Introduction: Autonomous R/C Tonka Truck With Head Tracking for FPV (Tonka Summit Build)
With some work , you'll be able to modify a classic, pressed steel, 1970's/1980's Tonka truck to fit on a remote controlled Traxxas Summit to make a scale looking monster truck to go exploring in. Not only that, you'll be able to drive as if you were in the driver's seat. It's not quite the same as going out in the real truck but it's a whole lot less expensive and can go just about anywhere you want and since it's scale, you can get the same sort of videos too!
This requires obtaining a HAM radio license or you can get by without a license and just drive it line of sight and enjoy the video later. Please abide by your local regulations regarding video transmission.
This instructable will go over how to modify a classic Tonka truck to fit on top of a Traxxas Summit. Additional components will be added to allow the camera to pan and tilt so you can look around and see your surroundings, much like you would if you were in a real truck. For added realism, you can use a GI Joe and Barbie doll to drive your truck all with a moving steering wheel.
The video below give you an idea of what you can expect.
Keep going to learn more!
Step 1: Parts / Tools You'll Need
As a note to avoid confusion with some of the pictures, I have made several versions of this truck and have pictures from all the builds so while the trucks may be different colors or different top styles, the actual modifications to the underlying body will be the same.
If you want a really basic setup, you'll need just a few things to buy:
1:10 Scale Traxxas Summit (DO NOT get the 1:16 scale version)
Pressed Steel Tonka Jeep from e-Bay
GoPro HD Hero or HD Hero 2 Camera (doesn't matter which version)
1x GoPro flat, sticky mount
1x GoPro J-buckle
1x GoPro extension
Just a few notes on the above items for however deep you go into the build. DO NOT get the 1:16 scale version as that is way too small. Yes, it's cheaper and a Summit but it won't work for this build.
When you look up the truck on e-Bay, use "pressed steel tonka bronco jeep" and you'll find it. Depending on the condition of the truck, prices will range from $25 shipped to $100+ for the really good condition trucks. If you're lucky, you can find one cheaper. If you're able to find a truck with the rack and gas can, that can add to the realism and it also makes for a good place to put the video transmission gear if you get your HAM radio license and go that far.
If you're making the really basic version, the GoPro Hero 3 will work fine too.
If you want to go all in, here are some more items you'll want:
7-8 channel radio system (I highly recommend the Futaba 9C if you can find it but the 2.4 GHz Futaba 8FG is fine)
1x Castle External BEC
1x Hitec HS-81 Servo
1x Futaba S3004 Servo
1x Hitec HS-55 Servo
1x Servo City Servo Blocks (Futaba version)
1x Servo Stretcher
1x 3/16" Servo to Shaft Coupler (Hitec version)
3x Servo Y-Harnesses (Futaba style, not Gangnam style)
4x Servo extensions (Futaba style and you'll possibly want more than 4 if you add more accessories later on)
1x Traxxas T-lock for differentials (If you have a 27 MHz radio Summit, it has one. All the 2.4 GHz stuff does not.)
1x Traxxas P2 Rockers
1x 4"x2"x1" project box
1x Dubro EZ Connector
1x Servo Reverser
2x Blind spot mirrors
1x GI Joe with Kung Fu Grip (e-Bay)
1x Barbie of your choice
1x Large zip tie
2x Thin, long zip ties
2x 6-32 3/8" screws
2x 4-40 1/2" screws and nuts, plus plastic spacers that go around the screw
1x 3/16" 2" long hex bolt (get lengths), fender washer, and lock nut
4-8x Large hitch pins
Piano wire
Hard foam to cut into small strips
Flat aluminum 3/4" x 1/8"
Double sided tape
Electrical tape
Masking tape
Sharpie
Tools
Drill with a selection of bits
Dremel tool
Square file
High-speed cut-off tool
Vice (not required but it makes things much easier)
Pliers
Phillips screwdriver
Flathead screwdriver
S2 size square screwdriver bit
Blue Loctite
Hobby knife
As a safety note, you should always wear safety protection when you work with any sort of tool, especially when doing this project. The cut-off wheel, especially, puts off a whole lot of sparks and you want, at a minimum, eye and ear protection. I would highly recommend eye protection, hearing protection, and while using the Dremel to cut away the plastic, a filtering mask of some sort as the fumes are pretty strong at times. If you need a parent's help, please get their help! It would actually be an excellent project to do together!
Step 2: Body Preparation
Once you have your Tonka truck, you need to do some work on the underside to make it fit on the top of the Summit. You'll need to cut out the metal bottom and then drill some holes into the front end and back end. After the holes are drilled, you need to square the holes out with a square file so they match the body posts of the Summit. This is done so you can quickly and easily change the body out if you want. If you have a Dremel, it will dramatically speed up the process but you can do it with the file too as I did for my first. The Summit body posts you'll use are made of excellent plastic that don't break so they are perfect for the job.
There's a lot of text here but it's mainly because when I did my first build, I had a lot of questions. If you're going to cut the bottom out, as I would recommend, then you can probably do most of it by looking at the pictures but the instructions here will give you a good overview of how and why some things are done. Use it how you would like!
First, take off the wheels. Some models have a wing nut type device that make it really easy to remove. Some don't and you have to cut the axle with a Dremel to get it off. Whatever works for your model.
Having done a few of these, I would first drill the holes and then cut out the metal bottom of the truck. If you leave the bottom intact, the whole frame is stiff and makes it easier to work with. I did this the other way on my first couple of builds so the pictures where the holes are drilled will show the bottom already removed. It seems trivial but if you cut the bottom out first, then it's harder to keep the metal and plastic lined up properly when drilling the holes, which makes it harder when you need to put the body mounts in.
