Introduction: 4S 18650 Li-ion Battery Cell Charger Powered by Sun
The motivation to undertake this project was to create my own 18650 battery cell charging station that will be a vital part in my future wireless (power wise) projects. I chose taking a wireless route because it makes electronical projects mobile, less bulky and I have a pile of salvaged 18650 battery cells laying around.
For my project I chose to charge four 18650 li-ion batteries at once and connected in series which makes this a 4S battery arrangement. Just for the fun of it I decided to mount four solar panels on top of my device which barely even charges the batteries cells… but it looks cool. This project is powered by spare laptop charger but any other power source over +16.8 volts will do as well. Other additional features include li-ion battery charge indicator to track the charging process and USB 2.0 port used to charge a smartphone.
Step 1: Resources
Electronics:
- 4S BMS;
- 4S 18650 battery cell holder;
- 4S 18650 battery charge indicator;
- 4 pcs 18650 li-ion battery cells;
- 4 pcs 80x55 mm Solar panels;
- USB 2.0 Female jack;
- Laptop charger female jack;
- Buck converter with current limiting feature;
- Small buck converter to +5 volts;
- Tactile button for battery charge indicator;
- 4 pcs BAT45 Schottky diodes;
- 1N5822 Schottky diode or anything similar;
- 2 pcs SPDT switches;
Construction:
- Organic glass sheet;
- Bolts and nuts;
- 9 pcs angle brackets;
- 2 pcs hinges;
- Hot glue;
- Handsaw;
- Drill;
- Duct tape (optional);
Step 2: BMS
Before I started this project, I didn’t know much about li-ion battery charging and for what I found I can tell that BMS (also known as Battery management system) is the main solution for this problem (I’m not saying that It’s the best and only). It’s a board that makes sure that 18560 li-ion battery cells operate within safe and stable conditions. It has the following protection features:
- Over charge protection;
- voltage won’t get higher than +4.195 V per battery cell;
- charging your battery cells with voltage higher than maximum operating voltage (typically +4.2 V) will damage them;
- if the li-ion battery cell is charged to maximum of +4.1 V, its lifespan will be longer compared to the battery that was charged to +4.2 V;
- Undervoltage protection;
- battery cell voltage won’t get less than +2.55 V;
- if the battery cell is allowed to discharge less than minimum operating voltage it will get damaged, loose some of its capacity and its self-discharge rate will increase;
- While charging a li-ion cell which voltage is below its minimum operating voltage it may develop a short circuit and put its surroundings at danger;
- Short circuit protection;
- Your battery cell will not get damaged if there’s a short circuit in your system;
- Overcurrent protection;
- BMS won’t let current get above rated value;
- Battery balancing;
- If the system contains more than one battery cells connected in series this board will make sure that all battery cells have the same charge;
- If for ex. we have one li-ion battery cell which has more charge than the others it will discharge on to other cells which is very unhealthy for them;
There are variety of BMS circuits out there designed for different purposes. They have different protection circuits in them and are built for different battery configurations. In my case, I used 4S configuration which means that four battery cells are connected in series (4S). This will approximately produce total voltage of +16,8 volts and 2 Ah depending on the quality of the battery cells. Also, you could connect almost as many battery cell series in parallel as you want for this board. This would increase the battery capacity. To charge this battery you would need to supply the BMS with about +16,8 volts. The connection circuit of BMS is in the pictures.
Take note that to charge a battery you connect the necessary supply voltage to P+ and P- pins. To use charged battery you connect your components to B+ and B- pins.
Step 3: 18650 Battery Supply
The power supply for my 18650 battery is HP +19 volt and 4,74 ampere laptop charger that I had laying around. Since its voltage output is a bit too high I added a buck converter to step down the voltage to +16,8 volts. When everything was already built I tested this device to see how it performs. I left it on the windowsill to make it charge using solar power. When I came back home I noticed that my battery cells were not at all charged. In fact, they were completely discharged and when I tried charging them using laptop charger, buck converter chip started making strange hissing sounds and it became really hot. When I measured the current going to BMS I’ve got the reading of more than 3.8 amperes! This was way above the maximum ratings of my buck converter. BMS was drawing so much current because the batteries were completely dead.
