Introduction: Replica T80 Battle Tank
Tanks are cool. This is a fact. The Russian T80 is one of the coolest tanks ever made....so I decided to make a replica!
Here's the thing about this project...it took about 9 months of daily work...there were so many individual decisions/steps that it would be impossible to detail everything I did. Using plastic sheets as the base tub, I used a 3D printer (A Makerbot Replicator 2) to print out all of the detail pieces. All pieces were modeled in 3DS Max using pictures from the internet as reference.
This Instructable is going to be more of a guided tour of the process from start to finish rather than a step by step.
The above pics show some of the final product as well as a few shots of how I created a hatch for the turret. The computer image shows the parts I modeled in 3DS Max. Each colored piece is a separate part I modeled and printed. I would then glue the simple pieces together to form the more complex part. In this way I made all of the detail you see on the tank. Simple shapes, glued together to look more complex. That's about it. It really was not complex...merely time consuming. The number one resource I used for this project was PATIENCE.
Step 1: Planning
How to plan for a scratch built replica of something you'll never see in real life?
I started by looking at every picture of the T80U tank I could find. A GREAT resource is a site called Primeportal.net. It is a compendium of hi res photos of pretty much every military vehicle you can think of. It is awesome in its scope...definitely check it out.
Once I had a ton of pictures to look at I dug around the internet and found some orthographic views of the tank. Side, Front, Back and Top. I printed these out to be the exact size I wanted the final model to be. This is super important...these are the closest things to blueprints you will get (unless of course you can somehow find blueprints!).
Above are a few pics of the orthographic images I used throughout the process...I don't have much more than that to go on actually.
Now that we have our line drawings of the final scale/size we can prep the other stuff we will need.
-Digital Calipers (invaluable...you can measure the diameter of the roadwheel to a thousandth of a millimeter)
-Glue (super glue, epoxy...)
-Plastic sheets
-knives....saws....tweezers...sandpaper... pretty much your standard 'putting together models' kit
-3D printer. I used a Makerbot Replicator 2 for the whole process.
Step 2: Let's Get Those Treads and Wheels Out of the Way
I like to start making the road wheels and treads first. Why? Well....why not. Tank treads are totally cool and so I got excited and decided to start here. Also...this can be the most complex part of the build...lots of interlocking parts that need to work together and form the base of scaling/sizing for the rest of the tank. So let's make some treads!!!
The T80 has some awesome treads. According to the pictures the treads are made up of 3 different parts. Once I made some tests that worked I then printed tons and tons of these things. I think the total count was around 900 total prints. Next step...assemble the treads using some stiff wire. This took a good 8 hours. fun?
The above pics show the different pieces and assembled treads. Next up...wheels! Each roadwheel has about 12 pieces...axle hub, inner wheel, outer wheel, rubber tread pieces, hub details, hub cap... While we're at it, lets knock out the arms that will hold the wheels. You can see in the pics that I imbedded a steel rod in the arms for the wheel to attach to and spin.
Step 3: Let's Build the Bottom Tub to Put Those Sweet Wheels/treads On
We need something to put those wheels and treads on. Let's get the main body of the tank going.
I'm going to use sheets of plastic to create the tub. It is easy to work with and strong....it just needs proper structural reinforcing. Using the orthographic images I used some card stock to make test pieces. I figured out the sizes of the bottom and the sides. The T80 has a weird little angle built into the bottom of the hull so I figured out the size of those pieces in card stock too.
Once I was happy with the templates I cut the pieces out of plastic. To glue them together I used the awesome power of 3D printing to create angled structural joints. You can see the angle pieces holding the sides/bottom together in the pictures...I just used super glue to hold them together. 3D printing is perfect for this...I just printed off a bunch of these angle pieces...all were identical and ensure things were constructed straight and true.
Once I had the bottom tub all glued together I 3D printed parts for spring suspension. You can see the arms designed to hold springs...one for each roadwheel. The arms I built for the roadwheels in the last step interfaces with the spring arms. There is a pic of all the wheel attached to the tub.
Step 4: Let's Cap Off the Tub to Create a Full Hull
So we have a SWEET lower hull. Let's cap that thing.
Using sheets of plastic I cut out the pieces to enclose the tank hull. There are 'shelves' that attach to the bottom hull...you can see this in the first picture. These shelves will hold a lot of detail in a bit. The rest of the cap is going to be built as one complete piece that can be removed from the lower hull...this is so we can access the innards of the tank when needed.
Front slope, the rear decking and finally the top of the cap all put together. You can see a hole in the top...this is for the turret...at some point we will make a sweet turret that interfaces with the printed ring.
Now that we have a mostly enclosed hull we should move on to making the turret....because the turret is going to really make this thing look like a tank.....but.....the lower hull needs details. so many. bolts. tubes. doodads. I am going to resist my urge to make details and focus on the turret...
