Introduction: How to Build a Quadcoptor. (NTM 28-30S 800kV 300W and Arducopter APM 2.6 & 6H GPS 3DR Radio and FlySky TH9X)
This is a tutorial about how to built a Quadcopter using NTM 28-30S 800kV 300W motors and Arducopter APM 2.6 & 6H GPS & 3DR Radio. I have tried to explain each step with a number of images. If you have any questions or comments please reply in comments or mail to rautmithil[at]gmail[dot]com. You can also get in touch with me @mithilraut on twitter.
Sponser: radlab.sfitengg.org
To know more about me: www.mithilraut.com
Step 1: List of Components
Motor Propeller and ESC
- NTM Prop Drive 28-30S 800KV / 300W Brushless Motor (short shaft version) 4PCS.
- NTM Prop Drive 28 Series Accessory Pack 4PCS(Get extra 2 because these get damaged or bend during crash).
- Afro ESC 30Amp Multi-rotor Motor Speed Controller (SimonK Firmware) 4PCS.
- APC 1147 Propeller Blade For RC Multi-Copter Helicopter Quadcopter 2Pair(Get extra 4 pairs if you expect to crash the drone very often)
Radio and Fail safe
- Upgraded FlySky FS-TH9X 2.4G 9CH Transmitter With FS-R9B RM002 Mode 2
- Turnigy TrackStar Epic Fail Safe for Car & Boat
- Turnigy 2650mAh 3S 1C Lipoly Tx Pack (Futaba/JR) OR HobbyKing 1500mAH LiFe 3S 9.9v Transmitter pack.
Frame
- Aluminium Square Tube (280-395x10mm) 4 PCS. OR Carbon Fiber Square Tube 750x10mm 4PCS
- Center plates from this frame (Initially I build the quadroter using this frame but the arms were made of low grade aluminium which bent during one of the crash. Now I am using just the top and bottom center plates of that frame. All those holes on the center plates are required. You can build your own out of Carbon Fiber plate or Lexan using these designs.) OR
- You can buy these off the shelf plates Hobbyking X550 Glass Fiber Main Frame Upper Plate 1PC
- Hobbyking X550 Glass Fiber Main Frame Bottom Plate 1PC
- You can buy these off the shelf plates Hobbyking X550 Glass Fiber Main Frame Upper Plate 1PC
- F450 F550 SK450 Z450 TL450 Universal High Landing Skid Gear 1 Package (Comes with 4 landing gears)
Wiring and Power
- ZIPPY Flightmax 5000mAh 3S1P 20C 1PC(Get a spare if you don't want to wait for recharging the battery)
- Lipoly Low Voltage Alarm (2s~4s)
- Turnigy High Quality 12AWG Silicone Wire 1m (Red)
- Turnigy High Quality 12AWG Silicone Wire 1m (Black)
- 5X Pairs 4mm Gold Bullet Connector Banana Plug (Don't need so many but good to have spare)
- 10x 3.5mm Gold Bullet Banana Connector Plug (Don't need so many but good to have spare)
- XT60 to 4 X 3.5mm bullet Multistar ESC Power Breakout Cable
- XT60 Male/Female Bullet Connector Plugs 2 pairs
Flight Controller Arducopter kit APM
- APM Flight Controller Set APM 2.6 & 6H GPS & OSD & 3DR Radio 1 set
- APM2.5/2.6/2.8 MWC Flight Controller Light & Buzzer Indicator V1.0 1PC.
Tools
- Screw driver set
- Wire Stripper
- Pliers
- Allen key or Hex key set (Get a set as we require 2 different sizes)
Nuts Bolts and Miscellaneous
- Nylon Spacer 3.5mm id * 2inch 4 pcs.
- Hex bolt 3.5mm x 25mm and compatible self locking nuts(These came with the frame but you can buy similar ones from hardware store) * 20
- 3.5mm * 10mm flat head bolts (which go in the nylon spacers) and compatible nuts * 15pcs
- Battery charger (if you don't have one already)
- Shrink tube 5mm red and black color
- Cable ties 6inches 25pcs.
- Cable ties 12inches 5pcs.
- Hacksaw (if you plan to cut the square tubes)
- Power drill
- Drill bit (3.5mm)
- Soldering iron
- Solder wire
- Hot glue gun and stick.
- Lighter
- Single and Double side adhesive tape
Step 2: Assembling the Motor * 4
Tools required:
- Allen key set
- Screw driver set
Unpack the accessory set. The motor mount will fix on the base of the motor using the silver screws. The propeller adapter will fix on the top of the motor using hex screws.The ring and prop saver nut will go on top of the adapter.
