Introduction: Machined Stainless Steel Bottle Opener
This instructable details how to machine a bottle opener out of stainless steel with a decorative brass insert. It makes a great gift or everyday tool.
Some notes first:
- The design is based off "The Hidebound" by Machine Era Co., available here.
- Stainless steel is difficult to machine. If you are new to machining, use aluminum or a free machining steel.
- I am a college student, and have been machining for about a year. I am mostly self taught. Any corrections or suggestions to this instructable are welcome!
- Sorry for poor photo/video quality - the project was documented with a flip phone.
- I will assume the reader has some basic machining knowledge. If you are new to machining, there are plenty of great instructables and YouTube videos to get you started. Here are some:
Instructable: Installing endmills
Instructable: Installing lathe tools
YouTube: Squaring stock on a mill
YouTube Playlist: Machining Tips by Tubalcain aka Mr. Pete - a great resource for machinists, new and experienced.
Still interested? Read on!
Step 1: Safety
Knee mills and engine lathes are dangerous, potentially lethal, machines. The best safety protection is your brain. Do not work when tired or distracted. If you are not 100% comfortable with the operation of a machine, ask for help. Some other general safety tips:
- Always wear eye protection. You only have one set of eyes.
- Think through every operation before turning on the machine.
- Do not leave the lathe chuck key in the lathe. It can become a lethal projectile. It's a good habit to never take your hand off of it.
- I also like to protect my lungs from cutting oil smoke. If you're work space doesn't have good ventilation, I recommend getting a decent respirator with general use cartridges - it's far cheaper than medical bills down the road.
---
Shake hands with danger, Meet a guy who oughta know,
I used to laugh at safety, Now they call me Three-Finger Joe.
Shake hands with danger, Find it anywhere you choose,
Be careless for a moment, Spend a lifetime with the blues.
Step 2: Material and Operations
The stainless steel (SS) and brass are from a scrap bin. I don't know what grade either of them is. Flat SS stock would be less wasteful, but this is all I could find. I also wanted to get some experience milling SS.
Stainless steel is difficult to machine because it work hardens. Some general advice:
- Surface Feet per Minute (SFM) - about 80 or below. This means 400 RPM for a 3/4" end mill (though I used 240 RPM). Reference SFM Calculator for a starting point.
- Feed rate must be sufficient to "get under" work hardened layer. Use power feed and climb milling whenever possible.
- Milling stainless produces a lot of heat. Use cutting oil or coolant, and be careful handling the (hot) part after milling.
Step 3: SS Stock - Round to Flat
The round stock was set in the vise, overhanging about 5 inches. This is not a very rigid setup, but since stainless is fairly strong, and dimensional tolerances don't really matter, it works.
Both sides were cut in a single pass, using a 3/4" roughing end mill (see next step for more details). RPM was set at 240, and power feed was slowly turned up until the machine complained, then down a little. Cutting oil was applied continuously with a brush. Both sides were climb milled.
The front face was easy enough (as the table fed towards the tool), but the back face required a plunge in the y-axis, before engaging the x-axis power feed, away from the tool. I recommend locking the y-axis during the cut. Try to be consistent with speed for any hand feeding.
The surfaces were then cleaned up with a regular 3/4" 6 flute end mill.
Step 4: A Note About Endmills
Roughing end mills have a wavy serrated cutting edge that allows for greater material removal rates. On a four flute cutter, the serrations on each edge are shifted by half a serration length from each other (or if you like to think in waves, phases 0, λ/2, λ, 3λ/2). For more information, see the patent. This design makes for smaller chips and lower cutting forces, but produces poor surface finish.
A regular 6 flute end mill is good for low depth of cut milling, as it make more cuts per revolution without increasing surface speed. The trade off is that small flutes limit the material removal rate. It produces needle-like swarf.
Step 5: Remove Flat Stock From Round Bar
The flat portion was removed from the round bar using an Ellis band saw. Wax lubricant and low speed keep the blade from overheating.
Step 6: Square Up Stock
Two of the bar's surfaces were still rounded. It would be nice to keep them, but the crown wasn't centered at all, so I went ahead and faced off the sides with a 3/4" end mill. The edges were then knocked back with a file.
Step 7: Making a Hole for the Brass Insert
On drilling stainless steel: Make sure RPM is set fairly low, use cutting oil. Locking both axes is recommended. The most important thing is to feed hard, either by hand or power. It's really important to be either producing chips or not engaged at all. Any in-between pressure will lead to work hardening and problems. Dull drill bits don't help. It's also a good idea to have a piece of scrap underneath the work, so when you break through, you don't nick the vice by accident.
Any size brass insert will work, but I feel around half inch allows for the use of a strong drill/reamer, and is fairly forgiving in terms of interference fit dimensions and arbor press use.
Step 8: Turning the Brass Insert
The hole in the SS body was reamed to 32/64", or about 0.4844". The brass rod was turned down to 0.4860", about a thou and a half over. There's plenty of calculators and tables regarding press fits, but I found for things under an inch, 1-2 thousandths seems to work fine. The rod was chamfered on one end, then parted off. The part was flipped over, and the parting nub was faced off.
Step 9: Press Fitting the Brass Insert
This operation is fairly straightforward. Place the insert, chamfered side down, on top of the SS hole, and apply the press. Do not press it flush, as some of the rod could be pushed below the surface. I left about 1/8" on either side to be milled and sanded flush later.
Step 10: Mill/Sand Insert Flush
The excess brass was milled off, then the sides were sanded flat so the part could be clamped well in the vise for the bottle opener milling.
Step 11: Milling Bottle Opener Slot
Various end mills and angles were tried on a scrap piece of aluminum. A successful test piece can be used to align the actual SS/brass bar in the vice. Make sure enough of the bar is being gripped in the vice to prevent slipping.
The slot was milled in multiple passes, advancing the knee up 0.1" each time. Locking the x-axis is recommended. The end mill was around 5/16", and run at 900 RPM. A finish climb pass a few thou to either side of the slot helps clean up any marks. Before removing the part from the vice, mill a flat on the acute edge to keep it from cutting people and increase bottle opening durability.
Step 12: Finishing
The bottle opening slot was still a little rough so it was clamped in a vice and smoothed with a file. The remaining surfaces were sanded using a belt sander - around 100 grit, I think. The part heats up while sanding, but a few seconds under cold water makes it easy to handle again. The edges were knocked back with a fine file. I also stamped the recipient's name on the top side using metal stamps and a hammer.
And that's it! All in all, took me about one and a half hours. The final part was about 3/8" thick, 3.5" long, and 1" tall.
It's a too weighty for a keychain, but makes a great gift or conversation piece.
Thank you for reading! If you have any questions or suggestions, please feel free to leave a comment.
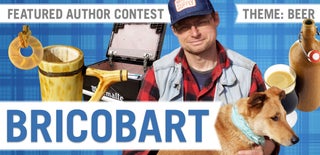
Participated in the
Featured Author Contest: bricobart
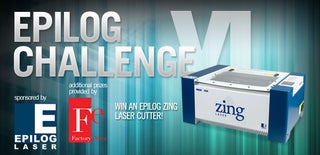
Participated in the
Epilog Challenge VI
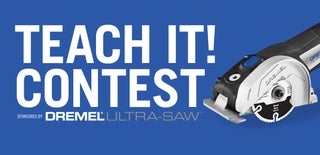
Participated in the
Teach It! Contest Sponsored by Dremel