Step 5: I Can't Wait...let's Start Detailing Out the Hull
So here is where the fun really starts. Modeling/printing/gluing all the little bits and bobs onto your hull. These little things really make your project come alive.
People always ask me if I modeled the tank....I do and I don't. When I get to this fun detail phase I model bits and pieces in separate files. Inevitably I end up modeling a bit, print it, put it on the tank and then realize it is slightly too large or too small....so scrap that piece and size it up/down and reprint.
When I detail out a particular area of the tank my goal is to print as many INDIVIDUAL parts as possible. So instead of printing an armor plate with the bolts in one print I will print the armor plate and each bolt....then I will glue the bolts onto the plate. The reason I do this instead of printing it in one go is for finishing. The Replicator 2 prints come out good but not perfect. I usually sand/bondo each piece I print. If the armor plate had bolts sticking out of it, bondo/sanding would be very difficult....by printing the pieces individually I can sand the flat armor plate very easily...then glue the bolts onto the now perfect flat plate. Done!
Oh! That pink stuff in some of the pictures is Bondo. It is awesome. you mix it up, spread it onto a piece, when dry you can sand it down really fine...this is what I do to as many pieces as possible because they end up feeling super smooth. If I used a 3D printer like a Formlabs printer with higher resolution I might not need to use bondo...
You can see that I am spraying the model with grey primer as I go. I did this because it looks awesome....and some pieces are easier to prime before assembly. If you do prime the pieces before gluing them together don't forget to sand/scrape the paint off where the glue will go!
Step 6: Turret Time!
Okay....so now after many months we have a pretty awesome bottom half of a tank replica. Time to give this thing the hat it deserves....the turret.
We will make the turret with the same mentality as the bottom....create the 'hull' of the turret and then layer details ontop.
The turret is pretty big. Much too large to print in one go. After modeling the skin of the turret (this took a few hours as I just couldn't quite get the contours of the shape right in 3DS Max), I split the turret up into 6 pieces. I printed each piece and then glued them together using strips of plastic. The first 6 pictures show the turret shell coming together...I printed on a low detail setting as I knew I would bondo the whole thing. You can really see how rough the prints were! The next few pics show the bondo going on and being sanded. Then I primed the shell grey once the sanding was done.
Next I built the bottom plate for the shell to sit on. The plate is basically a piece of plastic sheet with a printed ring in the middle. That printed ring fits right into the ring we put on the top of the hull. The final pic shows the primed shell sitting on our detailed tank hull (there are a few detail bits on the shell...I couldn't help myself).
Next up....Detail that Turret!
Step 7: Mmmmm....turret Details
Same drill as before...pick a piece, model that piece, glue that little thing onto your turret. Repeat over and over and over and pretty soon you will have a sah-weet detailed turret.
The armor plates were easy...all the bolts are the same size so I would just print dozens at a time.
The ammo boxes and cargo boxes were simple as well and there are a number of identical ones on the turret so before you know it the turret looks pretty detailed.
Hatches were oddly complex but by printing each piece on its own it wasn't so bad.
The main cannon was quite detailed....much more so than just a tube. I used a brass tube from a hobby shop as a base...I tried to print out the tube but it ended up being a big pain in the butt. So I used a brass tube with details on top of it. Plastic sheets wrapped around and glued down with printed latches for detail. The final pic with the primed turret and cannon look pretty good!
See that weird box thing on the back of the turret? That sweet little bit of detail is the river fording kit. In real life it clamps down on the air intake for the engine. A tube extends 20 feet up so the engine can breathe as the tank drives on the river bed! That's right...this tank can drive UNDER WATER. That's pretty awesome. Just wanted to throw that out there.
Step 8: Let's Paint This Thing!
This one is simple. I used an air brush to paint the camo onto the tank.
I started with the light color, then the green, then the black. That's all. I haven't done any detailing beyond that. My airbrushing is pretty amateur hour. I need to work on this.
Step 9: Admire Your Tank Like a Boss
It's been a long trek....Let's take a look at this bad boy....
Here are a few pics of the final tank and some pictures from Primeportal showing the tank I was aiming to replicate. I think it turned out pretty well...there are still some details I should work on but for a scratch built project I am very happy.
The end result weighs about 15 pounds and is 36 inches long. 10 inches tall. It's a big beast.
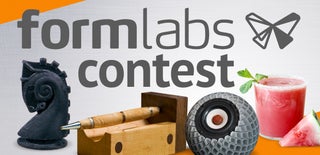
Participated in the
Formlabs Contest
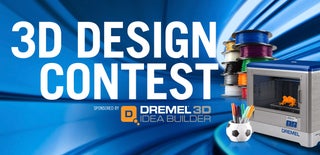
Participated in the
3D Design Contest