Introduction: Replacement Feet for Fellowes Stacking Wire Tray
Dearly beloved, we are gathered here today to morn the passing of another Fellows File Organizer... The rubber feet supporting the organizer have succumbed to dry rot and the trays no longer stack. Re-stacking efforts were initiated, but sadly there were no replacement rubber stacking feet available to save the patient...
Until now! Dun, Dun, Dun!
Clear! Get that patient a new set of stacking feet, um, stat!
3D Printed Replacement Foot for Fellowes Stacking Wire Tray
So, yeah, you've probably gathered by now that the rubber feet that come with the Fellows stacking wire trays can dry rot and fail. That wouldn't be a dealbreaker if you could get the feet separately, but Fellowes does not sell just the feet! That means you’re either stuck buying all new file trays or dealing with wire trays that don’t stack well anymore.
Now the trays aren't exactly expensive, but still, throwing out a perfectly good item because one of the rubber feet no longer, um... "feets" anymore feels wrong doesn't it?
This Instructable solves that problem, you can now 3D print all the replacement feet (feets?!) and continue using your file trays when the original rubber feet wear out.
I created this at the request of a family member who’s a teacher and has a lot of papers to keep track of. Hopefully it can help some other people out there (or at least give someone another excuse to play with their 3D printer) 😉
Supplies
This model is confirmed to fit with these trays:
- Front load tray p/n 66112: https://amzn.to/46ardWv (affiliate link)
- Side load tray p/n 62112: https://amzn.to/3Zyp3h8 (affiliate link)
- There may be more part numbers it fits, these are the trays it's been tested on.
1) You will need a 3D printer capable of printing flexible filament.
- I recommend using a direct drive style printer for printing flexible TPU filament. I know TPU can be printed on bowden style 3D printers (ender 3), but it's notoriously more difficult.
- I have printed these on 3 different printers successfully - Ol' Flasy the Flashforge Creator Pro, Peach the Prusa MK3S+ and Bamboozler the Bambu Labs X1C.
2) TPU Filament - I've had good luck with Yoyi brand TPU https://amzn.to/469wWMz (affiliate link)
3) One of the 3D models attached to this step. You have your choice of .stl, .3mf and .stp so pick your favorite flavor.
4) And you'll need a computer to slice the file and get it to the 3D printer.
Step 1: Design
This is a pretty unique shape. There's really no straight sections to pull a good measurement from. So... How's a maker to make it?
Well we're going to sudo cheat, or I mean utilize the full extend of our CAD package.
i.e. - We're going to import an image of the thing we want to make and digitally trace it.
(IE is kinda odd, like this isn't internet explorer, what is it and where did it come from cotton eye Joe? This link from grammarly helped me understand it if you're curious too https://www.grammarly.com/blog/know-your-latin-i-e-vs-e-g/ )
So, in this instance I took a picture of the side profile of the foot since it's the complicated part. It helps a lot to use a contrasting background, in this instance a sheet of paper worked great.
Save that image to the computer, and fire up Fusion 360.
Go to the INSERT tab and choose "Canvas" and then select the image we want to trace. This will place the image onto a plane.
Next the image needs to be calibrated since it has no scale. If the part is difficult to measure like this is, putting a ruler or something else of known dimensions in the picture helps a lot. Right click on the Canvas image in the design tree on the left side of the screen. From the drop down menu select "calibrate" and then pick two known points to measure between. Now we input the measurement and voila, the image is now digitally the "same" size as the part.
Create a sketch on the plane the image is on. Use line, arc and poly line to trace the image.
- After talking with the person who uses these daily, I chose to simplify the part and eliminated the "wavy" sections on the outside radius. It might be there as an "anti-skid" feature but in real world use the feedback I received was that it didn't do anything other than look pretty.
Now, use the extrude tool to turn the sketch into a 3D object.
Save the project!
Now export the 3D object in your favorite file flavor to your slicer.
(Fusion 360 does have a built in slicer, but I prefere a different slicer, probably because I haven't taken the time to fully configure the fusion slicer... Note to self... it's time to configure Fusion slicer...😉)
The native Fusion 360 file is also attached to this step if you want play with it. You'll see I ended up having to scale the part after preforming step 3 of this Instructable.