Repeat this for all 4 motors.
Step 3: Assembling the Arm * 4
Tools required
- Hack saw (if you don't have the tubes cut to specific length)
- Allen key set
- Power drill
- Drill bit (3.5mm)
- Pliers
Take the square tube and cut it into 4 pieces of same length between 280mm-395mm. 280mm is the minimum length because the recommended motor-to-motor distance for these motors and propeller is 560mm. I have kept the extra 115mm to attach a propeller saver but this is optional.
The distance between the 2 holes for the arm on my center plate is 20mm.
The distance between the 2 opposite holes of the motor mount is 34mm.
Hence from one end I drilled four 3.5mm holes with center at 5mm,25mm,221mm and 255mm. The first 2 holes are for attaching the arm to the base plate. The last 2 holes are for attaching the motor. Adjust the distance between the first 2 holes according to the distance between the holes on the center plate.
Attach the motor assembly to each arm using the hex nut & bolts, allen key and pliers such that the motor wires point in the center of the quadcopter.
Repeat this step for all the four arms.
Step 4: Assembling the Body
Tools required
- Allen key
- Pliers
Take the arms assembled in the previous step and sandwich them between the center plates such that it forms an 'X' shape. The arms are attached at an angle of 90 degrees to adjacent arms. Use the hex bolts, nuts and washers to attach the arms to the both the center plates.
I will attach the landing gear in the end.
Step 5: Soldering Connectors
Tools required
- Solder iron
- Solder wire
- Hot Glue gun
- Lighter
- Wire stripper
Soldering the battery connectors:
The battery mentioned in the list of components (ZIPPY Flightmax 5000mAh 3S1P 20C) has 4mm bullet connectors as the discharge plug. These connectors aren't directly compatible with the XT60 connectors used in most of the cases. Hence we will solder a small converter out of these components
1. 4mm bullet connector pair * 1
2. 3.5mm female bullet connectors * 2 (3.5mm bullet connectors are compatible with XT60 connectors). Alternatively you can use a female XT60 connector.
3. 10cms of 12 AWG wire (Black and red respectively) * 1
On left side of both red and black wire solder the 3.5mm female bullet connectors.
On the right side of red wire solder the 4mm male bullet connector.
On the right side of black wire solder the 4mm female bullet connector.
Once all the connectors are soldered, insert small cuts of 5mm heat shrink tubing on the connection and heat it using the lighter.
Soldering the power module:
The APM 2.6 kit has a power module which monitor the battery voltage in flight. It also has an inbuilt BEC which powers the the main board. The input end goes to the battery and the output end goes to the ESC's.
Cut 2 pieces of 5cms each from the red 12AWG cable and 2 pieces of 5cms each from the black 12AWG cable.
Solder the one end of both the red wires on the top of the power module(Top side is the one where 'power module' is printed). Similarly solder one end of both black wires on the bottom of the module.
Insert heat shrink tubing in all the four wires.
On the input side, solder a male XT60 connector checking for polarity of the connector with the red and black wire. On the output side, solder a female XT60 connector once again checking for polarity of the connector with the red and black wire.
Heat shrink the soldered connections of both XT60 connectors. On the power module apply layers of hot glue to insulate the soldered connections.
Step 6: Connecting the ESC's to the Motor and Battery
Electronic Speed Controllers are used to control the speed of motors. Since there are 4 motors, we require 4 ESCs. The ESC's are rated for the maximum current they can handle, the voltage and the input frequency. The ESCs given in the list of components come with 3.5mm bullet connectors attached on both ends. The input side of the ESC go to the power distribution. The output side goes to the motors. The servo cable is to be connected on the main board is used to issue commands.
Place the ESC on the arm. Connect the output side of the ESC to the motor. Here the polarity doesn't matter. The motor will simply rotate in opposite direction if any 2 pins are switched.
Slide the input side cables of all ESCs in between the 2 plates. Maintaining appropriate polarity, connect the 3.5mm terminals of power breakout board to the input terminals of ESC. Red wire of ESC goes to Red connectors of breakout board. Similarly black wire goes to black connectors. Slide out the XT60 connector from one side.
For now the ESCs are not firmly fixed to the body. We will do that later.
