Introduction: How to Design a Skateboard Frame Using Science
Hi All
I'm doing this project for a while now and it came to a major milestone which deserves its own instructable :)
And by the way, it IS engineering, so it is more than qualified to enter the explore science contest! If you think the same way, you can totally vote for it, thank you!
Let's begin, what is it all about?
I wanted to design my own skateboard/longboard frame concept, which will eventually end up as a personal electric vehicle. And I really wanted to get this done in the right way as we do in the industry, so:
- We calculated the loads or here.
- We understood what it means, or here.
- And we chose the appropriate hardware, or here.
Now, it's time to see the outcome and get the hardware ready and validated!
This instructable summarizes the three posts: first frame iteration, stress calculation and the actual build.
I hope you find this interesting as I do.
Step 1: First Frame Concept
My initial thoughts were using aluminum with carbon fiber as the building blocks for the frame and eventually the whole vehicle. But, as I went along with it I tend to change my mind towards PLA with carbon. Yes, it is weaker and much softer, and much more challenging than the simple aluminum but it is more affordable, accessible and simple. So currently my focus is on designing proper interfaces/joints for the purpose of this to work! You are welcome to follow!
When eventually anyone with a home printer can make his own scooter which will be practical and look amazing - my job will be complete! :) The design was done in Fusion360.
We are building the frame from 12mm ID and 16mm OD carbon tubes (look at the attached table, last line). The tubes will be the main load bearing element of the structure, and the "end units" will have to keep the tubes together and be in harmony with the loads and the deflections of the frame.
I chose the concept of keeping the tubes as the main load bearer in this units as well. So they run entirely through the units and rotate together with them - no relative deformations. In this way we don't have any significant bending stresses in the PLA parts. We will see how it works later it this instructable.
The test unit was printed, and we went towards validation of the concept with stress analysis.
Step 2: Stress Analysis - Finite Elements
First thing in FEM is always understanding what we are dealing with.
Look at the material table, right away we can see the "orders of magnitude" difference in material properties between carbon tubes and PLA. Now, after understanding this, let's deal with it!
I used Ansys FEM software here, both Classic version and Workbench.
First I wanted to see if our previous hand calculations still make sense. So, the first thing is to analyze the tubes themselves, with beam elements. As expected, the results were in par with the closed form formulas for this simple case. We've got ~26mm maximum deflection for the 860mm frame and ~13mm of deflection for the 690mm frame. The deflections in the pictures are really scaled up, for clarity.
Now for the real reason we use finite elements - it is to find out the stress levels in "irregularly" shaped parts. Now we shift to 690mm frame as this will be the one assembled first.
The analysis I did was of only half a structure with symmetric boundary conditions, it is a common trick we use in order to reduce the problem size, the results are the same as on the full structure.
Now, the deflections are slightly lower - 10mm vs 13mm for the tubes only case. This happens due to slightly shifted boundary conditions, not a big deal once we are aware of this.
Now let's see the stress levels in the PLA. The maximum level is around 7MPa which is way lower then the allowable level of 36MPa - the part will hold!
This is the outcome that we came to validate, now the parts can be printed and assembled.
Step 3: Print Your Parts, Sand the Joints
Now the parts can be printed. It took around 20 hours to print the two end pieces on Ultimaker 2.
Once the parts are ready and the tubes are here, we are ready to sand the joints.
The sanding was done with 180grit sandpaper, both for the PLA parts and the carbon tubes.
Step 4: Glue the Side Tubes, Glue the Center Tube
I cut the two side tubes to size (around 740mm for 690mm between wheels frame).
Then I used the center tube as the alignment jig and just dry insert it at this stage.
Glue the side tubes with epoxy.
Once they are dry, cut the center piece (it is slightly longer) and glue it too.
Put it for the final cure through the night.
Now, the frame came slightly less than 550gr!! Which is really cool.
Step 5: Attach Hardware, Test It!
Once everything is dry and good to go, attach standard trucks and wheels.
This is a simple 8 bolt step. I used 180mm trucks and 78mm wheels, kind of standard.
Then, the entertaining part - take it for a spin and test it.
The riding was not that awkward as one might think, the grip is good and the riding is smooth.
One thing to overcome is the weird looks from the surroundings, but the comments are mostly positive :)
Now, for the final thing - we need to validate our calculations, we do the "load test", here it is:
The results are really good, and I'm really happy with the outcome!
Now waiting for the electric parts to arrive and we do the electrification.
Want to be aware of the progress? you can subscribe to our mailing list:
http://dosimplecarbon.com/subscribe/
Enjoy,
Dani
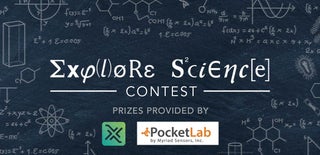
Participated in the
Explore Science Contest 2017