Introduction: Shaving Kit Shelf
I recently decided to give wet shaving with old-fashioned double-edge razors a try. I wasn't sure what kind of razor I'd like, though, and ended up buying a lot of 3 different vintage Gillette razors on eBay fairly cheaply so I could try several. After disassembly and a thorough cleaning, I gave one a shot, decided I liked it, and bought some more kit. I now have 3 new razors, a shaving brush, aftershave, pre-shave cream, and some other goodies cluttering up my bathroom sink and cabinet.
All this new kit deserves a dedicated shelf and there's a perfect spot of bare wall next to the cabinet just begging to be filled, so I hit the drawing board. This shelf is a double shelf, with one shelf two inches above the other. The lower shelf has slots to hang the razors and brush from; the upper shelf is just high enough above the lower to give enough clearance to the hanging items and provides a spot to place other frequently-used items. Both are made from identical boards and are attached to a third identical board that mounts to the wall. This instructable focuses on the design of the shelf rather than on woodworking techniques, but I do try to cover the important parts for completeness.
Step 1: Tools and Materials
I used the following tools and materials. Substitute others at your preference:
Tools
- Table saw
- Table saw sled for easy, repeatable cuts. I followed Nick Ferry's instructions here for mine.
- Box joint jig: I used a kerfmaker (brew your own) and a simple board with a finger of wood the same height and width as my box joints sticking out from the front to cut quite reasonable box joints. It's clumsier to use and more prone to mistakes than something like this but it was super-easy to slap together and made use of tools I already had.
- Scroll saw (for cutting the large hole for the brush)
- Belt sander
- Drill press
- Drill bits:
- 3/8" for narrow slots
- 1/2" for wide slots
- 1/8" for the mounting holes in the shelf
- countersink (to countersink mounting holes; you could just use a large twist bit, though)
- Router
- flush trim bit
- 1/4" roundover bit
- Clamps, clamps, clamps (for holding work on the saw sled and drill press tables and for the glue-up
- Paper towels (yes, I know they're a poor substitute for "lint free cloths" for applying stain. Fight me)
- Painter's triangles
- Rubber mallet for assembly
- Sandpaper at 80, 120, and 220 grits.
- Combination square for marking very accurate measurements onto boards to be cut
- Ruler/straight edge and protractor for design drawings
- Digital calipers for taking all the original measurements.
Materials
- 36" length board of Red Oak, 2.5" x 0.5"
- Gorilla brand wood glue
- Varathane wood stain in "Dark Walnut" to stain the contrasting back panel
- Watco danish oil in "golden oak" to finish
- EVA foam for prototyping
For Mounting Shelf to Wall
- 3 x Drywall anchors
- 3 x flat-head #8 screws 1" long (you can use a different head type to avoid needing to countersink your holes; just make sure they don't interfere with the razors)
- 1/4" drill bit
- cordless drill / screwdriver
- center punch
- hammer
- level
Step 2: Measurements and Design
Your first step is to grab the calipers (an accurate ruler will do in a pinch) and take all the relevant measurements. To hang the DE razors you need to know the widest diameter of the handle within a half inch below the head and the length, width, and depth of the head for each one. To hang the brush you need to find the diameter of the narrow part of the handle, and how much that changes within a quarter inch on either side (since we're using half-inch stock for this). While you're at it, also grab the diameter of the base of the brush -- so you have an upper bound on how large this hole can be without the brush falling through -- and the diameter of the bulb (the bristles of the brush) -- so you know how much room you need to leave between the brush hanger and the first razor hanger.
If you want to hang the cartridge razors that are more common today keep in mind that while double-edge razors tend to have big, flat heads and cylindrical handles that are really easy to measure and design for, cartridge razors have a more vertical shape and are much taller from the narrow part of the handle to the top. Their handles also have funny "ergonomic" shapes. It's hard tell exactly what angle they'll hang at or how high they'll rise above the shelf, so I recommend making mockups.
