Introduction: Panavise Jr Knob Turning Tool
I love my Panavise Jr Tool, and use it in all kinds of craft and electronics projects to hold parts (in all kinds of angles) while I work on them. The threads of the Panavise Jr are fine, which allows for very fine grained movements of the jaws. However, this also means that I have to turn the knob many many many times if I want to move the jaws over a longer distance!
What I wanted was a tool that could be used to tighten (and loosen) the Panavise Jr knob easily.
I would need a relatively high torque, low rpm motor to turn the knob. I
repurposed an led light (these things are really cheap now!) - the cylindrical 3 AAA battery holder was perfect for my needs, and the form factor for the tool was also good. Some 3D printed parts for holding the motor and for the knob, and a PCB for the wiring, and I was done!
Currently, the Panavise Jr Turning Tool only runs clockwise (therefore tightening the jaws). In my next iteration, I plan to add a DPDT momentary center off switch, so I can run the motor either clockwise or counter-clockwise.
Above, you can see the finished tool. Read on to find out how I made it! I made this at TechShop!
Step 1: Repurpose the Flashlight
I had to remove the LED casing, which was glued on to the flashlight (the model of flashlight that I had was an aluminum casing with a removable base for changing batteries. The top was not removable).
I removed the base and the battery holder. Then, using a heated exacto blade, I cut into and around the plastic cover for the led. I then used a screwdriver (from the base end), and used to to apply some pressure and push the led casing out from the top.
With a little cleanup, I had the aluminum casing with the top removed and available to accommodate the motor.
Step 2: 3D Printing the Parts
I had two parts to 3D print
1) holder for the motor that fit in the space in the flashlight where the led was
2) Knob that would fit the Panavise Jr on one end (and fit onto the motor shaft at the other end).
I've attached the design files for those.
Step 3: Final Assembly
Next up, cut a pcb round to fit the aluminum casing top. I didn't have a round pcb, and the local radioshack was out of stock (http://www.radioshack.com/product/index.jsp?produc... so I cut a regular one with a rotary tool and sanded to edges to make it into a round one.
Solder wires to the motor leads, and then solder the wires to the pcb, one to the center, and one to the side (perimeter). Desolder the spring from the led base, and then solder it onto the center of the pcb, and connect it to the center wire.
Ensure that the motor is wired such that it rotates clockwise. This will allow the tool to tighten the jaws when the flashlight button is depressed.
In the next version, I plan to add a DPDT momentary switch with center off to the aluminum casing, so that the motor may be operated in both clockwise and counter-clockwise rotations.
Slide the motor into the 3D printed base, and then push the pcb and 3D printed base into the aluminum casing top. Glue it in place for a permanent fix. Ensure that the electrical connections are ok and the motor rotates when the button is depressed. The wire connected to the edge of the pcb sits on the lip of the housing and acts as ground, and the spring connects to VCC of the battery. The pcb and base have to fit snugly and tightly to ensure proper electrical connection.
Push the 3D printed knob onto the motor.
You now have a Panavise Jr tightening tool. If you add the DPDT momentary center off switch, you can have a Panavise Jr tool for tightening and loosening the jaws.
I will create another Instructable once I have done that.
Enjoy!
Sridhar
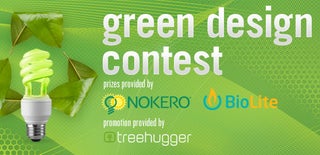
Participated in the
Green Design Contest
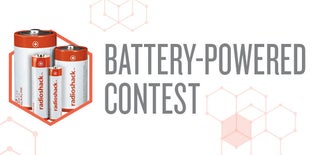
Participated in the
Battery Powered Contest

Participated in the
Gadget Hacking and Accessories Contest
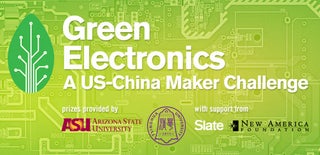
Participated in the
Green Electronics Challenge