Use the 1/4" drill bit to drill into the bottom of the truck at the front and the back. The front has the words "Tonka Corp." and "Made In U.S.A." stamped into the metal. At the front, you'll want to make sure the holes are at the top of the "C" in "Corp." and at the top of the letters between "D" and "E" in "made". Center it in the middle of the short, flat side of that area and it should be good. In the off chance it doesn't have the wording, you'll need to make sure the mounting post is centered properly. Don't use a bit larger than 1/4" because if you use a bit with a diameter larger than the mounting post width, it will be loose.
Do the same for the back of the truck. On my trucks, it was generally well centered if the center of the holes were approximately 3 1/8" and 5 7/8" from side edge of the truck but you'll want to make sure where the center point is on your truck and drill appropriately. Also, be sure the center of the holes are further from the back of the truck so you're not drilling through the back wall of the interior. As with cutting wood, measure twice and drill once because you don't want an offset body.
Once the holes are drilled, use the Dremel to turn them in to rectangles. The front holes will be sideways with the long side perpendicular to the front of the truck and the back is rotated 90 degrees. Make absolutely sure you enlarge the holes the proper way by looking at the body posts or you will end up with it wrong. You can use a square file to do this but it takes much longer and will be the most time consuming part of the build. For the final squaring of the corners, you'll definitely need the square file but if you're not too picky, you could get away with not using it. Whichever method you use, take the body posts and try to fit them to make sure you're getting the holes the right size. You want it to barely fit so it doesn't move around. You don't want any play. Some rough sizing measurements are shown in the pictures but again, use the posts you have to make them the right size for you.
Next, you need to grind down part of the body posts so they'll fit in interior section of the truck. Use the picture as a guide and make sure to grind the right side down for the back post. For my first build, I used a pair of wire cutters but a Dremel is faster.
You'll need to shorten the rear body posts unless you don't want to cut the plastic interior shell. I would highly recommend cutting the shell because you can mount the truck lower to the chassis and it will lower the center of gravity. If you just want to mount it on top, then leave the posts as is. If you're going to cut it, cut it so the posts are 3 1/4" long as shown in the picture. The measurement is from the bottom of the post to the bottom of the top cross bar. You may want to hold off cutting this down until after you are ready to dry fit it on the truck but it's up to you.
Once the holes are squared out, you'll need to get the hood of the truck off so you can install the front body post. This was the hardest part of the build. There are holes at the front of the truck on the bottom where you can see a small tab through the hole. You have to straighten that out however you can. I tried with pliers and that worked out but was a lot of work. You have to do what you can to get it straight enough on both tabs so the hood can open. It hinges up like a normal vehicle hood when you finally get it open. If anyone comes up with an easier way to do this, please let me know in the comments. I would love to know how to make this easier.
At this point, you have two options. You can be done with this step and have a body that is high off the truck or you can continue on and have a body that sits just over the chassis. The advantage of not continuing is it's faster and less work but it's a really high center of gravity if you have it up that high to clear the motor. It also won't look nearly as realistic as well. The advantage of continuing is it sits lower, looks better (in my opinion), but it definitely more work. It's up to you on how you want to proceed. I would highly recommend cutting the bottom out.
Once the hood is off, you need to take the top of the truck off. This is done by unscrewing the four screws at the bottom of the truck. On some models, these were rivets but the three I have seen so far didn't have them so hopefully you'll be lucky. If not, you'll need to drill it out and then get a screw to hold the top on.
With the top off, take the dashboard and the plastic interior out as we don't want to cut into that as we remove the undercarriage.
To remove the undercarriage, I used a $20 high-speed cut-off wheel from Harbor Freight for the job. I used a Dremel the first time as I didn't have this cut-off wheel and it took a while and I went through a lot of discs so use the right tool for it and be done with it in a couple of minutes, not half an hour. On the back of the truck, cut it past the metal line you can see on the inside of the truck where there is a layer of metal. When you make this cut, the metal with the Tonka name will come off but hold onto it because it will help keep it stiff in the back. At the front, you'll want about an inch of the slanted metal. After you make the cut, the bottom will still be connected on the sides. You don't need to cut the sides. There are six tabs on the inside that can be lifted up using a screwdriver. Lift those up, turn it over, and then you'll see two rivets on the bottom that need to be drilled. Once you drill those out, the bottom should fall out.
Once the cuts are done, flip the truck over, install the plastic interior, and put the body posts in. The back should slide right in and if you did the cuts right, it should be done. The front will be harder. The body mount has to fit in between the plastic interior and the metal frame. It can be a tight fit and can cause some fitting issues when you try to put the top back on. To make it go as smoothly as possible, make sure the posts are ground down as best as possible to make it thin enough to fit in the small space. It will work. Trust me, I've done it on three trucks already. You can use 4 hitch pins to hold the posts in place. Be sure to put the dashboard in and then the top back on so it holds everything together. You'll need it in this state so you can do a test fit after the next step.
You'll also want to drill holes in the plastic near the back of the seats for the zip tie seat belts. Ideally, you will have long, thin zip ties that will go around the bottom of the chair and Joe/Barbie but if you don't, then you can use two and string them together to get the length you need. Make sure to drill the hole to just larger than the zip tie.
They say pictures are worth a thousand words. If that's the case, then I'll save myself six thousand words with these next pictures. For this next part, you'll have to cut out the bottom of the plastic interior so the body fits over the motor and transmission. You'll get the basic idea of how it's supposed to be cut from the pictures. I tried to take as many measurements as possible to make it easy to cut and not have to keep fitting it on the truck but it's not going to be exact for your truck so use it as a guide. The best way to get the cuts made are with your Dremel. If you don't have one and made it this far, BRAVO! It's a lot of work and you can probably drill enough holes in the chassis and then file down the sides to get the proper fit but it'll take some more time.If you don't have a Dremel, I would highly recommend one.
