Introduction: Live Edge Reverse Waterfall Floating Shelf
In this build I will combine a few woodworking concepts that I enjoy into one easily-buildable project that will bring a functional and attractive natural display shelf into your home. Live edge furniture, floating shelves, and waterfall joints have all become popular in their own right, and this build incorporates all three to produce a beautiful, never-before-made bookshelf. If you enjoy this project and want to see more builds like this, follow me on Instagram @Resourced_Woodworking and vote for this in the Instructables 2018 Furniture Contest. Before we get started on the steps, here are the tools and materials that I used, along with optional substitutes in parentheses:
Rough sawn wood slab
Table Saw (miter or circular saw)
Bandsaw and circular saw (jigsaw)
Jointer and Planer (hand tools)
Festool Domino (biscuit jointer or dowel jig)he
Random orbit sander
Chisels
Epoxy (wood glue)
Oil varnish finish
Step 1: Rough Milling
If you're familiar with the lumber milling procedure then these steps should be commonplace to you, but let's take a look at the process I utilized. I had a 13" wide and 7' long cherry slab that I picked up from a local sawyer in New England that was the perfect size for this project. It was fairly flat and had no serious checking so I didn't have too much work cut out for me in regards to getting it milled flat.
I marked out the approximate dimensions of the shelf using white chalk onto the rough-sawn slab and cut it to length (52") using a circular saw. I then took the slab to the bandsaw to cut off the back edge of the piece. (Tip: While you'll use a jointer to clean up this edge, try to cut as straight of a line as possible to save yourself some additional work later.)
I then moved to the jointer to flatten one face, and then used that face against the jointer fence to clean up the edge that I cut with the bandsaw. With the face and edge now flat and at a perfect 90° angle relative to one another, I ran the slab through the planer to clean up the other face of the board and thickness down to my approximate desired thickness, 2". (Tip: Since even slight wood movement is unavoidable after rough milling, allow the board to rest for a couple of days before running it through the jointer and planer again to ensure that it is perfectly flat and at your final thickness.)
I'll also lend some attention to the live edge of this board before we get too far into the rest of the build. In this case, these boards were originally slabbed in the summer time and then air dried for a couple of years, so the majority of the bark had already fallen off. If you need to remove bark on a live edge, there are a number of options including using a draw knife, chisels, sanding, or the newly popularized Restorer from Porter Cable. Likewise, if you want to retain the bark on a live edge piece, options available to you include obtaining boards that were slabbed in the winter (when the sap in the tree is not flowing), buying kiln dried live edge lumber, using epoxy or CA glue to stabilize any loose chunks, and/or applying a thorough coating of thinned shellac to the bark to help it harden. In my case, all I needed to do was clean off some of the remaining outer bark and hand sand the edge smooth. I opted to maintain some of the inner bark, which helps reinforce the natural aspect of this piece and add a nice color contrast relative to the milled faces of the board.
Step 2: Creating the Waterfall Joint
The idea behind a waterfall joint is that you are cross-cutting a board at opposing 45° angles, allowing you to "fold" the board across the cut angle so that the grain of the wood seems to run uninterrupted along the joint, resulting in an effect that resembles a waterfall. The most common usage of waterfall joints in woodworking is to create a coffee or side table where the top and leg(s) of the table are both produced from the same section of a board (a google search will better illustrate this concept). But there's no reason that a waterfall joint has to angle downward! After some brainstorming on this concept, I realized that an upward waterfall (aka a "reverse waterfall") would be perfectly suited as a bookend on a shelf. As such, this project was born.
Cutting a waterfall joint is not overly complicated, but the effectiveness of the concept is accomplished with the precise execution of cuts. A table saw or track saw will produce the best result and the cleanest cut, but in theory nearly any type of saw (band, circular, jig) can cut a waterfall joint. Taking a look at the pictures above, you can see how I managed to cut a perfectly tight joint.
I began by first marking out on my board where the placement of my waterfall joint would be. (Tip: It's important to visualize how you want the board to fold so that you can mark out where the waste will be once the cuts are made - otherwise you may realize after your cuts that your board folds in the wrong direction!) I then set my table saw blade to exactly 45° using a digital gauge, and made the first cut ensuring that the board was securely aligned with the fence on the saw to produce a perfectly straight cut. By taking the offcut and rotating it 180° on the same face, you can now cut the other side of the joint. The important part here is ensuring that you remove as little as possible from what will be the outer face of the joint (the longer end of your 45° angles). If you shave off even a few too many millimeters from from this outer edge, the grain of the wood will not completely line up in the finished waterfall joint. A thin kerf blade on your table saw will help to remove the least amount of this outer face.
In the pictures above you can see that after your two cuts, you'll be able to lay the boards end to end in the same orientation that they were originally, and it appears that a wedge has been cut out from one face of the board. (Tip: Since most live edges have a natural angle or curve on them due to where in the tree/log they were slabbed from, you need to decide if you want your live edge slanting up toward the ceiling or down to the floor, as this will determine which face of the board will have the wedge removed from it. You can get a better feel for this concept in this guide's cover photos.)
