Introduction: How to Make Silver Rings the Perfect Size!
I can't find on here the method I use to get my sterling silver rings sized JUST right, so here you guys go!
There is a glossary at the end, let me know if there is any other info you want me to add!
Step 1: Materials and Supplies
Supplies
-lined white paper
-half round sterling silver wire 12g (2mm wide x 1mm thick)
-hard solder
-pickle solution
-flux
-sand paper: 400, 600, 1000, etc
-liver of sulphur (optional, for awesome black oxidized ring)
Tools
-pickle pot
-quenching pot/cup
-copper tongs
-caliper (optional)
-tweezers
-steel ring mandrel with ring sizes
-steel ring mandrel without sizes (optional)
-finger gauge (optional)
-torch
-jewelry saw and saw blade
-pencil
-sharpee
-files (large flat and small round)
-.925 stamp
-plastic jawed pliers
-tumbler with steel shot (optional, otherwise more finer sandpaper and polishing cloth)
-rawhide hammer
-steel hammer
-steel block or ring stamping block
Step 2: Pick a Size!
First, you have to pick a size!
If you make rings a lot it is nice to have a nice finger gauge with all the sizes as samples, but you can also just measure your finger with string or paper and find the corresponding circumference on the ring mandrel.
I chose size 6.
I first cut out a thin strip of paper. About 1/8" wide and 3 inches long. With the ends perfectly squared. Then wrap it tightly around the graduated ring mandrel with the size 6 line lined up with the very center of the paper and mark a point about 1/4" from where the paper starts to overlap. I removed the paper from the mandrel and cut it down to the mark. I then wrapped the paper back around the mandrel at the correct point. Being sure that the paper is perfectly placed and perfectly taut.
Getting these measurements exact is very important, the difference between size 7 and 7 1/4 is about 1/32"
I marked a line perpendicularly along the overlap line. This should accurately mark exactly the circumference of the mandrel at size 6. I remove and replace it once to be sure (measure twice cut once).
Now, I add twice the thickness of the wire being used to the total length of my template. The outside of the wire has to bend around its own fatness twice, so you have to add this to your measurements
I happened to have 2mm thick rectangular wire, which I used to add 2mm to my measurements.
Otherwise you are going to have to regular measure somehow. A caliper is nice for this.
Step 3: Marking and Sawing
Now I have a template for a size 6 ring made from 1mm thick material.
After making sure the end of my wire is nice and even, I use a sharpee to mark on the wire the length of my paper template.
Measure twice! I use a bench pin for all my sawing. I place the wire on the pin, lining my mark up with just past the edge of the pin. Recalling that the saw blade does remove material when it cuts so I have to cut not directly on the sharpee mark but just a smidge past it, otherwise my ring will end up too small. For this part I always want to end up cutting a little long anyway so I can go back and file to just to just the perfect length.
Now check your silver length to your template to gauge how much filing you need to do... file, check, repeat as necessary.
Step 4: Preparing to Solder
I use plastic nosed pliers, to carefully bend to two ends of the wire back around to each other. I am NOT trying to make a round shape at this point. I'm trying to get the two ends to perfectly meet each other, in order for the solder seam to disappear. So, depending on the size of the ring and the material, you may have to really mess up the shape of this ring to get the ends together.
Step 5: Soldering
I keep my flux nice and liquidy, and though people classically brush it on... I've taken to dipping my piece.
I then set my ring up on my solder board, leaning against some honey comb board. Because I use such a baaaby torch I need all the reflective heat I can get!
BEFORE I put a solder chip on the ring, I hit the ring with my torch. I want to dry out the flux so when I'm trying to melt the solder the steam doesn't pitch my little solder chip across the table.
Now I put a 1-2mm square piece of hard solder on the inside of my ring's seam, my dry and fluxed ring.
With a sharply tipped flame I circle around the ring to heat it evenly, then once the flux turns clear I focus my heat on the solder chip until the chip melts and flows in the seam.
Then I quickly take the ring with my tweezers and quench it and then drop it in my pickle pot.
If I don't do this quickly, the flux can harden and stick to my solder board and then I'm ripping up chunks of my solder board.
I also don't throw the ring directly in the pickle because I don't want a face full of acid steam.
Step 6: Shaping
After the pickle has done its job I grab my piece with a pair of copper tongs and drop it in my quench cup (the cup has TWO jobs), and take it to my bathroom sink to thoroughly rinse off and refill the cup with fresh water.