Firstly, I redid all the connections between BMS and external components then I went after the discharge problem that occurred while charging with solar. I think this problem was happening because there was not enough sunlight for buck converter to turn on. When that happened, I think charger started going in opposite direction – from battery to buck converter (buck converter light was on). All that was solved by adding a Schottky diode between BMS and buck converter. That way the current definitely won’t come back to buck converter. This diode has maximum DC blocking voltage of 40 volts and maximum forward current of 3 amperes.
To solve the huge load current problem, I decided to replace my buck converter with one that had current limiting feature. This buck converter is twice as big but luckily I had enough space in my enclosure to fit it. It guaranteed that the load current will never go above 2 amperes.
Step 4: Solar Power Supply
For this project I decided to incorporate solar panel into the mix. By doing so I wanted to get better understanding of how they work and how to use them. I chose to connect four 6 volts and 100 mA solar panels in series which in turn provides me with 24 volts and 100 mA in total at best sunlight conditions. This adds up to not more than 2.4 watts of power which is not a lot. From utilitarian standpoint this addition is quite useless and can barely charge 18650 battery cells so it is more as a decoration than a feature. During my test runs of this part I found that this array of solar panels only charges 18650 battery cells in perfect conditions. In a cloudy day it might not even turn on a buck converter which follows after solar panel array.
Typically, you would connect a blocking diode after PV4 panel (look in the schematic). This would prevent the current from flowing back to solar panels when there’s no sunlight and panels won’t produce any power. Then a battery pack would start discharging onto the solar panel array which could potentially harm them. Since I already added a D5 diode between buck converter and 18650 battery pack to prevent the current from flowing back I did not need to add another one. It’s recommended to use a Schottky diode for this purpose because they have a lower voltage drop than a regular diode.
Another line of precaution for solar panels are the by-pass diodes. They are needed when solar panels are connected in a series configuration. They help in cases when one or more of connected solar panels is shaded. When this happens, the shaded solar panel will not produce any power and its resistance will become high, blocking the flow of current from unshaded solar panels. Here’s were by-pass diode comes in. When for example PV2 solar panel is shaded the current produced by the PV1 solar panel will take the path of least resistance, meaning it will flow through diode D2. This will result in lower power in total (because of shaded panel) but at least the current will not be blocked all together. When none of the solar panels are blocked the current will ignore the diodes and will flow through solar panels because it’s the path of least resistance. In my project I used BAT45 Schottky diodes connected in parallel with each solar panel. Schottky diodes are recommended because they have lower voltage drop which in turn will make the whole solar panel array more efficient (in situations when some of the solar panels are shaded).
In some cases, by-pass and blocking diodes are already integrated into the solar panel which makes the design of your device much easier.
The whole solar panel array is connected to A1 buck converter (lowering voltage to +16.8 volts) through SPDT switch. This way the user can select how 18650 battery cells should be powered.
Step 5: Additional Features
For convenience sake I’ve added a 4S battery charge indicator connected through tactile switch to show if the 18650 battery pack was charged yet. Another feature that I added is USB 2.0 port used for device charging. This might come in handy when I’ll take my 18650 battery charger outside. Since smartphones need +5 volts for charging I added a step-down buck converter to lower the voltage from +16.8 volts to +5 volts. Also, I’ve added a SPDT switch so no additional power would be wasted by A2 buck converter when USB port is not being used.
Step 6: Construction of Housing
As a base of the housing enclosure I used transparent organic glass sheets that I’ve cut with a handsaw. It’s relatively cheap and easy to use material. To fasten everything in one place I used metal angle brackets in combination with bolts and nuts. That way you can quickly assemble and disassemble the enclosure if needed. On the other hand, this approach adds unnecessary weight to the device because it uses metal. To make the holes needed for nuts I used an electric drill. Solar panels were glued to organic glass using hot glue. When everything was put together I realized that looks of this device was not perfect because you could see all the electronic mess through transparent glass. To solve that I covered the organic glass with different colors of duct tape.
Step 7: Last Words
Although this was a relatively easy project, I had a chance to gain experience in electronics, building enclosures for my electronic devices and got introduced to new (to me) electronic components.
I hope this instructable was interesting and informative to you. If you have any questions or suggestions please feel free to comment ?
To get the latest updates on my electronic and other projects go ahead and follow me on facebook:
facebook.com/eRadvilla
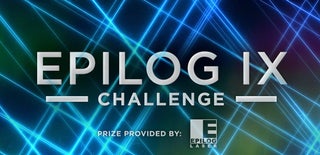
Participated in the
Epilog Challenge 9