After measuring everything you can think of, begin drawing detail plans for the slots required for the hangers. I used graph paper with large 1" squares divided up into smaller 1/8" squares, which is quite convenient if you're going to be working in a shop that has tools marked in fractional inches. A graph with 5 or 10 divisions per square would be better for working with decimal values (either inches or metric).
Some things to consider:
- When marking out measurements, keep in mind the process you'll use to cut the slots. I used drill bits to cut round ends to my slots, then sliced out the straight parts with my table saw, but you could use a router to do it in one pass, or use other tools. Since I used a drill bit I found it most useful to mark the very center of the semi-circle that terminates each slot so I could drill there instead of measuring to one of the edges and then having to compensate for the radius of my bit.
- When making repeated marks, measure each one from a known reference point (machinists call this a datum) rather than measuring them off of one another to avoid compounding measurement errors.
- After making a mistake on your drawing, either mark it clearly as a mistake or mark the entire drawing bad and start fresh. You don't want to have to decipher your crib notes in the shop.
- The point of this shelf is to be comfortable and to make it easy to access your goodies on a near-daily basis. Leave room to make sure it doesn't feel crowded to get at your gear or you'll just end up leaving them on the sink.
- My measurements worked out such that I could make my shelf a U shape out of three identical lengths of a 2.5" board using half-inch deep box joints and still have just enough clearance for my taller cartridge razors. Make sure you test this before building it if necessary.
Step 3: Mockup!
Spacing is rather subjective and the razors and brush are probably slightly weird shapes (with ridges, bumps or tapers rather than being perfect cylinders). That makes this project a perfect candidate for a mockup! Several instructables and this fantastic propmaker's YouTube channel can teach you more about working with EVA foam for costuming purposes than you ever knew existed. I had some on hand and it's just about the same thickness as the oak I wanted to use for this project, so I decided to use a scrap piece to double-check all my measurements and decide if I liked where the idea was going.
When cutting foam, hold a straight-edge down firmly against the foam and slide a sharp boxcutter along it, holding the knife as vertical as possible to get a straight, square cut. For the round ends of the hanger slots use an X-Acto knife and guide the blade through the foam with gentle sawing motions using little pressure and multiple passes. You wouldn't want to use the knife this way for a costume or prop piece, but we don't care about appearances here.
After you've cut your design out of the foam, hang the razors from it to see how it works! Make any adjustments you find to your design and cut out a new mockup from the new design. Iterate until you're happy with it!
Step 4: Bonus Step: the Box Joints
Box joints will give this shelf excellent strength and a classy appearance, but they're by no means necessary. You can use simple butt joints or rabbets or anything else. Be mindful of how different kinds of joints will change the dimensions of the finished shelf. In addition, there are plenty of resources out there (and many on this site) that describe making box joints in much greater depth than I do here, so this step is mostly just to follow along with what I came up with using the tools available to me.
My problem was that while I have this nifty "kerfmaker" device and a slick table saw sled, I don't have a dado stack, so I needed to figure out a way to make a box joint jig that I could use with the kerfmaker to cut my joints.
The jig consists of a piece of plywood scrap with a notch cut out partway along the face and a finger screwed into the notch so that it sticks out the front of the jig. Ideally this should be perfectly square to the face of the jig, and should not wiggle at all (photo 2). The finger and notch are both the same width as the joints you want to cut; make the finger, then use the kerfmaker to match the notch perfectly to the width of the finger. The top of the finger (and thus the depth of this initial notch) needs to be shallower than the notches you want to cut for your joints, or else your boards will not be able to lie flat against the table saw sled and each successive joint you cut will be shallower than the last.
