Introduction: Neighbor-Friendly Patio Light
I was motivated to play with lamp shades due to recent popularity in clear-glass fixtures & unfrosted (clear) "vintage" LED bulbs (harsh to look at). Also, the growing popularity of integrated LEDs in cool color temperature (4000k white, 5000k daylight; unfriendly to sleep/circadian rhythm; can't replace the bulb). Also the trend toward "security lights" that are more deterrent than friendly.
While viewing neighboring patio lights, I began to consider what I want in a fixture:
- Opal/milk diffusion glass diffusion (not a clear, direct view of the light source)
- Most of the light directed backwards & down (reflecting off the house & ground for a larger and less harsh source of light compared to light shining directly forward.). The ultimate ideal: a full cutoff hood (dark-sky compliant).
- Replaceable ordinary bulbs (not integrated LEDs). Repairable (not disposable), but more importantly: I can choose the color temperature & brightness I want.
- Dusk-to-dawn operation.
- Motion-sensing. Preferably not just "on/off" motion activation, but low/ambient light when no motion is sensed.
I decided to make my own using ordinary parts. The fixture I chose seemed like the best balance (HZ-5610, photo #1). It uses ordinary replaceable bulbs, has a milk-glass globe, and is dusk-to-dawn & motion sensing. The only thing lacking: motion-sensing is "on/off" (with more modification I was able to have low/ambient light when no motion is detected. See my other Instructable, Dual-Brightness Motion-Sensing Patio Light.).
This instructable improves the first two goals (less forward-emitted, glaring light). I show how to make a:
Paper Shade (steps 1-6)
A quick & easy way to reduce the amount of forward light (easier to look at). I show 4-layers of paper with feathered sides (more light coming out the side. Photos 2-5). But, you can modify this any way you wish. I ended up using 6 layers with no feathered sides (more of a full-cutoff effect. Photos 6-9).
Sheet Metal Shade (steps 7-9)
A sheet-metal shade to entirely replace the glass globe (photos 10-12). This is dark-sky compliant, but requires more tools & work (drilling, painting).
Supplies
Fixture: I used a Heath-Zenith HZ-5610-BZ which is dusk-to-dawn motion-sensing and accepts ordinary lightbulbs (giving you choice of color temperature). You could adapt these shade ideas to any fixture. (If you use a clear-glass fixture, consider using Rustoleum "Frosted Glass" spray paint to reduce the harshness of the light.).
Lightbulb: For the 4-layer feathered paper shade, I used a small A15-style[1] Philips "Amber light" (2000k) "vintage" (25w-equivalent, 3.3w actual, 200 lumen; Part: 3.3A15/VIN/820/E26/CL/GL/DIM; UPC: 0 46677 55655 6). This is a clear-glass bulb. I sprayed it with 2-3 coats of Rustoleum "Frosted Glass" to reduce glare. (Even though the fixture is milkglass, I felt that the frosted bulb reduced glare even more.).
When I replaced that shade with 6-layers of paper (no feathered sides; more "full cutoff") I switched to a large ST19-style Philips "Amber light" (2000k) "vintage" (40w-equivalent, 5w actual, 350 lumen, dimmable. Part: 5ST19/VIN/820/E26/CL/GL/DIM; order code from Philips spec sheet: #556803; UPC on box: 0 46677 55680 8; Home Depot SKU: #1004856101). This is a clear-glass bulb. I sprayed it with Rustoleum "Frosted Glass" too.
I still use this ST19 bulb with the full-cutoff sheet-metal shade. I needed a brighter bulb when I blocked more light coming out the front because reflecting light (the wall of the house, the ground below) loses light, so I had to use a brighter bulb for the same overall illumination of the yard. The larger bulb shape makes it slightly less glaring too.
Paper Shade: Ordinary printer paper (20lb, 92 brightness). Using paper as a shade would be a concern with an incandescent bulb due to the heat and potential for fire. But, with a low-watt LED bulb there's no problem.
Sheet-Metal Shade: 8x12" galvanized steel, 0.015" thick (28ga), called "flashing" in the roofing department.