Follow the instructions on each picture by hovering over the highlighted areas and it will give you pointers. I would use the measurements to draw an outline on the plastic and then make the cuts. It'll go faster that way. Once you're done, you can do a test fit to see how well it lines up. If it's resting on a part of the motor area, just make the modifications you need to get it how you like and then you're finished with what I consider the hardest part!
If you're doing the really simple setup, you can skip to the beginning of Step 4.
Step 3: Steering Wheel Modification
Now for the moving steering wheel. This step isn't necessarily required but if you want a more realistic truck, go through this step. If not, it's not a big deal if you skip it.
You'll need to remove the steering wheel from the dashboard. I did it by holding onto one end with a pair of pliers and a vice to keep the rivet from moving when you have to drill the rivet. Just a bit big enough to get the edge of the rivet but not drill into the steering wheel itself. Using a vice will make it much easier but it's also possible with a Dremel and a pair of pliers.
Once you have drilled the rivet, the steering wheel should slide out. Use the 3/16" hex bolt to act as your steering column. On the back side of the dashboard, you'll want to put a washer there and then use a locknut behind it as shown in the picture. Tighten the locknut until you get close to no play in the steering wheel. You'll also want to leave it loose enough that the steering wheel will turn freely. If you don't mind a more permanent setup, you can just epoxy the 3/16" hex to the steering wheel instead as it's much easier but I finally decided I wanted the ability to change things up in the future if need be and this has worked just fine in my builds.
To connect the steering wheel to a servo, I used a servo shaft coupler from ServoCity along with a Hitec HS-81 servo. Install the shaft coupler on the spline of the servo and then tighten the coupler onto the 3/16" bolt. You'll want there to be a small gap between the coupler and the nut but if the bolt you bought is too long, you'll want to cut it down some. It's a tight fit with the coupler but that's a good thing.
Once you get that done, then you'll need to anchor the servo to the back of the dashboard. I did it with aluminum strip and double sided tape. Again, a picture is worth a thousand words so I'll save myself three thousand more but will explain a couple of things. When you put one of the pieces of aluminum down, dry fit it and then stick the short side to the servo first. Once you're confident in where the metal needs to go, stick it on the servo first, rotate the entire servo with the aluminum stuck to it, and then peel the backing off the tape that goes to the dashboard and rotate it so the metal is stuck to the dashboard. On the other side, you don't have that luxury because it's fixed at this point. Again, do a dry fit and then peel the backing off both pieces and stick it on the servo first with a slight bend in the metal and then press it firmly against the dashboard. It should hold very well.
One more thing. See the notches on the metal on the vertical portion connected to the servo? You'll want to make sure that is cut out beforehand because the servo shaft coupler will hit the metal, limiting the travel of the steering wheel rotation.
At this point, you can put the truck back together and sit your GI Joe in the truck to see what it'll look like. We'll get to connecting the steering servo up later.
This isn't really related to the steering wheel but I couldn't find a better place to put it so here I go! You'll definitely want to know what's going on behind you while you drive. The easiest way to do so is to put side mirrors on the truck. If you use the blind spot mirrors from AutoZone, the installation is fairly straightforward. Take a couple of 3.5" long pieces of the aluminum you have left over from making the steering wheel servo support. Drill a large hole in one end big enough to fit the body post of the top of the truck. It will get sandwiched in between the top and the plastic interior. Then grind down the ends to the same form as the mirror profile. Use double sided tape to hold the mirror on the aluminum. When you tighten the top down, it'll be a bit difficult to get it all together but it will hold those mirrors in place very well.
Move on to the next step! We're getting closer!
Step 4: Pan/Tilt Setup and Mounting
If you skipped to this point because you want the simple setup, take your GoPro and use a flat, sticky mount and put it on the back of the driver's seat. Then using a J-buckle mount and a single extension, you can attach the GoPro case to it and have your camera in the driver's seat to drive around and take video. I never did this so I don't have a picture of it but it's simple enough to do and you should be done!
For the rest of you, this is the part I was originally dreading since I had never made a pan/tilt bracket before. Making the pan/tilt for the camera gives the appearance of Joe moving his head as he drives in the videos. The pan is easy to do. The tilt, I hadn't seen a good way to do without purchasing an expensive pan/tilt system or having to do a lot of custom work. I opted for the latter as I can't justify buying something that expensive when I can make it on my own with some effort.
The ServoBlocks are, in my opinion, the best option for a pan system on this truck and you'll see why. They go together really well and work with standard size Hitec or Futaba servos. If you have a Hitec servo, you'll want to make sure to buy the Hitec version of the ServoBlocks instead of what I have in the list of materials. I had a few spare Futaba S3004 servos from a while ago so I used that with the ServoBlocks.
I'll explain a few things here and then let the pictures do the rest of the work with notes on each picture.
Depending on the truck you have, you'll either have a roll cage type top or you'll have more of a Bronco type, closed top. If you have the roll bar top, you can follow most of the pictures as shown without much issue. If you have the Bronco type top, then you'll need to put the tilt servo on the right side of the project box and make the appropriate holes in the metal as the servo will hit the side of the truck if it's on the left side.
When you put the tilt assembly on the ServoBlocks, you'll want to make sure that the spline on the servo is on the right side if you're looking at the pan/tilt from behind.
If you're just going to do a pan setup, then that will be really easy. Just glue or screw down the project box to the top of the ServoBlock and you're done. If you want the ability to look up or down, then it's much more work. What you need to do is take that flat piece of aluminum and cut it to the right length to fit around the small project box. Be sure you cut it long enough to leave enough space between the box and aluminum so you can tilt down a little. When you do the measurement, you'll want to make sure you leave enough space for the 6-32 screw heads when the box is tilted up a little bit. Again, if you have the roll bar top, that spacing doesn't really matter as much as you can have more space between the box and aluminum. If you have the Bronco top, then you really need to be careful in your measurements here. See the sixth and also the second to last picture to get an idea of what I mean. You'll have to make a modification to the bottom of box by cutting out space to make sure it clears the screw heads. If you make it taller instead to clear the heads without having to modify the box, then the top of the box will hit the top of the truck and you won't be able to tilt up or down. It's a tight fit but it'll work fine.