To set up for cutting, place a second joint-width finger (call it the "floating" finger) against the jig next to the first (between the jig's finger and the saw blade) and position the jig so that the saw blade just kisses this floating finger. Place the kerfmaker against the end of the jig and clamp or screw another scrap (no thicker than the back board of your jig) up against the sled's fence on far end of the kerfmaker as a stop block. (see photo 3)
Set your saw blade depth to be just at or deeper than the thickness of your boards (I went slightly deeper, which made the teeth stand slightly proud of the joint. Then I trimmed them down with a router's flush trim bit). Make your first cut there, then pull the kerfmaker up so that its overhang rests on the stop block and slide the jig and boards together until the jig again touches the end of the kerfmaker (photo 4). Make a second cut and you now have both ends of the notch cut out. Remove the kerfmaker and slide the jig freehand making successive cuts between your first two until you've cleared out all the material.†
To cut successive joints pick up the board off the jig and move the notch you just cut forward to straddle the jig's finger. It should be a perfect fit! This finger holds the boards and jig fixed relative to one another so that adjusting the jig makes an identical adjustment to the boards. It's possible (and a good idea) to stack multiple boards at once to cut the joints all at the same time.
† Some boards will start with a tooth, and some with a notch. Boards that have a tooth first can be started by placing the end of the board directly against the jig's fixed finger. Boards that have a notch first need to be offset by the width of one joint, so place the floating finger between the end of the board and the fixed finger to provide that offset. The floating finger is not needed again after you've started the board.
Step 5: Practice Board, Test Fitting, and Hanger Slots
(apologies for putting all of this in one step; they should, perhaps be multiple, but I didn't take any action photos of this part of the work, so it's very light on visual documentation)
Practice
Now that you know *how* to cut your box joints...practice on a piece of scrap until you *actually* know how to cut them. Seriously, if you're trying some fancy joinery based only off my shoddy jig and instructions from the previous step it's not gonna go well the first time you try it, so practice on scrap until you get a feel for what you want to do. test-fit the pieces to make sure they line up properly and fit reasonably. My understanding is that your goal is to need to tap the boards gently with a soft mallet to fully seat the joint. You can sand the bottoms of the notches, but don't make my mistake and sand the sides of the teeth -- you'll make the joint too loose and it'll be a pain to get it glued up properly (and probably will be weaker for it).
While you've got that scrap out, go ahead and mark up the measurements for all the hanger holes and slots and practice cutting *those* too.
Cutting the Slots
If you're hanging DE razors, you're in luck! because the double-edged blades are a standard size, your razor's heads should all be nearly identical (and I've only seen razors with handles in the very center of the head). That means that no matter how thick the handle is, the centers of the handles are all going to be the same distance from the near edge of the board, and you can scribe a line at that distance from the edge and then mark the centers of the hanger slots along that line. Grab the closest drill bit you have that's larger than the diameter of the handle you measured for each slot and drill the holes on the centers you marked.
Once you have the holes drilled, draw parallel tangent lines from the widest points down to the front edge of the shelf. Set your table saw's depth to match the length of this line (it should be the same measurement as you used to scribe the guide line before drilling) then tip the board on-edge, line up the blade so that it just kisses the tangent line (and so that the kerf is on the inside of the slot!) and slice it out. Do the same thing on the other side of the slot to remove the rest of the waste and -- if you lined everything up properly -- you'll have a slick-looking oval slot with semicircular end and perfectly straight sides coming in from the edge of the board.
Test-fit the razors and marvel at how slick this is going to look hanging on your wall. If any of the slots are too small, re-cut with the table saw or sand them wider.
Cutting the Brush Hanger
If you've got a hole saw of the right diameter, or some better way of making a small (but larger than most drill bits) circular hole in wood you should use that. If, instead, you have a scroll saw or band saw, practice, practice and get comfortable following lines with that.
To mark the cut, find the center of the hole as you did above. Figure out the radius of the hole and use a compass to swing the arc that you want to cut. If you don't have a compass cheat using a nail and some string or if all else fails grab an accurate ruler and mark several points along the edge of the circle then connect the dots to make your guide line. If you're confident in your measurements you can position the hole just right so it's slightly more than half a circle -- as long as the opening at the edge of the board is wider than the narrow part of the handle and the whole hole (yuk yuk yuk) is smaller than the flared base of the handle it'll stay and be wonderfully secure!