- Paint: Zinsser 123 Bullseye primer (necessary to paint galvanized steel)
- Ace Rust Stop "Dark Bronze Satin" enamel #225B160
- Two #8 x 3/8" long sheet metal screws
- Tools: drill, "aviation" snips to cut the sheet metal, a file to smooth the cut edges
=Footnotes
1. The Edison Lightbulb Shape codes (A15, A21, ST19) have an easy-to-understand meaning. The alpha part refers to the style. "A" lightbulbs are standard-shape household lightbulbs. ST refers to "straight tubular" (you can google for "lightbulb shape & size charts" to see them all). The number refers to the bulb's size in 1/8" increments. E.g., "19" refers to 2-3/8" diameter.
Step 1: Paper - Mark & Draw
This example uses four sheets of ordinary printer paper (20lb, 92 brightness):
- Cut the sheets 10" x 5-1/4"
- Mark the following increments (for 1" layered steps) on all four sheets:
- Along the top edge: 0", 1", 2" & 3"
- Along the bottom edge: 1-1/4", 2-1/4", 3-1/4" & 4-1/4"
- Use a ruler to connect the top & bottom marks (on each page. Photo 1)
Hint: As shown in the Introduction, you can use 6 sheets all the same width (10") for a full-cutoff hood effect.
Step 2: Paper - Draw Radius
On just one sheet of paper (not all four):
- Draw a 19" radius which touches the top edge of the paper. This radius should exit the sides of the 10"-wide paper about 11/16" below the top edge.
- Mark 1/2" above the bottom edge (in the center of the paper), and draw a 14" radius which touches that mark. This radius should exit the bottom edge of the paper at the furthest taper line (which will be the bottom corner of the widest layer).
Hint: To draw a radius, tie a loop in the end of string. Put the pencil tip inside that loop. Hold the string down with your other hand 19" (or 14") back from the pencil tip, and draw an arc.
Step 3: Paper - Clamp & Cut Radius
- Clamp all four sheets together (I use Acco paper/binder clips).
- Cut each radius with scissors (move the clamps as necessary).
Step 4: Paper - Cut the Taper Lines
Cut the taper lines of each sheet. If you're making feathered sides, then you drew the lines on each sheet. Those lines will which remain on the wider sheets will be used to align the narrower sheets when you stack them. (If you're making them all the same width -- the full-cutoff hood effect -- then you can cut all the sheets at once.).
Step 5: Paper - Cut Fringe Along Top & Bottom Edges
The Heath-Zenith HZ-5610 fixture has come with two slightly different globes (photo 1). One (which I believe was in use many years ago, but still shown on the product literature/packaging) has sharper corners around the top & bottom. If you have this globe, you don't need to do this step. The shade will fit nicely within that globe.
If you have the globe with the more-rounded top and bottom (I believe comes with new fixtures today), you need to create a "fringe" along the top & bottom edges which will better conform to that curved surface.
- On all four sheets: make a few marks along the bottom & top radiused edges, about 3/8" from the edge of the radius. These marks will serve as a visual guide for how deep to cut (how long the fringe should be).
- Make 3/8" deep cuts about 1/8" to 3/8" apart.
- The depth of the cut isn't very important. Try to make it 3/8" deep. But, a little shorter or longer won't hurt, especially if it varies from one cut to the other (one layer to the other). It shouldn't be any shorter than 1/4", nor longer than 1/2". (I aimed for 3/8" to 1/2".).
- The width of the fringe isn't very important either. It's better to have randomness so the fringe from each layer overlaps. Aim for 1/4" wide, but make some narrower, some wider. I wouldn't go any narrower than 1/8", nor wider than 3/8".
Note: You can cut the fringe with the Acco clips holding the sheets together. But, you need to cut each sheet separately for randomness/overlap of the fringe. They will jam up against each other if they cuts are all the same (especially if you're not feathering the sides, and all the sheets are the same width (more fringe to jam up against each other).
Step 6: Paper - Stack & Tape
1. Stack the sheets. If you did feathered sides: the wider sheets will have drawn lines for centering the narrower sheets. Affix a small (1") piece of scotch tape on each side of a sheet to hold it to the sheet beneath. Do this near the vertical center. (It's important not to tape the entire length from top to bottom. The sheets need to "give" a little as they're rolled into the globe.).
2. If you cut fringe in the previous step (because you have the more rounded globe), you should gently roll/bend the fringe to help it conform to the curve inside the globe.
