Introduction: Live Edge River Coffee Table
Live edge wood is great. Live edge wood coffee tables are greater. Live edge coffee tables with glass down the center are the greaterest. This project was inspired by some of Greg Klassen's work, and is deceptively simple. All up it was about a week of work for a few hours each day.
The wood was sourced locally, cut, routed for the glass inset, sanded, and finished. The hairpin legs were cut, bent, and welded to brackets mounted underneath the tabletop. You can purchase hairpin legs (online, at local woodworking shops, etc) instead, but we wanted to make everything from scratch. Finally, the glass sheet was purchased, cut, shattered, purchased a second time, cut successfully, and fit into place. That's it!
If you like this Instructable, please vote for it in the Hand Tools Only contest! :-)
Step 1: Cutting the Wood
The most important thing in this step is to make sure you know what you want your table to look like, and to take care when cutting the wood itself. We wanted the live edge to run at an angle in the table, and to preserve the interesting wood patterns at each end. This meant we had to cut the wood at an angle lengthwise down the piece.
Tool
- Circular saw
- DO NOT USE A TABLE SAW FOR THIS. As there is not a straight edge to guide the cut on a table saw, and the wood is large and heavy, you can easily get the saw blade stuck, and the table saw would then throw the wood straight back into your body...which wouldn't be awesome for you. Use a circular saw with a good rip cut blade instead.
- Rip cut blade
- Rip cut blades have fewer teeth (typically 24-40 tooth count), and a distinctive shape to the blade profile. Rip cut blades are designed to move quickly through wood with the grain, removing material and maintaining a relatively smooth profile. Look for a thin-kerf blade in particular. The thinner profile helps maintain a smoother cut, and because it isn't as wide, you aren't removing as much wood. This prevents the wood from overheating and burning as the blade cuts.
Photo credit: Rockler Saw Blades 101
This step is pretty easy. Lay the wood down on a set of 2"x4"s or some other elevated material so you can cut through without the saw blade hitting the ground. Be sure to support the wood well enough so that each half will still be stable even after the piece is cut in two.
Tip: Find a flat edge and clamp it to your wood so that you can run the circular saw against the edge and ensure that you get a straight line. The circular saw will do a reasonable job itself of cutting a straight line, but having a clamped straight edge to run the tool against will help.
Once you have cut the wood slab down its length, swap the two pieces so that the live edge is facing inward. Arrange them so that the freshly cut edges are parallel to one another.
Then, square off the short edges with the circular saw; again, using a straightedge and guide will help. Changing blades to a crosscut blade would be preferable, but you can get away with using the rip cut blade. Just be careful of tear-out.
Congratulations! You have the beginnings of a table!
Step 2: Ah...the Glass...
Now that you have the wood tabletop cut and square, it's time to cut your glass inset.
- Source a pane of glass. You'll be cutting the glass yourself, and in a slight curved pattern, so note the following:
- Annealed, not tempered. Tempered (i.e. safety) glass will shatter if you cut it conventionally, so make sure to buy normal annealed glass.
- 1/4" is a good thickness for this. Any thicker and cutting the glass yourself will be difficult/impossible. Any thinner and you'll end up with a weak pane of glass that's more likely to become damaged.
- Determine how far apart you want your table halves to be.
- Accordingly, determine how large your sheet of glass needs to be. You won't cut the two short edges of the glass (the less you cut the glass the less likely you are to shatter it, so limit your cuts to the two curved edges). Since you don't cut the two short edges (i.e. the edges that will align with the square ends of your table), you immediately know how LONG the glass needs to be. Next figure out how wide the glass needs to be. You want there to be enough overlap for the profile you're going to cut so that you have some room to work with. Since you'll be using the off-cut glass later as a template for your routing, it's important to make sure that there will be a reasonable amount left.
- Our sheet of glass was 42" long, 16" wide, 1/4" thick, and cost $47. You can get tinted glass (blue is popular for these tables) at an additional cost. Contact your local glass and mirror shop for this; hardware stores seldom carry glass long enough, so you'll have to go to a specialized place.
- Acquire a glass cutter. A good one, with oil. This works really well.
- Place your glass over the wood. See the first image in this section's photos. Make sure your wood is laid out as you want the final product to be. Now use a marker to trace the line of the curve you want to cut. Tip: Smooth and longer curves will cut better than sharp or angled lines, so try to trace out a profile that's as smooth as possible.
- Remove the wood, and lay your glass pane down on something soft and cushioned. We used towels.
- Take the glass cutter, oil it if applicable, apply pressure to the glass sheet with the cutter, and move the tip along the line you traced, starting at the edge/beginning. If the cutter makes a grating sound, it's working.
- Now turn the glass over, and use the ball end of your glass cutter to tap on one end of the line. You should see a fracture appear. Continue tapping in this manner (fewer hard taps work better than many light taps) and the glass will crack along your line. It may need some persuasion, but eventually the glass will crack.
- If you glass breaks unexpectedly, use the *now scrap* piece to practice your cutting techniques, get another sheet, and try again. You can see the results from our first and second attempts above. :-)
Step 3: Routing an Inset for the Glass
This is a step that benefits from practice and experience with a router. There are a few different approaches to this you can take, depending on your access to router tools and familiarity with routing techniques. I've outlined the approach I used below, where the glass offcut remnants were used as a template to define the boundaries to cut in the wood.
I used a template guide and cut approach. The glass offcut is laid over the top of the relevant piece of wood, with some spacer material between the wood and the glass; I used some 1/8" wood remnants for this. Clamp the glass to the wood slab. Gently. The glass edge will be the template that defines the profile you'll cut in the wood.