(It is more common to have a cup with water and baking soda to neutralize the pickle before washing your piece in the sink... I should maybe also do this...)
Now I check to see if I got solder through all of the seam, if not, I go ahead and flux/solder/pickle again.
If there is a fair amount of extra solder on the inside of the ring I file that down with a baby file before shaping.
Since I just got the ring hot enough to melt hard solder the ring was thoroughly annealed and is now super soft!
So I slip it on my super nice ring mandrel (with no graduations on it and I NEVER use a metal hammer on it). And pull it down the mandrel just with my fingers (it is VERY soft). I pull by the parts of the ring in contact with the mandrel and NOT the parts hanging out in the air. When I pull those it bends my ring sideways in a very undesirable way.
Once I stop being able to easily pull and stretch out the ring I grab my rawhide mallet and hammer the offending un-rounded edges. Sometimes I can get this just right in one go, if there are stupid corners that won't go away I try flattening them out with my plastic pliers (at the expense of losing my round shape), and/or annealing again. When you anneal a piece after you have melted solder onto it, be very vary not to chase the solder back out of your solder seam by over heating.
Also, I never use a metal hammer for shaping a ring unless I'm trying to put hammer marks on it.
Step 7: Stamping .925
It is about this point that I add a metal purity stamp. If my ring is made of flat wire I often add it at the beginning.
I got this fancy block with little indents that match various common ring shapes so that I don't smash the pleasant curve of the wire when I hammer the ".925" stamp onto the back. Not necessary...... but this makes a piece look loads more professional.
To use this block I had to also buy weird wiggly stamps =P
I carefully place the ring in the block, and then sneak in the wiggle stamp so that the pressure of the stamp is what is holding the ring in place. I need one hand to hold the stamp in place and the other to hold the regular steel hammer. Kind of tricky actually. I give the stamp a few hard blows. Once you lift of the stamp you are done, there is no getting the stamp exactly back and trying again to get a deeper impression.
Step 8: Filing and Sanding
I generally have some solder clean up to do. Before I mentioned, any "big" chunks that I can safely get with a tiny round or oval needle file I will go after. But my stupid hands like to accidentally make giant gashes on my piece with the file for no reason, so I lean in the direction that is is better to spend a long time sanding removing solder than a long time sanding to remove ugly gashes that I added to my piece on accident with the needle file.
I start with 400 usually. I rip off little pieces and write the grit number of the back with a sharpee. I have little piles of labeled sand paper bits all over. If there turns out to be gashes I've made or whatever and the 400 isn't cutting it, I will warily go up to 320. 400 is about the finest grit that kind of polished and kind of removes material. Then I can go down to 600 and 1000. I have a fantastic little tumbler which I employ at this point, other wise you should go to 2000 and or 2500 and maybe polish with some micron sheets and/or silver polish.
I always tell people that about 90% of jewelery making is polishing =/ Totally boring I know, but it will really give your piece a professional air and separate your work from that of jewelry 101 students.
Step 9: Polishing and Finishing
So.. if you have a tumbler, you can load it with all kinds of things! Here is the same ring tumbled with steel shot (for a shiny polish), then tumbled with ceramic shot (for a satin matte finish), and as a finale, oxidized completely black, my favorite!
To use tumbling media, that is shot, load it into the tumbler and add water so that all of the media is covered in water. Also add a hint of liquid soap for lube. I do the same for either steel or ceramic shot.
To blacken a piece, this is the veeery last thing you do. My favorite "blackener" is "maid o metal liver of sulphur". I get a little disposable plastic cup and fill it about half way with water, and add a little squirt of the liver of sulpur and then add the ring. In about 20 minutes it should turn totally black, if you leave it less time you can get colors and antiqued browns. Too long is bad because the oxidation will become pretty thick and just immediately peel off. Also, don't touch the solution, use tweezers. Otherwise your fingers will smell like rotting eggs for a few days.
Step 10: Glossary
anneal
-annealing is when you heat up metal to get it soft again. put a little flux on your metal before annealing so you can gauge how hot you are getting. when the flux goes glossy it is plenty hot. .....this works because metal atoms are shaped like christmas trees. when you bend a soft piece of metal once it is fine, by when you go back and for a couple times it snaps. it is because you are squishing up all the metal trees and giving them nowhere to move, so they snap. when you anneal metal you open up the trees so they have room to move again and the metal becomes soft.
block
-steel blocks are great for flattening pieces, or stamping pieces.
