Introduction: Match Box Picture Frames
While living in India, became mildly obsessed with matchboxes. There are countless different designs for the box covers from hundreds of tiny companies that make matches in India. From what my friends tell me, the majority of these companies are based in the same town called Sivakasi in the southern state of Tamil Nadu.
I got tons of weird looks for picking up trash, but I would have gotten weird looks anyway, so no big deal. They are like little pieces of art, and finding a new one was like finding a little treasure every time.
In any case, I have over 400 of them now. According to the serious collectors, my 400 is far from an impressive sum, but it's enough to fill a wall in my living room. Taken one at a time, they are teeny tiny paintings, all at once, this is the largest work I have yet completed.
Supplies
Match boxes, Scrap wood, acrylic, matte board, glue, magnets, dowels, plywood.
Step 1: Collecting
The first image above of the six boxes is what sparked my obsession. I was working for a company that makes cooking stoves, and in the office we always needed to have matches to light the stoves. These six boxes were all lying around the office one day. I particularly love the one named Puppy. That box is and will always be my favorite one. I think the design is just great, the puppy looks so regal and happy, and it is a PUPPY. Anyway, many of the others have stories too, but I won't bore you with them now.
Ok, just one more mini story. My good friend Santhosh went on a little vacation while we were living together, and when he came back I found those two boxes on the kitchen table. Each one had a bug inside. Clearly, Santhosh knows the kind of garbage that I like (the sign of a true friend).
Step 2: Copy Cats
One of my favorite parts about the match boxes is the design styles that get copied, ripped off, reused and changed. Each of the boxes above (or at least most of them) are made by a different company. I find this just fascinating. If you have knowledge of this industry PLEASE reach out. I would absolutely love talking to someone who knows more about the Indian matchbox making industry.
Step 3: Ok, on to the Frames
As with any art, it looks best when framed.
For the first few frames, I used discarded molding from the renovation of the Maker Space where I was working. (See my Instructable about the Maker Auto if you are curious about that).
The rest were made from scraps in the wood shop where I work now.
As with anything to be made in large batches, the first step should always be to make jigs and/or fixtures. Jigs save you tons of time, and ensure that all the pieces come out looking similar. In this case, I designed a jig in Fusion360 for the table saw that helped me cut all 1600 frame pieces to exactly the same length and angle. The pieces of the jig were cut on the laser cutter and pinned together with bolts to ensure precise alignment.
Step 4: Routing
My goal was to have a wide variety of frame styles for this project, so I started by scavenging for old molding and then moved on to making other profiles with the router. The one thing all of the molding needed to have in common was a channel to fit the glass and matte board in. This was also done on the router (could have done it just as easily on the table saw also). For the first few frames, I used a home made router table at the Maker's Asylum in Mumbia. The rest were done on a real router table in my workshop. The major difference is fence vs no fence. I highly recommend using a fence, even if you have a bearing on your router bit.
Step 5: Using the Jig
I ended up making this jig twice. I first made one for use on a home-made table saw in Mumbai, and then later I rebuilt it and used it on the SawStop back in Cambridge. Using a commercial table saw rather than a circular saw screwed under a table has a few major benefits, but the one I found most important was having tracks that run parallel with the blade. This increased accuracy significantly since I wasn't relying on a fence.
One side of the jig cuts a 45 degree angle on a piece of molding, and the other cuts a perpendicular 45 at the correct length on the other side.
Step 6: Glue Up the Frames
Once again, I tried a few different strategies for gluing up the frames. The one that I found to work best was to lay the four pieces in a row on a piece of masking tape, then add glue, fold the frame up, and clamp it with rubber bands. This ended up being by far the fastest and most accurate way to glue up. I recommend getting some snacks and music going for this step, it gets pretty tedious.
Step 7: Painting and Finishing
Again, for added variety I decided to paint and stain many of the frames. Some were spray painted, some were brush painted, some were finished with urethane. I pretty much used what ever finishes were available at the time.
Step 8: Matte Boards
Traditionally, a professional framer would cut the matte board with a knife or matte cutter, but in the interest of time, I used the laser cutter. The result is that there is a burned edge and no bevel facing the match box, but these were sacrifices I was willing to make in order to finish this project within the decade. I also used the laser to cut the acrylic that I used instead of glass for the frames.
Step 9: Assembly
Once all the frames were made, matte boards, and glass was cut, it was time to assemble. A framing point tool saved countless hours in this step.
Step 10: Storage
All told, I worked on this project for upwards of four years, and in the intervening time, I found that the match box frames fit perfectly in old cassette tape racks. As the collection grew, so too did the collection of old cassette tape storage.
Step 11: Drilling and Magnets
I quickly realized that hanging these frames with normal frame hardware would be far too tedious. Instead I decided to add a small magnet to the back of each one and hang them on a grid of screws in plywood. Here's the simple jig I made to align the frames for drilling. In the end, the single 1/8 inch diameter magnet was not strong enough to hold the frames. I ended up drilling three holes in each frame. One was for the magnet, and two more were for 1/8 inch dowels sticking out from the wall in a grid.
Step 12: Mounting
Thankfully I have access to a 4X8 foot CNC router at work. I used this to drill 1200 holes in two sheets of plywood. Sets of 3 holes are spaced in an even grid on the whole sheets. Each set of three holes has one for a steel screw that the magnet will attach to, and two for thin dowels to help hold up the frames. For installation I pressed 1/8 inch dowels in each hole and cut them flush with a simple jig and a Japanese flush cut saw so they would stick out a consistent distance from the wall. Flat head screws were counter-sunk to be flush with the wall. The install was again tedious, but in the end, I couldn't be happier.
Step 13: Party!
I have dreamed of hanging all these little works of art in a gallery somewhere, but for now they are in my house. Lucky for me, I share a home with 5 other lovely people, so we had a small gallery opening just for us. Complete with wine, cheese and a strict dress code.
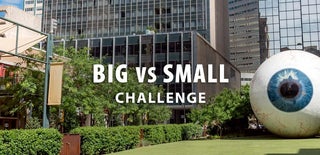
Participated in the
Big vs Small Challenge