Step 2: 3D Print
Slice and 3D print the file from the materials section in TPU filament.
- The TPU in the 95A hardness range works well. Softer filament will be more squirrely to print and I don't believe the tradeoff of increased squishiness is worth the extra hassle in this instance. I've had good luck with YOYI brand TPU, here is the direct link if you want to try it https://amzn.to/469wWMz (affiliate link)
Printing:
I sliced this part in Simplify 3D because it's the best slicer I have for the Flashforge. For other 3D printers I typically use Bambu Studio. One of these days I should get around to putting a replicator/flashforge profile into Fusion 360...
I used a .4mm nozzle, .2mm layer height, 3 walls, 30% grid infill, no top layers, no bottom layers, no cooling fan, Hot end temp 220*C, Bed temp 60*C and Speed of 35mm/s.
- I've found TPU likes grid or full honeycomb infill the best. Other infill styles tend to be more prone to pin holes or layer shifting.
I found that the top and bottom layers make the part stiffer and harder to snap onto the wire tray. If you do print with top and bottom layers consider reducing the walls and infill.
If this is your first time printing TPU the Prusa Blog has some good tips here https://blog.prusa3d.com/how-to-print-with-flexible-filament_29672/
Notes:
This was not designed to work with PLA or other rigid filaments. I think PLA will be too brittle, but I could see a modified design possibly working with ABS or PETG with some adjustment and testing of the clip on area. I've included a .step file in the materials section if you feel like giving it a shot!
Step 3: Test and Iterate
Now that we have our first specimen, time to see if it fits!
My first attempt was too large and the clip didn't clip. I rescaled the model smaller and tried again.
Attempt #2 was much closer but the porridge was too small this time. The clip cliped but the bottom part was too short.
- I think I hear someone asking, why didn't I just measure it more better-er?! Two reasons, 1) This is an odd shaped part, and the distance I needed to measure to have a more accurate scale measurement was hard to pull repeatable measurement off of. 2) It's also possible the digital calipers died while trying to measure things and I didn't have the right batteries on hand or the patience to fine the dial calipers so I defaulted to the ol' "eyecrometer" with a ruler and just sent it... We may never know... 🤐
Number 3 nailed it on size, but was a bit too stiff. So for 3.1 I removed the top and bottom layers in the slicer. This was what it needed to be a little more squishy and it looks pretty cool too!
I sent a set of 3.1's off to be tested in a classroom and the feedback I received is that they work great! Full speed ahead!
*Looking back on things now, I also think there might be a slight angle in the picture I used (can't see all the way through the top clip) to trace the outline of the part which skewed things when I digitally scaled the image. Or at least that sounds like a pretty reasonable excuse right?!🤣
Step 4: Better Than New!
These feet have been in use in a classroom for about 6 months now and so far so good!
One other useful thing that's been pointed out is now it's really easy to color code your file organizers. This is reported to be superior to the sticky note method, no more file chaos if your sticky note falls off!
So if your file organizer feet need replacing you could color code them and have one color feet for your inbox, different color for your outbox, another color for your ignore/round file box...
Alrighty, well that's about all for this episode - No more throwing out your Fellows File Organizers, go 3D print new feet for them!
PS, I did it again... we're not wrapped up... there's still one more question to answer: Is feet the plural of foot? Or is it foots or feets or metric or standard?! Consulting the merriam webster dictionary, we find that feet is the plural of foot. Feets and foots are not real words. And now we know, and that's not nothing! https://www.merriam-webster.com/dictionary/foot
________________________________________________
If you'd like to see what I'm up to when I'm not Instructable-ing you can also find me at these places:
My Website: https://www.makerneer.com/blog
Instagram: https://www.instagram.com/makerneer
YouTube: https://www.youtube.com/@makerneer
My Etsy Shop: https://www.etsy.com/shop/Makerneer
Note: My posts may contain affiliate links to products I use and feel comfortable sharing. Which means when you click the marked product links in my Instructable nothing changes on your end, and I earn a small % on qualifying purchases. Thank you for your support!
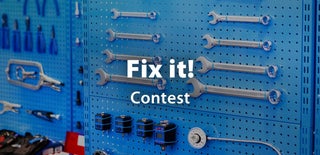
Participated in the
Fix It Contest