Step 7: Assembling the Shock Absorber and APM Board
The APM 2.5 kit from Banggood come with a shock absorber kit which is used to protect the APM board from the vibrations caused during flight. It consists of 2 plates connected with 4 rubber paddings. The bottom plate is attached to the frame. The top plate holds the APM board.
Tools required
- Double sided adhesive tape
- Screw driver
Take the bottom plate and insert the protruding parts of the rubber paddings on the four corner holes of the plate using a screw driver. Repeat the same procedure and attach the top plate to this assembly. Cut 2 small portions of double sided adhesives tape and stick it on the top plate. Remove the insulating cover of the tape and attach the APM board right in the center of the top plate.
Step 8: Assembling the GPS Module
The APM 2.6 kit mentioned in the list of components comes with the Ublox LEA-6H GPS with compassbuilt in .The GPS module comes with a stand to attach it. Assemble the stand as shown in the image. While attaching the module to the body, make sure the the triangle on the top of the module points in the forward direction.
Step 9: Attaching the APM Assembly and GPS Assembly to the Body
The high amount of current consumed by the motors can generate magnetic interference in the wires. As a result it is advisable not to attach the board near the motor wiring. Hence, we will use nylon spacers to offset the distance from the center plate.
Tools required
- Screw driver
- Pliers
To attach the APM board assembly.
The APM board assembly can be attached to the body using four bolts spaced 4.5cm from adjacent bolts in a square configuration. If you are using a different plate drill these 4 holes equidistant from the center of the plate.
To attach the nylon spacers to the body, take four 3.5mm bolts and insert them upside down in the corresponding holes if the top center plate as shown in the image. Press the bolt with your finger from the bottom and screw the nylon spacer until its fixed tightly. Repeat this process for all the four spacers.
Now place the APM board assembly on top of the spacers and fix them using four 3.5mm bolts such that the "forward" direction marked on the APM board point to the forward direction of the quadcopter.
To attach the GPS assembly.
You can fix the GPS assembly anywhere near the APM board. Drill 2 (3.5mm) holes 2-3cms apart and fix the GPS assembly stand using two 3.5mm nut bolts as show in the picture. Stick the piece of double sided adhesive tape in the cavity on the bottom of the GPS module. Carefully paste the GPS module on top of the stand so that the triangular arrow aligns in the forward direction of the quadcopter.
Step 10: Attaching the 3DR Radio Telemetry Module
The 3DR Radio telemetry consists of a receiver and a transmitter. The transmitter has wires coming out of it as shown in the picture. The receiver has a male USB output on its end. The package also comes with 2 antennas which are to be connected at the end of each module.
Take a piece of double sided adhesive tape and stick it anywhere on the edge of the center plate. Then stick the transmitter module on the tape and press firmly. Point the antenna outwards and facing vertically downwards.
Step 11: Attaching the APM Light & Buzzer Indicator
The light and buzzer indicator helps the user to know the modes of operation by a change in color even while flying. The Buzzer sounds in case of low voltage. Since the light should be visible while flying, it is recommended that the indicator be attached on the bottom of the body. I used a piece of double sided adhesive tape to secure the indicator on the bottom plate. I router the wires through one of the many holes present on the plate.
Step 12: Attaching the Landing Gear
The landing gear has 4 holes on the top which can be used for attaching it to the arms. However, since the arm is 10mm wide and the distance between holes is grater than 10mm, I used 2 cable ties to attach the landing gear to the arm and also secure the ESC.
Place the landing gear on the bottom side of the arm 50mm away from the end of the plate and run a cable tie through the 2 holes, bring it over the arm and secure the tie. Run the second cable tie through the other 2 holes, bring it over the arm, place the ESC on the arm and secure the tie. This way the ESC gets attached to the arm.
Step 13: Attach the Power Module Assembly
Connect the "OUT" side of power module assembly soldered in Step 5 to the XT60 connector of XT60-4x3.5mm power distribution. Paste the power connector module between both the plates(using double sided tape) so that it doesn't hang outside.
Connect the 3.5mm side of the battery connectors (soldered in step 5) to the "IN" side of the power module.
Step 14: Attach the Battery
Use a Velcro strip about 25cms long and insert it through the slits in the bottom plate such that there is a gap of 5-8cms for the battery to fit. Place the battery in the gap and secure it using the Velcro. If the battery slips use 2 cable ties to secure the battery on both ends of the battery.
