Introduction: Palette Wood Wine Rack
I find great enjoyment in the process of taking raw material and turning it into something attractive. Having raw material that is being thrown out or otherwise only adds to a projects value to me. The second half of the pleasure is doing so by-hand as much as possible. You could buy new wood, and even give them the cut list, but what fun would that be?
This project does not have to be done from palettes, and could be done entirely from new wood. The backdrop is all made from palette wood, and the protruding shelves are made with new wood. There are two reasons for that. There are no palettes that are 8” wide. You could use two pieces to do so, but that would make the design look heavier, and would leave visible screws (or awkward gluing). Also, I wanted a hand tool project, and the lack of jointer and planer makes turning out flat shelves too difficult to be enjoyable.
I provided a technical drawing in the pdf. It is formatted to print on an 11x17" paper, but you could just use 'fit to page' in the print dialogue box. If you follow the drawing, you may not even need to follow the steps I outlined below.
Let’s begin shall we?
Equipment (most of which are standard hand tools):
Drill
Hammer
Miter box
Belt sander with 32, 80, and 120 grit paper for said sander (orbital sanders will take a lot more time but could work)
Doweling tools: dowels, correct drill bit, drill stop (optional), dowel center marker (centering pin)
Safety equipment: fine particle respirator, safety glasses, gloves
Backsaw
Combination square
Block plane
Chisel
Clamps, the more the merrier
Good wood glue
15 #8 screws 2"
30 #8 screws 1-1/2"
Sealant and Stain of your choice, I recommend polyurethane and Minwax English Chestnut
Wood:
1 Palette
3ft 1x8
3ft 1x7
3ft 1x4
3ft 1x2
3ft 1x2 cut in half lengthwise to make ¾” square pieces. Because this is a hand tool project, I had to get it cut at the store. They did the cut for me for a dollar. I can’t complain.
Note on safety: if you are doing this in a closed area like I was, then a regular sanding mask will not be sufficient. I tried, and it was far too much dust in an unventilated area. The half-mask respirator is well worth the money. Or use a sanding mask and do it outside. The glasses and gloves are for chips and splinters. They too were useful during sanding.
Note on picture: I made a change to the wine glass holders from that of the picture as you will notice. The one I took a picture of does not hold all wine glass sizes. The one your building will.
Attachments
Step 1: Prepare Wood
Get all the nails and staples out.
Take out the belt sander. Put on the respirator, glasses, and gloves. I use ear protection mostly so I can listen to some music as I work with the screaming sander. It is optional.
Start with 32 grit and get top layer off. Once it looks good, but scratchy from the 32 grit, change to 80 grit. The 80 Grit should remove those scratch marks. Finally go for the 120 grit to smooth it off. If it is not flat, and can be the case, use the block plane.
Don't forget to do the short side too.
Remember that some palettes can contain harmful chemicals, or lead paint. Get informed, and look for markings which may indicate how your wood was treated. There is a lot of information online, and markings can differ from country to country. Generally, I favour HT, which means heat treated, and is usually chemical free. Lastly, check what the palettes were used for. If they carried buckets of pesticides, might not be good. Mine came form a pulp and paper plant to move around finished toilet paper. I considered this safe. The best bet, is to ask questions and use common sense. Good luck.
Step 2: Cut
Now that the dust has settled, literally, and you won't be using any dangerous power tools, you can let your loyal companion join you :)
You could just use the technical drawing in the pdf. Note that I refer to pieces by their nominal size in the text, but the actual size in the drawing. For example, a 1x8 is actually 7.25", hence the 7.25 in the drawing measurements. The width of my palette wood is likely to differ from yours. This shouldn't affect the design since the precision cuts are made from new wood of proper dimensions.
When cutting, especially by hand, it is a good idea to leave a little extra past the line and sand or plane down to it. Make for nice flat cuts or correct dimensions. Unless your amazing with a backsaw.
