one handle I simply sanded down a piece of a limb from a mesquite tree. But for the other handle I thought I would try something more people would have access too. In this case I was able to find some small scraps of 3/4" plywood in the scrap wood pile in the shop. There's a never ending supply of this stuff in the shop.
So I cut two pieces on the band saw (but you can cut them any way you like) roughly the same size and roughly handle sized. I actually didn't measure anything I just eye-balled it.
Now I love Gorilla glue and I use it all the time. I think it's great stuff. It expands, which is a feature that I like and find useful. It's strong, and it's fun! So the secret to gluing with gorilla glue is to rough up your surface with sandpaper or some abrasive, and then get it wet, then clamp it well. This is wood so it's porous enough, we don't need to sand it. I just wiped the two surfaces that I was going to mate together with a wet shop cloth.
Next you just put a little dab of glue on each of the surfaces, and spread it out with something. I used a razor blade in this instance. Then it's time for clamping. I like to set my wood pieces that I'm gorilla gluing aside to cure overnight. 12 hours should be plenty.
After the glue has cured then it's time for shaping. I shaped my piece of wood on the disc sander, but you can use any method you'd like. Basically I wanted to get it from a rectangular/cube shape into that of a cylinder. On the disc scander this was done in less than a minute.
Once we have our cylinder shape for our handle, next we need to drill our holes for inserting the pieces of our metal skewers into (from the previous step). I used a scrap piece of wood and drilled holes with progressively larger drill bits until I got a hole big enough for the metal skewers to snugly slip into. I did this before drilling the holes in the handle.
I marked a line along the handle lengthwise as a guide then I marked where I wanted the skewers to go. Since I wanted the skewers to come up between my fingers when holding it, I just poked a pen through the space between my fingers to mark the positions of them.
Then it's just a mater of setting the depth on the drill press so that all your holes are the same depth. This is kind of important, but something you shouldn't have too much trouble doing even if you don't have access to a drill press. I drilled my holes somewhere between 1/2" and 3/4" (15-20 mm) deep.
The final picture shows our completed handle ready for accepting our metal skewer pieces. I took a moment here to so a final sanding of the handle. I started with 220 grit , then to 400 something(ish). This is also when I sanded off the lines I drew for hole placement earlier.
Step 3: Assemble the Parts
After the skewers have all been cut to the same length, it's time to glue them into the holes we drilled in the handle on the last step. I was able to drip water into the holes (remember Gorilla glue needs moisture to cure) and I put some glue in the hole and some on the metal skewers. Then slide the metal skewer pieces into the holes. I actually did clamp them together while the glue was drying (sorry forgot to get a picture of that). I didn't want Gorilla Glue to expand and force the skewers out of their holes. Once the glue starts to cure it will foam up. That's when I wipe of any extra that leaks out of the hole. Personally I think the foaming action of Gorilla Glue is one of it's strengths.
Step 4: Finish
So now we are done. You can use them as they are. Personally I recommend putting a finish on the handles to protect them. Since this is wood it's not going to be dishwasher safe. But a nice polyurethane coating makes them easier to clean and protect the wood. I put 6 coats of Poly on my handles, making sure to sand with a fine grit 400 something(ish) grit sandpaper (lightly!) between coats. The coats dry in about an hour or two. This is something that takes some patience but you can do it over the coarse of a couple of days.
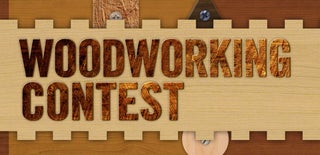
Participated in the
Woodworking Contest
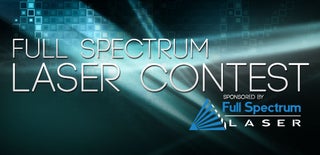
Participated in the
Full Spectrum Laser Contest