When you get the aluminum cut to the proper length, you'll need to drill 5 holes in the aluminum. Two are used to mount the bracket to the ServoBlocks hub. The hub is already threaded for 6-32 screws so make the hole about that size and make sure they line up with the hub. Once you have that done, it'll mount onto the pan system pretty easily. You'll also need two holes on opposing sides for the project box to mount it so it can rotate without resistance. Finally, you need a hole to put the pushrod in so you can tilt the box with a servo. This hole, ideally, should be on the right side of the tilt assembly.
Follow the notes in the rest of the pictures and you should be able to get it made. It's easier to explain on each picture.
Once you get it installed, you'll want to get Joe in place. To prepare Joe, you'll have to remove his head unfortunately. If you bought the Kung-Fu grip version, there's a hook connected to the head that holds tension on the rest of his movable arms and legs. You'll need to hook it on his chest to keep everything tight. If you have a regular Joe, then it's easier to deal with for that part. Once his head is off, you'll just glue his left hand to the steering wheel and you'll have the doll driving the truck!
To keep Joe and/or Barbie safe in their travels, you'll need to hold them in place. Remember in step 3 where you made holes in the plastic interior for the seat belts? Well, this is where you should put them in place. It's especially important for Joe because he needs to be sitting low enough that the tilt bracket clears the top of his chest when the assembly pans left and right.
You're off to the next step!
Step 5: Connections and Mounting
Before you mount the top onto the truck, you're going to want to swap the front and rear springs. The truck comes stock with stiffer springs on the front. This truck is going to be quite heavy once you mount the Tonka body on and you want more stiffness in the back. When you go to swap the springs out, you're also going to want to change the rockers out from the Long Travel version that is stock to the Progressive 2 (P2) version. This stiffens the suspension up considerably. If you were driving it stock, it would be too stiff (although perfect for jumps) but with the extra weight of the body, it's perfect. Swap them out and make sure you put the red rings in between the metal bar and bar ends. Instructions are also provided with the P2 rockers.
You'll also want to remove the stock waterproof receiver box and take the servo cables out if you're planning on the more complicated setup. If you're doing the simpler version without the GI Joe or movable steering wheel, then leave it as is. When you remove each cable, mark each with the channel number it was plugged in to so you know the function of the servo. Masking tape and a Sharpie work quite well. The servo cables and the channels they go to are as follows:
1 - Steering servo (there are two of them)
2 - ESC (throttle)
3 - Gear shift servo
4 - Front differential servo
5 - Rear differential servo
Depending on if you bought the servo extensions and Y cables I linked to or not, you may have different colored wiring on your cables than what you see on your servo cables. This is just a lack of a common standard between some brands. In general, the ground wire is black but can also be brown depending on the brand. Red is always power. The signal wire can be white, yellow, or orange. When you make all your servo connections, just make sure black is going to black/brown and everything else should line up just fine. For a more detailed explanation, you can read up on the types of connections at ServoCity.
For the connections, you'll need to take one servo Y cable and plug both steering servos into the Y. Then you'll need to take another Y cable and plug one differential servo into it and then the servo reverser into the other part of the Y cable. Then plug the other differential servo into the servo reverser. We'll have them both lock at the same time. If you want them controlled separately and have a spare channel, you can do so without any issue, but that is not how it will work using this setup. Depending on where you decide to mount your receiver, you may need servo extensions. Put it on the single end of the Y cable to save on having to use too many extensions.
Using the Traxxas T-lock module, you'll want to plug in the shift servo (labeled channel 3) into the 'A' port of the module and then the Y cable end that the differential servos are connected to goes to the 'B' port of the module. Then use a servo extension on the other end so you'll have enough reach to get to the receiver. What this part effectively does is it takes the signal from the transmitter and when the channel reaches a certain threshold, it shifts the truck from high gear to low gear. Then when we to flip the switch the rest of the way, it locks the differentials at the same time. It's an easy way to get away with what used to be controlled by three channels with just one. You can't run in high gear with the differentials locked and you can independently lock the front or rear differentials but it's a small trade-off. Running in high gear with the diffs locked isn't recommended anyway as you can blow them out and for general purposes, locking both diffs at the same time is just fine.
The steering servos are connected to a Y cable and the single end of the cable needs to go to another Y cable. The servo used for moving the steering wheel will go into the other side of the second Y cable. You'll have three servos running off a single channel using this setup. When you turn the wheels, the steering wheel will now follow the wheels.
For the ESC cable, you will need to remove the red wire from the servo plug. Using a hobby knife, lift up the tab for the red wire and pull the wire out. I usually use black electrical tape to cover the pin itself so I can always use it again later. Some people just cut the red wire but it seems a little wasteful. What this does is it eliminates use of the built-in BEC on the ESC. For running 5 servos on a stock Summit, it works just fine but with the steering wheel and pan/tilt system, you are running 8 servos and you could possibly overheat the stock BEC. You'll use an external BEC instead that will supply more than adequate power to your servos.
Now you're ready to mount the body on the truck. If you followed the instructions up to this point and did some test fits, then it should go right on. I would lay the truck body on it's side on the wheels while you run all the servo cables through the hole on the vertical wall on the back of the truck that you should have made in Step 2, picture 12. Once the connections are through that hole, then roll the body onto the truck. Be sure to put the body mount posts into the proper location. You can use the stock body mount pins to hold it in place or use bigger hitch pins to be able to quickly take the body off. Either way works. I used smaller hitch pins (use the body pins from the stock body) to hold the body in place while I used the original body post pins to secure the body to the chassis.
