Introduction: Leather Tool Holder for Scallywags and Tinkerers
There are so many fasteners in the world, and so many bits to go with them. This case is to take to project bigger than a cell phone and smaller than car. I mostly intend to use it for fabrication, working on machine tools, my telescope, and appliances. I needed someplace to stash common metric and imperial bits, some bit holder handles, a small wrench, and some pliers. It has a removable cover to keep metal swarf and dust away from the magnetic bits, a handle that can be moved out of the way, hinged pallets to make it easier to see and grab bits, and is open on the bottom so it can be blown out with compressed air. The general idea is to avoid making trips back to my big toolbox and keeping bits in their final storage as I use them, rather than collecting a pile of bits that has to be sorted and put back at the end of a project.
I'll spend some time talking about how to make square cuts, use dividers for layout, make a topcoat finish, measure for pallets, and fit hardware. Some measurements are listed. But since I doubt many folks have the exact same collection of tools and bits, it is more a discussion about how to organize and layout bit holders than a set of plans.
Tools
Powered: vintage Singer walking-foot sewing machine, miter saw, rotary tool, hand drill
Layout: Starrett spring divider with round legs, Pentel Graphgear 500 mechanical pencil with soft 0.9 mm leads, 12" rule, 6" rule, yard stick, plastic squares
Cutting: Gingher 10" forged scissors, Swann-Morton scalpel, large end nippers for pulling rivets
Leather: set of hole punches, seam ripper, squeeze action micro scissors, letter stamp set
Hand: ball pein hammer, transfer punch set, hex/allen driver, p1 Phillips screwdriver, clamps
Supplies
Dye/Coatings: Fiebings Professional Oil Dye in black, bee's wax, mineral oil, neatsfoot oil, Fiebings Resolene, barge cement, Black Magic patina, yellow glue
Hardware: leather rivet assortment, button studs, Chicago screws, screw assortment, pop rivets, hinges
Materials: resawn white oak or mahogany, tanned leather hide, milled leather hide, wood scraps for clamping
Step 1: Arrange Your Tool Collection
The first task is to identify the minimum height and width of the pallets. What is the longest bit, and what is the widest set? The pallets can be bigger than that, but not smaller. My goal was to have all of the bit tips flush with the top edge of the wood backer boards. I left some unused space to accomplish that, and still had one pallet with two rows, but generally was able to make really fast access to almost everything in the case. I've made tool organizers that required some fumbling, or two hands to get to things, and wanted a more ergonomic design this time.
The second photo jumps ahead in the build process, but shows how the tools are arranged.
Step 2: Layout Sleeve Sizes
Good dividers make this step so much easier. Starrett makes really good tools. These are quality tool steel instruments that are heat treated to perfection. The moving parts are all silky smooth. They are tough enough to punch through leather, and make a nice dent for your mechanical pencil to find when connecting points. They are set to a distance with an etched metal rule, or from marks that need to be repeated.
The distance to layout between the sleeve tubes will depend on the thickness of the leather. I've tried a measuring tape, but the easiest way to lay these out is to mock-up a sleeve with scrap pieces. Loop the leather over the bit shaft, push it down tight against the bit, and mark the seam on the pallet back piece, and the piece that loops over the top. Then use a pencil to mark a square seam line on the back piece and top, and sew it to test. When the measurements are in hand set dividers for the top and bottom using the pencil marks as a guide. Walk the dividers to mark the stitch lines, and either connect two rows of marks or create a single row and use a triangle to create a stitch line. Create stitch lines on both the top and bottom pieces.
The height of the panel is about 1/3 the length of the bit.
Step 3: Cut Square Panels for Pallet Backs
The photos are mostly annotated, but the general idea is to avoid creating a parallelogram. Create an initial horizontal reference line, then keep one side of the triangle on that line for the two vertical lines. Connect the top lines, and make sure the diagonal measurements are both the same to verify square corners. Since I made multiple pallet backs the same size, I created a cardboard template. The template is used to mark corners on the leather, then the corner marks are connected with a straight edge. The corners are marked using the dividers as a punch.
Step 4: Layout Wide Pockets
This is mostly annotated in the photos. The general idea is to allow for the height and width of the bit set, plus enough material to get under the presser foot. Cut the corners out up to the stitch lines. Wet the pockets and clamp a board over the top to wet mold to fit your tools bits. I had to buff surface rust off my bits after I wet molded, I should have coated the bits in beeswax first.
Step 5: Sew the Sleeves
I'm running a old Singer walking foot machine. I'm not that great at sewing straight lines (shown), so I put a stepper motor upgrade on the machine to slow it way way down. It works great. For my skill level, the machine was nearly unusable without this.
Sewing these seams is one of the hardest part of the project. This could be done with hole punch forks and two needles, and would make a stronger seam, but it would take a while.
I can't fully describe how to keep the seam marks on the top and bottom aligned when sewing, but will try. I align the top and bottom panels, and drop the needle to hold it in position. Then I align the bottom marks, and hold everything really tight using both hands. The bulge of leather will push the stitch off the line, so one finger goes against the presser foot, and the thumb on the bottom side to sort of pinch the layers of leather together, and at the same time against the foot. Then the other hand holds the bottom marks aligned. As the machine sews watch to stay on the line, and watch the bottom marks stay aligned. Once there is about an inch of seam it gets easier, but keep a seam ripper handy.