Step 15: Attaching the 2.4 G Radio Receiver Module
The FlySky FS-TH9X 2.4G 9CH Transmitter comes with a FS-R9B 8 channel receiver. This radio is responsible for sending navigation and control commands to the quadcopter. We will use servo cables to make connections between the receiver module and the APM board. Since those cables are 12.5cm in length, stick the receiver module near the APM board using a double sided tape. Secure the antenna facing vertically downwards to an arm using a tape.
Step 16: Connecting the Modules With the Main Board
Connecting the GPS module
The GPS module has 2 outputs. One output gives the GPS reading. The other output gives the Compass reading. The GPS output goes into the upper "GPS" slot. The compass output goes in the "I2C" slot.
Connecting the 3DR telemetry radio
The 4 pin output of the telemetry radio goes into the "Telem" slot on the upper left corner of the APM board.
Connecting the power module
The 6 pin out output of the power module goes into the "PM" slot on the lower left corner of the APM board.
Step 17: Connecting the ESC's to the APM Board
The quadcopter is built in a "X" configuration. Connect the 3pin signal cable of each ESC to corresponding slot in the output as shown in the diagram. Connect the ESC of each motor to these pins.
A Top Right--------- Pin 1
D Top Left----------- Pin 3
C Bottom Left------ Pin 2
B Bottom Right---- Pin 4
The signal cable consists of 3 pins
Brown - GND
Red - VCC
Yellow - Signal
From the edge of the boards connect the cable as shown in the image.
Step 18: Connecting the Radio Receiver
The APM needs commands from at least 5 channels. The other 3 channels can be connected optionally. The 5 channels required are
Input channel - Receiver channel
1 - 1 (Roll/Aileron)
2 - 2 (Pitch/Elevator)
3 - 3 (Throttle)
4 - 4 (Yaw/Rudder)
5 - 5 (Auxiliary - Used to switch modes)
6 - 6
7 - 7
8 - 8
Use four 3pin servo cables to connect the signal side of receiver module to the signal side of APM board. The receiver module is powered via the APM board, so make sure at least 1 of the 3 pin connectors is connected horizontally across all 3 columns.
Step 19: Assembling the Radio Transmitter
The Fly Sky TH9X comes with
- FlySky FS-TH9X 2.4G 9CH Transmitter Mode 2
- FS-R9B 8CH 2.4GHz Receiver
- RM002 2.4GHz Module
- Bind Plug
The RM002 module connects in slot behind the Transmitter. It comes with an attached antenna.
Attach the transmitter battery and place it in the battery compartment as shown in the image.
If this is the first time that you are setting up the Radio system then you will have to perform the binding procedure to bind the transmitter with the receiver. The steps to the procedure are mentioned here.
You can also watch this video and do the same.
Step 20: Connecting the LED Indicator and Buzzer
Connect the Red and Black jumper pair in the '+' & '-' pin of the APM. The other three wires connect on the signal pins.
White---> Pin 5
Blue----> Pin 6
Red----> Pin 7
The indicators will glow or blink corresponding to GPS and ARM status. The buzzer will sound when ARMING, low battery or GPS connectivity issues.
Step 21: Configuring the Radio Transmitter
The FlySky TH9X is an entry level 9 channel radio transmitter. In mode 2 the throttle stick is on the left. To match the connections made in the earlier step, the transmitter needs to be configured to indicate what stick controls what function. Use the UP, DOWN, +, - arrow keys and MENU, EXIT select keys to operate the transmitter.
System Setting
For setting the "Type" follow these steps
1. Menu --> System Settings --> Type Sele --> ACRO
Press MENU to confirm. EXIT twice to return to home screen.
For setting the "Mode" follow these steps
1. Menu --> System Settings --> Modevat --> PPM
Press MENU to confirm. EXIT twice to return to home screen.
For setting the "Stick set" follow these steps
1. Menu --> System Settings --> Stick Set --> MODE 2
Press MENU to confirm.
2. When asked about "Thro Reverse" press Exit.
EXIT twice to return to home screen.
Function Setting
For setting the "E.POINT"
1. Menu --> Func Settings --> E.POINT --> THR
2. Move the Throttle stick down and press "+" till the value becomes 120%.
3. Move the Throttle stick up and press "+" till the value becomes 120%.
Leave all other values at 100%.
Press MENU to save and EXIT twice to return to home screen.
For setting the AUX-CH
Channels 1-4 are used for Roll, Pitch, Throttle and Yaw. The other 5 channels can be assigned to different switches and Pots on the remote. APM provides various flight modes as mentioned here. We will set 2 flight modes "Stabilize Mode" and "Altitude Hold Mode" as these are the basic recommended once using the GEAR switch. Other and more than 2 flight modes can be set using the Pots which provides more range and flexibility to provide a value.
