Introduction: (Not So) Portable Bluetooth Speaker
I took on this project inspired by my colleague who had a spare unused Volvo V70 speakers laying around. He gave them to me with a condition that I would build an enclosure for them. After doing a quick search on eBay I found that you can buy a decent amplifier for relatively low price so I accepted the challenge which would give me more experience in many areas like: woodworking, speaker, electronics and maybe even in battery management.
At first this task seemed to be quite easy but as soon as it began the expenses and the time needed to complete the project escalated exponentially. With a help of my friend we managed to complete this project in 5 weeks (the first part) which totaled 100 of work hours. We worked about three times per week after work hours for about 4 hours. Since I needed to buy new tools in addition to material needed for the build, my overall expenses were over €100 (it was too painful to track expenses in the end so I stopped counting).
Step 1: First Things First
The vision:
Speaker dimensions are 55 cm X 25 cm X 30 cm. Its wall thickness is 8 mm and it’s made of plywood. (I did some enclosure volume calculations but now I’m not sure about their validity so I will not give any advice on that) All corners of the enclosure are supported with 45 mm X 20 mm battens to make the enclosure sturdier and improve acoustic qualities. This enclosure has isolated room for all the electronic parts. The core of this speaker is TDA7492P 2 x 50W bluetooth amplifier.
My vision during this project changed and expanded several times. Read on to understand why it was so.
Let’s start with a part list for enclosure:
- 45 mm X 20 mm batten;
- 8 mm thick plywood;
- One tube of silicone and its holder;
- Screws, bolts, washers and nuts;
- PVA glue;
- Duct tape;
- Weatherstrip;
- Angle bracket;
- Wood protection (dark color);
- Super-glue;
- Hinges for the back door;
- Lock for the back door;
- Sandpaper;
- Matte lacquer;
Part list for electronics:
- 2x 25 W 8 Ω speakers scraped from Volvo
- V70;
- 2x 100 W 2.5 kHz – 20 kHz 8 Ω speakers;
- 2x KASUN L-280C 2 Way Crossover filters;
- 3,4 kHz Intersect frequency;
- Lithium Battery Capacity Indicator;
- 250V 6A SP3T switch;
- TDA7492P 2 x 50W amplifier;
Tools used:
- Handsaw;
- “Skil” 500 W jigsaw;
- Hand jigsaw;
- Electric screwdriver;
Step 2: Making the Enclosure - Cutting the Walls
On the first evening when we gathered the main resources and started thinking how would we start the project the first (and probably the most crucial) change to our vision was made – instead of making a simple boring box we would make a box with tooth-like edges for the walls and connect it like a jigsaw puzzle. Well, in the end this change made this project much more difficult and it took twice as much time as it could’ve but now it is much more esthetically pleasing… RIGHT?
After trying to cut the first wall with a regular handsaw we quickly realized that it takes way too much effort and time to cut one wall and the precision isn’t that great either. We needed a solution… I decided to spend some cash and make my life a bit easier by buying an electric jigsaw. This improved the speed of cutting plywood significantly and the precision was improved also!
Even though the precision was improved, enclosure wall dimensions got a bit off by few millimeters. We tried sanding it to improve the situation but it still wasn’t perfect. This was the start of our problems. We decided to make each “tooth” 3 centimeters wide and 8 millimeters deep so walls would come together nicely. This added up to a lot of “teeth”, a lot of drawing, a lot of cutting and, most definitely, a lot of error. We ended up having six jagged-edged walls that looked quite cool by themselves but when put together we would have a horrific see-through box.
Step 3: Making the Enclosure - Electronics Room
We tried evening-out the biggest errors which took up another two or more of our evenings to finish. This enclosure needs to be air-thigh so we realized that sawdust and PVA glue combination, screws and silicone are going to be our best friends when solving this issue.
