Introduction: Make Your Vise Portable
In this instructable I'll be going over one relatively quick, simple, and inexpensive way to make a vise more useful for those who may not have a dedicated shop space - or for those who would just like to have the option to move their vise around. While I wouldn't recommend this for a vise that's going to see hard use (heavy hammering and bending, etc), it works well for the light to medium duty that my vise tends to see 99.9% of the time.
I've had a Craftsman 5-1/2" metal vise for maybe 20 years, and for most of that time it has lived in a box on a shelf ... staring at me accusingly ... mostly because I never could seem to find the "perfect" place to bolt it down. After restoring and mounting another vise to a base, I came to realize how useful it is to have a vise mounted to a portable base. I also realized that while the Gyro-Vise is awesome, it's a light-weight vise and it's jaws aren't suitable for most metal-working that I do - so I figured, "Hey, what's good for the Gyro should be good for the Craftsman..." and decided to mount it to a base and get it back in the game.
Step 1: Materials and Supplies
1) First you need a vise (Thank You, Captain Obvious).
2) Next you will need a suitable base. I've found that a roughly 12"x12" square gives enough room to provide a variety of clamping configurations as well as allowing good force distribution to the supporting table, counter, or bench without being so big that it's unwieldy to store or move. I made my base out of Baltic Birch Plywood, but you could probably get away with regular plywood or *maybe* even MDF (although it might be kind of brittle). I wouldn't go any thinner than 3/4" for the base material. Baltic Birch Ply would be my first choice ... if for no other reason than when I was a kid in school, we could not destroy the desks that were made from it no matter how hard we tried ;) BBPlywood used to be a lot harder to come by, but lately I've seen it at some of the big box stores - so it's available. (Another possibility: drop by a shop that makes counter tops - they may have a sink cut-out that they would sell or just give to you.)
3) Some kind of "skin" or veneer material would also be nice - it keeps the surface clean and reduces damage from the holding clamps. Realize that unprotected "standard" plywood would probably get dented up pretty quickly from regular C-Clamps. I used some scrap Wilsonart (like "Formica") veneer that I had on hand.
4) Bolts, washers, and Tee-Nuts. I chose Grade-5 bolts (chronic over-engineering), but Grade-3 would work fine as well. The Tee-Nuts I used were the kind with "prongs" - they're easy to install and mount securely. If your vise has countersunk holes, you may want to choose the appropriate Allen-head machine screw for a tidier installation (see Step 3) I originally considered putting some handles on the base ... but then sanity prevailed and I scrapped that idea ... they'd just get in the way.
5) Some contact adhesive for the Formica / Wilsonart, and optionally some thread-locker for the bolts (LocTite #243 in this case).
6) A table saw and drill press are handy, but not mandatory. You will also need drill bits, a Forstner bit sized for the base of the Tee-Nuts as well as a drill bit sized for the shank of the Tee-Nuts ... and a hammer, marking tool of some kind, ruler, etc.
Step 2: Cut, Drill, and Assemble
- First thing you'll want to do is cut your base material to size - a little oversized actually. Add about 1/8" to your base dimensions.
- Next, cut your "surface" material to the same size as the base - it doesn't have to be exact because once it's bonded to the base, you'll clean up the edges on the table saw. You want to cut it a *little* oversized as it will make bonding the surface to the base a heck of a lot less stressful.
- Using contact adhesive, bond the surface material to the base. You want to have two edges perfectly flush - and overhang on the other two sides. These flush edges will be your "working edges" when you clean up the base on the table saw.
- Once the adhesive has set, go ahead and set your saw fence to the final dimension of the base. Place your working edge against the fence, and trim the base to final size. Do the same with the other working edge and trim the surface material flush. You may want to break the edges of the surface material with a file or hand-plane as they will be sharp
- Center your vise on the base. Keep in mind that you want the back jaw of the vise to clear the outer edge of the vise - so that you can have long work pieces hang over the edge of the bench. When you have the vise positioned, mark your mounting holes.
- Remove the vise from the base and drill pilot holes in the center of what will be your larger mounting holes. You do NOT want to drill the Tee-Nut shank holes yet - these pilot holes will help guide the Forstner bit.
- Flip the base over and, using a Forstner bit that is slightly larger than the Tee-Nut base, countersink the base to accomodate the Tee-Nut bases. By sinking these slightly below the surface of the base, you can make it much less likely that you will damage whatever you clamp the base to.
- After countersinking, go ahead and drill holes that will allow the Tee-Nut shanks to slide in. Drill these holes so that there is a snug fit - not too loose. Once these holes are drilled, you can install the Tee-Nuts flush with the back of the base using a hammer and block. Be sure to protect the surface material by placing it against something that won't scratch it - like scrap wood when installing the Tee-Nuts.
- You may want to round over the corners of the base - I used a rasp for most of the material removal, follwed by some files to smooth things out.
- Go ahead and test-fit the vise to the base. If everything looks good, put some thread-locker on the threads of the bolts and torque them down. You might also want to put some finish on the base before final assembly - I sanded the edges and back smooth and applied two coats of polyurethane. The urethane will keep the base from absorbing water, oil, and other contaminants that you really don't want soaking into the wood.
And there you have it! A handy vise that you can take along with you just about anywhere you'd need it. I really like being able to take the vise to the work as opposed to not using the vise because I might not be able (or want to) take the work to the vise :)
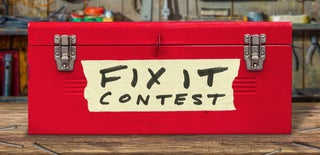
Participated in the
Fix It Contest