Once the body has been mounted, you can now connect all the servos to your receiver. Assuming you are using a Futaba radio and receiver, the Y cable with the three steering servos on it will connect to Channel 1. If you are using a Spektrum system or one that has words instead of numbers, connect it to AILE (for aileron). For the ESC, you will need to connect it to Channel 2 or ELEV (elevator). These two channels are on the right stick of a standard radio and the reasoning for putting the ESC on the elevator stick is that for the ESC to properly calibrate, you have to have a stick that self-centers. If you have owned a Traxxas vehicle, you'll need to make sure to re-calibrate the ESC as stated in the ESC manual so it reads the PWM values from the receiver properly for operation.
The tilt servo needs a servo extension on it and will connect to Channel 5 or GEAR. The pan servo will connect to the servo stretcher and then the other end of the servo stretcher will connect to Channel 4 or RUDD (rudder). Your pan will be controlled with your left stick. The pan will center properly being on channel 4. Tilt will be controlled by the slider on the left side of the radio. It will stay at wherever you leave the slider but will also let you move it as you wish. Convenient huh?
The reason we use a servo stretcher on the pan here is that the standard PWM signals from the receiver only move the servo 45 to the left or right from center for 90 degrees of travel. This is okay for most things but for this application, you want to be able to see 90 degrees to the left and right so you can "look both ways" before you cross a street. You'll want to adjust the servo stretcher according to the manual that comes with it. I'm not going to reinvent the wheel and write that all out here in my own words as theirs is good enough!
The T-lock module will likely need a servo extension and will go in to Channel 7 or AUX 2 (auxiliary 2). I left Channel 3 and 6 (THRO and Aux 1) open for other accessories in the future as it's always fun to install a switch to turn the lights on/off, install a car horn, or have volume for a speaker system.
Finally, you'll need to connect your UBEC into the Batt/Bind/Data port to give plenty of power to all the servos as the stock ESC cannot supply all the current it needs for so many servos. The other end of the UBEC will connect to the balance port of the video transmitter battery.
At this point, you can proceed to the next step!
Step 6: Radio Setup and Use Plus Head Tracking!
Please refer to the pictures for exact radio settings. I'll explain here what each does but the actual settings will be in the pictures. I'll explain in sets of two images but if it's annoying, let me know in the comments and I can change it up. It just made more sense for me as I wrote this.
The first two images are for controlling maximum throttle settings. With switch B up (forward away from your body), you get full throttle. With it down, it cuts throttle to 40%, handy for keeping yourself from driving too fast. If you have a spare 3 position switch (switch C in this build), you can actually get three different throttle settings!
The next two images are the end point and sub-trim settings. The end point just changes the travel of your servos. For example, the camera pan servo moves 45 degrees to the left and right for a total of 90 degrees. When the end point setting is at 100/100, you get the 90 degrees left and right. If you lower the end point to 50/50, that changes the movement of the servo so it only travels 45 degrees left and right for a total of 90 degrees of motion.
The sub-trim is subtle. The trim switches on the radio allow you to change the trim as you fly/drive. Typically, if it requires more than a few clicks of trim, then what you do is see where the servo horn/arm is, set the trim back to 0, and then take the horn/arm off and try and manually put it where it should be. Once it’s as close as it can be, then you adjust the sub-trim so it’s where it should be. Then you have full trim range and should be back at 0 trim.
The next two images are for reversing servos and trimming. For the setup using the servos on the truck, all the reverse settings should be set to normal. This will change if you have to replace a servo and you do so with one that is not identical to the one you are removing. In some cases, the servo will move in the opposite direction compared to the previous one. That happens because of how the manufacturer makes the servo. Change the setting here. If you use the gear I have outlined, these settings should be correct, although after three different trucks, there could be a setting I changed without realizing.
The trim screen allows you to see the current trims on the radio. In this case, the number 4 signifies how much each click will move the trim value. The number in ( ) is the number to the left multiplied by how many clicks you made. In this case, I had to give it three clicks to the left to get my truck to drive straight. Remember, Trim and Sub-Trim are similar but two different settings.
The next two images are for the failsafe settings and channel switch assignments. If you ever run out of range or turn off the radio, this is the default value all the channels will go to. The most important settings here are the ones for the throttle. Make sure the elevator (channel 2) failsafe is set properly with the stick in the center position. You don't want it to continue going if you lose signal!
The Aux-Ch menu allows you to select what switch, knob, or slider controls each channel from 5 to 9. If you start messing with this while the truck is on, you could potentially cause some damage as you’ll be scrolling through different switches if you decide to change it. Each one you change is in a different position so if you scroll through, the servo on that channel could bind or have issues. It’s not guaranteed but just be careful and make sure the truck is off. For this build, channel 5 and 7 are the only ones that have to be set as shown and the others can be different.
The final two images are the parameter screen and trainer menu. The parameter screen is for basic radio setup if you want airplane or heli programming. For ground vehicles, just use the airplane (acrobatic) setting.
The trainer menu allows signals from devices connected to the trainer port on the back of the radio to control certain aspects of the control. If you use a headtracker to control pan/tilt, then you would want channel 4 and 5 to be allowed to be controlled by an external device that is plugged in to the trainer port. You allow those signals to pass through by pulling switch F towards your body. If you do decide to use a headtracker, I recommend this one from Flytron.
Take note of a few driving tips below.
