Introduction: Making a Kriegsmesser
I wanted to make a kriegsmesser for a while now and when I saw the work of a renaissance master called Hans Sumersperger I knew how it would look. I based my design mainly on the picture found here:
http://sword-site.com/thread/476/straight-single-g...
If you would like to make this messer or any other sword and don't have experience with forging I suggest you cut out the blade shape out of some sheet steel. Overall this build wasn't any different from any other sword or long knife I made previously.
And here are some specifications:
-Overall lenght: 123cm,
-Blade lenght: 100cm,
-Hilt lenght: 23cm,
-Crossguard lenght: 23cm,
-Point of balance: 20cm,
-Weight: 1400g.
Step 1: Making the Blade.
For the blade I decided I would use a coil spring about 15mm thick. I started with straightening the whole thing which came out about 3 m long. Then I cut it in half and started flatening it from there. The shaping of the blade took a long time and lots of charcoal but in the end it was worth it.
After I was done forging the blade the whole thing was about 140 cm long which was way to long. I decided on 100 cm for the blade and about 20 cm for the handle. Then I decided I would also like a fuller so I made a quick fullering tool and started forging. The fuller runs about 3/4 of the blade lenght and is 15mm wide. I wanted some more width so I started by forging the bevel which took a long time to get a consistent edge.
After all the forging I started to grind the blade and started on the fuller. I ground the fuller on a 7 cm radious belt grinder wheel. Grinding the fuller was quick and fun to do and after I was done I started to grind the bevel with an angle grinder. I used an angle grinder to rough grind the bevel and then finished it on the belt grinder with a 24 and 40 grit belt. I left the blade a litle thick so I wouldn't have problems heat treating it.
After the grinding I started the heat treat, first I heated up the whole blade and left it to cool slowly and get all the stress out the steel. After annealing it I heat it up again and then quenched it in hot oil to harden the blade. The blade did warp some but I was able to get it back straight by applying pressure to the curved areas. After the blade cooled down I ground the surface to expose the steel so I could temper it on the still hot coals. The blade was tempered to a dark straw color (about 270°C) and then ground to the final thickness on the belt grinder. After I was satisfied with the blade I started to polish and sharpen it with a 300 grit belt on the grinder.
Step 2: Making the Crossguard.
After looking at some originals I decided to cut the crossguard out of a 2 cm thick mild steel rather then forging it.
The crossguard was a simple design and was not hard to make, basically I cut out the final shape of the guard and then ground the arms round and made a slight fuller to serve as a thumb rest.
After the polishing came the hard part - making a slot for the tang to fit in. I drew a line to represent the middle of the guard and then center punched holes for the dilling process. I drilled the slot with a 6mm drill bit and the slowly filed away until the tang came all the way trough. This was by far the longest proces of the whole build, it took me about two days of constant filing and fitting to get in on correctly, but in the end I got a good fit and all the time spent was worth it.
Step 3: Making the Pommel.
The pommel was the easiest of all the parts of the build. I traced the shape I wanted on to 2 cm thick steel plate and then cut it out with an angle grinder. After the cutting I ground in a fuller that matched the one made on the guard and beveled some of the edges so it felt good in the hand. After I was satisfied with the shape I polished it with a 300 grit belt and then finished it on a buffing wheel.
After polishing I drilled a 6 mm hole through the whole pommel so I could peen it after gluing.
Step 4: Making the Handle and Some Conclusions.
For the handle I chose a nice piece of light colored wallnut. First I cut a smaller block and then sawed in half, I then marked where the tang comes trough and cut in a slot. After everything fit nice and tight I marked where I wanted the holes for the brass pins.
With the holes drilled in the wood I maked where the holes come in the tang and drilled those too. Then I assembled everything together and decided I want some thin brass spacers where the handle touches the guard and pommel. Cuting the brass sheet was done with a hack saw and the hole was made with a chisel.
With the brass cut, everything was ready for gluing. But first I cleaned all the surfaces with acetone to ensure a good bond.I mixed up some two part epoxy and applied it to the tang, handle, brass, pins and the pommel and then clamped everything together. After a day when the epoxy fully hardened I peened the tang back on the pommel.
And with that the messer is completed, all it needs now is a good sharpening and testing. It was a fun and exciting build full of challenges and new acquired knowledge. I hope this instructable inspires you to try making your own and bring you many days of fun builds.
Good luck on the path.
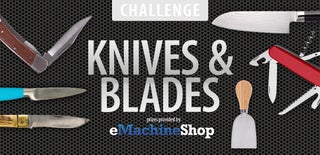
Runner Up in the
Knives and Blades Challenge
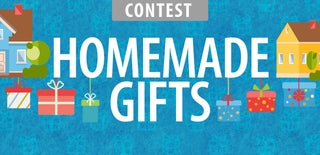
Participated in the
Homemade Gifts Contest 2016