For the big 7 and 8 inch pieces, square up with your workbench and follow the line you drew and squared with the combination square as best you can.
Cut list
From the palettes: two 31" pieces, six 29" pieces
three 9" pieces of 1x2
three 9" pieces of 1x4
two 17.25" pieces of 1x8
two 17.25" pieces of 1x7
eight 6.25" pieces of those 0.75 x 0.75" pieces
Step 3: Dowel Bottle Shelves
To dowel, first set the drill stop, or alternatively a piece of electrical tape, so that the drill bit hits a depth slightly more than half the length of your dowel. This may take some practice on a scrap piece before finding that sweet spot height on the drill bit.
You could refer to the drawing or read this. Place the dowel holes in the end grain of the 1x4. There are three on each bottle holder where the 9" 1x4 meets the vertical 9" 1x2. Dowel placements are 3/8" from top or bottom of the short side (a.s.a. halfway) and a half inch from each end. Then another 4.5" from an edge. This does not need to be precise, as long as the holes do not protrude from either side. When drilling your dowel holes, make sure you are as vertical as possible. I am lucky enough to have a level on the drill (the bubble that tells you if your vertical). If you drill crooked, then when it's time to align all your dowel holes, it will not work. Trust me, I made that mistake before.
Now that you have 3 holes in the 1x4 end, place a centring pin in the dowel hole. Align the vertical 1x2 to the 1x4 which is laying flat with your combination square and press them firmly into each other so that the pin can leave a mark. Now drill a hole on that mark. Again being sure it is vertical.
Remove the pin and put it in the next hole. Put a dowel in the pair of holes you just made. This will assure you aligned for the next mark. Make necessary alignments, and press firmly together. Drill where the mark is.
Repeat the process for the final hole, and then again for the next two bottle shelves.
Finally, grab the chisel or some sand paper and clean up those holes so they don't introduce a gap when trying to glue the pieces together in the next step.
Step 4: Glue Bottle Shelves
Make a test run with your clamping system. Pretend there is glue and that your clamping it together. Make sure all the faces come up tight against each other, and that the dowels are not going to cause any gaps. Also make sure you can squeeze the clamps tight on your pieces without and buckling. I put a perpendicular piece across so that it holds down the 1x4s and keeps everything nice and flat. I have enough clamps to do this in one move, but you can do it in three steps if you like. Make sure there are at least two strong clamps per shelf.
Now you can glue. Remove all dowels. Put a bit of glue in each dowel hole. Then with a small brush (any cheap one works) make sure a thin layer of glue is spread across the entire surface of the 1x4. No need to make a thick layer, it will only gush out as you clamp down. Put in the dowels, give them a light tap with a mallet to make sure they are properly seated, and put it all together. Now clamp down. Wipe off any excess glue.
When gluing, the glue will have only a limited amount of time before it begins to set. Often about 5 minutes. After 5 minutes, if you have started clamping tight, don't. If it makes a bad bond it will be hard to dis-assemble and correct. Better let it dry and sand it odd than ruin your piece.
Wait for however long your glue tells you to. Probably 30 minutes. While this is setting, the next step can begin.
Step 5: Dowel and Glue and Dowel Again
Note: I opted to skip this step, and glue the trapezoidal pieces to the 1x8 right away. That is the picture I used in the intro. The new wine glasses do not fit, so I made this adjustment so it can fit any glass. Please forgive the fact that I forgot to take another picture.
This step is long, but also straightforward. You will need to dowel a 6.25" long piece of the 1x2" you had cut in half. One flush with each end. And then another 4.75" inwards from each of the end pieces. This makes 4 pieces.
Simply make 2 dowel holes in the small 3/4" pieces. The holes can be anywhere as long as you remember where they are. I chose close to each end. The reason you want to remember is because you will be putting dowels on the other side in the next step, and don't want to drill into your freshly glued dowels.