To drive the truck, you use the right stick. Moving it up moves forward. Moving it backwards will engage the brake. The Traxxas ESC only allows you to go in reverse after you brake and have stopped. Basically, if you want to jam it in reverse, you need to move the stick backwards quickly twice but it's not good for the transmission. The ESC does not prevent going from backwards to forwards. Be very careful doing that because it's very easy to pop a wheelie and that will end up with the truck upside down. I have also found that with the stiffer suspension, if you are on a high traction surface, like asphalt, if you give it full throttle from a stop with switch B in the UP position, you can pop a wheelie as well so be careful. Use switch B to lower the throttle rate if you need to. Before you take it out, be sure to calibrate the ESC to the new radio. Instructions for calibrations can be found here at the Traxxas website.
With the switch G in the position away from you (towards the ground), the truck should be in high gear. When you move the switch to the middle position, the truck shifts into low gear. Never switch gearing while moving. You can if you want but after a few times, you'll likely mess up the transmission. You can always fix the parts but it requires a lot of dis-assembly if you haven't noticed! If it doesn't change gears upon shifting, move forward or backwards just a blip and it should shift.
When you move the switch to the position closest to you, it will stay in low gear and will lock the front and rear differentials at the same time. Again, never switch while you are moving. Same as the transmission, you can sometimes but you'll blow them out if you do it while moving much. This is only to be used when you get stuck or can't quite get over something. All 4 tires will move at the same speed. As soon as you are over an obstacle, unlock them as your turning radius is horrible otherwise and there is a lot of strain on the drive train.
I'm adding head tracking here because the site was having issues with me adding steps so here is the section on head tracking!
The head tracker for this step is the DT-3K from www.flytron.com. The direct link is here. All the instructions are for the Futaba 9C that is a part of this Instructable. Some of the connectors may be different for your radio. Your radio must have a supported trainer plug on the back.
First, plug in the head tracker to the back of the 9C radio. This should be done before you power on the transmitter. To get it set up for the first time, you'll need to hold the button down when turning the radio on. After you let go, the LED will blink 10 times very quickly.
Then you'll need to hold the button down and the LED will start to blink. Keep holding it down until the it has blinked 4 times and let go. It should blink 10 times fast again to show it accepted the setting. You basically programmed it to say that the pan channel is on channel 4 and tilt is 5. If you have it on two other channels, let go when it gets to your pan servo channel. You'll have to have your connections such that the pan servo is the channel number that is one lower than your tilt servo (i.e., pan on 4, tilt on 5).
Then hold the button down again until it blinks twice and let go. It'll blink 10 times fast again. This setting basically inserts the signals it needs for the Futaba 9C radio. If you have a different radio, be sure to consult the manual for the head tracker for your particular setup.
The next two parts are to determine the proper direction of movement for the pan/tilt. For my setup, I have the wire of the head tracker facing forward. Basically, the box sits on my head and the cable comes out to the front. With this setup and the servos I have, you'll want to hold the button down and let go when it blinks twice. Then hold the button down again and let go after the first blink. That will set the proper servo direction movement for the pan servo first and then the tilt servo second. If it doesn't move the way you need it to, try letting go after 1 blink for pan or 2 blinks for tilt. Just a warning! If you need to re-do it, you have to start over by turning off the radio and starting programming back up again. Yes, it's a pain but it's worth it once you get it working.
Now that your head tracker is set up, you can use it by holding the trainer switch on the radio and doing the calibration procedure. This assumes you did the radio setup properly in the above steps when you set everything up as shown in the pictures.
To calibrate, you'll need to hold the trainer switch on your radio in the on position. While facing north or south, push the button on the head tracker. Then move the head tracker to the left, right, then up and down like you will be when you use it. That sets the minimum and maximum positions on the sensors in the tracker. Ideally, you'll want to do that with the tracker mounted on your hat. Then press the button one more time after you did those steps and you should be good to go.
To use the head tracker, you must be facing magnetic north or south. Although this can be considered a downside to other trackers, this tracker is very reliable and I really like it and adds to the realism.
The next step in this Instructable is only for those that want to drive first person view (FPV). You don't need to do that using what you've done up to this point but that's kind of the point of the build. Getting a HAM radio license can be time consuming depending on your previous electronics knowledge but it's a useful skill to have. If you want to go all in, then continue on to the next step! If you don't have a license, then get on out and make some videos!
Step 7: Wireless Video Setup
To legally use the truck with wireless video equipment in the US, you need to be licensed as a HAM radio operator. The transmitted video should have your call sign on it at the beginning and end of transmission and should also show every 10 minutes if you are transmitting for a long time. You can do that using an on-screen display (OSD) or by writing it somewhere visible to the camera. That's just the start of some basic things you need to know. You should get your license as it gives an appreciation for that side of the hobby. If you are outside the US, you'll need to find out the regulations regarding transmission at various frequencies. You will be responsible for proper use of wireless equipment.
The basic equipment you need for this step are:
1x GoPro Video/Audio Cable
1x Transmitter Cable
1x Video Jumper Cable
1x Audio Jumper Cable
2x Batteries
1x A/V Cables
1x 1.3 GHz Video Transmitter
1x 1.3 GHz Video Receiver
1x Power Cable
2x Low Voltage Alarm
I put this list of items above on this page instead of the first parts listing because there is no need to buy any of this gear if you don't get a HAM license.
Once you have all your gear from above together, setup is fairly straightforward.
On the receiver side, all you have to do is connect the RCA cables from the receiver to a TV or video goggles, screw on the antenna, and plug in the power cable. After you plug the battery into the power cable, the receiver is ready to go. Just make sure you watch the polarity or you'll blow the receiver out. Remember, red on red, black on black! Don't leave it plugged in for too long though. Using the above battery, you'll probably get about 45 minutes out of it but I recommend plugging the low voltage alarm into the battery balance port to monitor the voltage. Once it gets under 10.0 V, you should recharge the battery.