Next, get your router set up. I used a router template guide which allows a spinning bit to trace a profile above the work. The image below shows how this works. Credit to Popular Woodworking.
Then use the router to cut into the wood slab and rout out an appropriate negative space for the glass to eventually fit into. Tip: Rout a little deeper then the thickness of the glass as you'll remove some of the slab thickness when you sand it down to be finished.
Check the fit with your glass, and make adjustments as needed.
Step 4: Feet!
This step can be easy, or less easy; it all depends on your comfort with a welder and/or desire to make everything by hand. If you don't want to weld the legs yourself, there are plenty of pre-fabricated versions available online, some not much more expensive than it would cost to make them yourself! As I enjoy welding, we decided to make the table legs from scratch.
First, decide what style of leg you want. Two easy options are hairpin legs with cross-beams (what we chose to make) or bar steel legs. But there are many more options out there, so look around for inspiration.
Determine the height you want for the table first. This allows you to determine the length of your table legs. If they will be angled, as with hairpin legs, make sure you take into account the extra length required for the perpendicular height from floor to table, since the angle means that height is slightly shorter than the length of the legs.
We purchased four 36" lengths of 3/8" steel round from the local hardware store. I then bent the legs into the desired shape, and used an angle grinder to cut the ends of the legs to the right length and at an angle that would allow the legs to weld nicely to the flat steel plate used to mount the legs to the table.
Once the steel legs are bent and cut to the right length, they'll need to be welded to some steel plate that will be screwed into the underside of the wood tabletop. Drill holes for your screws before you do any welding. You can use a handheld drill for these holes if you clamp the metal plate down appropriately. Use a drill bit suitable for steel. I used a carbide center drill bit with LOTS of cutting fluid applied regularly.
I do not have pictures of the welding process, unfortunately. I used a MIG (Metal Inert Gas) welder to spot weld the legs to the plate, and then went back and laid a weld bead all the way around where the rod meets the metal plate. Use about 1/8" thick steel bar for the plate as it allows for a good weld and will support the table sufficiently.
If using hairpin legs, the tabletop needs to be supported with cross-beams. Small c-channel works really well for this as c-channel is super strong, looks good, and is easy to work with.
Finally, protect your metal from rust! Unless you like the rust look, the steel will need a coating to prevent it from rusting over time. I used a spray polyurethane coating available from any local hardware store and coated all the metal.
Step 5: Finishing!
Finishing wood always takes the longest, I find. But it means you're almost done!
We really liked the natural color of this walnut wood, so wanted to keep it as light as possible after sealing and finishing. That's typically quite difficult, especially with darker woods like walnut that really like to absorb finishes and get even darker. But, where there's a will there's a way! In this case, we used a flat, water-based finish from General Finishes that seals and finishes wood perfectly; because it's a water-based finish, it doesn't alter the wood color too much! As always, test your finish before you commit to it. We tried five different finishes before settling on this one.
- Take 100 grit sandpaper to the wood, followed by 150 grit. At this point you can apply you first coat of finish.
- But wait! This is a water-based finish, and walnut grain has a tendency to raise up when it becomes moist. So apply a fine mist of water to the wood surfaces you want to finish with a spray bottle. Wait 15 minutes and feel the wood. Chances are it won't feel smooth anymore. The wood grain became moist, expanded, and raised up out of the surface. If you sand the surface again now, you'll sand off the grain that raised up, and there shouldn't be any more grain to raise up when the wood gets wet! To be safe, wait until the wood dries, and repeat this process. There shouldn't be much grain which rises up, and the surface should be smooth after this step.
- Use a higher grit sandpaper; 220 is good to get the wood nice and smooth before applying the finish.
- Now you can apply the finish. Use a foam brush to apply a thin coat of the the finish in the direction of the grain. Allow the finish to dry (it will probably take a few hours).
- Use either the same 220 grit sandpaper or some light scrubbing pads (white pads in image above) to rub lightly over the finish. This scores the surface so that the next coat of the finish has something to bond to. You aren't sanding the finish off; it's really just to rough it up.
- Apply a second coat of finish.
- Sand the surface lightly one more time with a high grit sandpaper (300+) and apply a third coat of finish if desired. It's all about aesthetics at this point, so decide what look and feel you want for your table surface.
- Admire your pretty tabletop!
Before
After
Step 6: Assemble and Admire
Home stretch. No pictures of the actual assembly process (I was too excited), but here's how it went.
- On a large surface, lay down the wood with one end sticking out over an edge. Place the glass inset in the table so that it all fits together nicely.
- Gently remove the glass and clamp down the wood.
- Clamp the c-channel you cut earlier to the table, and drill pilot holes. Install screws nice and tight. That's one half of the top support done!
- Switch the table around and do the same to the other end.
- Now you should have a sturdy tabletop that's all connected. Flip the entire top upside down.
- Lay your legs out where you want them, drill pilot holes, and install screws (see image below).
Flip the table around, and install your glass. Don't forget to clean the glass first so it looks all spiffy!
Now apply some decorative touches, take pictures, and send them to everyone you know. Congratulations! You built a live edge river coffee table!
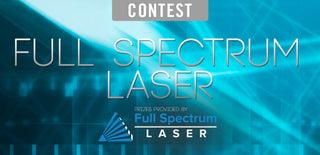
Participated in the
Full Spectrum Laser Contest 2016
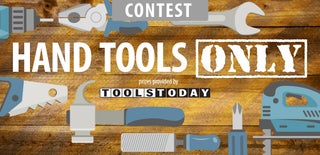
Participated in the
Hand Tools Only Contest 2016