Introduction: Rocketeer Cirrus X3 Rocketpack
I've wanted a replica of the Cirrus X3 rocketpack from The Rocketeer forever. I finally decided to build one, from scratch. Everything made by me, by hand. This was also a cool project because I finally taught myself to mold and cast. This is the culmination of about 5 months work. The Rocket pack seemed like an almost insurmountable project, but I soon saw that it was really many smaller builds, each with their own challenges.
Push the button and the Rocket pack comes alive with lights and sounds right from the actual movie.
Step 1: The Rocket Housing
Dimensions on the Cirrus X-3 are really hard to verify. I'm not shooting for EXACT screen accuracy, just proportional-correctness.The main booster are built from a 6" thin-walled PVC. The outer dimension is actually close to 6-5/8" so it's not too far off from the 7.5 size of the actual prop. I built a jig to hold each body and get the same dimension on the angle cuts.
Step 2: The Rocket Engines
The bottom/bell portion of the engine was built from a plastic bowl, a drainage fitting and various trim pieces. The rings were added with clay to mimic the look of the actual rockets. This part was then molded in silicon and slush cast with resin. Side note: This is the first time I've molded and cast anything. I'm really excited.
I scratch/kit-bashed the upper portions of the two rocket engines – made from various parts in my shop and from the hardware store. I tried to match the general look and topology of the screen-used rockets. It was cheaper to build both, instead of building and casting.
The stainless steel lines were drinking water lines bought at the hardware store with fittings made for the ends. I used Duplicilor Metalcast paint to create the heat distortion colors at the ends.
Step 3: The Nosecones
The two nosecones were cast from a master. First I made a skeleton for the cone shape from styrene. I cut the profile shape of the nose cones and glued them onto a brass tube in a radial pattern. This was then filled with expanding foam and trimmed. I fiberglassed and Bondo'd it into shape. For sanding I created a sort of "vertical lathe" with my drill press. The brass tube at the center allowed me to mount it vertically on the press and hold sand paper on each side and work it into shape. Had to run the drill press SLOW, but it worked great and saved time.
I marked and scribed the line work around the top and used a drill to mark the hole indents.
For the 16 little "finlettes" that go around the top of the cone I carved a single finlette from styrene and made a tiny mold to cast the 16 of them I need. All 16 were then glued into place.
I then created a brush-on silicon mold of the cone and slush-cast the two resin cones for the final pack.
Step 4: Eggs, Vents, and Flaps
The Cirrus X3 has several detail parts that was each a build process. For the two "egg" shapes on each side I created a clay egg shape, built a mold box and poured silicon over it. Two resin casts were made for the pack.
Each of the two rocket bodies also has a vent that I build from thin bars of styrene from a hobby store. To curve the vent, I applied a heat gun to the finished vent and poured a mold over the final piece. Again, two casts were made of resin.
1/8" sheet styrene was used to create the two flaps on the bottom of the pack. A heat gun was used to make the bends.
Step 5: Body Assembly and Rivets
The two nose cones were glued onto the end of each rocket housing.
Two structural supports were needed to join the two rocket housings together. First, a piece of 3" PVC was heated with a heat gun and "smushed" into a flat shape to use as the bottom connector for the pack. Getting the compound curves required a paper template before making the final shapes.
A larger frame piece (that will be hidden inside the finished pack) was built from 1/2" thick Sintra. This piece not only joins the two halves of the rocket, but provides mounting points for various other panels and electronics inside the pack.
The pack contains hundred of rivets that had to be drilled and glued into place. I designed a spacing graphic that allowed me to accurately mark each hole.
Step 6: Center Section
This large, organic center section proved to be the biggest challenge. I wanted this piece to be removable to access the inner workings of the pack. This required building the master right on top of the rocket. I built up the master with non-hardeing clay. Once that was perfect, I poured a rubber mold over the clay section. This was followed by a rigid mother mold. These pieces were then removed from the pack and the clay was discarded. This mold was used to slush-cast the resin center section to be installed on the final pack.
Step 7: Upper Radiator
The upper "radiator" on the pack was built from a series of individual fins that were cut from 1/8" styrene. These we are all glued together and shaped to fit in between the upper rocket nose cones.
Step 8: Final Structural Assembly
Several final parts were added to complete the main assembly. A series of bolts were fitted to the main housing that will later accommodate a harness system. A back panel was attached to enclose the interior of the pack – again, removable for pack maintenance. A series of rods and connectors were attached to the bottom flaps.
Step 9: Painting
The final pack was primed and finished in Design Masters Modern Metals paint. The color is called Champaign Silver. It's a great metallic silver paint. Unlike any I've used, it dries fast and locks in the metallic particles so it doesn't need to be clear coated and doesn't rub off on your hands. The top of the cones were also painted a bronze color.
Step 10: Flight Harness
The harness system started with an aluminum subframe that bolts securely to the body of the rocket. I cut a series of 2" leather straps for the main harness system. This was riveted together into the final strap system. The padded back liner looks like leather but is actually a synthetic leather that attaches to the subframe with velcro.
Step 11: Electrical
The final pack is wired with lights and sounds and triggered by a push button. The LED light rings that hide inside the rocket bells are actually bright LED light rings for car headlights. Found them on eBay cheap. The vent in the center section hides a speaker that plays through the vent.
I purchased a custom programmed sound chip from replicaprops.com which includes the actual sounds from the film – ignition, thrust and wind-down. Push the put-on and it all comes to life.
Step 12: Final Rocketpack
The final pack is the culmination of hundreds of hours over the course of 5 months. What seemed like an almost insurmountable project ended up being dozens of smaller builds where I was able to learn new things and complete small tasks all while moving ahead on the larger project.
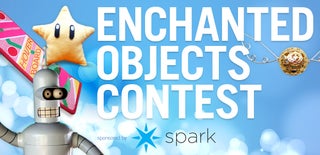
Second Prize in the
Enchanted Objects
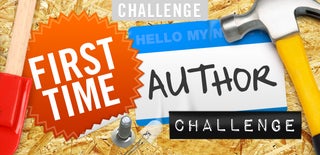
First Prize in the
First Time Author Challenge
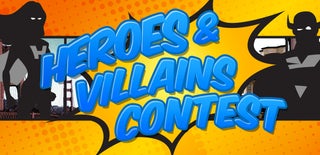
Third Prize in the
Superheroes and Supervillains Contest