The transmitter side is a little more complicated and the pictures will do more to explain than I can!
I prefer mounting the video transmitter in the back where the gas can goes but you can install it on the top for better range. It just looks better mounted behind the truck in my opinion.
Finally, use a large zip tie to hold the GoPro in the pan/tilt mount. Connect the audio/video connector into the GoPro. At this point, turn on the GoPro, plug the battery into the transmitter, hit record, and GO DRIVE!
Step 8: Adding an Autopilot
This is an addition to the truck to make it drive on its own. It's useful mainly if you're in an open field and if you're trying to cover a lot of ground, it's kind of nice to be able to let the truck go on its own while you look around.
For this modification, you'll need the following items.
1x 3DR APM 2.5+
1x 3DR Radio Telemetry Kit (add-on to above)
1x GPS Module (add-on for $20 above or get this better one)
3x 8" Male-to-male servo cables (this is a pack of 10)
Velcro
Plexiglass or something thin and flat to make a platform
For the GPS, if you plan on running on the street in front of your house, I would recommend the $90 Ublox GPS over the $20 MediaTek. The MediaTek does okay if you have a clear view of the sky all around but the Ublox is just that much better and for a ground vehicle, it'll be important to have that extra bit of accuracy. I have already run up on the curb multiple times and have had to stop the truck from driving into mailboxes because I don't have the nicer GPS.
To begin, you'll want to take the top off the truck. Now you have a convertible Tonka! Just don't run it like that. During my testing with the autopilot, I ran into the curb and it flipped backwards and broke my video transmitter antenna. I'm glad my GoPro wasn't installed at the time. If you have the Bronco style top, you need the room to be able to make this modification. If you have the roll bar top, you might be able to get by without taking it off. I don't have a truck like that anymore so I couldn't test it out. Once you're finished, you'll put the top back on to protect everything.
Once you have the top off, you'll want to measure the section in the back and cut a piece of Plexiglass to fit in that area. The measurements for mine were 7 7/16" and 2 3/4". You'll use Velcro on the underside of the sheet to stick the piece on the two back seats of the truck. If you do a little bit of wiring management, you should be able to fit your receiver, UBEC, and wires all underneath in the space between the two seats without issue. It cleans up the previous installation and makes it easier to work with.
Once you have the platform cut out and put down with Velcro after test fitting, remove it and set it aside. We need to remove the servo connections on the receiver for steering and throttle. For a Futaba system, that will be channels 1 and 2. If you labeled everything like I mentioned earlier, it should be easy to find! Set those connectors aside for the moment. Take two of your male-to-male servo cables and plug them in to the receiver where you just removed steering servo and ESC connectors. Then take your other male-to-male cable and plug it in to an open channel that is on a two-position switch. On my installation, it was channel 9 but your setup may be different. Be sure to label the ends that are not plugged in so you know which is for steering, throttle, and mode change. After you label everything, neatly place the receiver back in the space between the two back seats and place the Velcro platform on the seats so you have a place for the autopilot.
At this point, take the male-to-male cable that corresponds to steering and plug it into channel 1 of INPUT. You'll plug the cable for throttle into channel 3 of INPUT and finally, the mode switch cable will go to channel 8 of INPUT.
Remember the servo and ESC cable you moved aside? Plug the servo cable into channel 1 of OUTPUT. Before you plug in the ESC, you'll want to put the power wire back in to the servo connector if you removed it previously. The steering servos without 6 V and the ESC's BEC will provide the power on the output rail. Once you have connected it back up, plug it into channel 3 of OUTPUT.
MUST DO NOW! Remove the jumper from JP1 at this time. The jumper would normally allow the ESC to power the APM and servo(s) but the Traxxas ESC puts out 6 V and it would fry your autopilot board. With the jumper removed, you'll need to supply power to the INPUT and OUTPUT. The OUTPUT is taken care of by the ESC if you followed the instructions in the previous paragraph.
WARNING! If your external BEC was powering all your servos at 6 V, you need to change the setting on the BEC from 6 V to 5 V or you will fry your board! If you used a cheaper Chinese unit, just make sure the jumper is in the 5 V position. If you use the Castle one I linked to in my original BOM, then you'll need to reprogram it to 5 V. If you only have a 6 V BEC, then you'll need to get a 5 V one. Once you make this change, the INPUT should be fine as you should be powering the rest of your servos and APM off the external BEC from the previous steps in this instructable.
PLEASE BE CAREFUL WITH THE VOLTAGES AND FOLLOW THE PREVIOUS PARAGRAPHS!
At this point, plug in the telemetry module and GPS into the APM 2.5+ in their respective ports. Then, you'll put some Velcro on your APM 2.5+ board, on the back of the GPS, and on the back of the telemetry module so they will stay in place. Lay them out so you can get everything on the little platform you made with the brown and white antenna on the GPS pointing up toward the sky. If you are using the Ublox GPS, don't connect the magnetometer sensor connector as the APM 2.5+ has one onboard. If you purchased the APM 2.6, then you will need to plug the magnetometer cable in to the APM and GPS module.
At this point, move to the next section to set up the board itself!
Step 9: Mission Planner and Parameter Settings
This is going to be a basic explanation on how to get things running as well as what settings I used. I'll be sure to point out when you need to make sure to check your settings because it's likely you may be running different servos, a different radio, or just want it a little different. For the most detailed explanation of the mission planner settings and setup, you can go to http://rover.ardupilot.com/wiki/mission-planning/ and get all the information to your heart's content!
Download the Mission Planner (MP) MSI file from http://ardupilot.com/downloads/?category=4 and install the program. This program will be used to load the firmware onto the APM and the main screen can be seen in the first image.
Note: It is only for Windows systems but they are working on a new program that will be cross compatible with Linux and Mac as well as Windows.