Since I’m planning on making this a two-part project I figured that I will need some access to all the electronic parts for future improvements. For this reason, I decided to make an additional room inside my enclosure that would be completely isolated from the rest of the enclosure so acoustic qualities would not be at risk. I roughly estimated that 15 cm by 15 cm dimensions would be enough for the room’s purpose. The next task was to figure out how would I attach the inner room’s walls to my enclosure. The best solution that I could come up with was to use aluminum angle brackets in combination with bolts to fasten the walls and use a lot of silicone to prevent any gaps in wall intersections. I also added silicone in every drill hole and next to every bolt and washer to be extra sure that the air would not come out. Drill holes at the top were made for future mounting as well. I had to add an additional angle bracket to fasten one upper corner which had way to wide of a gap between the walls. At this point, at least one part of this project started to feel sturdy.
Step 4: Making the Enclosure - Main Wall
The next logical step for me was to prepare the walls on which the speakers will be fastened. For the main speakers, the big mistake that I made was not using a pair of compasses – I drew the speaker holes by hand and, of course, it wasn’t perfect. At this point I haven’t decided how would I tighten the speakers – would they be inside the enclosure or outside. I assumed my not so even speaker hole would be covered with my speakers.
I thought that it would be wise to apply some wood protection now so later I would not smear my speakers with any of the coatings (I ended up doing that anyways). After doing a closer inspection of the speakers I decided that they should be mounted inside the enclosure rather than outside. That way I would have less gaps between speakers and my enclosure that I would have to cover (remember that my speakers were not made to be mounted in the enclosure, they were just spare car speakers). To save the uneven speaker hole situation I decided to cover the edges of the holes with some weatherstrip. I used silicone to make weatherstrip stick to the enclosure but this was a bad approach because it wasn’t sticking that well so I ended up using super glue. After doing so, speaker holes looked better already. This also decreased the gap between the speaker and the enclosure problem.
Step 5: Making the Enclosure - Tweeter Wall
I did some more research I found out that often crossover filters are used to separate low frequencies from high frequencies. For this I needed to have low frequency speakers – subwoofers, and high frequency speakers – tweeters. I decided that my car speakers would be the subwoofers and I would need to buy myself some tweeters for the high frequency range. When the project was done I realized that car speakers are wide range speakers and their low-end isn’t that great, and I should’ve used proper subwoofers. Since all the space in the front was virtually taken up by the main speakers, I decided to place the tweeters at the top of the enclosure. These speakers mounted on top of the enclosure so any cutting discrepancies would not be visible in the end result. For the tweeters I also used some silicone to prevent any air gaps.
Step 6: Making the Enclosure - Mounting the Main Speakers
Finally, came a time when I had to mount my main speakers to the front wall. For me this seemed the most challenging part of this project. For this I had to adapt car speakers to be suitable for my enclosure. For lack of space reasons, I had to trim the excess plastic parts of one speaker and drill five new holes in the remaining plastic so I would have a place where I could screw the bolts. Other speaker was even more challenging because one of its mounting legs was broken – I had to find a way of tackling this issue. I decided to use angle bracket again and screw it directly to the speaker using bolts. Since this mounting leg was positioned quite high I had to add an additional plywood layer to make it sturdy. To connect the rest of the speaker legs to the enclosure I used long bolts because the legs were hanging in the air (see the pictures). While mounting the main speakers I, of course, used a lot of silicone to prevent air gaps. For bigger gaps, I used left over weatherstrips because they were black so it would look more pleasing from the outside.
Step 7: Making the Enclosure - Preparing for Assembly
Before connecting the walls to form an enclosure I needed to connect the wires to the speakers. When I started doing that I noticed that none of my speakers had polarity marked on them so I had to figure it out myself. I tested each speaker separately and used random wirings and then launched polarity tester app to know if the wiring was correct. I used “Polarity checker” app but I’m sure that any other would work just fine.
I bought not the smallest speaker wires possible because I thought “the bigger the better” but in the end, in my case, I don’t think it’s entirely true. These wires are not that good at bending and they take up quite some space in my “electronics room”. Speaking of “electronics room”, another thing that I needed to do is to drill wiring holes there and some holes for DC input jack, battery charge indicator and power switch on the side wall.