Since my table saw blade left some slight burn marks, and more importantly because I wanted to ensure that both sides of this joint were absolutely flat relative to one another, I threw them in my workbench's vise and took a jack plane to the cut face, taking light passes and ensuring that I was centered on the face to clean both of these ends up.
Step 3: Prepping and Gluing the Joint
In order to apply good clamping pressure to this joint and ensure a tight glue seam, we need to get creative. A 90° angle jig or some angle clamps can suit many mitered angle glue ups (such as picture frames), but these are beefy 2" thick boards and I want a little more pressure. I begin by cutting some 3/4" plywood strips to 2" wide and 12" long (a little wider than the width of the shelf), and then giving one edge a rip on the table saw with the blade angled to 45°. Then I laid the newly cut cauls on the outer faces of the boards, about 1" from each edge of the waterfall joint with the angled edges pointing in opposite directions (see pictures above). Apply a little bit of wood glue and make sure the the cauls are lined up perfectly parallel to the waterfall joint edges, and clamp them down to dry.
With the cauls now attached, I can do a dry fit with clamps to make sure that the joint seam is perfect. If it's not, return to the workbench with a hand plane to continue to work the joint's problem areas. With the shelf dry fitted, I can see that I need to do a little clean up work on the live edge. Since most trees don't have perfectly straight sides, there may be a slight variation in how the live edges meet up in a waterfall joint (remember that I cut out about 3" from the inside face of the live edge when making my angled joint cuts in the last step). Some gentle attention with a rasp or file will shore up the live edge seam and make sure that all of the lines will meet up cleanly. (TIP: use a pencil to shade in the areas that need to be removed from the edge, so you can monitor your progress while you do any filing.)
Now let's bust out one of the coolest tools in the woodworking kingdom: the Festool Domino. This is a very expensive tool as most of you woodworkers are aware, and I am a proud recent purchaser of a DF500. No tool does better what the Domino is designed to do, and while you can find ways to accomplish similar joinery - in this situation using a biscuit jointer or a homemade 45° doweling jig - the Domino makes quick work of this task.
The idea here is that I will be using floating tenon joinery to attach the two ends of the shelf together. The Domino guarantees proper alignment and strength in this joint, and the process is a breeze. I need to make reference marks for both boards on the inside edge of the waterfall joint, which I do with a machinist's square. With these in place, I simply have to set the proper angle on the Domino (45° obviously), and adjust the cutter head position close to the inside edge of the joint. (TIP: when using a Domino, make sure that you consider the length of the tenon stock - and the subsequent plunge depth of the cutter head - to ensure that you won't be removing material too close to the outer face of the piece.)
With the mortises cut into the joint edge, I put the Domino tenons in place and do another dry fitting to make sure that everything aligns properly. With a green light, it's time to epoxy this joint. I prefer epoxy in larger glue-up situations, as it gives a little more working time than typical wood glue. I use West System epoxy, which contains a resin and a hardener, mixed in the correct proportions. I begin by using just the resin to fully cover the surface of the joint, repeating as necessary until fully penetrated (since this joint is mostly end grain, the wood will absorb several applications of resin). When I see the wood stop absorbing so much of the epoxy resin, I mix a batch of resin and hardener together and liberally apply to the joint edge, the mortises, and the tenon stock. Slide the two ends of the shelf together, apply a few clamps to the cauls, and wipe off any squeeze out from both the inside and outside seams. (TIP: When preparing to do any sort of glue up in your projects, think ahead a few steps to the finishing process. Since sanding the inside of this 90° angle will become more complicated after the glue up, I sanded the top and inner side of the shelf up to 150 grit, taking care of the bulk of the work that will be more tedious with the two pieces glued in place.)
The last step here is to remove the cauls. Being careful not to disturb the face of the shelf, take a chisel and mallet and break apart the plywood parallel to the shelf face. Plywood is ideal to use as a caul material as the layering of the plys allows for them to be separated easily. Once the bulk of the plywood has been removed, a random orbit sander makes quick work of the remaining caul material and glue to reveal your newly glued waterfall joint.
Step 4: Cutting Mortises for Mounting Hardware
With the shelf now fully assembled, we need to figure out how to mount it. Other projects on here have detailed the use of floating shelf hardware, and I got the kind I'll be using on this shelf from Rockler. This style consists of a mounting plate that attaches to the wall with two screws, and a 5" pin that connects to this plate and slides into a hole that's been drilled into the shelf material. Since this shelf is a little larger and has a more storage capacity than many other floating shelves, I'll be using four mounting brackets to ensure that the shelf stays where I want it to... (aka on the wall).