1. Menu --> Func Settings --> AUX-CH --> CH5
2. Set CH5 to GEAR using '+' '-'. Press MENU to save and EXIT twice to return to home screen.
P.S. Most transmitters provide a 3 position switch but you can find instructions here for setting up a 6-position flight mode switch which allows you to set and switch additional modes on APM.
Step 22: Setting Up Mission Planner
Mission planner is the GUI used to configure the APM board. The download and install instructions are given here.
Start Mission Planner, connect the APM board to the computer using a Micro USB cable. Wait for the the drivers to be detected and COM port to be assigned. You can check the assigned COM port through Device Manager in Windows based system. On the top right corner of the planner, select appropriate COM port, set the Baud rate to 115200 and click connect. The APM board will connect and load various parameters.
1. On the "Initial Setup screen", select "APM Copter V 3.x.x Quad" and wait for it to download and install the firmware.
2. Once the firmware is loaded, select the "Wizard" option from the left. This will open a new window and guide you to perform the initial setup.
3.Once in the wizard follow the series of images to make the setting in each step.
Step 23: Monitoring Using 3DR Radio Telemetry
You can perform in flight monitoring and issue certain commands using the Radio Telemetry also known as the MAVLink. MAVLink enables remote sensing connection over a wireless channel.The receiver has a male USB output on its end. Connect the receiver and wait for Windows to search for drivers. If not, then drivers can be downloaded from here.
Open device manager to check the COM port assigned to the receiver. Start Mission Planner and select appropriate COM port on the top right corner. Click connect.
Step 24: Checking Motor Rotation Direction and Connecting the Propellers
As shown in the diagram, motor 1 and 2 should rotate in counter-clockwise direction.
Motor 3 and 4 should rotate in clockwise direction. Arm the APM board and push the throttle stick just enough for the motors to start. Check the direction of rotation. If any motor is rotating in opposite direction, simply switch any two connections between the Motor and ESC.
The last step of finishing this build is to connect the propellers.
Tools required
- Allen key
The pair of propellers come with a set of 4 adapter rings which are used to fit the propeller perfectly in the motor shaft. Before twisting the ring out of the package, insert the ring in the propeller and check which one of them fits perfectly. Twist that ring out of the package and insert it on the back side of the propeller(The side which doesn't have anything written on it). The ring will fit tightly. Do this for all the four propellers.
To attach the propellers, place the propellers (written side facing up) on the motor shaft, insert the propeller press fit ring upside-down and screw the propeller saver nut tightly using the Allen key.
On motors 1 and 2 attach the propellers labelled 11x4.7. These are the counter clockwise rotating propellers.
On motor 3 and 4 attach the propellers labelled 11x4.7R. These are the clockwise rotating propellers.
Step 25: Preflight Checklist and Warnings
- Motor propellers are attached correctly and secure.
- Batteries of both the Radio transmitter and Quadcopter are charged.
- All the antennas are facing in the correct direction.
- All mechanical linkages and connections such as nut bolts and screws are proper.
- Landing gears are attached tightly.
- APM, GPS and compass module are facing in correct direction(Forward).
- The polarity of all connections is correct and the pins are in appropriate slots.
- All the cable ties fittings are secure.
- The accelerometer, compass/mag are calibrated.
- Ensure there is no electrical interference with the compass/mag.
- On the Radio transmitter all the sticks, switches and pots are in the default positions.
- Ensure radio signal reception is good and responsive.
- Ensure Failsafes are programmed correctly.
Checklist
Warnings
- Ensure you are not flying in or around a no flying zone.
- Check your country's regulations in respect to operating of Unmanned Aerial Vehicles.
- Don't go near the quadcopter when the motors are spinning.
- Do not fly high in populated spaces. There are chances of Flyaways which can cause harm to person or property.
- Please adhere to the buzzer warning and land the copter to check for any problems.
- If you are not using FPV(first person view), do not let the quadcopter out of your sight when flying.
- Make sure you fly within the range of the antennas.
- Do not fly in rainy/snow conditions.
- Do not fly at night or in areas with low illumination.
- Do not invade people's/animals privacy.
- Be a responsible pilot and fly safe.
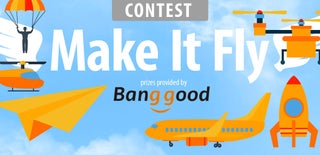
Participated in the
Make It Fly Contest 2016