If you're less confident in your measurements you can set the hole back a bit from the edge and make an oval slot like you did for the razors.
You can use the same table-saw trick as above to take care of the straight lines, then slap the board on the scroll saw's bed and carefully cut along your guide. Once again, cut small, test-fit, and recut or sand wider as necessary.
Mounting Holes
Once you've got everything cut the way you like it and you've verified that the joints and hangers all fit the things they're supposed to, assemble the hanger flat as in picture 2 on this step and trim up the edges so they're all flush with one another. Mark, drill, and (if using flat-head screws) countersink the mounting holes now, before assembly and definitely before trying to mount the shelf to the wall -- you don't want the screw to have to push any wood out of its way as it goes through your board or you'll risk splitting it, so pick a drill bit that's the same diameter as the shaft of the screw so that only the threads bite the wood.
Step 6: Staining, Assembly and Finishing
This is a shaving shelf, so it's going to get at least a little bit wet. Thus, whatever you do you need a finish that'll protect it. I'm new to woodworking and upon further research didn't give mine quite the finish it deserves. I'll keep an eye on it and decide if I need to take it down and refinish it at some point. In light of that I encourage you to look around for some other instructables or resources on proper staining and finishing techniques. I've written up what I did, but as with the box joints in step 4, my focus in this step is more aimed towards my intent and particular circumstances than on teaching proper technique.
Before you get to glue, stain, or finish, you need to sand. Just about everything I've heard about finishing woodworking projects says that the magic is in the sanding. Start with a 120 or 150 grit sandpaper and go up to 220 or, if you're feeling ambitious, 320. Use tools like sanding blocks where possible to avoid rounding edges and leaving grooves where you don't want them. Avoid tools like belt sanders unless you're familiar with them because they can remove a lot of material very fast and if you use them freehand you're distressingly likely to turn a straight edge into a wavy or rounded edge that you didn't want.
I wanted my box joints to show some contrast, so I stained my back panel a dark color before assembling and finishing. If you choose to do this, make sure you mask off the three interior faces of each notch to protect them from stain (otherwise the glue won't stick as well). To do this, tear of a small piece of painter's tape and affix it tightly to the wood with the back of a knife. Make sure you get as far down into the corners as possible. Once it's firmly affixed, use the front of the knife to slice it off flush with the wood.
Apply your stain according to the manufacturer's directions to put as many coats of stain as you want. Once it's properly dried remove the tape and apply glue on one of the corners. I put a dab of glue on each inside face of the box joints and used my finger (gloved for easy cleanup) to spread each dab evenly across the surface. Fit the joint together and tap the pieces together with a soft mallet to make sure they're fully seated. Take as many clamps as you can find and then tetris them onto the shelf to hold it together. Wipe up any squeeze-out with a damp rag and let the whole thing dry overnight.
The astute observer will notice that I assembled all three pieces of my shelf in a single glue-up. I would not recommend this, and in fact it was an accident after I applied glue to the notches of the wrong edge of my back panel. Doing the glue-up in two stages will make it easier to clamp each joint well, I think, and to make sure that each joint is properly square.
Once it's assembled you can apply the finish. I used Watco Danish Oil which both stains and finishes but should probably be combined with a polyurethane topcoat anyway. The most interesting thing about this was that the danish oil seemed to pull the stain I'd already applied to the back panel out of the wood. It's not terribly noticeable on the large face, but nearly all of the dark stain is gone from the exposed ends of the joints, leaving them just about the same color as the top of the shelf.
Congratulations! You're now the proud owner of a custom shaving station including hangers for your brush and razors and a shelf for shaving cream and aftershave. Give yourself a high five, then grab a level and your cordless drill and go put it up!
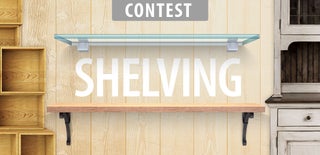
Participated in the
Shelving Contest 2016