I like micro-scissors for trimming loose thread, and use yellow glue on the hidden side of the seam.
Step 6: Wet Mold the Pockets
A couple clamping arrangements are shown. I ran the leather under warm water, and clamped overnight. In one case I only clamped for about an hour, and it seemed to hold the shape pretty well.
To keep the nut driver heads at the same level, a board is used to push against. I pushed pretty hard to get them to the same level by forcing the ends into the bottom pocket, then clamped it in place.
Step 7: Make a Holder for a T-handle
Create a large pocket like in the earlier step, leaving a cutout for the bit holder chuck. Loop a sleeve over the chuck. These are big pockets. During the finishing step I use Resolene to stiffen up the leather and keep it from folding over when the tool goes in.
Step 8: Hinge the Front and Back Panels
Or, "what the round end of a ball pien hammer is for" . . .
I'll jump ahead and say the round end of a ball pien is for spreading out metal. Drill 1/8" holes through the steel and wood, put the rivets in, and pop them. It leaves an ugly nub that turns into an ugly puck shape when hammered flat. Pein the puck into a dome with the hammer to make fair lines.
I skipped the step about cutting the wood. Just make a rectangle a little bigger than the pallets, and cut in the miter saw. This is resawn white oak from Sears Trostel in Fort Collins, CO, USA. It is hard to find, even at hardwood suppliers. It is planed on both sides to about 5/16" thickness.
I fumed the oak with household ammonia by wiping it with ammonia, and sealing it in a plastic box with ammonia poured in the bottom. It is a cumbersome process, but I think it is worth the effort.
Step 9: Layout the Front and Side Panels
To keep things symmetric for the front panel, I sketched one corner, then folded a piece of heavy paper into fourths and cut the shape like making a paper snowflake. The shape is transferred onto the leather using the cutout as a template. Use the dividers to layout the rivets.
Important note on laying out rivets: start at the center of the top and work down the right side to the center of the bottom, then go back to the center of the top and mark rivets down the left side ending at the center of the bottom. If the distances don't perfectly add up, there is one extra wide gap centered at the bottom, rather than an off-center gap at the top.
Drill punch and set the rivets.
My daughter said this bit case looked like something a pirate would bury on the beach, hence the 'scallywag' in the title. To get that vintage pirate look, the finish is sanded off the rivets and they are blackened with a metal sculpture patina. Careful with this stuff, it will make your nose bleed if you breath too much of it. But after stamping the rivets with an X, the patina ages and darkens the metal so it doesn't look so upholstered.
I used milled leather for the sides since it is more flexible. Allow enough material to wrap around to the back of the case. In hindsight, I would have made separate panels for each side.
Step 10: Make a Handle
There are better write-ups on making a handle than this. I saw one person glued a stack of strips in place, then sanded it down to a fair shape. Overachievers if you ask me (kidding). I was low on glue so I made a stack of successively shorter straps, marked the center of everything, lined it up, and put a stitch down the center. The stitch starts at the center and runs out.
Also shown is the top cover. Two strips sewn to a flat panel.
Step 11: Dye the Leather
The company that sold me the 32oz bottle of Fiebings Pro Dye had a video that suggested dipping the leather, so I tried it. I can't help but wonder if the fact that relative to wiping on, this process uses about 4x as much premium dye. But it came out really good. It dyes the leather all the way through, and get inside the sleeves.
I like the long wrist nitrile gloves. The dye doesn't soak through like happens with latex gloves.
Hinged pieces are finished with neatsfoot oil, stiff pieces get Resolene.
All of the bits and leather get a coat of beeswax and mineral oil as a final finish. It looks a little rough, but is waterproof and smells good. I mix my own to get a very stiff consistency. George's Clubhouse wax is pretty much the same thing if you don't want to mess with melting wax. Either one can be buffed to a dull shine, but I don't bother. This is a working tool holder, not art.
Step 12: Final Assembly
Attach a 1" wide hinge flap to the bottom of the backer boards, before attaching the leather pallets. Arrange the leather pallets back-to-back, and punch through both pieces, then drill through the punch hole to make room for a Chicago screw to hold both pieces of leather to the wooden back. I have an assortment of screws with the same thread pitch (8-32) as my Chicago screws so I can pick a length that fits depending on how many layers I connect.
After attaching the hinge flap and leather pallets to the backer board, fill the pallet with tools to gauge the clearance between pallets. Then attach the hinges to the wooden base. The base is sized by stacking the pallets and measuring the combined height.
I didn't have any 4mm screws for the button studs, so I used what came with the studs. They are short and designed to attach to leather, not a board, so I countersunk the hole with a forestner bit to account for the short factory screw.
A washer is used for the straps that hold the back. It lets the sides move as you carry it, and keeps the leather from gaping open.
Wrap the sides with the milled leather, mark and cut button holes, then trim any excess leather.
Button holes are punched about 1/2" apart, then a slit is made with the scalpel to connect the holes.
That wraps it up. Thanks for checking it out.
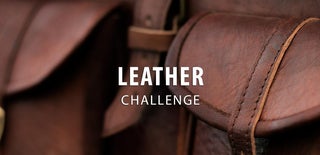
Second Prize in the
Leather Challenge