Introduction: Laser Cut Omni Wheels
Being a mentor on a FIRST FRC robotics team (Go Team Beta!) is a demanding calling. You end up giving a lot of your time, talent, and energy to the team and community as a whole. But the benefits far exceed the costs. Watching the student grow and mature, succeed at challenging problems, and consider career paths that they at one time considered inaccessible is payment enough, but the benefits don't end there. One of the many other benefits is being inspired to take on personal projects that you wouldn't have considered otherwise.
For me, one of those inspirations is building a kiwi drive robot.
Two "in process" bots are shown above. The larger is a 11.75" by 15.75" oval and the wheels are 5.5" in diameter. Planned controller is an arduino, raspberry pi, or Freescale ARM Cortex development board. (The half hidden yellow plate is for a raspberry pi.) The smaller bot is 6.75" in diameter, with 2.00" diameter wheels. Planned controller is a TinyDuino from tiny-circuits.com. (The green stack is the actual size of four TinyDuino boards.)
Step 1: What's a Kiwi Drive?
As shown above, a kiwi drive robot uses three specialized wheels called omni wheels. An omni wheel has rollers along its circumference so the wheel can drive in its direction of rotation, but easily slip if a force is applied perpendicular to it. By controlling the speed and direction of rotation of the three wheels, the robot can be driven in any direction, without changing its orientation.
Can I go out and purchase manufactured omni wheels? Absolutely, but where's the fun in that! Especially when you're trying to push the boundaries of what is possible.
Is it possible to design an omni wheel that can be cut from eighth inch stock? Yes, and here are two designs.
Step 2: 5500 Omni Wheel Overview
The first image above shows the front, isometric, and side views of the 5.5" omni wheel.
The rollers are made from fourteen 1/8" wide disks mounted on a 3/16" shaft. Disks are cut to different diameters to follow the arc of the wheel's circumference. As you can see in the CAD drawing below, the disks add "teeth" to the circumference that will give it better traction on carpet. The disks can be made from any material such as wood or plastic, but if the robot is going to be let loose on hard surfaces a hard rubber would probably be best. The wheel design allows you to easily change the disks if they are damaged or you need to change the disk material.
The wheel is made of an inner and outer assembly and the assemblies are offset by 30 degrees. The wheel is designed for a 1/4" hex shaft. This means that the five pieces in each assembly that have a shaft hole are different from the five pieces in the other assembly. This doesn't increase the number of parts needed, but may increase the cost if the design is set to an outside house.
Step 3: 5500 Omni Wheel Parts
The above pictures show the parts that need to be cut before the inner and outer assemblies can be put together into a single wheel. Note that a kiwi drive robot requires three completed wheels.
The attached zip file contains the Bill of Material for a complete wheel and Corel Draw files of the parts that need to be cut.
WARNING: The outlines in the Corel Draw files have not been offset to accommodate for the width of the cutter. If you use a laser cutter to make these parts, you must account for the width of the laser beam to cut accurate pieces.
Attachments
Step 4: 5500 Omni Wheel Assembly - Step 1:
Start with six of the male-female #6 standoffs, six of the female-female #6 standoffs and one of the outer plates for the inner assembly. Attach the spacers through the plate as shown in the figure. Note the holes that are used, or the roller support beams will not fit on the next step. Leave the standoffs loose for now. The M/F standoffs have to be aligned with the roller support beams later. An inner assembly torque plate can be placed in the center of the outer plate with the shaft hexagons aligned.
Step 5: 5500 Omni Wheel Assembly - Step 2:
Take six of the roller support beams and lay them on the outer plate so that they touch the torque plate and the hex standoffs. You have to place them so that each beam only touches one side of the torque plate. When your done with the assembly, you'll see that these beams end up supporting the right or left sides of the rollers. You can also place six of the #6x0.125" spacers on the outer plate, but there will be nothing to hold them in place until you put in the screws later. (There is room to put them in later with a pair of needle-nose pliers if you so desire.) Finally, place the inner assembly - inner plate on top of the roller support beams so that the notches in the beams line up with the inner plate and the inner plate sits flush on the torque plate.
Step 6: 5500 Omni Wheel Assembly - Step 3:
With the first six roller support beams in place (now gold color in this step), place the remaining six roller support beams into the inner plate. The second inner assembly torque plate is now placed between the beams. Like before, six of the #6x0.125" spacers can be placed on the plate, but there is nothing to hold them in place until you put in the screws in the next step. (There is room to put them in later with a pair of needle-nose pliers if you so desire.)
