Introduction: Put Your SMD Parts on Standard Perfboard
Instructables is having an Electronic Tips and Tricks Contest now, so I thought I would share some of mine regarding the use of SMD parts and techniques on standard issue, single sided, good ole perfboard. Many of us more thifty types often find the parts to our creations out of old, broken, cheap electronics from all sorts of places. Of course in the modern age its pretty rare to see many, or any though hole components.
While you could break out the CAD and laser printer to make your own PCB's, sometimes its a pain in the butt if you just want to wire something together and be done with it. The good news is that many SMD packages will fit on standard 0.1 inch perfboard with little hassle. Of course this does not cover all the possible SMD packages, but I hope it encourages you to try new ideas about getting these little packages of electronic goodness in your project.
Step 1: What You Will Need
Tools:
Soldering Iron
Solder
Solder Wick
Flux (I like liquid in a felt tip pen)
Tweezers
Magnifying Glass (helpful but not required)
Utility Knife
Wire Cutters
Parts:
As stated before, many SMD parts will fit on normal perfboard, off the top of my head ...
TSOP
SOT
603, 805 1206 and larger chip style parts
SMA, SMB
Some PLCC
Most Electrolytic Capacitors
A Plan:
For illustration I will be making a simple circuit that uses a DIP 8 IC, normal though hole ceramic cap, 6 1206 size resistors, a mid sized SMD electrolytic cap, 4 pin PLCC led's and a TSOP 16 IC.
The circuit is a 555 timer that's simply sending a clock pulse to a 74161 4 bit binary counter, which has its outputs tied to LED's, Impressive? no ... easy to make and I found the parts laying around? yes!
Step 2: Surface Mounted Though Hole Parts
Wait what!? I thought we were soldering surface mount parts to perfboard, why would I want to solder though hole parts to perboard, it has the holes already!
There is a few good reasons to do this, let me explain...
1) Maybe you have a mix of SMD parts and though hole parts and want everything on one side
2) Maybe you don't want to flip your board over every 2 seconds and get all your pins backwards, sometimes its just easier
3) Maybe your putting your circuit in a metal mint tin, without stuff poking though the board you don't have to worry about insulating the metal can
4) Maybe your tight on space and that extra 8th of an inch saves your butt (which is has for me a couple times)
5) Even if you print your own circuit board, maybe you don't want to drill a billion tiny little holes with a ultra fragile drill bit
Anyway this is real simple, on DIP IC's you just simply grab the leads with a pair of pliers. If you look at the leads you will see that near the body of the chip the leads are fat, then sharply cut away to thin pins. Position the chip in the pliers at the point where they go from fat to thin and bend outwards to 90 degrees. Now they sit flat on the board and the leads are ready to solder surface mount style.
For other components its just a matter of bending the leads out in a L shape and trimming with cutters.
Soldering the components I find it easiest to flux the pins, and add a single bead of solder on the board, keeping it molten you can then put the part in to place. Once secured its easy to solder all the other leads. This technique is used for all the parts going onto the board.
Step 3: Electrolytic Capacitors
SMD electrolytic caps are a bit different than most SMD parts as the leads are very long (long enough that if you pull them straight and remove the plastic spacer you can use them as though hole parts), so you have to be careful about where you position them.
If you try to space them evenly against the grid on the perfboard there might be a pad that just touches the two leads, which would bypass the cap. Large caps don't suffer this problem, but its good to take a look before you get everything soldered down. Check it out, and if need be offset the cap.
For soldering, flux up the leads and put a little solder on a pad. The leads extend just slightly past the body of the part which will be good enough to get a temporary solder joint. Once the part is somewhat stuck to the board, move to the opposite side, heat what little lead is extended and the pad below it. You should get a bead soldering the edge of the lead to the pad, and if you have good flux it should suck it under a little bit as well. Go back and properly solder the side that was just holding on by a hope and a prayer and you should be done.
Step 4: Chip Parts
Chip parts or SMA/SMB parts, like resistors, ceramic capacitors, and diodes are super easy, just flux up the end a little, heat up a solder blob on the board and push it in making sure the solder wicks to the part . Almost every single time the parts will line up on the pads. 603's seem a little short but will solder, 1206's are just about perfect, 805 sized parts are great, lining up with the edge of each pad
SMA/SMB parts are quite large and usually line up over 2 or three holes.
In my second Picture I have the electrolytic part, and 2 1206 resistors with a solder bridge between the 2 resistors because I know I will need to place a wire there later.
Step 5: A TSOP 16 IC
Now that I have the components I need for the 555 timer laid down, its time for the next IC. Its a 74F161 (yea I said F, so its quite old) which is in a TSOP16 package. TSOP's are similar to DIP packages in layout, just smaller and thinner.
The problem with laying them down on perfboard is you end up with 2 pins of the IC sharing a single pad. Sometimes this can work out to your advantage on a couple of pins, but this is a major deal breaker. There are a few ways to deal with it.
One is to solder a bunch of tiny wires to the leads and then solder them to pads, I have done this a few times and its a exercise in patience. Plus since your putting the chip on the copper side of the board you have to put some tape down to insulate the pins from shorting out on the pads below the chip.
Another is to order a breakout board which converts the size of the chip. which can get expensive, and you have to wait for it.
Or you could just double the amount of pads you have to work with, and this is really easy with an utility knife. Let me tell you how you how. Take your utility knife and place it about half way across the pad on one side of the hole, holding it at an angle to the left similar to \, press down slightly ... it doesn't take much and lift. Then do the same on the other side of the cut you just made holding it on a / angle, and it will produce a (more or less) V notch.
I don't try to do both sides of the hole at once, as it works best if you concentrate the light pressure at the end of the blade, but feel free to experiment. This works ok with circular pads, but it works great with square pads ... Obviously this wont work if your perfboard has the inside of the hole plated, but you could use a small drill to clear that away if you wish.
Step 6: PLCC
PLCC's come in all sorts of sizes, but you will find that many of the larger packages will fit on a perfboard, and they often have leads exposed on the sides of the chip you can solder to. In my case I am using PLCC 4 pin LED's and they fit just about perfect on 4 pads, simply plop down and solder.
After that its just a few more resistors and some wiring and this board is ready to go. I wont go into too much detail about wiring, cause, well, its wiring. I do like using non insulated wire whenever possible, you can solder one end down and run it wherever you need without having to worry about cutting and stripping a bunch of little pieces.
You can get 24 gauge copper wire from CAT5 and other similar types of telephony cables that were originally meant to go though your walls, though you have to strip it.
For Items that require insulation I use strands of ribbon cable. Its usually plentiful and if you strip a length of it, twist it tight, flux it up, and run a bead of solder down it, you now have another source uninsulated "solid" wire.
For the super tiny connections on the TSOP IC I used 30 gauge wirewrap wire, since its so tiny its easy to solder to the likewise tiny pins of SMD parts, and is available just about anywhere that sells electronic components.
After the board is all wired up, we are ready to plug it into 5 volts and watch the LED's count away in binary. I hope you found some useful information in this instructable and if you have any related experience, questions or comments please post in the comments!
Thanks for reading.
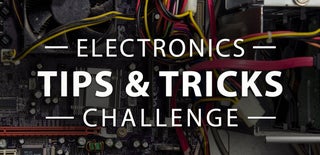
First Prize in the
Electronics Tips & Tricks Challenge