-ring stamping block are especially for stamping the insides of rings with curved stamps
caliper
-a magical measuring device. there are basic little ones that round like $5. slightly fancier digital ones for like $20. mine cost a whooping $170 or so i think, and worth every penny. one of the few extravagant purchases I have made that was worth it.
copper tongs
-are an absolute must if you have a pickle pot! if you try to use your steel tweezers... the steel reacts with the chemicals in the
pickle and causes and copper particles in your pickle solutions to plate any pieces you happen to have pickling. not generally what you want to have happen. this is an on purpose technique for something else though...
files
-metal files (just like a nail file, but metal, and badass), come in all shapes and sizes. don't get them wet, don't stack them on each other, and clean them out when they get full of filed bits with oil.
finger gauge
-a handy dealie for finding the right size for you finger. a large ring with a collection of sample rings in "all" the ring sizes. they come in metal and plastic. you can also get cheap little ones that are like mini belts for your finger
https://www.etsy.com/listing/72243099/multi-sizer-adjustable-finger-gauge-find
flux
-flux is used when soldering, it keeps 'dirt' in the air from getting into the areas you are trying to solder and helps the solder to flow easily. if you don't use enough flux your solder will just ball up and not flow at all, no matter how much solder you pile on
hammer
-steel hammer, yup a regular hammer, though one meant for jewelry with a rounded end and a flat end would be nice
-rawhide hammer, a leather hammer, how weird is that? used to shape annealed metal without marking it
hardness
-Right after metal is annealed it's softness is described as "dead soft".
-Slightly worked (ie metal is bent, hammered, etc) is "half hard" and springy, generally useful for wire wrapping, or anything that doesn't involve using a torch.
-Metal is also sold in "hard"... it is hard, and uninterested in bending at all. Or it becomes hard from being hammered/bent a lot. If it gets to this point and you want to keep bending, it is time to anneal! Otherwise your metal will soon break.
liver of sulphur
-a solution with a little bit of sulpur and some other various things, it pretty much makes you metal dirty, and sometimes that is good! be aware this is only a patina and can rub off.
mandrel
-a long tapered object, used as a shaping template, they have them in all shapes, sizes and materials, big wood ones for bracelets, square little ones for bezels, stepped round ones... for, uh, fat rings i guess..? i used two steel ones meant for regular round rings in this project. one was marked with sizes, and the other one wasn't. i only recently got the unmarked one because the one with sizes left marks on my pieces sometimes =(
pickle
-pickle is a solution for cleaning metal, in this case I use a pickle for non-ferrous metals. it cleans off both flux and oxides deposited from the air during soldering/annealing
pickle pot
-something glass (or pooosibly plastic) to hold your pickle. needs a lid. crock pots are a very popular choice because hotter chemicals means faster chemical reaction.
pliers
-about what you'd expect, though there is a far larger variety perhaps. my favorite fancy pliers are the plastic jawed kind because they don't mark up my metal.
quenching pot/cup
-a container to hold water to quickly cool your piece. i use an old ceramic cup. my stuff is small and fits easily. avoid anything burnable or meltable (ie paper or plastic). also avoid glass... you don't want a face full of glass shards in case you accidently touch something very hot to a very cold piece of glass. so... use ceramic or metal!
(mine also doubles as my container for washing pieces removed from the pickle)
sand paper: 400, 600, 1000, etc
-yup, regular wet dry sand paper! Start with 400, if that doesn't cut it try 320... I'm vary wary of going past 320, you will in in giant scratch territory
saw
-jewelry saw frames take a wide variety of saw blades. for metal there are super thin 8/0 and super thick 8. there are weird shaped ones special for wax, acrylic, wood, etc.
sharpee
-mark your metal all you want with these, they will burn right off =)
shot/media
-for filling up a tumbler!