Put a centring pin in one of the holes and align it. Press firmly to make a mark. Drill in mark. Then remove pin, place a dowel, and repeat with the next hole. Hopefully your first gluing session is over by now and your clamps are available for this step. Clean holes. Make a test assembly and clamp to verify. Glue these together. I use as many clamps as I can. The more pressure distributed across the piece, the better. Pockets/gaps do not make for good bonds., glue, and clamp. Then move on to the next piece. That way it can dry as you work.
Make the holes for the dowels and align them for the remaining three pieces. Then start over on the second shelf. Each time your clamps are free, start gluing the next one. This will save time.
When those dowel holes are done but the glue is still setting: You will be making dowel holes in the 1x8 because it will be glued onto this setup you just made. Make two holes on each 3/4" piece in an area where the previous dowels will not get nicked. Place a centring pin on a hole in one of the corners. Next align the 1x8 to be flush on one end and both sides. Press firmly.... I think you got the process mastered by now. This will make the holes for the dowels on the 1x8. DO NOT GLUE THE 1X8!
Step 6: Tape and Stain
Now you need to stain inside there because after the next step, you won't be able to reach inside there. Luckily you will only be staining the inside, not the outside or the edges. This allows you to work while it dries.
The art of wood stain is quite unique for each person. I use pre-stain treatment to get a more even colouring, especially on palette woods and even more so when it is pine since it does not tend to absorb stain evenly. Then I like to use a darker stain, and only put a little on the cloth. Then rub it hard into the wood across the whole piece, adding more stain when my cloth is dry. Then immediately wipe off excess stain. This technique seems to bring out a lot more of the grain character. I am sure some wood experts would recommend other techniques. If you like the look in the picture, then give it try. If you also like the colour, it is English chestnut from Minwax(C).
You will also be staining the 1x8 board too. So you will need to place 3/4" tape flush to each shorter end. Then again 4.75" from each of those pieces. In other words, the same placement as the small 3/4" pieces on the previous board (so covering up the dowel holes you just made). Why? Because wood stain seals the wood to an extent (it even says so on the can of stain) and prevents the glue from getting in there and making a good bond. Once you have finished staining, you can remove the tape. No need to stop working as it dries, the remaining sides are not stained. On to the next step!
Step 7: Glue
If you have enough clamps to firmly press each of the pieces together then great; that is probably the best idea. I was short in clamps and used two big bags of dry cement. It was really heavy, and worked well.
You can move on to the next step as these two shelves are being glued. It will likely use all your clamps and heavy objects.
While this sets, move on to the next step
Step 8: Drill and Countersink Clearance Holes
IMPORTANT: these clearance hole placements only work if our boards have the same width. If we do not, you will need to adjust it, which I will explain how to below.
The clearance hole placement on the 31" pieces can now be done. You should really look at my drawing for this one. But if you insist, the holes are all 1-3/16" from one edge. The starting from one end mark at 1-3/16", 4-3/4", 13-1/8", 16-11/16", 25-1/16", 28-5/8". Starting from the other edge and other end, repeat.
Now use a drill bit that is the same size as the screw including the threads, and drill vertically on each mark.
Then take out the countersink, and countersink those holes. To do so, hold it vertically, let it spin for a few seconds, and check if the screw head can fit in the cone shape you just created. If no, go for a few more seconds. If too big, don't let it run as long the next time. You will get the hang of this fast enough.
Next set of clearance holes:
On a 29" board, places 4 marks at 3/8", 5-7/8", 11-3/8", 16-7/8" from one end. All holes are 1-7/8" from one edge. Repeat on a second 29" board.
