Introduction: Laser Marquetry From a Photo: Kaleidoscope Algorithm
Kaleidoscope Algorithm is an exhibition of work based on computer image manipulation algorithms translated to laser-cut wood marquetry. This series of 30 artworks is based on images from corresponding top Google search trends for each day in September 2011. The Kaleidoscope Algorithm exhibition is on display at the Lois Lambert Gallery in Santa Monica, CA through May 6, 2012.
All 30 works and process videos can be viewed on my website, christyoates.com
This instructable is entered in in the "Make it Real" Challenge to win a 3D printer, and votes are appreciated!
I am also a finalist in a contest to win a laser from Hurricane Lasers, and I'd also REALLY appreciate votes for my entry on their site:
http://hurricanelasers.com/facebook-contest/
Description:
I used Adobe Illustrator's live trace function to generate a vector file, then mirrored and repeated the objects in Rhino CAD to create files for laser cutting. The files were cut from Alder, Walnut, Bubinga, Zebra Wood, Purpleheart, and Wenge paper-backed veneers.
Image to Laser Marquetry Process:
I chose randomly generated images from corresponding Google trends for this project, but you can use any image to turn it into marquetry.
- Import your image into Adobe Illustrator and use the live trace function to turn it into a vector image (I started with a 6-color trace option then adjusted my settings/constraints to get my desired effect) You want to adjust your settings so the parts are not too small. Any parts smaller than 1/16" almost disappear when cut.
- After you've got the image converted to your desired effect, seperate each color into a layer. These layers correspond to whichever woods you chose for your project.
- Mirror, copy, or manipulate the layers to your desired effect. I chose a kaleidoscope pattern. Nest your parts closely together to conserve material (At this point, I used the Rhino Nest plugin for Rhino CAM because I had lots of parts, but Illustrator works fine as well).
- Cut each layer from its corresponding wood on a laser cutter. Settings depend on your laser's power, and you can find this information on your manufacturers websites and forum sites like www.cnczone.com. Mostly though, these settings are trial an error to find the best speed, power, and focus.
- Assemble your parts using blue tape on the back. Then mask the front with tape and remove the blue tape from the back- the tape you use on the front will depend on the glue you choose.
Veneering Process:
There is a lot of information on the internet for veneering and I would recommend reading up if you've never done it. http://www.joewoodworker.com/ has great information on veneering and all the tools you need to help you get started. Here are the basics for this project:
- Find a substrate to glue your parts onto. MDF works best. Anytime you glue veneer to a substrate, you need to glue front and back so the piece doesn't warp. Use the same thickness veneer on the back side.
- Glue the parts to a substrate. Make sure you uniformly clamp the piece. I recommend using a pressurized vacuum bag.
- After the glue dries, sand and finish as desired.
Good luck!
I've included the pdf cut file. If anyone tries the process, I'd love to see pictures and post them on my website.
Attachments
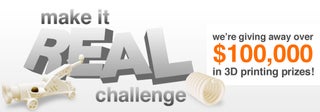
Participated in the
Make It Real Challenge