Since my workshop and my home are not in the same place, accurately transferring the locations of my wall studs relative to the placement of my shelf can be difficult. That's why I'm employing a common method for marking and transferring measurements: a story stick. The idea here is that a small scrap piece of wood can be trimmed to the same length and thickness as my shelf, and I can mark out the location of my mounting hardware on this piece. I can then take it back to my shop, transfer the layout lines, and cut into the workpiece.
With the mortises marked on the back edge of the shelf, I hogged out most of the material with a router, setting the depth just shallow enough that the mounting hardware will be concealed when the shelf slides fully onto the pins. After going as close to the lines as I was comfortable doing freehand with the router, I cleaned up the mortises all the way back to the lines with chisels, and then test fitted one of the mounting plates. Having a little bit of play in these mortises isn't necessarily a bad thing, as you won't be severely punished if you are just slightly off during the mounting process.
To mark out the location of the hole I need to drill for the mounting pin, I use the mounting plate as a guide for a punch, which sets the exact point for the hole. Not only does the location need to be precise, but the angle of the hole also must be perfectly straight. Since the depth of this hole requires an extra long drill bit, I cant fit this bit into my drill press and have to do this by hand. (Tip: if needing to drill a perfectly straight hole by hand, utilize a drill guide block. These can be bought for various bit sizes, but you can make them yourself with a piece of hardwood and a properly calibrated drill press.)
Step 5: Sanding and Finishing
With all of the assembly and mounting holes taken care of, it's time to dive into one thing that I truly hate (sanding) and another that I truly love (finishing). As I mentioned before, I sanded the inside face of this board up to 150 grit before the glue up, but now I made sure the entire piece was tediously sanded up several stages of grits (80, 120, 150, 220, 320, 400). Before applying finish, I wiped down the entire board with mineral spirits to clean off any remaining dust left over from sanding.
My go-to finish is Arm-R-Seal from General Finishes, which is an oil-based varnish, as I find it's super straight forward to apply and produces a crystal clear, beautifully smooth finish surface. The wood is very thirsty at this point (this is especially true with live edge lumber that contains sapwood), so for the first coat I apply the varnish generously, allowing the finish to fully soak into the wood grain. Once it's saturated, I very lightly make long strokes along the wood grain with my finishing rag to remove any lines or swirl marks before flipping the piece over and repeating the process on the other side. (Tip: You always want to apply finish to the "show side" of your piece last, as this will ensure that any potential marks left over from your painters pyramids or other support bases wont dry on the side that is predominantly visible in the final piece.)
After the first coat is fully dried, I lightly sand both sides of the piece with 600 grit sandpaper to remove any nubs or unevenness before giving the piece a very light wipe down with mineral spirits to clean up this finish dust. I then repeat this entire process 2-4 more times depending on how durable I want the finish to be (in this case, I did four applications of finish). After the last coat has dried, I lightly sand with 1000 grit and wipe off any dust, leaving behind a gloriously bright finish that is just about the smoothest surface you've ever felt.
Tip: The finishing process used to seem intimidating and daunting to me when I first begain building nicer pieces, but this great video from one of my woodworking heroes Matt Cremona sheds some light on the finishing process that I detailed above. I highly recommend giving it a look if you want to take your finishing skills to the next level.
Step 6: Mounting and Final Thoughts
With the piece home and ready to be mounted, I needed to come up with a way to perfectly align the shelf relative to the wall studs. While the story stick ensured that the mounting plates are properly spaced along the back edge of the shelf, I needed to transfer the location of the screws such that the mounting pins will be perfectly situated to slide easily into their accompanying holes once installed on the wall.
To accomplish this, I laid some double sided tape into the mortises, inserted some short screws into the mounting plates and then attached the pins before sliding them into place on the shelf. This holds the screws pointing outward in the position that they will be mounted into the wall. These shorter screws allow me to align the shelf next to the wall where my indicator marks are, and press the shelf into the wall to transfer the points of the screws into their final placement on the drywall.
With the points marked out on the wall, I drilled pilot holes into the studs to hold the longer permanent screws, and then mounted all four brackets onto the wall. Now came the moment of truth, and thankfully the shelf slid fairly painlessly onto the brackets and up against the wall. Phew. It wasn't a minute later when my girlfriend walked into the room with armfulls of books ready to see how well I did, and the shelf didn't budge a millimeter when weighed down fully with books.
This was a fun and relatively quick project that utilized a number of unique woodworking concepts to create a deceptively simple piece of furniture that just about everyone asks about when they walk into the room. The beautiful live edge perfectly contrasts the rich color of the cherry, and the seamless grain running up the side of the shelf really illustrates how nice of an effect a waterfall joint can impart.
Please share any thoughts or questions about this build below, and if you enjoyed this project, follow me on Instagram @Resourced_Woodworking and vote for this in the Instructables 2018 Furniture Contest. Thanks for reading!
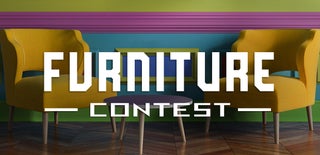
Participated in the
Furniture Contest 2018