Step 7: 5500 Omni Wheel Assembly - Step 4:
Place the second inner assembly-outer plate on the top of the assembly and screw six #6-32 x 0.250" screws into the #6 0.375" standoffs. Six #6-32 x 0.750" screws are placed in the other six holes, through both of the spacers. If you decided to put the spacers in with needle-nose pliers, now is the time. You can now tighten the F/F #6 standoffs from step 1.
Step 8: 5500 Omni Wheel Assembly - Step 5:
Repeat assembly steps 1 through 4 (Instructable steps 4 - 7) to build the outer assembly.
Step 9: 5500 Omni Wheel Assembly - Step 6:
Connect the inner and outer assemblies by screwing the 0.750" screws into the hex standoffs of the other assembly.
Step 10: 5500 Omni Wheel Assembly - Step 7:
Put a roller axle through a roller support beam. Thread fourteen disks through the axle in the following order ABCDEFGGFEDCBA. Slide roller axle through the other roller support beam.
Step 11: 5500 Omni Wheel Assembly - Step 8:
Attach an axle support piece on one side of the shaft you just placed. It requires one #4-40 x 0.750" screw, a #4-40 nut, and two #4 x 0.125" spacers. If this is the first roller you are putting on the assembly, place the second axle support piece on the other side of the roller.
Step 12: 5500 Omni Wheel Assembly - Step 9:
Repeat assembly steps 7 and 8 (Instructable steps 10 ann 11) for the rest of the rollers. The omni wheel is now complete.
Step 13: Reality Check
These instructions assume that the tolerances on all the pieces is near ±0.000. This is not reality. The biggest problem this design faces is the tolerances on the thickness of the material used in the cut pieces. I've seen acrylic sheets with a listed tolerance of ±10%. If this wheel is cut from a sheet that is 0.113" thick (-10%), every piece will be loose and if it is cut from a sheet that is 0.138" (+10%), nothing will fit.
This design calls for material that is inspected before it is cut. Acrylic or PETG thickness will have to be matched. It should be possible to find dense wood that is held to close tolerances, but it may be expensive.
The other problem is the inside corners when laser cutting. The laser beam is round and will leave a rounded edge on any inside corner. If the material is thin, the radius will not matter. If the material is right at the correct thickness, the rounded edge may prevent the pieces from mating. The solution is to file the corners or introduce a relief cut in the cutting path. The figure above shows an inside 90 degree corner with a 0.005" diameter beam. The distance from the laser's edge to the ideal corner point is about 0.001". If this is the resolution of the cutter, it may be difficult to correct for.
Step 14: 2000 Omni Wheel
The major flaw with the 5500 omni wheel is the need to cut multiple pieces and layer them up. The cost and design complexity really begin to add up quickly. If the cutter was capable of cutting 0.375" material, the inner and outer assemblies become two pieces instead of ten and all of the 0.125" spacers and all of the M/F standoffs are completely eliminated.
If a 5.5" diameter wheel is too large to cut, what size wheel can be cut from 0.125" material? I have designed a 2 inch diameter wheel, and 1.5 inch also seems to be possible.
The image above is a completed 2 inch wheel. Each assembly requires some precise drilling after cutting for the roller axle. The hex shaft makes it easier to fixture and align each assembly while drilling.
Each roller is made of ten disks instead of the fourteen in the 5500 wheel. The roller axle is two pieces, a 0.032" x 0.875" piano wire that goes through the assembly, and a 0.063" OD x 0.500" tube between the piano wire and rollers. The rollers are not easily changeable as the piano wire must be held firmly in place.
The inner and outer assemblies are one piece each, with a single 0.125" laser cut spacer between them. The wheels are held together with three #2 x 0.375" screws. The outer assembly and center spacer have through holes. The inner assembly part is tapped for the #2 screw. Threadlock should be used to keep the pieces together.
Step 15: Conclusion
Without a laser cutter, I am left with two options, sending the files out to a service, or cutting prototypes on a jigsaw. So, as I sit in front of my jigsaw with my safety glasses on, contemplating the hours of cutting and filing I have in front of me, I can't help but think, “Wow, this would be a lot easier if I had a laser cutter!”
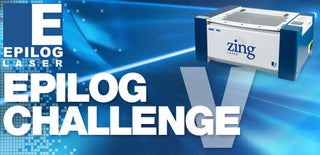
Participated in the
Epilog Challenge V