Now your done for the day. All that glue needs to set. Grab a cold one
If you have a different width of board:
If your boards are not the same size, the hole placements are made so that there are two screws on each end of each 29" board. I divide the width of the board by three, call that distance X. I place a screw X from the bottom end of the 31" board, and X from the side edge. Then 2*X from the end and 2*X from the same side edge. Now move each hole up by the width of one board staying parallel to that reference side edge. Now you have clearance holes for two boards on one end of the 31" board. Then do the same thing from the other end of the 31" board. Finally you need to place two boards in the middle. This part is easy. Draw a line at 15.5" from either end of the 31" board. Place a hole X from the edge, then X above the line and X below the line. Two more holes, 2*X from the same edge, and then 2*X above the line and 2*X below the line.
Done for the day
Now you are done for the day. The glue needs to fully set before the next step. This takes 24hrs. Anyway, by this time, it's usually pretty close to beer-o'clock. So grab your loyal companions, a tennis, a cold one, and enjoy the evening and the fresh air. You've earned it, and they are looking forward to it. Mine were.
Step 9: 45deg Cuts
Start by cutting a guide. This is any piece, at a 45 degree angle. You will rest your blade against it as you saw through the 1x7. Using your miter box in either of the two methods demonstrated in the photo works. I was lucky and found an old French cleat, which saved me a step. Now line it on your cut lines, and start sawing. I wish I had a trick to offer, sadly all I can say is good luck!
It is mostly for aesthetics, so you can cut a 0.5" hole vertically if you prefer. You only really see the first inch, so if it waivers after that no one will notice. Mine do, and so far no one spotted it.
Step 10: Edge Cleaning and Stain
All the glue is set, now you can use a combination of sanding and planing to get perfectly flat and square edges. Using a backsaw makes not so nice edges, and then gluing doesn't make them align all that great. This step is vital for a nice clean square look. Make sure no glue is left anywhere so that your stain can looks great.
Place a piece of tape on the edge where the 1x8 shelf will sit. It too will be glued and cannot be stained.
Now stain everything.
Time for lunch while the stain dries.
Step 11: Dowels, Dowels, Dowels
On the edge of the 29" piece where there is tape, you can now remove it and start making dowel holes. The first at 5/8" from the edge, then every 2" after that until you reach 8 holes. You know the routine by now, so line that up with the glass holders you just finished, dowel away, and glue hard. Do this for both shelves.
Step 12: Screw the Bottle Holders to Their Board
Clearance hole and counter sink marks at 0.5", 4.5" and 8.5" from the end, all 3/8" from the edge.
Before screwing, you need to make a pilot hole. Use a drill bit the size of the shaft of the screw without the threads. Now when you line up the shelf nicely with the board, and make the pilot hole by putting the drill through the clearance hole and making a small shallow hole. This will prevent splitting when you screw in your piece.
Using the 2" #8 screws, you can screw in your first screw. Then align nicely again and place your second pilot hole and screw. Alignment is now fixed in place. You can pilot hole and screw your last one.
Repeat for all three shelves.
Step 13: Screw Glass Holders
Now that you glass holder is nicely glued, you are going to screw into the trapezoidal shapes. The clearance holes are already there from a previous step. The shelf won't move since you glued it there, so just pilot hole and screw away with 2" #8 screws
Step 14: Assemble and Seal
The assembly should be a breeze since your a pro at pilot holes and screws now. Use the 1-1/2" #8 screws for this job.
There is going to be wine bottles, and likely wine spills. I use a water based sealant everywhere except the 1x8 shelves; those shelves are going to have full glasses and open bottles on them so I put on two layers of polyurethane.
I did a few of these racks, and decided to add a little wood burning art to one of my ledges. Also, you'll notice I had to cut a notch so that it fit nicely with the vertical board.
You worked all day yesterday, and it's likely Sunday afternoon by now. But your done!!!!! I would recommend hanging it with a French cleat on the second board from the top. There are many resources explaining how to do that.
Hope you enjoyed!
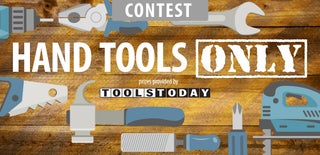
Participated in the
Hand Tools Only Contest 2016