Step 8: Making the Enclosure - Assembly
Now I was ready to assemble my speaker enclosure. I have cut all batten to needed measurements so they would fit nicely inside the enclosure. Oh, and one helpful tip that I learned was to cover the wood with duct tape before cutting it with a jigsaw. That way the wood is cut much more neater and without breaking the edges.
My process for assembling the enclosure was:
- cover the side of the batten which will be touching the enclosure wall with silicone;
- place the batten in the corner of the wall;
- screw this batten to the wall (2 screws on the short edge and 3 on the wider edge);
- connect the adjacent walls;
- screw the remaining battens;
- fill the gaps with PVA glue and sawdust mixture;
- before assembling the back wall, I glued battery charge indicator, DC input jack and power switch onto the left wall of the speaker;
Screwing battens to the enclosure really helped me to reduce gaps between the tooth-like edges but nevertheless I needed to fill these parts with PVA and sawdust mixture. At first, I had a problem with screwdriver heads – they were using up REALLY fast. Something like one screw – one screwdriver head. After trying few different techniques and ruining 4 or 5 screwdriver heads I bought a more serious and expensive screwdriver head that worked flawlessly.
Step 9: Making the Enclosure - Preparing the Surface
Since I filled the enclosure’s gaps with the PVA glue and sawdust mixture I was left with uneven surface near the edges. This meant to me two to three evenings of sanding the speaker enclosure to have a nice surface.
When that was done I moved to covering the enclosure with wood protection to give my speakers a dark wood look. I decided to make the speaker enclosure look better by making the toothed edges of the speaker light-colored. For this I covered them with painting tape before coating the enclosure with the wood protection. The enclosure was covered with three layers of wood protection until I’ve got the color I was looking for.
Step 10: Making the Enclosure - Logo and Finishing Touches
I’ve gotten another creative idea – to add my logo on top of the speaker. The logo is light-colored to make it stand out. I achieved this my covering it with olive oil and putting paint tape on top to protect it while I was covering the rest of the speaker with wood protection. In addition to that I made the contours of my logo black by burning the wood with the soldering iron.
At this point only finishing touches were left for this part of the project. I cut out the backdoor for “electronics room” and added additional inner walls next to backdoor’s edges to minimize the dust that could come in the room.
Step 11: Making the Enclosure - Last Steps
Lastly, I covered all enclosure with three layers of matte lacquer to make the wood more durable and soldered the electronics: amplifier board and two crossover filters. While testing the first main speaker I was quite surprised to see that both of my main speakers were moving and emitting sound. I was amazed because I was sure that I connect only one. Then I realized that the airwaves created by the connected speaker made the other speaker move. This meant that my enclosure is airtight and everything is built as it should be. ?
Step 12: The Video
Here’s a short video showing my new speaker from all sides with some creative touches.
Step 13: Conclusion
This project escalated more than I expected it to escalate. It was mainly because of:
- implementation of tooth-like walls;
- lack of quality tools that could reduce the build time and increase the precision and quality of the build;
- lack of experience in woodworking;
- poor selection of speakers. I should’ve used real subwoofer that were made to be placed in enclosures;
This speaker ended up being not so portable because of its size (my bad for not thinking about that beforehand!) and weight.
Nevertheless, in my humble opinion, the speaker ended up looking pretty good and the sound quality is clear and better than I had hoped for.
If you have any questions or need more detail about some part of this project, please leave a comment bellow.
If you enjoyed this read, consider following me on facebook: https://www.facebook.com/eRadvilla where you will see the latest DIY or photography projects that I do, including the second part of this project.
You can also follow me on Instagram: https://www.instagram.com/eradvilla/
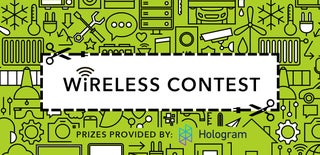
Participated in the
Wireless Contest