3. Roll this into a 2" tube (with the smaller sheets facing inward) and insert into the globe. You may have to get your fingers in there and help press the fringe into place.
Having the smaller (stacked) sheets face inward will reduce the sharpness of those layers' edges (as seen from outside, through the globe).
Step 7: Sheet Metal - Layout, Cut & Curve
1. On a sheet of metal (I used galvanized "flashing" from the roofing department. It's cheap.), draw the shade as shown in photo #1. (See the paper-shade instructions for how to draw a radius. You can also practice this shade on construction paper before doing sheet-metal.).
The two tabs on the top won't be visible. You can draw those roughly by hand. I give measurements as a target.
2. After drawing, cut the shade using "aviation" snips. (There are "yellow" snips for straight lines, "red" for left-hand curves, "green" for right hand. These curves are so mild that the "yellow" snips will work.).
Warning: The cut steel edges can be very sharp. Wear gloves to protect against cutting your skin.
Use a steel file to smooth/straighten the cut edges, remove burrs (sharp edges). Sometimes these snips can leave dimples in the cut edges. You can lightly tap those flat with a hammer (against a clean, smooth surface). You want a "finished" edge that the snips don't do by themselves. (This isn't like cutting paper with scissors. You need to put some effort into it after it's cut.).
3. After finishing the cuts, use a can as a form to roll the sheet metal into a curve. You want it to be ready to slip into the fixture after painting. I used a large-diameter can as shown (photo 3), and also a regular diameter can.
Be aware that the metal will tend to crease where the tabs are (that additional length of metal resists curving more than either side of the tab). It's soft metal and you can "fix" mistakes by pushing the metal back into place with your fingers against an opposing surface. (The "flashing" metal I used is cheap. I wasted 1-2 sheets practicing this shaping technique.).
Step 8: Sheet Metal: Paint, Drill Tab Mounts
1. After curving, you can fold the tabs in, drill the 1/4" diam hole (1/2" down from the top center), and the 5/32" tab holes anywhere in the tab (it's not a critical measurement. It won't be seen.).
If you drilled this hole before curving the metal, the metal would tend to crease at the hole (being weaker than the surrounding metal).
2. Paint the fixture. You'll need to clean the galvanized steel with soap & water, then wipe with methylated spirits. Then prime with two coats of Zinsser 1-2-3 Bullseye. (If you use galvanized steel and don't do use this primer, it will peel later.). Then paint the inside with two coats of gloss white enamel, and the outside with one coat Dark Bronze enamel (you'll paint the 2nd coat after the shade is installed).
3. Fit the shade into the fixture & mark the holes in the tabs onto the plastic fixture. Drill 3/32" holes into the fixture's plastic. Use #8 x 3/8" sheet-metal screws to secure the shade to the fixture.
The hole in the plastic is slightly too small for these screws (and the next drillbit size is too large). If they're difficult to thread into the plastic hole, back it out 1/4 turn, then tighten 1/2 turn. Don't force it. The plastic could crack. Just repeatedly go 1/2 turn forward, 1/4 turn back. It will thread all the way in this way without much effort.
Step 9: Check Angle, Install & Paint Last Coat
The way we radiused the top edge should cause the shade to tip forward as shown in photo #1. You can install washers beneath the tabs to make it tip out further.
After the shade is installed, tape as shown in photo #2, and give the 2nd coat of dark bronze enamel to the outer side. (The inner side should already have 2 coats of gloss white enamel).
I do this final dark-bronze coat after installation because installing can scrape/mar the paint.
Note: Don't rush the painting. The Zinsser primer needs 6-8 hours between coats. The enamel needs 24 hours.
The edge of the shade will have an irregular bronze & white appearance. After this final (installed) coat dries, you can carefully rub the side of a Sharpie pen around the edge to create a uniform black edge.
Step 10: More Ideas...
"Dual-Brightness" (ambient and security light)
My ideal fixture would have both motion-sensed full brightness and dusk-to-dawn ambient light. I figured out how to do that with any fixture! (Photo 1). See my other Instructable: Dual-Brightness Motion-Sensing Patio Light.
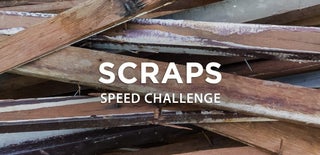
Participated in the
Scraps Speed Challenge