You'll want to set up your telemetry radio system. For instructions regarding that, I defer to the proper documentation website as you don't want to mess them up. Here is the link: http://plane.ardupilot.com/wiki/common-using-the-3dr-radio-for-telemetry-with-apm-and-px4/
Once the program has been installed, connect the APM to the computer using the micro USB cable that came with it. Then click on "Pick Previous Firmware" at the bottom right. Click the top one with AR2.42 on it because that is the version that was used for this. I fully intend to upgrade to the newest 2.43 and it has better navigation code but all my parameters so far are for 2.42. Once you have that, the icon for the rover should changed and the text should read "ArduRover v2.42 AR2". Click on it and it will load the firmware to the APM.
When the firmware loads properly, you should connect to the APM through the planner. This can be done either by keeping it plugged in via the USB cable or using the telemetry module and connecting through that. If this is your first time, you'll need to set up the telemetry module first before you can connect with it. Make sure to select the proper COM port at the upper right of the MP, leave the baud rate at 115200, and click connect. At first, it will likely look for MavLink messages and then will start loading up the parameters. The very first time you connect, it will need to format the dataflash on the unit and will take a few minutes. Just let it go and wait. If you see no change after 5-10 minutes, then reboot the APM and it should connect. I had an issue the first time but after a reboot, it worked fine. My other one didn't give me any issues.
Next, load up the parameters from the parameter file attached to this step to get you most of the way there. If you're using the stock Traxxas steering servos and ESC with a Futaba radio and also have the APM mounted sideways with the arrow pointing to the left of the truck, these parameters should get you going quickly. You'll need to calibrate your radio but we'll go through that. Keep on reading though as you'll need to go through each step if you have issues.
To load up the parameters, you need to go to the CONFIG/TUNING tab and then click on the "Full Parameter List" at the left. Then the buttons at the right give you an option to load a file. Be sure to download the parameter file on this step. After you download it, you'll need to change the file extension from .txt to .param. This had to be done so it would upload to the website as it did not accept a .param file. Once loaded, you can peruse the parameters. Once you've explored to your hearts content, then write the parameters to the APM.
Once the parameters are set, be sure to run the radio calibration before you do anything else and set the proper modes on the third channel on your radio. The radio calibration is under the INITIAL SETUP tab. Make sure your ESC is turned off but that your receiver and APM are powered on from your external BEC. Click on "Calibrate Radio" and then move the right stick to all the extremes and then move the switch you have for the mode to get the switch positions.
After you have the radio calibrated, you'll want to set the modes up properly. With the switch in one position, it should show to be in Flight Mode 6, which is MANUAL mode and you'll be able to control the truck as you normally would. When you move the switch, it should change to Flight Mode 1 and that should be set to AUTO.
Finally, you'll want to make sure your compass is set up properly. Under the INITIAL SETUP tab, there is a "MANDATORY HARDWARE" section and under it, the Compass. The only thing you need to do is make sure it is enabled and that the orientation is set to Manual: ROTATION_YAW_180. That setting is if you installed as I did with the arrow pointing to the left of the truck.
Now you're ready to plan waypoints and try and AUTO mission! I'll defer again to the ArduPilot documentation as they do a good job. Here's the link: http://plane.ardupilot.com/wiki/common-planning-a-mission-with-waypoints-and-events/
For general troubleshooting, try these changes as your setup may be slightly different from mine.
If your truck goes backwards in AUTO: Click the Reverse checkbox for throttle in the radio calibration.
If your truck snakes back and forth going to a waypoint: Click the Reverse checkbox for Roll in the radio calibration.
If your truck goes in a different direction than expected, change the compass orientation under mandatory hardware in the initial setup tab. This one is harder to track because of the errors in GPS positioning. If you don't have a good lock sometimes, it'll be off a bit and may seem like it's going the wrong way. You'll have to try a few different orientations but there are only 4 to choose from for YAW that are 90 degrees apart so it should be obvious which is correct very quickly.
Enjoy the view while your autopilot takes you on a drive!
Attachments
Step 10: Further Customization and Videos!
Headtracking so the camera follows your head movement
Remote controlled lights to turn the lights on/off
A switch activated car horn (yes, an actual car horn)
Two-way radio communication
Radio system connected to an iPod shuffle with selectable tracks and volume control
The light switch and radio communication (walkie talkies) are simple enough. Headtracking is easy enough if you know how to read instructions and can program your radio. The car horn and radio system are more complicated and warrant an Instructable by themselves. If you absolutely must have tunes while you drive around, you can get a set of these JBL speakers and put it in the hood of the car, connect a small MP3 player to it, and start it up before you take off. It helps pass the time! Maybe if there is enough interest, I'll do one for each project.
There are so many more things you could do with this truck. I'll let your imagination take over from here! If you do need more inspiration, you can check out the following websites that have been the staple for anyone looking for information about the Tonka Summit.
RCGroups Tonka Summit Thread
Tonka Summit Website
Enjoy these other videos. It's nothing special, just driving around the yard and neighborhood from my house. All video footage is from the GoPro and not the actual, transmitted video. Before anyone asks, that loop I drive is about a quarter of a mile long and the furthest point is roughly 120 meters away from where I was sitting with several houses between me and the truck. It's not very long but it lets me drive around where I want to go in my neighborhood.
Have fun and post any videos you make in the comments!
This is a separate video I made showing this truck as the lead truck driving autonomously while I followed with my other truck. The video turned out kind of weird on the first part as the audio didn't sync properly. All of it is me driving around through the video goggles.
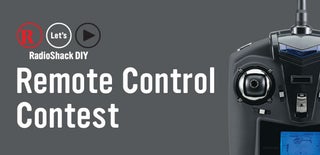
Participated in the
Remote Control Contest

Participated in the
Microcontroller Contest