--steel shot gives a nice polished finished
--ceramic media makes a nice even satin finish (you got to get your piece polished with the steel first before using this one, i learned the hard way)
solder
-solder, in particular silver solder (there are many varities of solder for different kinds of crafts) is silver with other metals added to lower the melting temperature. commonly there are 3 levels of silver solder, hard, medium and soft. so if you are making a piece with many parts, first you use hard solder. then you use medium, then you use soft. this way you can keep soldering more pieces without the pieces you have already soldered falling off. (Additionally there is a super hard solder called ITC and a super easy solder)
stamp (for metal purity)
-a fancy little friend to make your jewelry legit! they have stamps for all the metals and in different font sizes. they also come in bent or straight. the bent ones are used with ring stamping blocks for rings that are particularly rounded or just already assembled. the straight ones are for flat pieces to be used on regular steel blocks or anvils.
sterling silver vs silver
-pure silver is an element on the atomic table of elements (when used in jewelry it is marked ".999", for aaaalmost pure). it is a little too soft to be used as silverware or jewelry, so people figured out that they can add a little bit of copper (or other things) to the silver to make it harder, a stonger alloy (alloy is a metal which isn't a pure element but rather a mix). Sterling Silver is the name for the alloy that is 92.5% silver, the other 7.25% can vary, but the common thing is for it to be copper.
torch
-i use a tiny butane refillable torch that you could make creme brule with! i am afraid if i use a giant torch my house will exploud... but there are all kinds of torches that would work well.
tumbler
-tumblers are super convenient, another of the very few pricey things that i don't regret getting. there are both rotary (what i used in this project) and vibrating tumblers. these are the same thing you would use if you wanted to get into rock tumbling yo! you put in different filler aka media, and the media tumbles all over the pieces you add and gives a nice even finish while you watch tv.
tweezers
-metal tweezers for handling hot pieces! bigger than swiss army knife ones, ones about the length of a pen are the handiest. there are soooo many kinds... you can end up with a pretty big tweezer collection...
where/what to buy
Everything I used in this instructable can be bought from riogrande.com, they are pretty fairly priced, though I got my baby torch from amazon for significantly less. And some tools from rude ebay sellers...
oh, and only dickblick.com has my favorite sulphur-> http://www.dickblick.com/products/liver-of-sulphur/
Here is a list of specific supplies and their item numbers from riogrande,
many are optional and the 'cheapest' versions are included when appropriate
100414 Sterling Silver Half-Round Wire, 14-Ga., Dead Soft 1 pieces of 1 feet 0 inches
502063 Solderite Pad, Hard, 6" x 6"
502005 Ceramic Honeycomb Block
112218 Rawhide Mallet 1
112211 Ball Peen Hammer, 8-oz. head 1
115080 Economy Diamond Tweezers, Fine Tip 1
501012 Little Dipper Economy Pickle Pot 1
501017 Heavy-Duty Bent Copper Tongs 1
5010233 Rio Pickle for Non-Ferrous Metals, 3 lbs. 1
337308 3M Tri-M-Ite Imperial Polishing Paper Assortment 1
337342 3M Abrasive Paper Assortment, Set of 16 1
11213001 Marking Stamp "925", Bent Shank, 1mm 1
112560 Steel Bench Block, 2 x 2 x 3/4" 1
1120852 Ring Marking / Stamping Anvil 1
101702 Silver Sheet Solder, Hard 2 pieces of 2 X 1 inches
111627 Flat-Nose Pliers with Nylon Jaws 1
500230 Blazer Butane Torch 1
500181 Butane Cartridge 1
114257 Miniature Needle File Set 1
114702 Friedrich Dick Flat Hand File 1
111237 German Shop Shears, Straight Tip 1
110130 Jeweler's Saw Frame 1
110192 Jeweler's Saw Blades 1
116021 Standard-Width Finger Gauge Set 1
112575 Durston Hardened Ring Mandrel, 16" 1
112366 Tapered Ring Mandrel 1
331033 Midas Liver of Sulfur XL Gel 1
202210 Dura-BULL Single-Barrel Rotary Tumbler, 110-120V 1
339097 Stainless Steel Shot, Mixed 1
339416 Ceramic Aluminum Oxide Cylinder Media, 5/32" (4mm) 1
504086 Handy Flux for Soldering and Annealing 1
504009 Non-Contaminating Flux Brush, #1 1
115189 Electronic 4" Digital Caliper 1
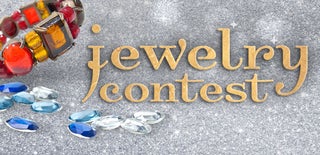
Second Prize in the
Jewelry Contest

Participated in the
Craft Contest